As with any process, you are bound to encounter defects in the process. You can encounter things such as misshapes and off sizing of the metal. This can occur due to either a bad welding process or bad technique. Listed below are the most common defects that you’re likely to find.
There are 2 types of welding defects: External Welding Defects and Internal Welding Defects.
Internal welding defects include:
- Necklace Cracking
- Slag Inclusion
- Incomplete Penetration
- Incomplete Fusion
External welding defects include:
- Porosity
- Welding Cracks
- Crater Cracks
- Cold Cracks
- Heat Cracks
- Spatter
- Overlap
- Undercut
What are External Welding Defects?
Overlap
What is Overlap in welding?
Overlap is the considered a protrusion of weld metal beyond the weld root. Overlap typically occurs in butt joints and fillet welds and results in notches occurring at the toe of the weld. These notches are undesirable due to the stress concentration that occurs under load. These discontinuities are caused by either insufficient current or incorrect welding technique.
How does overlap occur in welding?
Overlap in welding occurs when the molten metal from the weld flows over the surface of the base material and then cools without fusing to the base material. A common cause of overlap in welding is having too much weld metal supplied because of the weld speed being too low. When there is overlap in fillet welds it’s typically caused by the effect of gravity on excessive molten metal.
How do you fix overlap in welding?
To avoid overlap you must make sure to review your welding settings (welding speed and current).
Video credits to Weld.com. It goes over ways to prevent weld overlap.
Spatter
What is spatter in welding?
When you have particles that attach to the surrounding areas of the surface the result is spatter. Surprisingly it’s pretty common in welds done with gas metal arc welding. It’s also one of the defects that you can’t completely eliminate, no matter how hard you try. It is, however, possible to keep its occurrence as low as possible.
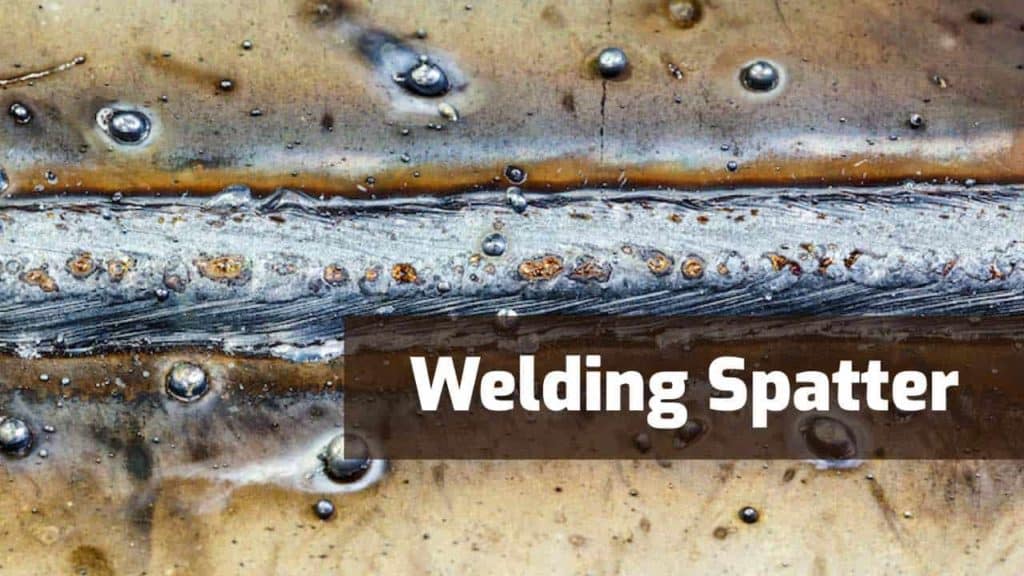
How does spatter occur in welding?
- When your amperage is too high
- When the setting of voltage is too low
- When your welding surface is contaminated
- When your arc is long
- When you have an incorrect polarity
How do you fix spatter?
- Make sure you welding surface is clean before you weld
- Reduce your overall arc length
- Fix your weld current
- Fix the electrode angle
Cracks
What are cracks in welding?
A serious complication that many welders tend to encounter during the process are cracks in the weld. These cracks can manifest anywhere in the weld, such as in the metal, on the surface, or anywhere else that touches the heat of the welder.
The different types of cracks are:
- Heat cracks
- Cold cracks
- Crater cracks
What are heat cracks in welding?
These typically occur in the crystallization portion of the welding process. Temperatures of the metal at this point typically rises to over 10000C
What are cold cracks in welding?
These types of cracks typically show up after the weld has been finished. They can sometimes take longer than average periods to show and will manifest as slight deformities in the metal.
What are crater cracks in welding?
These types of cracks tend to show at the end of the entire process and occur at the end of the weld. When there is not enough room at the end of the weld for shrinkage of the weld metal a crater crack forms.
Why do welding cracks occur?
- When you use hydrogen while welding ferrous metals
- When there’s residual stress from the solidification shrinkage
- When the base metal is contaminated
- When you are welding with a high welding speed but with a low current
- When you don’t preheat before you weld
- When there’s a bad joint design
- When there’s a high sulfur content and alot of carbon in your metal
How do you fix welding cracks?
- Preheat your metal when it’s required
- Properly cool the welding area
- Have a correct joint design
- Take away any impurities
- Use the right metal
- Have a sufficient sectional area
- Use the correct amperage and welding speed
- Make sure your crater is properly filled
This is also one of the reasons why it’s important to hold these welding skills
Video credits to Garry Pace. It details the different types of welding cracks.
Porosity
What is porosity in welding?
When there is contamination in your weld porosity can result. When you have gases in your weld you have a weld that is weak and collapses over time.
Why does porosity occur in welding?
- When there is not enough electrode deoxidant
- When you use a longer arc
- When there is moisture in the weld
- When you don’t use a correct gas shield
- When you use too much gas flow
- When your surface is contaminated
How does porosity occur in welding?
- Clean your welding material before you weld
- Make sure your electrodes and materials are dry
- Have the correct arc distance
- Make sure that the gas flow to the machine is properly adjusted
- Reduce your arc travel speed
- Make sure you have the correct electrodes
- Weld with the correct technique
Video credits to Miller Welders. It goes over how to fix porosity in your welds – The right way!
Undercut
What are undercuts in welding?
When you have a groove formation at the weld toe you come into contact with this imperfection. When you have an undercut you have a weakened weld.
Why does undercutting occur?
- When you weld with too high a current
- When you weld to quickly
- When you use an incorrect angle when you weld
- When the electrode you weld with is too large
- When you use an incorrect amount of shielding gas
- When you don’t have the right filler metal
How do you fix undercutting in welding?
- Use the correct electrode angle
- Make your arc length shorter
- Weld with a lower electrode travel speed
- Weld with the correct shielding gas
- Use the right electrode angle
Video credits to Herbert Bartley. It talks about how to avoid undercut in welds.
What are Internal Welding Defects?
Unfinished Penetration
What is Unfinished Pentration in welding?
When the groove of the metal isn’t filled completely the result is an incomplete penetration. This also means that the weld metal won’t fully extend throughout the thickness of the joint.
How do unfinished penetrations occurs?
- When there is to much space in the metal you’re welding
- When you move the bead too quickly
- When you’re using too low of an amperage setting
- When there is too large of an electrode diameter
- When there is an improper joint
How do you fix unfinished penetration in welding?
- Make sure to have a proper joint geometry
- Have a properly electrode size
- Reduce your overall arc travel speed
- Make sure to have the correct welding current
- Have the correct alignment
Video credits to Kevin Caron, Artist. It goes over way to make sure you get good welding penetration.
Slag in the weld
What is slag in the weld?
When you have slag in your weld you can tell by simply looking at it. Slag is a byproduct of flux-cored welding, stick welding, and submerged arc welding. When the flux used in the welding melts you can encounter slag in your weld.
How does slag in the weld occur?
- When you don’t clean the weld correctly
- When the weld speed is too fast
- When you neglect to clean the weld pass and move on to another one.
- When you have an incorrect welding angle
- When your weld pool cools too quickly
- When the current you use to weld is too low
How do you fix slag in the weld?
- Make your current denser
- Fix the cooling rate of the weld
- Fix the angle of the electrode
- Remove the slag from the bead
- Fix the speed of the weld
Video credits to xAZAZELx13. This video goes over how to repair slag in the weld.
Unfinished Fusion
What is unfinished fusion?
When there isn’t a proper fusion in the base of the weld and in the weld metal you have an improper fusion. You can also find this in the adjoining beads of the weld. When you have unfinished fusion, you have a weld with gaps that don’t have molten metal in them.
Why do unfinished fusions occur?
- When you don’t have enough heat
- When the surface of the weld is contaminated
- When you have an incorrect electrode angle
- When you weld with too fast a travel speed
How do you fix unfinished fusion?
- Make sure to use the correct arc voltage for your weld
- Clean the metal before you weld
- Keep the molten metal from flooding the arc
- Lower your disposition rate
Necklace Cracking
What is Necklace cracking in welding?
Necklace cracking occurs when the electron beam weld doesn’t fully penetrate fully and a blind weld occurs. In these instances molten metal neglects to flow into the penetration cavity and onto the side walls of the workpiece. This occurs in metals such as is carbon steel, nickel base alloys, stainless steel, titanium alloy.
What is the cause of necklace cracking in welding?
The common causes of necklace cracking in welding are:
- Improper welding tehnique
What are a few remedies for necklace cracking?
A few known remedies for necklace cracking are:
- Using proper welding technique
- Using proper materials for welding
- Making sure to use a constant speed while welding