Table of Contents
A Comprehensive Guide to Welding Amperage and Voltage Selection
Welding involves various techniques, materials, and equipment settings, making it vital to understand how to select the proper amperage and voltage for your specific application. Are you asking yourself, how do I know what amp to weld at? This guide dives into the key factors affecting amperage and voltage selection, how these relate to different welding processes, and practical tips for optimal performance.
Understanding Amperage in MIG Welding
MIG welding relies on wire size, and as a general rule of thumb, for every 0.001 inch of wire diameter, 1 amp of output is required. For instance, a wire with a diameter of 0.125 inches will require approximately 125 amps. While this rule is a good starting point, the choice of amperage and polarity depends on several factors:
- Electrode and Base Metal: The welding electrode and the type of base metal (ferrous or non-ferrous) influence the amperage needed.
- Welding Process: The amperage impacts penetration depth, weld bead quality, and the electricity flow per second.
MIG welders also require precise coordination of wire feed speed and voltage. Increasing voltage requires a corresponding adjustment to the wire feed speed to maintain adequate filler material in the weld puddle. For thin materials, lower voltage settings are essential to avoid burn-through, while thicker materials benefit from consistent, higher settings.
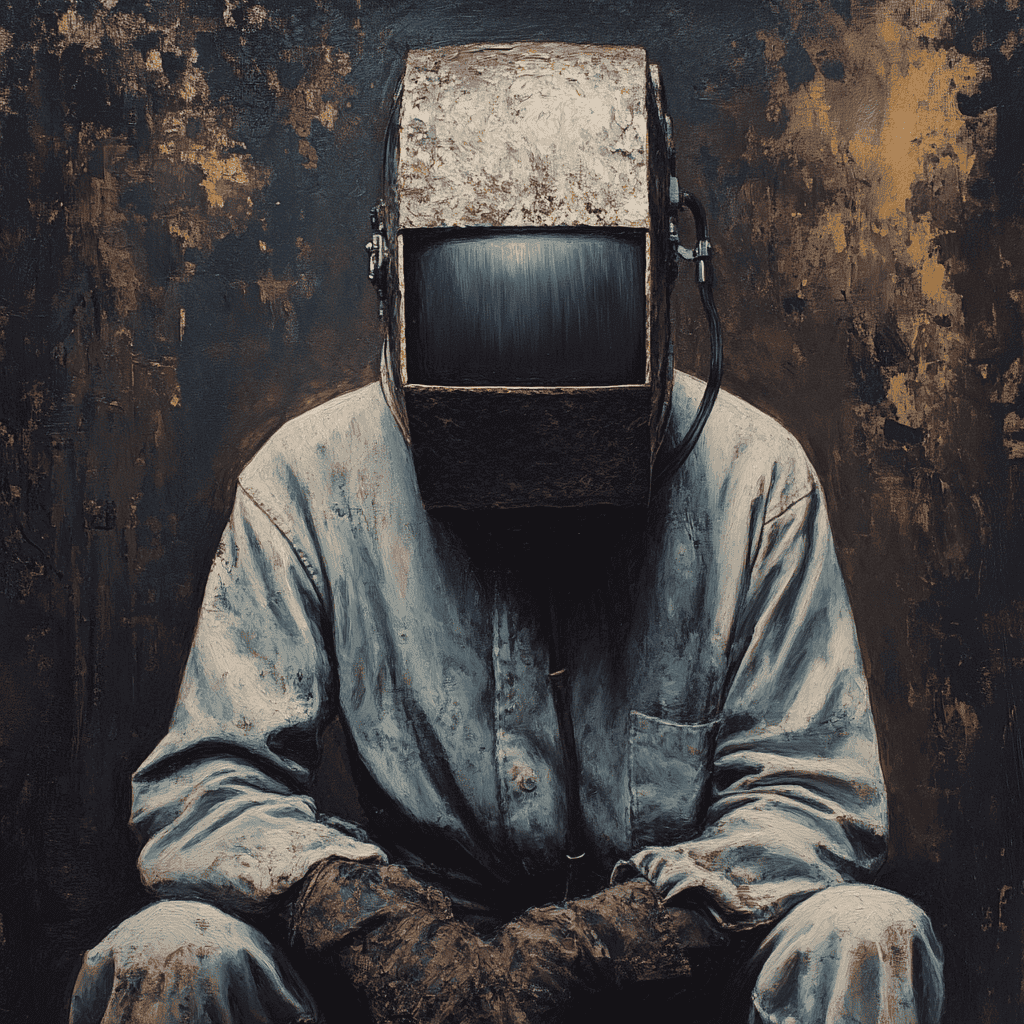
The Complexity of TIG Welding Controls
TIG welding involves significantly more controls than MIG or stick welding. Advanced TIG machines can feature up to 20 knobs, allowing operators to fine-tune settings for arc initiation, amperage, and gas flow. The complexity offers unparalleled precision but requires practice to master.
- Amperage Control: Often managed via a foot pedal, TIG welders allow dynamic adjustments during welding. Pressing the pedal increases amperage, while releasing it reduces power.
- Alternating Current (AC) for Aluminum: AC is preferred for TIG welding aluminum due to its “cleaning” effect, which removes oxide layers for a cleaner weld.
- Duty Cycle: Operators must monitor the machine’s duty cycle—higher amperage reduces the time a machine can weld continuously.
Understanding Amperage in MIG Welding
MIG (Metal Inert Gas) welding is a popular and versatile process, and selecting the correct amperage is crucial for achieving high-quality welds. The amount of amperage required in MIG welding primarily depends on the wire size and material thickness. Here’s an expanded look at how amperage works in MIG welding and the factors that influence its selection.
Wire Size and Amperage Correlation
Wire size is a key determinant of amperage in MIG welding. A general rule of thumb is that for every 0.001 inch of wire diameter, 1 amp of output is required. This means that larger-diameter wires require more amperage to melt and deposit properly. For example:
- 0.030-inch wire requires approximately 30 amps.
- 0.035-inch wire requires approximately 35 amps.
- 0.125-inch wire requires approximately 125 amps.
This rule provides a starting point, but fine-tuning is often necessary based on the specific application, material type, and joint design.
Electrode and Base Metal
The type of welding electrode (wire) and the base metal being welded significantly influence the required amperage.
- Electrode Material: The composition of the wire affects its melting point and the amperage needed to achieve proper deposition. Common MIG wires include mild steel, stainless steel, and aluminum, each with unique characteristics:
- Mild Steel: Requires moderate amperage and is suitable for general-purpose welding.
- Stainless Steel: Typically requires slightly higher amperage due to its higher melting point and lower thermal conductivity.
- Aluminum: Demands significantly higher amperage because of its high thermal conductivity and relatively high melting point.
- Base Metal Type: The material being welded also affects the amperage:
- Ferrous Metals (Steel): Ferrous metals like carbon steel generally require lower amperage than non-ferrous metals.
- Non-Ferrous Metals (Aluminum): Non-ferrous metals like aluminum absorb heat more rapidly, necessitating higher amperage settings to maintain a stable arc and adequate penetration.
Welding Process Considerations
MIG welding relies on a continuous wire feed and shielding gas to protect the weld pool. The amperage impacts several critical aspects of the welding process:
- Penetration Depth: Higher amperage increases penetration, which is necessary for thicker materials. Too little amperage can lead to insufficient penetration, resulting in weak welds.
- Weld Bead Quality: Proper amperage ensures a smooth and uniform bead. Inadequate amperage may cause defects like lack of fusion, while excessive amperage can lead to burn-through or excessive spatter.
- Electricity Flow per Second: The flow of electricity determines how effectively the wire melts and fuses with the base material. Amperage must match the heat requirements of the welding task to achieve strong and clean welds.
Coordination of Wire Feed Speed and Voltage
MIG welding requires precise synchronization between the wire feed speed and voltage to achieve optimal results. These two parameters are interdependent and must be balanced to ensure a consistent weld puddle:
- Wire Feed Speed: Controls the rate at which the welding wire is fed into the weld pool. Faster speeds require higher amperage to melt the wire efficiently. Conversely, slower speeds require lower amperage to avoid overheating the weld pool.
- Voltage: Determines the arc length and stability. Increasing voltage allows for a wider arc, which is beneficial for thicker materials, but it also necessitates a corresponding increase in wire feed speed to maintain proper filler material delivery.
Application Examples
- Thin Materials: When welding thin materials, such as sheet metal, use lower amperage and voltage settings to avoid burn-through. For instance, a 0.030-inch wire might be paired with 30–40 amps and a low wire feed speed.
- Thicker Materials: For thicker materials, increase amperage and wire feed speed to achieve deeper penetration and adequate fusion. A 0.035-inch wire may require 100–130 amps with a higher wire feed rate.
Tips for Optimizing Amperage in MIG Welding
- Start with Manufacturer Recommendations: Consult the MIG welder’s manual or the wire manufacturer’s data sheet for suggested amperage and wire feed speed settings based on wire size and material thickness.
- Test on Scrap Material: Experiment with different settings on scrap pieces to find the optimal combination of amperage, voltage, and wire feed speed.
- Monitor Weld Appearance: The weld bead should be smooth, uniform, and free of defects like porosity or spatter. Adjust settings as needed to improve weld quality.
- Use the Right Shielding Gas: The type of shielding gas affects arc characteristics. For example, a CO₂ or argon-CO₂ mix provides better penetration, which may impact amperage requirements.
By understanding the relationship between wire size, amperage, and other factors, you can optimize MIG welding settings for a wide range of applications, ensuring strong, high-quality welds every time.
Base Material: Thickness and Type
The type and thickness of the base material are among the most critical factors influencing amperage settings in welding. These variables determine the heat input required to achieve adequate penetration, fusion, and weld strength. Here’s an in-depth look at how material characteristics and application needs impact amperage selection.
Material Type
The material being welded has unique properties, such as melting point, thermal conductivity, and composition, that dictate amperage settings.
Aluminum
Aluminum has high thermal conductivity, which causes heat to dissipate quickly throughout the material. This requires higher amperage to maintain the heat needed for proper welding. With a melting point of approximately 1,200°F, aluminum requires significantly more energy to reach the weldable state compared to other metals. Alternating current (AC) is commonly used for aluminum welding, particularly in TIG welding, as it facilitates oxide cleaning while maintaining arc stability. Aluminum is prone to warping and cracking due to its heat sensitivity. The welder must move quickly to manage heat input effectively and prevent damage to the material.
Steel
Steel, including carbon steel and stainless steel, has a lower melting point compared to aluminum, making it easier to weld at lower amperages. Carbon steel welds well with moderate amperage and is forgiving to variations in heat input. Stainless steel requires slightly higher amperage than carbon steel due to its lower thermal conductivity and higher resistance to heat flow. Steel is versatile and commonly used for structural work, automotive repairs, and industrial fabrication.
Non-Ferrous vs. Ferrous Materials
Non-ferrous metals like aluminum, copper, and brass generally require higher amperage settings due to their high thermal conductivity and unique melting characteristics. Ferrous metals like carbon steel and cast iron typically need less amperage compared to non-ferrous counterparts. They are more resistant to warping, making them easier to weld with consistent heat input.
Material Thickness
The thickness of the material directly impacts the amperage needed to achieve adequate penetration and fusion.
Thicker Materials
Thick materials require higher amperage to provide sufficient heat for deep penetration into the material. Inadequate amperage can result in weak welds or lack of fusion. For very thick sections, welders may need to perform multiple passes. The root pass often requires a higher amperage for penetration, while subsequent passes may use slightly lower settings. High amperage can generate excessive heat, so managing cooling between passes is essential to avoid overheating or distortion.
Thin Materials
Thin materials like sheet metal require lower amperage to avoid burn-through or warping. Short-circuiting (MIG) or pulsing (TIG) techniques are commonly used to control heat input while maintaining adequate weld quality. For tasks like edge welding on thin materials, precision in amperage adjustment is critical to avoid overheating and achieve clean welds.
Welding Application
The specific purpose and environment of the weld also influence the amperage settings.
Precision Tasks
Applications involving thin, exotic, or high-value materials, such as helicopter exhaust manifolds, require lower amperage for controlled heat input. TIG welding is often preferred for precision tasks, as it allows precise amperage adjustments through foot pedals or control panels. Reducing amperage minimizes the heat-affected zone (HAZ), preserving the material’s integrity and appearance.
Heavy-Duty Welding
High-amperage settings are essential for heavy-duty tasks such as oil pipeline construction or structural welding. High amperage ensures proper fusion and strength, critical for materials exposed to high stress or load conditions. Stick welding is often used for heavy-duty applications due to its ability to handle high amperage and work in harsh environments.
Convenience Settings
For less critical applications, such as workshop repairs or quick fabrication tasks, operators may increase amperage slightly to speed up the welding process. Higher amperage can produce faster welds, but care must be taken to ensure bead quality and adequate penetration. This approach is suitable for non-structural tasks where appearance and precision are less critical.
Practical Tips for Managing Amperage Based on Material Type and Thickness
Start with recommendations from the material manufacturer’s guidelines or the welder’s manual for suggested amperage ranges based on material type and thickness. Perform test welds on scrap material to fine-tune amperage settings before working on the actual piece. Monitor weld appearance, as proper amperage produces a smooth, consistent bead. Signs of insufficient amperage include lack of fusion or weak welds, while excessive amperage may cause burn-through or spatter. Use preheating for thick materials, as preheating can reduce the amperage required by lowering the material’s resistance to heat flow. Control cooling for thin materials by allowing adequate cooling between welds to prevent overheating or warping.
By understanding the interplay between material type, thickness, and welding application, you can effectively select the appropriate amperage for any welding task, ensuring high-quality, durable welds while minimizing defects.
Specific Welding Processes and Amperage Selection
MIG Welding
MIG (Metal Inert Gas) welding is one of the most versatile and user-friendly welding methods. It uses a continuous wire feed and shielding gas to create clean, strong welds with minimal spatter. The process primarily relies on variable voltage settings, with adjustments to wire feed speed ensuring the proper delivery of filler material.
Voltage and Wire Feed Coordination
Voltage controls the arc length and heat input. Higher voltage settings create a wider arc, which is necessary for thicker materials, while lower settings produce a narrower arc suitable for thin materials. Wire feed speed determines how much filler material is fed into the weld puddle. If the wire feed is too fast relative to the voltage, the wire can pile up, causing irregular welds. If it’s too slow, the arc may become unstable. Proper balance is essential for smooth, consistent welds.
Application to Different Material Thicknesses
For thin materials like sheet metal, start with the lowest possible voltage settings to avoid burn-through. A slower wire feed speed is also recommended to reduce heat input and control the weld puddle. Techniques like short-circuiting transfer can further minimize heat and spatter. For thicker materials, use consistent voltage settings to ensure adequate penetration and fusion. Since thicker materials can absorb more heat without damage, higher voltage settings and faster wire feed speeds are typically required. Multi-pass welding may be needed for very thick sections.
Stick Welding
Stick welding, also known as Shielded Metal Arc Welding (SMAW), is a highly flexible welding method that uses a consumable electrode coated with flux. It’s particularly well-suited for outdoor and industrial applications due to its ability to perform well in less-than-ideal conditions, such as wind or rain.
Electrode Selection
The choice of electrode plays a significant role in determining the weld characteristics and the required amperage. Common electrodes include:
6010: Designed for deep penetration, making it ideal for structural work or welding through rusted or painted materials. It requires higher amperage for optimal performance.
6013: Provides less penetration and is suitable for thin materials or less critical applications. This electrode works well with lower amperage settings.
7018: Known for its smooth, strong welds and high tensile strength, it’s used for critical applications like bridges or pressure vessels. This electrode requires precise amperage control and is often used with DC current for optimal performance.
Amperage Adjustments
Operators adjust amperage settings based on the following factors:
Material Thickness: Thicker materials require higher amperage for sufficient penetration, while thinner materials need lower amperage to avoid burn-through.
Welding Position: Different positions (horizontal, vertical, or overhead) require specific amperage adjustments to maintain control of the weld puddle and prevent dripping or spatter. For example, vertical welding often requires lower amperage to keep the molten metal from sagging.
TIG Welding
TIG (Tungsten Inert Gas) welding offers unparalleled precision and is often used for tasks that demand clean, high-quality welds. It employs a non-consumable tungsten electrode and requires careful control of heat and amperage.
Foot Pedal Control
A foot pedal allows operators to adjust amperage in real-time during the welding process, providing greater control over heat input. This is particularly useful for applications involving varying material thicknesses or intricate weld paths. The pedal offers the ability to start with low amperage to create the arc and gradually increase it for optimal penetration, then reduce it again to finish the weld cleanly.
Peak Amperage Settings
Many TIG machines allow operators to set a peak amperage 40–50% above the expected operating range. This ensures sufficient power for challenging weld sections, such as thick or heat-dissipating materials like aluminum.
Background Amperage
Some advanced TIG machines offer background amperage settings, which allow operators to adjust the baseline amperage used to sustain the arc during low-power phases. This is useful for applications requiring precise control over heat input, such as welding thin or delicate materials. Background amperage is often used in conjunction with pulse settings, which alternately increase and decrease the amperage to control heat input and minimize distortion in thin materials.
Key Takeaways for Each Welding Process
MIG welding relies on variable voltage to control arc characteristics, with wire feed speed adjusted to maintain filler delivery. Thin materials require low voltage to prevent burn-through, while thicker materials need higher voltage for penetration. Stick welding amperage settings are closely tied to electrode type, material thickness, and welding position. Common electrodes like 6010, 6013, and 7018 have specific amperage requirements based on their intended application. TIG welding offers precise control of heat and amperage through foot pedals and advanced machine settings like peak and background amperage. It is ideal for high-precision tasks requiring clean, defect-free welds, such as welding aluminum or thin materials. Understanding these processes and how their settings impact weld quality will help operators achieve the desired results for a wide range of materials and applications.
Practical Tips for Optimizing Amperage and Voltage
Selecting the right amperage and voltage settings is crucial for achieving high-quality welds and ensuring safe, efficient operation of your welding machine. Here’s an expanded guide to help you optimize these settings for various materials and applications.
Start with Manufacturer Recommendations
Welding machine manufacturers and electrode producers provide detailed guidelines for amperage and voltage based on material type, thickness, and electrode specifications. These recommendations serve as a reliable starting point, reducing trial and error. Check the machine’s user manual for recommended settings. Refer to electrode packaging for amperage and voltage ranges. Many electrodes, such as stick welding rods, include a chart outlining optimal settings. Always adjust settings slightly to accommodate environmental factors such as humidity, temperature, and the condition of the base material (e.g., rusted or painted surfaces).
Test on Scrap Material
Testing on scrap material lets you evaluate how your chosen settings affect penetration, bead quality, and overall weld integrity without risking damage to critical parts. Ensure the weld penetrates adequately without burning through the material. Check for smooth, uniform beads with minimal spatter. Verify that the weld has fused properly with the base material. Use scrap pieces that closely match the actual material and thickness of your project. If welding thin materials, pay particular attention to preventing burn-through, while for thicker materials, check for sufficient depth of penetration.
Consider Duty Cycle
The duty cycle refers to the percentage of time a welding machine can operate within a 10-minute period without overheating. For instance, a machine with a 60% duty cycle at 200 amps can weld continuously for 6 minutes, followed by a 4-minute cooldown period. Operating the machine beyond its duty cycle can lead to overheating, triggering automatic shutdowns or damaging the equipment. Use lower amperage for tasks requiring long continuous welds to extend the duty cycle. For high-amperage tasks, plan for pauses between welds to allow the machine to cool down. Industrial-grade welders often have higher duty cycles, making them better suited for prolonged, high-amperage tasks like pipeline welding or structural work.
Use Charts for Guidance
Welding amperage and voltage charts provide a quick reference for matching settings to material type, thickness, and electrode diameter. These charts eliminate guesswork and save time during setup. Common sources include welding machine manuals, electrode packaging, and online resources and welding community forums. Most charts include factors like base material type (e.g., steel, aluminum), electrode size (e.g., 1/8 inch or 3/32 inch), and welding position (e.g., flat, vertical, overhead).
Monitor Weld Quality
The appearance and characteristics of the weld bead provide immediate feedback on whether your amperage and voltage settings are correct. A smooth, consistent bead indicates proper settings. Irregular beads may suggest too high or too low amperage. Adequate penetration ensures the weld fuses deeply with the base material. Shallow penetration may indicate insufficient amperage, while excessive penetration can weaken the material. Excessive spatter or undercutting along the edges of the weld bead suggests settings need adjustment. Spatter is often caused by high voltage, while undercutting may result from incorrect electrode angles or amperage. Make small incremental changes to amperage and voltage until you achieve the desired bead quality and penetration.
Additional Tips for Success
Understand material properties as different metals (e.g., aluminum, carbon steel, stainless steel) respond differently to heat. Adjust amperage and voltage to suit the material’s thermal conductivity and melting point. Maintain a steady travel speed and electrode angle to complement your machine settings and ensure uniform welds. Inspect your machine, cables, and electrodes regularly to ensure they are in good condition, as worn or damaged components can affect performance. Keep a log of successful settings for specific materials and projects to streamline future tasks and reduce setup time. For complex or challenging tasks, consult welding experts or community forums for guidance on optimal settings and techniques.
By following these practical tips and continuously refining your settings based on weld performance, you can achieve strong, high-quality welds with efficiency and confidence.
Conclusion
Selecting the proper amperage and voltage for welding requires consideration of multiple factors, including base material, application, and electrode type. Each welding process—MIG, TIG, and stick—has unique requirements and settings that influence the quality and efficiency of the weld. By understanding these variables and practicing with your equipment, you can master the art of setting up your welding machine for any job.
Additional Resources
Get your welding gear here.
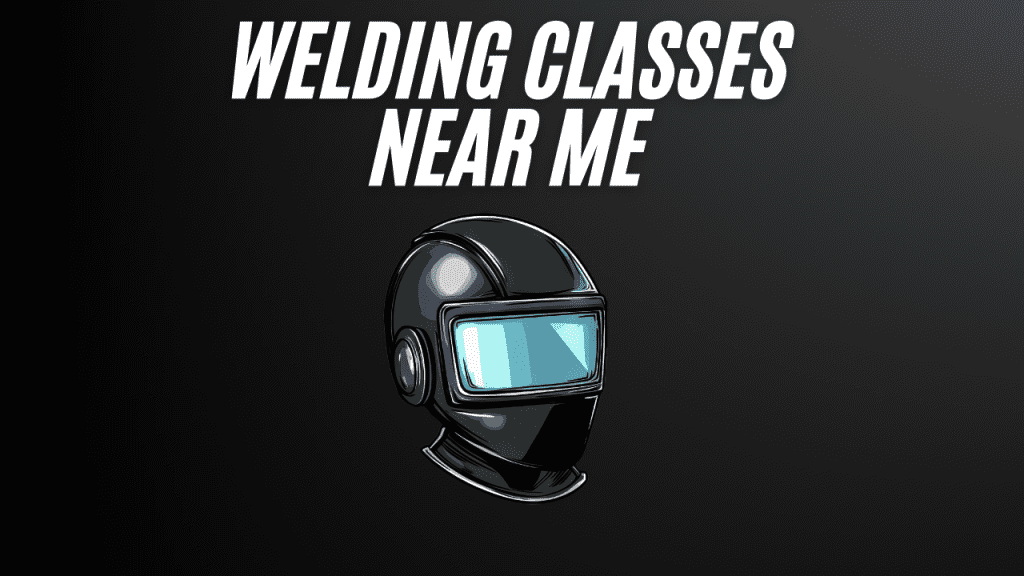