Table of Contents
TL;DR
A 7000-watt generator can run many welders, but compatibility depends on the welder’s voltage, amperage, and starting power requirements. It’s crucial to match the generator’s output with the welder’s demands to ensure smooth operation.
Will a 7000 Watt Generator Run a Welder?
Introduction
The question of whether a 7000-watt generator can run a welder often arises for those who need portable power for welding projects. The answer depends on several factors, including the welder’s power requirements, the generator’s capacity, and how they interact. Understanding these factors ensures you avoid damaging equipment and maintain safe operations.
Understanding Generator Wattage
Rated vs Surge Wattage
Generators have two wattage ratings: Rated Wattage and Surge Wattage.
Rated Wattage
Rated wattage is the continuous power a generator can supply without interruption. It reflects the generator’s steady-state performance and its ability to consistently power devices over an extended period. For example, if a generator is rated for 7000 watts, it can continuously provide up to 7000 watts of power for as long as there is fuel and proper maintenance. This steady capacity is critical for welders, as a welder’s continuous power demand must remain within this limit to avoid overloading the generator.
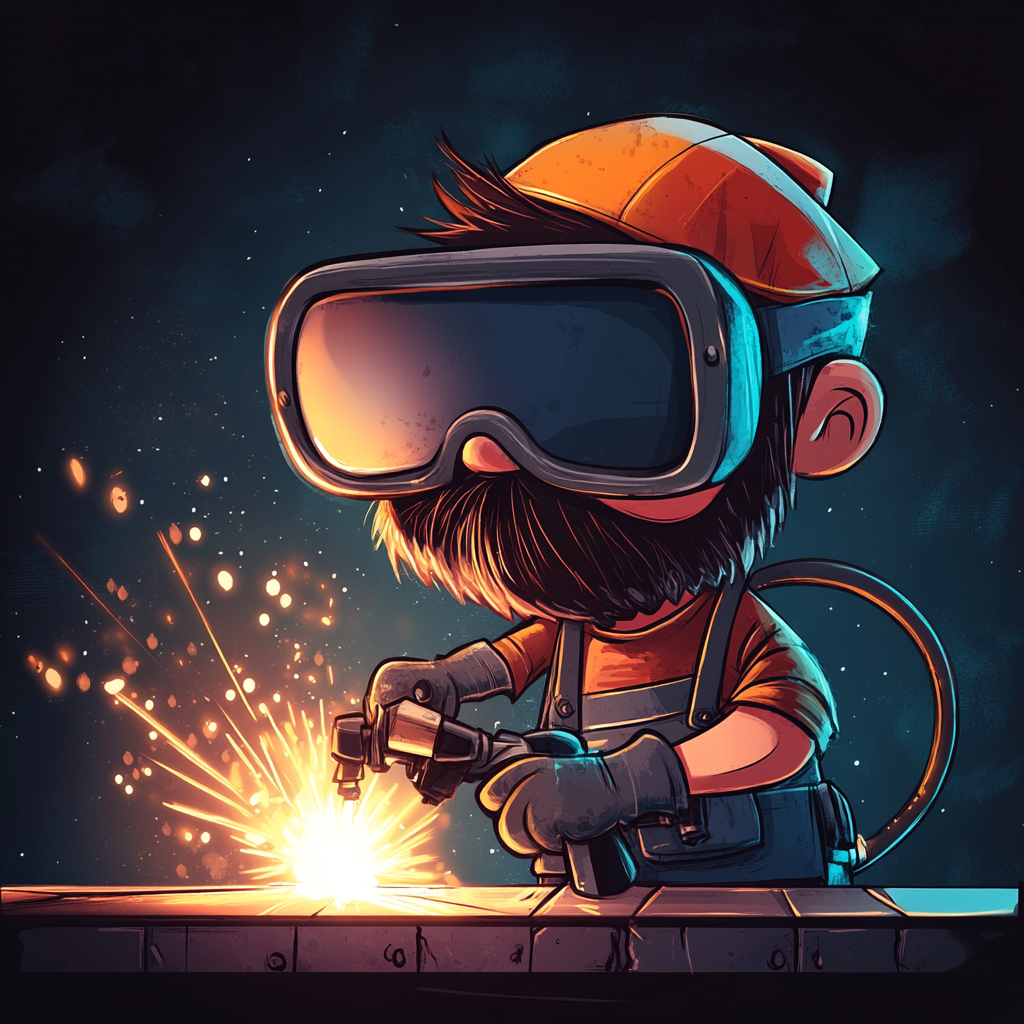
Surge Wattage
Surge wattage, sometimes called peak wattage, refers to the additional power a generator can supply for a short duration—usually a few seconds. This extra power accommodates the initial surge of electricity required by some devices when starting up. Welders, for instance, may draw significantly more power at startup than during normal operation, making surge wattage a key consideration.
A 7000-watt generator might have a surge capacity of around 8000 to 8500 watts. This temporary boost is essential to prevent the generator from tripping or failing when the welder starts. However, if the surge demand exceeds the generator’s capability, the equipment may fail to start or cause an overload, potentially leading to equipment damage or operational downtime.
Matching Wattage to Equipment
To ensure compatibility between a generator and a welder, it’s important to compare the generator’s rated and surge wattages with the welder’s requirements:
- Rated Wattage Alignment: The welder’s continuous wattage demand should be less than the generator’s rated wattage. For example, if a welder requires 6500 watts to run, a 7000-watt generator provides sufficient headroom for steady operation.
- Surge Wattage Alignment: The generator’s surge wattage should exceed the welder’s startup demands to prevent operational issues.
Risks of Overloading
Operating a generator beyond its rated capacity can lead to serious consequences:
- Overheating: Continuous overloading generates excess heat, which can damage the generator’s internal components.
- Mechanical Wear: Pushing a generator beyond its designed capacity accelerates wear and tear, shortening its lifespan.
- Voltage Fluctuations: Overloading may cause inconsistent power output, which can damage sensitive welding equipment or result in poor-quality welds.
Choosing the Right Generator
Selecting a generator with a margin above your welder’s requirements ensures reliability and safety. A generator’s rated wattage should comfortably handle the welder’s continuous load, while its surge wattage must accommodate the initial power spike during startup. This extra capacity reduces strain on the generator and prolongs its operational life.
Key Factors to Determine Compatibility
Expanded Section: Key Factors to Determine Compatibility
Welder Power Requirements
Welders can vary widely in their power needs, making it essential to understand the specific requirements of your welding equipment. The following considerations are crucial:
- Voltage: Most welders operate at either 120V or 240V, with the voltage often dictating the equipment’s power range and application.
- 120V Welders: Typically smaller, portable models designed for light-duty tasks, such as home repairs or small projects. These welders are compatible with standard household outlets.
- 240V Welders: Larger, more powerful units used for heavy-duty tasks, requiring a dedicated 240V outlet to handle their power demands.
- Amperage: Welders’ amperage requirements depend on the model and intended use.
- Smaller welders may need 20-30 amps.
- Industrial-grade welders can draw up to 50 amps or more.
- Wattage Calculation: To calculate wattage, multiply voltage by amperage. For example:
- A 120V welder drawing 20 amps requires 2,400 watts.
- A 240V welder drawing 30 amps needs 7,200 watts.
- Knowing these values ensures you choose a generator capable of meeting both the continuous and surge power requirements.
Generator Output
A generator’s output must align with the welder’s power demands to ensure efficient and safe operation.
- Rated Wattage: This represents the continuous power a generator can supply without interruption. A 7000-watt generator is generally suitable for welders requiring up to 6500 watts for steady operation, providing a margin for safety and reliability.
- Surge Wattage: Generators also have a surge capacity for handling temporary power spikes. This is crucial for welders, which often draw significantly more power during startup. Ensure the generator’s surge wattage exceeds the welder’s initial demand.
Ensuring Clean and Stable Power
Welding equipment is sensitive to power fluctuations, which can result in poor weld quality or damage to internal components. To ensure compatibility:
- Voltage Regulation: Choose a generator with built-in voltage regulation or stabilization to provide consistent output.
- Inverter Technology: Generators with inverter technology offer cleaner power, reducing the risk of damage to sensitive electronics in the welder.
Matching the Generator to the Welder
To determine compatibility, compare the welder’s power requirements to the generator’s output:
- Continuous Power: Ensure the generator’s rated wattage is higher than the welder’s steady-state power needs.
- Startup Surge: Verify the generator’s surge capacity meets or exceeds the welder’s startup wattage.
- Power Supply Type: Match the generator’s output voltage (120V or 240V) to the welder’s input.
By understanding and matching these key factors, you can ensure reliable and safe operation of your welder with a 7000-watt generator.as fluctuations can affect welding performance and equipment lifespan.
Types of Welders a 7000-Watt Generator Can Power
Smaller Welders (120V)
A 7000-watt generator is more than capable of running most 120V welders, making it an excellent choice for portable and light-duty welding tasks. Here are the common types of smaller welders it can power:
- MIG Welders:
- Applications: These welders are widely used for automotive repairs, metal fabrication, and hobby projects. They excel at welding thinner materials like mild steel, aluminum, and stainless steel.
- Power Requirements: MIG welders operating at 120V typically require around 2,000 to 2,400 watts of continuous power, making them well-suited for a 7000-watt generator.
- Advantages: Their user-friendly nature and compatibility with household outlets make them ideal for beginners and DIY enthusiasts.
- Stick Welders:
- Applications: Stick welders are versatile and can handle a range of materials, including steel and cast iron. They are often used for basic construction, maintenance, and repair work.
- Power Requirements: Most 120V stick welders draw between 2,000 and 3,000 watts during operation. A 7000-watt generator provides ample capacity for these units.
- Advantages: Their robust design and ability to perform well in outdoor or less-than-ideal conditions make them a popular choice for fieldwork.
Medium-Sized Welders (240V)
For 240V welders, a 7000-watt generator can power certain medium-sized models, provided their power demands are within the generator’s capacity. Compatibility depends on the specific welder’s requirements:
- TIG Welders:
- Applications: Known for their precision, TIG welders are commonly used for intricate tasks like welding aluminum, stainless steel, and other non-ferrous metals. These welders are ideal for automotive work, aerospace projects, and custom metal fabrication.
- Power Requirements: Medium-sized TIG welders running on 240V often require 6,000 to 6,500 watts of continuous power. This fits within a 7000-watt generator’s rated output, though you should confirm the surge requirements.
- Advantages: TIG welders produce high-quality, precise welds, making them a favorite for professionals who prioritize aesthetics and durability.
- Stick Welders:
- Applications: Larger stick welders operating at 240V are commonly used for structural welding, heavy equipment repair, and industrial applications.
- Power Requirements: These welders may demand 5,000 to 6,500 watts during operation. A 7000-watt generator can handle such units, provided their surge requirements do not exceed the generator’s capacity.
- Advantages: Their ability to weld thicker materials and work in challenging environments makes them a reliable choice for professionals.
Verifying Compatibility
To ensure the 7000-watt generator can effectively power your welder:
- Check Power Demands: Refer to the welder’s specifications for continuous and surge wattage requirements.
- Consider Runtime Needs: Prolonged operation at high loads can strain the generator; ensure you allow for cooling periods as needed.
- Evaluate Voltage Requirements: Match the generator’s output (120V or 240V) to the welder’s input to avoid mismatched connections.
By understanding the capabilities of your 7000-watt generator and the specific requirements of your welder, you can confidently tackle a variety of welding projects without interruption or damage to your equipment.
Limitations of a 7000-Watt Generator
High Starting Wattage
One of the primary limitations of a 7000-watt generator is its ability to handle the initial power surge required by some welders during startup. Welders, especially larger or industrial-grade models, often demand significantly more wattage when they first power on. For example:
- Surge Power Requirements: While a welder may need 6,500 watts for steady operation, its startup surge might exceed 8,000 watts. If the generator’s surge capacity falls short, the welder may fail to start, causing interruptions or potentially damaging both the generator and the equipment.
- Mitigation Tips:
- Choose welders with lower startup demands or invest in a generator with higher surge wattage.
- Use soft-start or power assist devices to reduce the initial power draw.
Continuous High Loads
Operating a 7000-watt generator near or at its maximum capacity for extended periods can lead to overheating and accelerated wear and tear. This can result in:
- Overheating: Generators produce heat during operation, and running continuously at high loads increases the risk of overheating. Overheating can damage internal components and reduce the generator’s lifespan.
- Mechanical Stress: Prolonged strain on the generator’s engine and alternator can lead to mechanical failures or increased maintenance requirements.
Best Practices to Avoid Issues
- Limit runtime at maximum capacity to short periods, allowing the generator to cool down between uses.
- Opt for a generator with a higher rated wattage if continuous high loads are unavoidable.
Voltage Drops
Inconsistent power delivery is another challenge when using a 7000-watt generator for high-demand welding tasks. Voltage drops can occur due to:
- Fluctuating Loads: Sudden changes in power demand during welding can cause voltage to dip, impacting the quality of the weld.
- Generator Overload: Running the generator beyond its rated capacity can result in unstable voltage output.
Consequences of Voltage Drops
- Poor weld penetration or uneven beads due to inconsistent power supply.
- Potential damage to the welder’s internal electronics, especially for models sensitive to power fluctuations.
Solutions to Minimize Voltage Drops
- Use a generator with built-in voltage regulation or add an external stabilizer to ensure steady output.
- Reduce the load on the generator by disconnecting non-essential devices.
While a 7000-watt generator is versatile and capable of powering many welders, its limitations must be carefully considered. Understanding and addressing these challenges—such as high startup wattage, continuous high loads, and voltage drops—can help maximize the generator’s performance and protect your equipment.
For demanding welding tasks, consider upgrading to a generator with higher capacity or additional features to ensure reliable and consistent operation.
Tips for Using a Generator with a Welder
Proper Setup
Ensuring your generator is properly set up to power your welder is critical for safety and efficiency. Follow these guidelines to optimize the setup:
- Match Voltage and Amperage Requirements: Verify that the generator’s output matches the welder’s input requirements. For example, if the welder operates at 240V and requires 30 amps, ensure the generator is capable of supplying this power consistently.
- Use the Right Extension Cord:
- Select a heavy-duty extension cord rated for welding applications.
- Ensure the cord is appropriately sized for the welder’s voltage and amperage to avoid power loss or overheating.
- Keep the cord as short as possible to minimize resistance and voltage drops.
- Ground the Generator: Proper grounding prevents electrical hazards and ensures safe operation. Follow the manufacturer’s instructions to correctly ground your generator.
Generator Maintenance
Regular maintenance is essential to keep your generator running smoothly and providing stable power. Key maintenance practices include:
- Service Schedule: Follow the generator’s recommended maintenance schedule for oil changes, air filter cleaning, and spark plug replacement.
- Fuel Management:
- Monitor fuel levels during operation to prevent the generator from running out of fuel.
- Use fresh, high-quality fuel and stabilize it if storing the generator for extended periods.
- Drain fuel from the tank and carburetor if the generator will be unused for long durations to prevent clogging.
- Inspect Components: Regularly check the generator’s components, such as wiring, outlets, and circuit breakers, for signs of wear or damage. Address any issues promptly to prevent failures.
Voltage Stabilizers or Inverters
Fluctuations in power output can negatively impact welding quality and damage sensitive equipment. To ensure consistent performance:
- Use Voltage Stabilizers: These devices regulate the generator’s output, maintaining steady voltage levels even during fluctuations in load demand.
- Consider Inverter Generators: Inverter generators produce cleaner, more stable power compared to conventional models, making them ideal for welders with sensitive electronics.
- Avoid Overloading: Keep the generator’s load within its rated capacity to maintain voltage stability. Disconnect non-essential devices to prioritize the welder’s power needs.
Additional Tips for Efficient Operation
- Allow Warm-Up Time: Before starting your welder, let the generator run for a few minutes to stabilize its output.
- Cool Down After Use: Avoid turning off the generator immediately after heavy use. Let it run without load for a few minutes to cool down gradually.
- Store Properly: When not in use, store the generator in a dry, ventilated space to protect it from moisture and dust.
Using a generator with a welder requires careful preparation and regular maintenance to ensure reliable and safe operation. By matching voltage and amperage requirements, using proper equipment, and maintaining the generator, you can optimize performance and extend the lifespan of both the generator and the welder. Investing in voltage stabilizers or inverter generators can further enhance stability, providing a seamless welding experience.
Alternative Solutions
Consider the Wattage Requirements
The generator’s maximum output plays a pivotal role in determining its compatibility with your welder. Ensuring the generator meets the power requirements of your welding equipment helps prevent performance issues or damage to the welder.
Different welders have varying power demands based on their amperage and application. Below are general wattage guidelines:
130 Amp Welders
- A generator rated at 7 kVA (kilovolt-amperes) is suitable for welders operating at this amperage. These welders are typically used for light-duty tasks and smaller-scale projects.
250 Amp Welders
- A generator rated at 15 kVA or higher is necessary for welders with higher amperage requirements. These models are ideal for heavy-duty and industrial applications.
Key Features to Look For in Generators
To ensure compatibility and optimal performance, prioritize generators with the following features:
Low THD
- Generators with Total Harmonic Distortion (THD) rates below 6% provide cleaner power. Clean power minimizes electrical surges and protects sensitive components in the welder, particularly in inverter models.
Voltage Regulation
- Consistent voltage output is essential to maintain welding quality. Voltage regulation reduces the risk of weld defects caused by fluctuating power.
High-Quality Components
- Investing in a reliable generator with durable components minimizes the risk of frequent breakdowns or maintenance issues. High-quality builds ensure long-term, dependable operation.
Matching your generator’s wattage to your welder’s requirements and investing in key features such as low THD and voltage regulation ensures efficient and safe operation. By following these guidelines, you can protect your equipment and achieve consistent welding performance in any setting.
Inverter Generators
Inverter generators are an excellent alternative for welders with sensitive electronics or those requiring stable, clean power. These generators utilize advanced technology to deliver consistent voltage and frequency, making them ideal for modern welding equipment.
Key Advantages of Inverter Generators
Cleaner Power Output
- Inverter generators produce a pure sine wave output, which closely mimics the clean power from a standard electrical grid. This minimizes the risk of power fluctuations that can damage sensitive welders or result in poor-quality welds.
- They are particularly suitable for welders like inverter TIG machines, which demand stable and precise power.
Efficiency
- Unlike conventional generators, inverter generators adjust their engine speed based on the load demand. This results in:
- Improved Fuel Efficiency: Reduced fuel consumption under lighter loads, leading to lower operating costs.
- Quieter Operation: Lower noise levels, making them more suitable for work environments where excessive noise can be disruptive.
Compact Design
- Many inverter generators are designed to be lightweight and portable, offering enhanced mobility. This makes them an excellent choice for welders who frequently work on-site or need a power source they can easily transport.
Suitability for Precision Welding
- Precision welding tasks, such as those performed with TIG welders, benefit from the stable and consistent power output provided by inverter generators. This ensures high-quality, professional-grade welds.
Considerations When Using Inverter Generators
While inverter generators offer significant advantages, there are important factors to consider:
Limited Wattage
- Most inverter generators have a lower maximum capacity compared to conventional models. Ensure the generator you select meets your welder’s specific power requirements, particularly for heavy-duty tasks.
Higher Initial Cost
- Inverter generators tend to be more expensive upfront than conventional options. However, their fuel efficiency, portability, and ability to protect sensitive equipment often offset the initial investment over time.
Compatibility
- Not all welders are compatible with inverter generators. Check both the generator’s and welder’s specifications to confirm they can operate together without issues.
Conclusion
Inverter generators are an excellent choice for welders who prioritize clean, stable power and portability. Their advanced features and efficient performance make them particularly well-suited for precision welding tasks. However, selecting the right model and ensuring compatibility with your welding equipment are critical steps to maximizing their benefits.efits that can enhance your welding setup and ensure smooth, efficient operation.
Conclusion
A 7000-watt generator can run many welders, particularly smaller or medium-sized units with lower power requirements. However, always check your welder’s specifications and the generator’s capabilities to ensure compatibility. Taking precautions like proper setup and regular maintenance will help you achieve smooth, safe welding operations.
Additional Resources
Get your welding gear here.
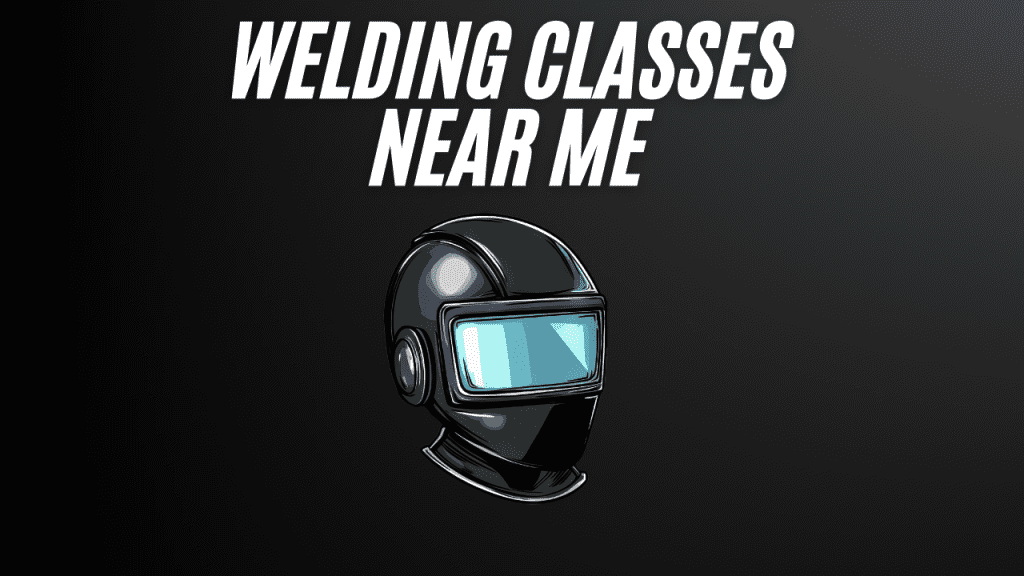