Table of Contents
Why Would You Use MIG Welding?
Introduction
MIG (Metal Inert Gas) welding is a widely used arc welding process that joins metals by feeding a continuous solid wire electrode through a welding gun directly into a weld pool. This method utilizes an inert shielding gas, such as argon, to protect the weld from environmental contaminants that could lead to defects. Its versatility and efficiency make MIG welding a staple in numerous industries and applications, ranging from aerospace to automotive and construction.
Below, we explore the industries that rely on MIG welding and why it has become an indispensable tool in modern manufacturing and repair processes.
Why Would You Use MIG Welding?
Industries that use MIG Welding
MIG welding is a versatile and efficient welding method utilized across various industries. Its ability to produce strong, durable welds on a wide range of materials has made it a staple in sectors like aerospace, automotive, and construction. Below is an in-depth look at how these industries rely on MIG welding and why it remains a preferred choice.
Aerospace Industry
MIG welding plays a crucial role in the aerospace industry, particularly in the manufacturing and maintenance of aircraft. Historically, gas welding was the go-to method for joining materials in aerospace applications until the 1950s. However, MIG welding quickly gained prominence because of its superior precision, strength, and ability to work effectively with lightweight metals like aluminum and stainless steel.
Aircraft components demand materials that are both lightweight and durable to ensure optimal performance and safety. Aluminum, a primary material in aerospace construction, pairs perfectly with MIG welding techniques due to its specific requirements for clean, high-quality welds. MIG welding allows for seamless joints and ensures the structural integrity of critical components like fuselage sections, wing panels, and fuel tanks.
In maintenance operations, MIG welding is frequently used to repair damaged parts efficiently without compromising their performance. The process’s speed and consistency make it ideal for keeping aircraft operational, reducing downtime, and ensuring safety standards are met.
Automotive Industry
The automotive industry heavily relies on MIG welding for both manufacturing and repair processes. It is used in numerous applications, including:
Repairing Vehicles: MIG welding is ideal for fixing damaged vehicle parts, including car bodies, motorcycle frames, and van panels. Its precision ensures a clean finish, maintaining the vehicle’s structural and aesthetic integrity.
Welding Sheet Metal: Automotive production involves significant use of aluminum, stainless steel, and mild steel, particularly for car frames and panels.
The automotive industry requires welding methods that can handle materials subjected to constant stress and environmental exposure. MIG welding’s flexibility allows it to create durable, corrosion-resistant welds that can withstand years of road use. Additionally, its ease of use and high welding speeds make it a cost-effective option for large-scale manufacturing.
Laser MIG Welding: The Future of Automotive Welding
An advanced variation of MIG welding, laser MIG welding, combines traditional MIG welding with laser beam technology. This hybrid process uses a laser beam to concentrate energy on a small area, allowing for deep penetration and faster processing. MIG welding adds filler material to the weld pool, ensuring a strong bond.
Advantages of Laser MIG Welding:
- Efficiency: Laser MIG welding processes welds faster, reducing production times significantly.
- Material Savings: It uses less filler material than traditional methods, making it more cost-effective.
- Precision: The laser beam ensures high-quality welds with minimal distortion, even on thin or intricate components.
The automotive industry is increasingly adopting laser MIG welding for modern vehicles, particularly for working with aluminum, which is becoming more prevalent due to its lightweight properties.
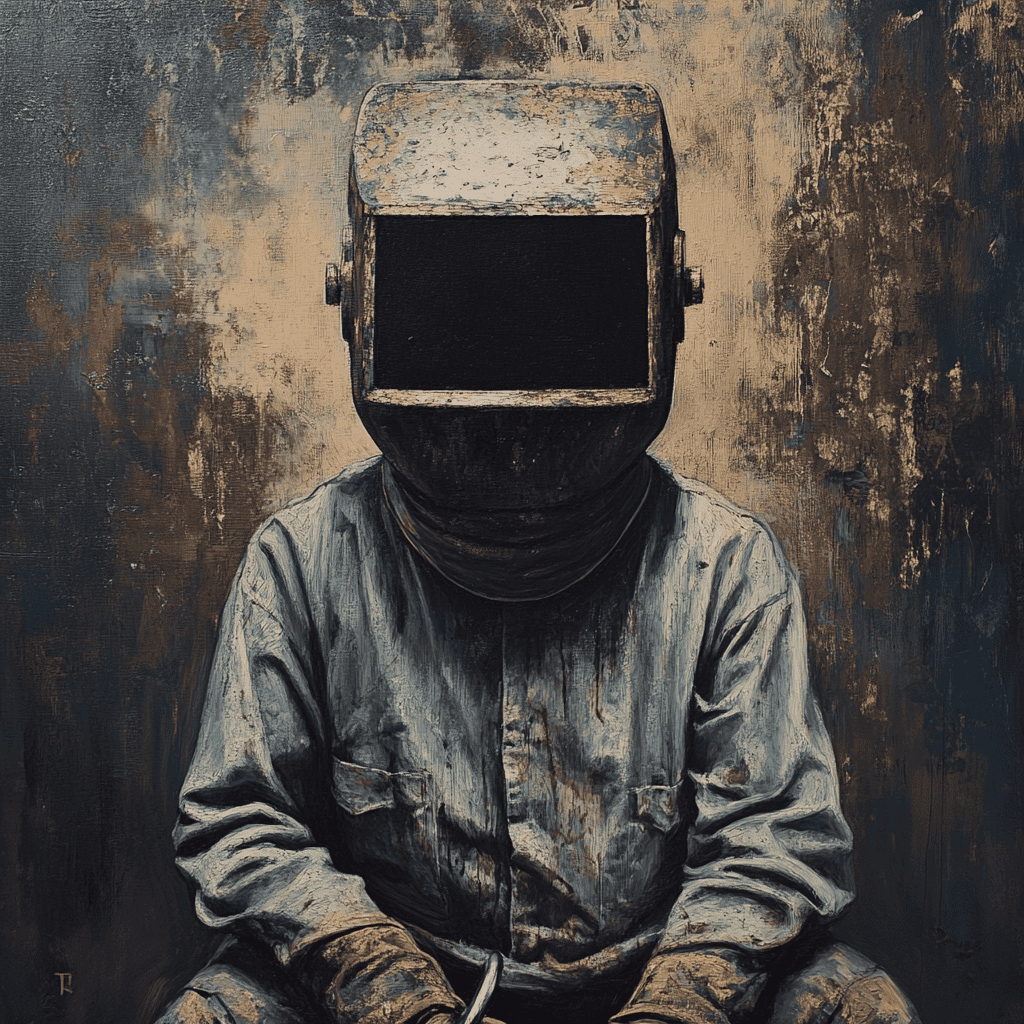
Construction and Infrastructure
The construction and infrastructure sectors heavily depend on MIG welding for fabricating and assembling essential structural components. As more than half of the world’s steel is used in construction, MIG welding has become a vital process for ensuring the durability and safety of buildings, bridges, and infrastructure.
MIG welding is renowned for its ability to handle diverse materials and provide strong, long-lasting welds. It is particularly effective for large-scale projects requiring consistent, reliable results. Key applications in construction include:
- Building structural frameworks.
- Fabricating rebar for concrete reinforcement.
- Creating durable bridges and industrial equipment.
Metals Used in Construction and Their Importance
Carbon Steel
Carbon steel is one of the most widely used materials in construction due to its exceptional durability, strength, and versatility. It is available in a range of grades, from mild carbon steel, which is easier to shape and weld, to high-carbon steel, which is harder and more resistant to wear. This variability allows engineers and builders to select the right grade for specific applications.
Applications
Structural Frameworks: Carbon steel is the backbone of modern construction. It is commonly used for beams, columns, and other load-bearing elements due to its high tensile and compressive strength.
Highway Plates and Infrastructure: Its durability makes it a popular choice for bridge plates, retaining walls, and highway guardrails, where strength and longevity are critical.
Rebar and Reinforcement: Carbon steel’s tensile strength and ability to bond with concrete make it ideal for reinforcing concrete structures, enhancing their durability under heavy loads.
Hollow Structural Sections (HSS): These sections, used for welded frames and trailer beds, offer a lightweight yet strong solution for transportation and industrial projects.
Copper
Copper is renowned for its excellent corrosion resistance, high conductivity, and recyclability, making it indispensable in various construction and infrastructure projects. Its malleability allows it to be easily shaped into pipes, wires, and other components, while its resistance to environmental factors ensures long-term reliability.
Applications
Piping Systems: Copper tubing is extensively used in plumbing for water supply, as well as in HVAC systems for refrigerant lines and heat exchangers. Its antimicrobial properties make it a preferred choice for potable water lines.
Electrical Wiring: Its superior conductivity and resistance to corrosion ensure efficient and safe power distribution in buildings.
Roofing and Flashing: In some high-end construction projects, copper is used for roofing and flashing, where its aesthetic appeal and weather resistance add value.
Recyclability: Copper is one of the most recycled materials in the construction industry, making it an eco-friendly choice that aligns with sustainability goals.
Aluminum
Aluminum’s combination of lightweight properties, resistance to corrosion, and high ductility makes it a popular choice for outdoor and structural applications. Its ability to withstand harsh weather conditions while maintaining structural integrity makes it especially valuable in construction.
Applications
Window Frames and Doors: Aluminum is widely used for modern window frames and doors, providing strength without adding excessive weight.
Streetlights and Signage: Its corrosion resistance ensures long-lasting performance in outdoor environments, even in areas exposed to moisture and pollution.
Structural Elements: Aluminum is often used in lightweight framing systems, curtain walls, and temporary structures due to its easy workability and high strength-to-weight ratio.
Transportation Infrastructure: Aluminum is also used in bridge construction and other transport-related structures where reduced weight can lead to significant cost savings.
Stainless Steel
Stainless steel is highly valued for its resistance to corrosion, staining, and wear, making it suitable for a wide range of structural and decorative applications. Its longevity and ability to retain its appearance over time have made it a material of choice for both functional and aesthetic purposes.
Applications
Architectural Cladding and Facades: Stainless steel provides a sleek, modern look while offering protection against weathering, making it a staple in contemporary building design.
Drainage Systems: Its corrosion resistance ensures the reliability and longevity of drainage systems in commercial and residential buildings.
Handrails and Balustrades: Stainless steel is a popular material for safety and decorative features in buildings, offering both strength and visual appeal.
Food-Grade and Sanitary Applications: In environments such as hospitals, kitchens, and food processing plants, stainless steel is used for its hygiene properties and ease of cleaning.
MIG Welding’s Role in Working with These Metals
MIG welding plays a crucial role in joining and fabricating these metals across various industries. Its ability to create durable, high-quality welds with minimal defects ensures that these materials perform optimally in their applications. The versatility of MIG welding allows it to adapt to the unique requirements of each metal, whether it’s welding thick carbon steel beams for structural frameworks, delicate copper tubing for HVAC systems, lightweight aluminum components for outdoor signage, or polished stainless steel for architectural elements.
This adaptability and efficiency ensure that MIG welding remains a cornerstone of modern engineering and manufacturing, enabling industries to meet the demands of durability, sustainability, and innovation.
Why Choose MIG Welding?
MIG welding (Metal Inert Gas welding) is one of the most versatile and efficient welding methods available, offering distinct advantages across a variety of industries. Its unique combination of ease of use, speed, versatility, and weld quality makes it a preferred choice for professionals and beginners alike.
Ease of Use
One of the most appealing aspects of MIG welding is its straightforward operation. The process involves feeding a continuous wire electrode through a welding gun, making it easier to control than other methods like TIG or stick welding. This simplicity makes MIG welding an excellent option for beginners, as it requires minimal training to produce satisfactory results. The automated wire feed system also eliminates the need for frequent stops to replace electrodes, which further simplifies the process and reduces errors.
Speed
MIG welding is renowned for its speed. The continuous wire feeding system enables welders to maintain a steady pace, significantly reducing the time required to complete projects compared to methods like stick welding. This advantage is particularly important in industries like automotive manufacturing and construction, where efficiency and productivity are crucial. The ability to weld quickly without sacrificing quality allows MIG welding to meet the high demands of large-scale production.
Versatility
MIG welding stands out for its ability to work with a wide range of metals and material thicknesses. It is compatible with materials such as aluminum, stainless steel, mild steel, and copper, making it suitable for diverse applications across aerospace, automotive, and construction industries. This versatility means that welders can use a single machine to handle multiple tasks, from repairing thin sheet metal to fabricating heavy-duty structural components. Additionally, the adaptability of MIG welding extends to different welding positions, whether flat, horizontal, vertical, or overhead.
Quality
MIG welding produces high-quality welds with minimal spatter, ensuring clean and visually appealing results. The use of inert shielding gases like argon or a mixture of argon and carbon dioxide protects the weld pool from contamination, resulting in stronger, defect-free welds. This level of precision and reliability makes MIG welding ideal for applications where the appearance and integrity of the weld are critical, such as automotive bodywork and architectural elements.
The Role of MIG Welding in Sustainability
MIG welding is not only efficient but also contributes to sustainability efforts in manufacturing and construction. By maximizing material usage and reducing waste, MIG welding aligns with modern eco-conscious practices. Here’s how:
Efficient Material Usage
The continuous wire feeding system ensures that filler material is used optimally, reducing wastage compared to other welding methods. This efficiency is particularly valuable in industries that work with expensive metals like aluminum and copper.
Recycling Capabilities
MIG welding is compatible with recyclable metals, such as aluminum and steel, making it a key process in sustainable manufacturing. The ability to repair and reuse existing components further minimizes the need for new raw materials, reducing the environmental footprint of production processes.
Reduced Energy Consumption
Compared to traditional welding methods, MIG welding’s faster process times mean less energy is consumed per weld. This advantage is especially significant in large-scale industrial operations where cumulative energy savings can have a substantial environmental impact.
Cleaner Welding Process
The use of inert shielding gases minimizes the production of harmful fumes and spatter, resulting in a cleaner and safer work environment. This contributes to improved air quality in manufacturing facilities, protecting workers and reducing the need for additional ventilation equipment.
Why MIG Welding Remains a Cornerstone of Modern Manufacturing
The combination of ease of use, speed, versatility, and high-quality results makes MIG welding a cornerstone of modern manufacturing and construction. Whether you’re repairing an automobile, building a bridge, or fabricating aerospace components, MIG welding offers a reliable and efficient solution that meets the demands of precision and productivity. Its role in promoting sustainability further solidifies its relevance in a world increasingly focused on eco-friendly practices. As technology continues to evolve, advancements in MIG welding equipment and techniques will ensure its place as a leading welding method for years to come.
Conclusion
MIG welding is an essential process in industries ranging from aerospace to automotive and construction. Its ability to produce strong, durable, and clean welds on a variety of materials has cemented its place in modern manufacturing and repair work. Whether you’re building an aircraft, repairing a car, or constructing a skyscraper, MIG welding offers the reliability and versatility needed to get the job done efficiently and effectively. As advancements like laser MIG welding continue to emerge, this technique will remain at the forefront of innovation in welding technology.
Additional Resources
Get your welding gear here.
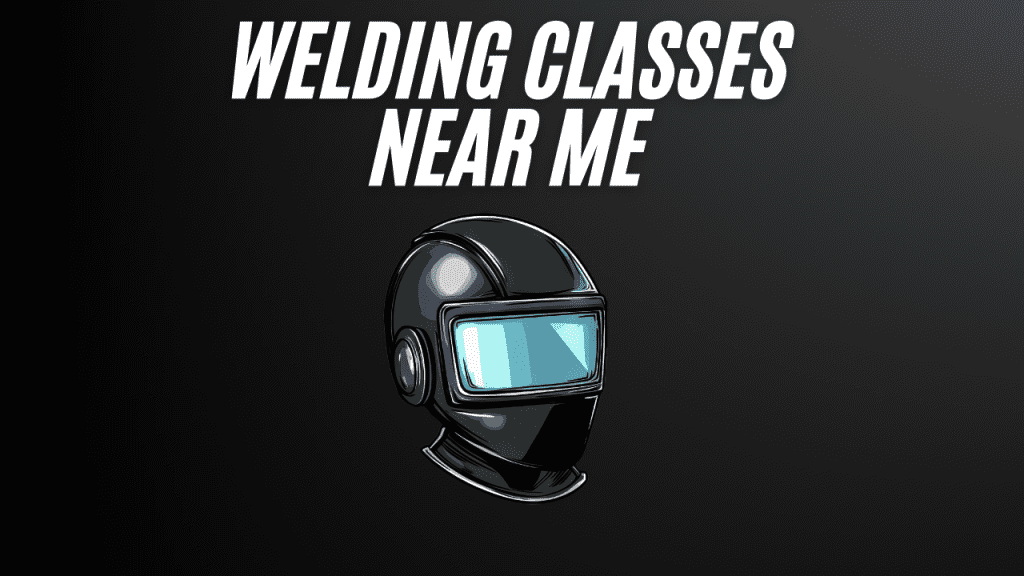