Table of Contents
TL;DR
Welders typically use specific plug types depending on their power requirements. Common options include standard household plugs for small welders (120V) and industrial-grade plugs, like NEMA 6-50 or NEMA 14-50, for higher-powered welders (240V). The type of plug depends on the welder’s voltage and amperage needs, as well as local electrical standards.
What Kind of Plug Does a Welder Use?
Introduction
Selecting the correct plug for a welder is crucial for ensuring optimal performance and safety. With a wide variety of welder types and power requirements, understanding the plug you need can save you time, money, and potential electrical issues. This guide breaks down the most common plug types and factors to consider when choosing one for your welder.
Understanding Welder Power Requirements
Voltage Options: 120V vs. 240V Welders
Welders operate on either 120V or 240V power supplies, depending on their size and intended use:
- 120V Welders: These smaller, portable units are ideal for hobbyists or light-duty welding. They can plug into standard household outlets, making them convenient for home use.
- 240V Welders: Designed for heavy-duty or industrial applications, these require higher voltage and special outlets to handle their power needs.
Amperage Considerations
The amount of current (amperage) your welder needs plays a critical role in determining the plug type. Larger welders often demand 40-50 amps, while smaller units may only require 15-20 amps. Using the wrong plug could lead to insufficient power or electrical hazards.
Common Plug Types for Welders
Standard Household Plug (120V)
For 120V welders, a standard NEMA 5-15 or 5-20 plug is sufficient. These plugs are compatible with typical home outlets and support up to 20 amps. They’re suitable for smaller welders used for DIY projects or light repairs.
- NEMA 5-15 Plug: This is the most common plug for household appliances and smaller welders. It fits into standard two-prong or three-prong outlets and is limited to 15 amps.
- NEMA 5-20 Plug: A slightly upgraded version of the NEMA 5-15, this plug is designed for up to 20 amps and features a horizontal prong for added stability. It’s ideal for welders requiring slightly more power but still within the 120V range.
- Suitability: These plugs make it easy to use welders in residential settings without needing specialized outlets or significant electrical upgrades.
NEMA 6-50 Plug (240V)
The NEMA 6-50 plug is one of the most commonly used for 240V welders. It’s designed to handle heavy power loads, making it ideal for most professional-grade welders.
- Design Features: This plug includes three prongs: two for the hot wires and one for the ground. The sturdy construction ensures durability under demanding welding conditions.
- Applications: NEMA 6-50 plugs are standard for medium-to-large welders used in workshops, garages, and industrial environments. They can handle up to 50 amps, making them suitable for welders with high power demands.
- Compatibility: Ensure your welder and outlet are specifically designed for this plug type to avoid any mismatched connections.
NEMA 14-50 Plug (240V)
A NEMA 14-50 plug is often used for larger welders or applications requiring multi-purpose outlets. It supports higher amperage, typically up to 50 amps, and includes four prongs for added grounding and safety.
- Four-Prong Design: Unlike the NEMA 6-50, this plug features an additional prong for a neutral connection. This setup allows for more versatile electrical use, including compatibility with some RVs and electric vehicle chargers.
- High-Amperage Needs: The NEMA 14-50 is ideal for welders that require stable, high-capacity power for prolonged use.
- Versatility: While primarily used for heavy-duty welders, this plug can also serve other high-power equipment, making it a flexible choice for workshops.
Other Plug Types
While less common, other plug types may be used for specialized welders or regional electrical standards.
- Twist-Lock Plugs: Found in some industrial settings, these plugs ensure a secure connection by twisting into place. They are often used for welders that need a highly stable power source.
- International Standards: Depending on your location, plugs like the IEC 60309 may be necessary. These are common in Europe and other regions for industrial-grade equipment.
- Custom Configurations: Some high-end or unique welders may require proprietary plug designs. Always check the manufacturer’s recommendations.
Consult your welder’s manual or an electrician to determine if a less common plug is needed for your specific setup.
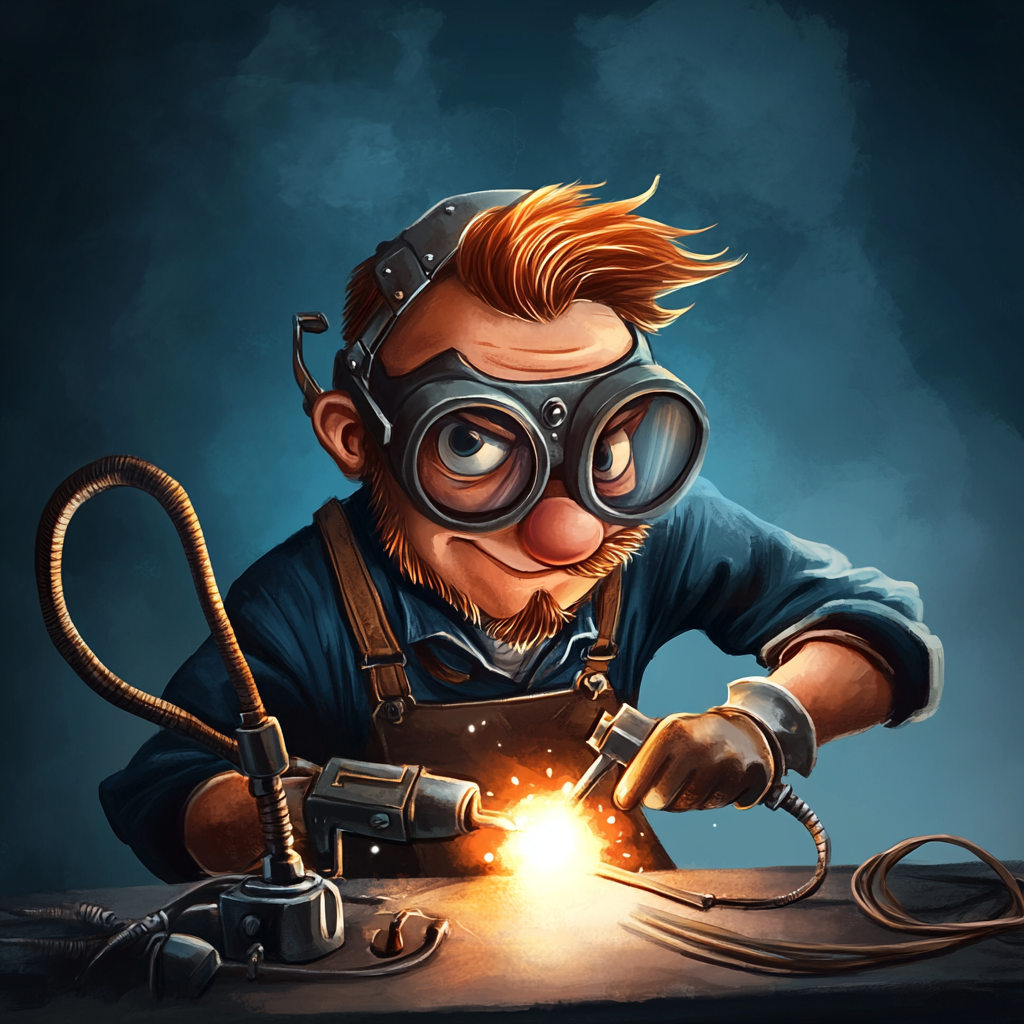
Factors to Consider When Choosing a Plug
Selecting the right plug for your welder is crucial for optimal performance, safety, and compliance. Here are the key factors to evaluate:
1. Welder Specifications
Understanding your welder’s power requirements is the first step in choosing the correct plug. These details are typically provided in the welder’s manual or on the machine’s nameplate and include:
- Voltage: Whether the welder operates on 120V, 240V, or dual-voltage.
- Amperage: The current draw of the welder, which determines the plug’s compatibility with your power source.
- Plug Type: Some welders specify a particular plug, such as NEMA 6-50 or NEMA 14-50.
Using an incompatible plug can lead to:
- Equipment Damage: Overheating, short circuits, or electrical surges.
- Underperformance: Insufficient power delivery can result in weak welds or inconsistent operation.
- Safety Hazards: Improper plugs increase the risk of electrical fires or shocks.
Double-check these specifications to ensure that the plug you choose aligns perfectly with your welder’s requirements.
2. Electrical Setup
Your home or workshop’s electrical system must be capable of safely powering your welder. Key considerations include:
- Circuit Breaker Ratings:
Ensure that the circuit breaker matches or exceeds the welder’s amperage requirements. For example:- A 50-amp welder requires a 50-amp breaker.
- Installing a breaker that is too small will cause frequent tripping.
- Oversized breakers may fail to trip during an overload, increasing fire risks.
- Outlet Compatibility:
Verify that your existing outlet matches the plug type for your welder. Common plug types include:- NEMA 6-50: Standard for most 240V welders.
- NEMA 14-50: Often used for high-amperage welders.
If your outlet doesn’t match, you may need to install a dedicated outlet for your welder.
- Wiring Capacity:
The wiring in your home or workshop must support the welder’s voltage and amperage. Check for:- Wire Gauge: For example, a 50-amp welder requires 6-gauge wire.
- Insulation Quality: Older or damaged wiring may need replacement.
- Length of Wiring: Longer wiring runs may require thicker wires to prevent voltage drops.
- Dedicated Circuit:
High-powered welders should ideally have their own circuit to avoid overloading shared circuits, which could disrupt other devices or create safety issues.
3. Local Electrical Codes
Adhering to local electrical codes ensures safety and avoids potential legal complications. These codes dictate the standards for wiring, outlets, and installation procedures.
- Wiring Standards:
Local codes specify:- Conductor sizes and materials, such as copper or aluminum.
- Insulation requirements for specific environments (e.g., damp basements or outdoor workshops).
- Outlet Placement:
Codes may mandate:- Minimum distances between outlets and water sources.
- Height requirements for outlets in residential and industrial spaces.
- Grounding Requirements:
Proper grounding is essential to prevent electrical shocks and ensure safe operation. This includes:- Grounded outlets (e.g., NEMA 6-50 plugs require grounding).
- Compliance with local grounding protocols, such as the use of ground rods or bonded metal components.
- Safety Protocols:
Local codes often include rules on circuit breakers, arc fault interrupters (AFIs), and ground fault circuit interrupters (GFCIs) for added safety.
Failure to comply with these codes could result in fines, insurance issues, or hazardous working conditions. It’s advisable to consult a licensed electrician or your local building authority to confirm compliance.
Summary
Choosing the right plug for your welder involves more than matching components; it requires careful consideration of the welder’s specifications, your electrical system’s capacity, and adherence to local codes. By addressing these factors, you can ensure safe, efficient, and legal operation of your welding equipment. When in doubt, consult a professional electrician to avoid costly mistakes and potential hazards.
Adapters and Alternatives
Using Adapters
Adapters can allow welders to connect to outlets with different plug configurations, providing flexibility in certain situations. However, adapters should be used with caution:
- Power Loss: Adapters can introduce resistance, leading to reduced power output and potential damage to the welder.
- Safety Risks: Improperly rated adapters may overheat or fail, creating a fire hazard.
- Temporary Solution: Use adapters as a short-term solution only; long-term use warrants proper outlet installation.
Extension Cords for Welders
When extension cords are necessary, use ones designed specifically for welding applications:
- Heavy-Duty Design: Look for cords rated for the welder’s voltage and amperage.
- Cable Length: Minimize cord length to reduce power loss and overheating risks.
- Durability: Choose cords with tough insulation to withstand workshop conditions.
Professional Installation and Safety Tips
Importance of Professional Wiring
Hiring a licensed electrician to install a dedicated welding outlet ensures that your setup meets safety standards and is tailored to your welder’s requirements. Professional installation offers:
- Correct Sizing: Ensuring the right wire gauge and breaker size.
- Compliance: Meeting all local electrical codes.
- Reliability: Reducing the risk of outages or equipment damage.
Safety Checks
Regular inspections can prevent accidents and prolong the life of your welding equipment:
- Visual Inspection: Check plugs, cords, and outlets for fraying, discoloration, or wear.
- Functional Testing: Test outlets and breakers periodically to ensure they are functioning correctly.
- Timely Repairs: Replace damaged components immediately to avoid electrical hazards.
By considering these factors and taking the necessary precautions, you can ensure a safe, efficient, and compliant setup for your welding needs.
Conclusion
Choosing the right plug for your welder is essential for performance, safety, and compliance with electrical standards. By understanding your welder’s power requirements and consulting local codes, you can ensure a reliable and efficient setup. When in doubt, seek professional guidance to make the best choice for your welding needs.
Additional Resources
Get your welding gear here.
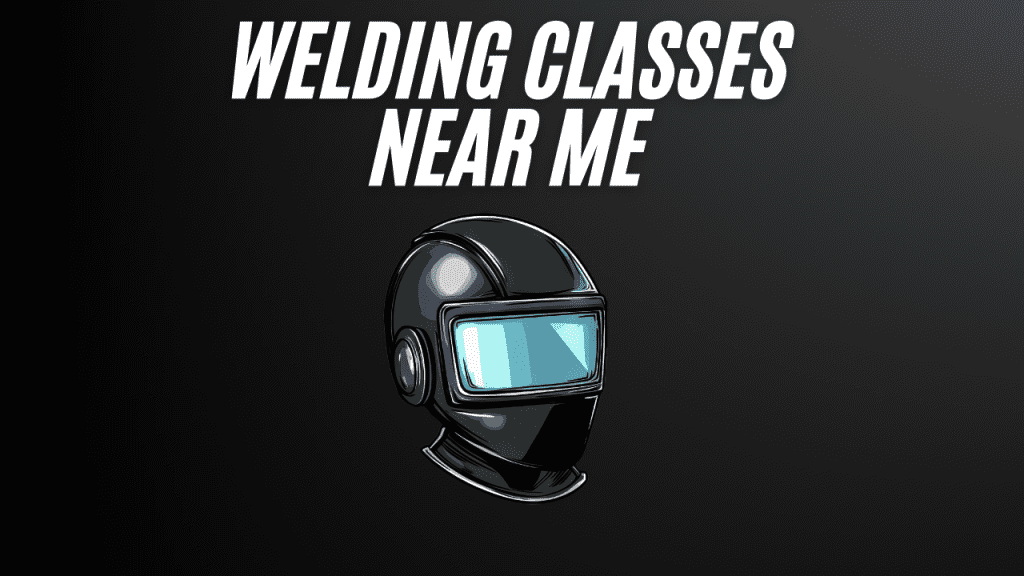