Table of Contents
What is Weld Penetration?
Weld penetration, also known as depth of fusion, refers to the distance the fusion line extends below the surface of the metal being welded. It is a critical parameter that determines the strength and quality of a weld. Achieving proper weld penetration ensures that the materials being joined form a strong bond capable of withstanding stress and loads.
Factors Influencing Weld Penetration
Welding Current
The welding current plays a major role in determining the depth of penetration:
- Higher Current: Increases penetration as more heat is generated, allowing the weld to fuse deeper into the base material.
- Lower Current: Reduces penetration and may lead to weaker joints.
Tip-to-Work Distance (CTWD)
The distance between the welding tip and the workpiece inversely affects penetration:
- Shorter Distance: Increases current and penetration.
- Longer Distance: Reduces current and penetration, making it a key factor in controlling weld depth.
Voltage
Voltage impacts weld penetration by influencing the arc’s spread:
- Higher Voltage: Creates a wider arc, leading to less penetration and a broader bead.
- Lower Voltage: Produces a narrower arc with greater penetration but can result in erratic arc behavior if set too low.
Travel Speed
The speed at which the welding gun moves along the joint affects the energy transferred to the base material:
- Faster Travel Speed: Reduces penetration as the arc spends less time on each section.
- Slower Travel Speed: Increases penetration but can cause overheating and excessive bead size.
Polarity
Polarity directly influences the distribution of heat in arc welding processes:
- Direct Current Electrode Positive (DC+): Focuses more heat on the base metal, resulting in deeper penetration.
- Direct Current Electrode Negative (DC-): Focuses heat on the electrode, reducing penetration.
- Note: This effect is reversed in TIG (GTAW) welding processes.
Welding Process
Different welding processes exhibit varying penetration characteristics:
- High Penetration Processes: SAW (Submerged Arc Welding), FCAW (Flux-Cored Arc Welding), and GMAW (Gas Metal Arc Welding) in spray, pulse, or globular transfer modes.
- Low Penetration Processes: GMAW in short-circuit mode and GTAW, depending on the electrode and settings.
Electrode Type
Electrodes significantly affect weld penetration:
- Deep Penetration Electrodes: E6010 for SMAW and E70T-1 for FCAW.
- Shallow Penetration Electrodes: E7024 for SMAW and E71T-1 for FCAW.
Shielding Gas
Shielding gas composition influences arc stability and heat conductivity:
- High Conductivity Gases: 100% CO₂ and 100% helium result in deeper penetration.
- Lower Conductivity Gases: Argon blends provide a smoother arc with shallower penetration.
Travel Angle
The angle of the welding gun affects how much arc force is directed into the base metal:
- Lower Angles: Increase penetration.
- Severe Angles: Decrease penetration, reducing weld depth.
Improving Weld Penetration
Improving Weld Penetration
Achieving proper weld penetration is essential for creating strong, durable welds. Here’s an expanded look at how to address common issues that impact penetration and their corresponding solutions:
Slow Wire Feed Speed
Issue: Insufficient wire feed speed limits the amount of filler material entering the weld pool, reducing energy transfer and penetration.
Solution: Increase the wire feed speed to ensure that enough material is deposited into the joint. This adjustment allows for better energy transfer from the arc to the base metal, resulting in deeper penetration. However, care must be taken not to set the speed too high, as it can cause excessive spatter and poor bead quality.
Additional Tip: Use welding charts or equipment settings provided by the manufacturer to determine the optimal wire feed speed for your specific wire type and material thickness.
Low Voltage
Issue: Low voltage leads to a weaker arc that cannot effectively penetrate the base material.
Solution: Adjust the voltage to a higher setting, which will create a more concentrated arc with greater heat intensity. This improves arc stability and enhances penetration.
Additional Tip: Ensure that the voltage increase is appropriate for the welding process and material. Overly high voltage can cause a wider, shallow bead instead of deeper penetration.
Excessive Wire Stick-Out
Issue: A long stick-out (the distance between the contact tip and the workpiece) increases electrical resistance, reducing arc energy and penetration.
Solution: Shorten the wire stick-out by positioning the contact tip closer to the workpiece. This reduces resistance, allowing more current to flow through the wire, which increases penetration.
Additional Tip: Maintain a consistent stick-out length during welding for uniform penetration and bead appearance. The ideal stick-out length varies depending on the wire diameter and welding process but is typically around 3/8 inch to 1/2 inch for MIG welding.
Thick Base Material
Issue: Welding thick materials without proper preparation or equipment can result in incomplete fusion and poor penetration.
Solution: Ensure that the material thickness is within the capacity of your welding process and equipment. For thicker materials, bevel the edges to create a groove for the weld. This allows the arc to reach deeper into the joint, ensuring full fusion.
Additional Tip: Use multi-pass welding for very thick materials. Each pass penetrates further into the joint, building up the weld for added strength and depth.
Fast Travel Speed
Issue: Moving the welding gun too quickly reduces the time the arc spends on each section of the joint, resulting in shallow penetration.
Solution: Slow down the travel speed to allow more heat and filler material to transfer into the base material. This ensures adequate melting and fusion for deeper penetration.
Additional Tip: Practice consistent, steady movement to maintain a uniform bead profile and avoid overheating the weld pool.
Poor Base Metal Preparation
Issue: Contaminants such as rust, oil, paint, or mill scale on the base material can prevent the arc from effectively melting and fusing the metal, leading to weak welds.
Solution: Thoroughly clean and prepare the base metal before welding. Use tools like wire brushes, grinders, or chemical cleaners to remove surface contaminants. For heavy-gauge materials, bevel the edges and increase the weld gap to allow better penetration.
Additional Tip: Consider preheating the base metal for thicker or high-carbon steels to reduce the cooling rate and improve fusion. Preheating also minimizes the risk of cracking in the heat-affected zone (HAZ).
Summary
By addressing these common issues, welders can significantly improve weld penetration, ensuring stronger and more reliable joints. Consistently evaluating and fine-tuning factors like wire feed speed, voltage, stick-out length, travel speed, and base metal preparation can optimize weld quality and meet project requirements effectively.
The Importance of Proper Weld Penetration
The Importance of Proper Weld Penetration
Weld penetration plays a critical role in determining the overall quality and reliability of a weld. Achieving the correct penetration ensures that the weld meets functional, aesthetic, and safety requirements. Here’s a closer look at why proper weld penetration is so essential:
Structural Integrity
Preventing Weak Points: Proper weld penetration ensures complete fusion between the base materials and any filler material, eliminating weak points that could compromise the structure. This is especially important in applications subject to high stress, such as bridges, pipelines, or load-bearing components in construction.
Load Handling: Adequate penetration allows the weld to distribute stress evenly, preventing localized failure. Without proper penetration, the weld may not withstand the loads and forces it was designed for, leading to structural failures that can have serious consequences.
Fatigue Resistance: Welds with proper penetration are less likely to fail under cyclic loading or repeated stress, which is crucial for components subjected to vibration or heavy usage, such as in automotive or aerospace industries.
Defect Reduction
Porosity Prevention: Proper penetration reduces the likelihood of voids or air pockets (porosity) in the weld, which can weaken the joint and make it prone to failure under stress.
Crack Resistance: Incomplete fusion or shallow penetration can lead to cracks, particularly in high-stress applications or materials with varying thermal properties. Correct penetration minimizes these risks by creating a uniform and cohesive joint.
Avoiding Incomplete Fusion: Insufficient penetration often results in incomplete fusion between the weld and the base materials, significantly reducing the strength and reliability of the joint. Proper welding techniques ensure complete melting and bonding of all components.
Code Compliance
Meeting Industry Standards: Many industries have strict standards for weld quality, strength, and durability, such as those set by the American Welding Society (AWS), ASME, or ISO. Proper penetration is often a mandatory requirement to meet these codes, especially for safety-critical applications like pressure vessels, pipelines, and structural frameworks.
Pass Inspections: Welds that lack proper penetration are more likely to fail visual, radiographic, or ultrasonic inspections, leading to costly rework or rejection of the project. Ensuring correct penetration helps welders avoid these issues and maintain high-quality results.
Certification and Accountability: Companies working in regulated industries must provide proof of compliance with weld specifications. Correct weld penetration ensures that projects meet certification standards, protecting the company from liability or legal repercussions.
Enhanced Performance and Longevity
Corrosion Resistance: Proper penetration helps create a uniform weld profile, reducing areas where moisture or corrosive agents could accumulate. This extends the lifespan of the structure or component.
Aesthetic Quality: While structural soundness is the priority, welds with proper penetration often appear smoother and more consistent, enhancing the visual quality of the finished product.
Cost Efficiency: Achieving proper penetration on the first attempt reduces rework, material waste, and inspection failures, saving time and money in the long run.
Summary
Proper weld penetration is a cornerstone of successful welding, ensuring the structural integrity, reliability, and compliance of welded components. By achieving the right depth of fusion, welders can reduce defects, meet industry standards, and enhance the overall performance and durability of their projects. Whether for critical infrastructure, industrial applications, or everyday repairs, the importance of proper weld penetration cannot be overstated.
Conclusion
Weld penetration is a critical factor in welding that affects the quality, strength, and reliability of the joint. By understanding and controlling variables like current, voltage, travel speed, and shielding gas, welders can achieve optimal penetration for their specific applications. Proper base metal preparation and adherence to best practices ensure that welds meet the required standards, resulting in durable and defect-free joints.
Additional Resources
Get your welding gear here.
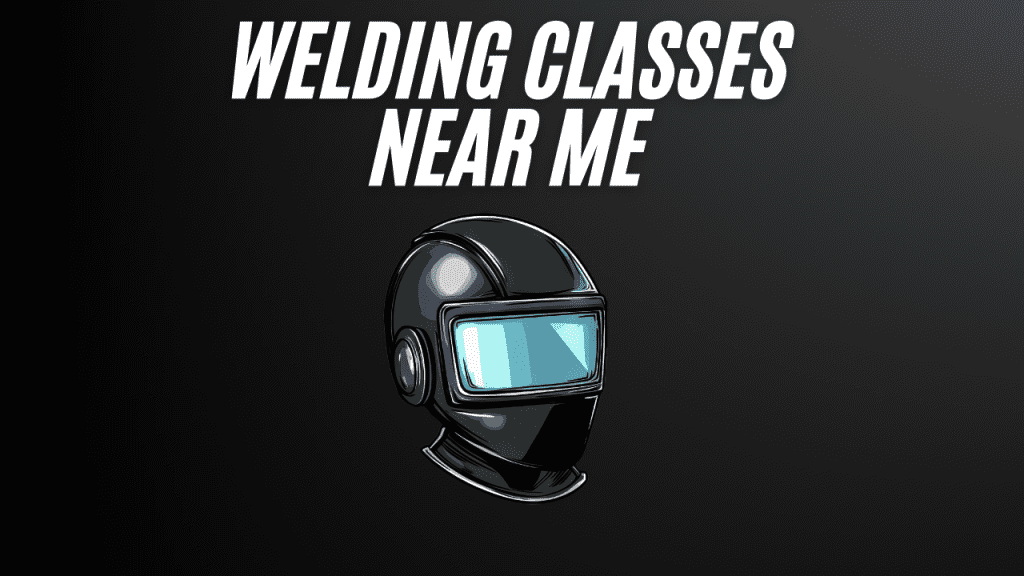