Table of Contents
What is the Difference Between Arc vs Tig Welding?
Arc welding and TIG (Tungsten Inert Gas) welding share fundamental similarities because TIG welding is actually a type of arc welding. Both rely on the principle of creating an electric arc to generate the heat needed to melt the base material and, if applicable, filler material. However, TIG welding is distinct due to its use of a non-consumable tungsten electrode and its precision.
Similarities Between Arc Welding and TIG Welding
Electric Arc as the Heat Source
At the heart of both arc welding and TIG welding is the electric arc, a highly concentrated source of heat. This arc is created by passing an electric current between an electrode and the workpiece, generating temperatures exceeding 5,000°F. This intense heat is sufficient to melt metals, forming a weld pool that allows materials to fuse together. This reliance on the electric arc is a foundational aspect of all arc welding processes, including TIG welding, and underscores their shared technological basis.
Shielding Gas Use (in Specific Types)
While traditional arc welding methods such as SMAW (Shielded Metal Arc Welding) rely on a flux coating on the electrode to create shielding gases during welding, TIG welding employs an inert shielding gas—most commonly argon. This gas flows continuously from a separate tank to shield the weld pool from contaminants like oxygen, nitrogen, and hydrogen in the atmosphere. In advanced arc welding techniques such as GMAW (Gas Metal Arc Welding or MIG welding), shielding gases are also used, bridging the gap between flux-based and gas-based shielding methods. Both approaches ensure the weld pool remains protected from defects such as porosity or oxidation.
Material Fusion
The primary goal of both arc and TIG welding is to achieve strong and durable material fusion. In traditional arc welding, a consumable electrode melts into the weld pool, contributing filler material directly. In TIG welding, the base metals are melted by the arc, and a separate filler rod may be used if additional material is needed. Both methods create a cohesive bond between metals, ensuring strength and structural integrity, though the precision of TIG welding often makes it preferable for detailed work.
Electric Current Types
Both methods offer flexibility in terms of the type of electrical current used. Direct Current (DC) is commonly employed for welding steels and other ferrous metals, providing a steady and concentrated arc. Alternating Current (AC), on the other hand, is used for materials like aluminum and magnesium in TIG welding, as it helps break down oxide layers on the metal surface for cleaner welds. This versatility in current type allows both methods to adapt to various materials and welding conditions.
Applications in Industrial and Commercial Settings
Arc and TIG welding are widely utilized across numerous industries. Arc welding’s ruggedness makes it ideal for heavy-duty construction, shipbuilding, and pipeline work, where thick materials and outdoor conditions are common. TIG welding’s precision, however, is better suited for industries like aerospace, automotive, and manufacturing, where intricate details and high-quality finishes are essential. Both methods are integral to the success of projects in these fields, highlighting their complementary roles in welding technology.
By sharing these foundational principles while maintaining distinct techniques, arc welding and TIG welding demonstrate how innovations in welding processes build upon core methodologies to address a wide range of industrial needs.
Overlaps in Equipment
Modern welding technology has enabled significant overlaps in equipment used for both arc welding and TIG welding. Multi-process welding machines are a prime example, offering the flexibility to switch between different welding techniques, including traditional arc welding methods like SMAW (Shielded Metal Arc Welding) and TIG welding, with relative ease.
Inverter-Based Welders
Inverter-based welding machines have become a popular choice for their ability to handle multiple welding processes. These machines use advanced electronics to convert and control the power supply, making them compact, efficient, and versatile. By simply adjusting settings or attaching appropriate accessories, such as a TIG torch or a stick electrode holder, the same machine can seamlessly transition between SMAW and TIG welding. This capability is particularly useful for welders working on diverse projects requiring different welding techniques.
Shared Power Sources and Controls
Both arc welding and TIG welding rely on similar power sources, such as DC or AC outputs, which can often be provided by the same machine. The overlap in controls includes:
- Amperage Adjustment: Both methods require precise control of amperage to match the material and thickness being welded.
- Polarity Settings: Machines designed for both processes typically offer options for DCEN (Direct Current Electrode Negative), DCEP (Direct Current Electrode Positive), and AC settings.
- Arc Start Features: In TIG welding, a high-frequency start or lift-arc feature ensures smooth ignition of the arc. Similar arc-start mechanisms may also be incorporated into advanced arc welding machines.
Common Accessories
Some accessories are interchangeable between the two methods, further enhancing the versatility of the equipment. For instance:
- Ground Clamps: Used in both processes to complete the electrical circuit.
- Foot Pedals: TIG welding often employs foot pedals for precise amperage control, and some multi-process machines can accommodate these for added functionality.
- Gas Regulators and Cylinders: If the multi-process machine supports TIG or gas-based arc welding methods like GMAW, the same shielding gas system can be used.
Cost and Convenience Advantages
The ability to use a single machine for both arc and TIG welding reduces the need for multiple dedicated units, saving space and costs. This is especially beneficial for small workshops or mobile welders who need to tackle diverse tasks efficiently. Additionally, welders transitioning from one method to another benefit from the familiarity of operating similar controls and equipment.
Real-World Applications
Multi-process machines are commonly used in repair shops, fabrication industries, and fieldwork, where versatility is key. For instance, a welder might use SMAW for outdoor structural repairs and switch to TIG welding for precision work on thinner or more intricate materials—all with the same machine.
The overlap in equipment highlights the evolution of welding technology, allowing welders to maximize efficiency and adapt to a variety of project requirements without investing in entirely separate setups.
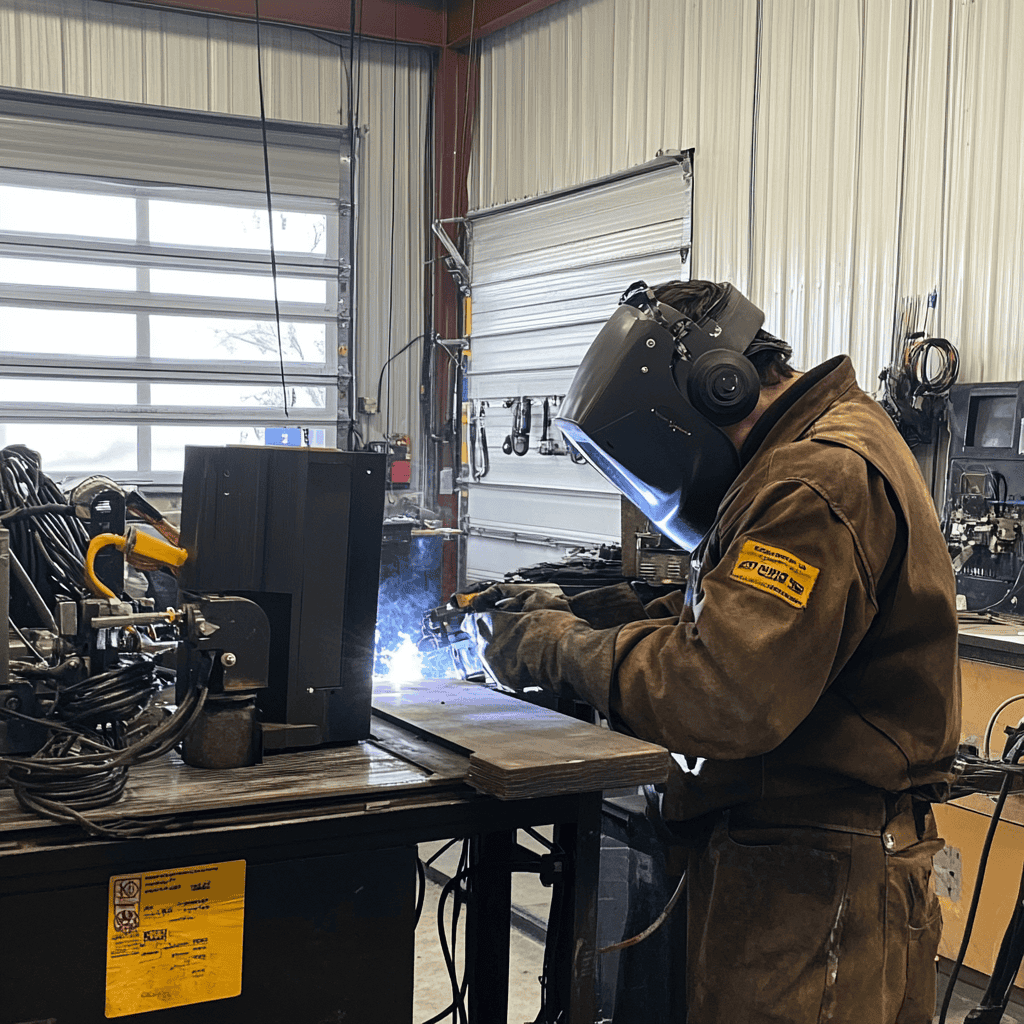
How They Differ
While both arc welding and TIG welding share fundamental principles, their differences in execution and applications make them suited to distinct purposes. Understanding these distinctions is critical for selecting the right method for a specific project.
Material Suitability and Conditions
- Arc Welding (e.g., Stick Welding): This method is ideal for thick, rugged materials such as structural steel, cast iron, and heavy-duty equipment. Its ability to handle less-than-pristine surfaces, such as rusty or dirty metals, makes it highly versatile in outdoor conditions. For example, arc welding is often used in construction, pipeline work, and shipbuilding due to its robust performance in windy, wet, or otherwise challenging environments.
- TIG Welding: In contrast, TIG welding excels in applications requiring precision and finesse. It is the preferred method for thin materials and intricate work, including aluminum, stainless steel, and titanium. The clean, high-quality welds produced by TIG welding make it indispensable for projects like aerospace components, automotive repairs, and artistic metalwork. TIG welding’s reliance on shielding gas, however, makes it less effective in windy outdoor environments where the gas can be blown away.
Execution and Technique
- Arc Welding: Arc welding is known for its straightforward setup and execution. It uses a consumable electrode coated in flux, which generates the shielding gas when heated. This simplicity makes arc welding relatively easy to learn, especially for beginners. However, it produces slag and spatter, requiring post-weld cleanup.
- TIG Welding: TIG welding demands greater skill and precision. It uses a non-consumable tungsten electrode and often incorporates a filler rod for material fusion. The process requires the welder to control multiple variables simultaneously, including the arc, shielding gas flow, and, in some cases, a foot pedal for amperage control. This complexity results in welds with superior aesthetics and minimal spatter but comes with a steeper learning curve.
Applications and Industries
- Arc Welding: Common in industries requiring durability and high productivity, arc welding is often the go-to method for heavy-duty repairs, structural welding, and fabrication of large-scale equipment. Its ability to perform in harsh environments and on thick materials makes it a workhorse for industrial and field applications.
- TIG Welding: TIG welding shines in industries where precision and quality are paramount. It is widely used in aerospace, automotive, and medical equipment manufacturing, where clean, strong, and visually appealing welds are non-negotiable. TIG welding is also a popular choice for artistic and decorative applications, such as sculptures and ornamental railings.
Cost and Efficiency
- Arc Welding: The equipment and consumables for arc welding, such as electrodes, are generally more affordable. Its faster setup and execution make it a cost-effective choice for large-scale or time-sensitive projects. However, the need for cleanup and the less refined weld appearance may offset these advantages in some scenarios.
- TIG Welding: TIG welding requires a greater initial investment in equipment, such as high-quality TIG torches and shielding gas. The process is slower than arc welding, which can increase labor costs. However, its ability to produce near-perfect welds with minimal rework often justifies the expense for high-precision projects.
Complementary Roles
While arc welding and TIG welding differ significantly, they often complement each other in practice. For example, a welder might use arc welding for the structural framework of a project and TIG welding for finishing touches or intricate components. This dual approach allows for optimal efficiency and quality, leveraging the strengths of each method to achieve the best results.
In summary, arc welding and TIG welding cater to different needs but share a place in the toolkit of skilled welders. Arc welding is a reliable and rugged choice for heavy-duty applications, while TIG welding provides the precision and quality needed for delicate or high-value work. Understanding these differences helps welders make informed decisions tailored to their project requirements.
Advantages and Limitations of Arc vs. TIG Welding
To further clarify the differences and applications of arc and TIG welding, it’s essential to explore the specific advantages and limitations of each method. This comparison provides insight into their practical use cases and highlights where one method might outperform the other.
Advantages of Arc Welding
- Robust Performance in Adverse Conditions
Arc welding thrives in outdoor environments and on imperfect surfaces, including rusty or dirty metals. Its ability to perform under windy or wet conditions makes it indispensable for fieldwork and structural repairs. - Cost-Effectiveness
The equipment and consumables, such as flux-coated electrodes, are relatively affordable. This makes arc welding an accessible option for beginners, hobbyists, and large-scale projects on a budget. - Ease of Learning and Quick Setup
Arc welding is straightforward, with minimal setup requirements. Beginners can quickly grasp the basics, making it an excellent starting point for those new to welding. - Versatility in Material Thickness
Arc welding is ideal for welding thick materials, offering deep penetration that ensures strong bonds in heavy-duty applications.
Limitations of Arc Welding
- Slag and Cleanup Requirements
The flux coating produces slag that must be chipped away after welding. This adds an extra step to the process and may detract from the weld’s aesthetic appeal. - Difficulty with Thin Materials
Arc welding struggles with thin metals, as the high heat can easily burn through the material, limiting its versatility. - Less Precision
Compared to TIG welding, arc welding lacks the fine control needed for intricate or high-quality welds.
Advantages of TIG Welding
- Exceptional Precision and Quality
TIG welding delivers clean, aesthetically pleasing welds with minimal spatter. It is ideal for projects where appearance and detail are paramount. - Versatility with Material Types
TIG welding works well with a wide range of metals, including aluminum, stainless steel, and titanium, making it a preferred choice for industries requiring diverse material handling. - Control Over the Welding Process
The use of a foot pedal for amperage control and the non-consumable tungsten electrode provide welders with unparalleled precision and adaptability. - Minimal Post-Weld Cleanup
TIG welding produces no slag, and spatter is negligible, reducing the time spent on finishing and polishing.
Limitations of TIG Welding
- Higher Equipment Costs
The initial investment in TIG welding equipment, including shielding gas and torches, is significantly higher than arc welding. - Slower Process
TIG welding is time-intensive, making it less efficient for large-scale projects or scenarios where speed is a priority. - Steeper Learning Curve
The complexity of TIG welding, with its multiple variables to manage, requires greater skill and training, posing challenges for beginners. - Sensitivity to Environment
TIG welding’s reliance on shielding gas makes it unsuitable for windy or outdoor conditions where gas coverage can be disrupted.
Choosing the Right Method
The decision between arc and TIG welding ultimately depends on the specific requirements of the project.
- Choose Arc Welding for
- Outdoor or fieldwork projects.
- Budget-friendly and fast execution.
- Applications involving thicker, less pristine materials.
- Choose TIG Welding for
- Projects requiring high precision and clean finishes.
- Working with thin or non-ferrous materials like aluminum or titanium.
- High-value or intricate applications, such as aerospace components or artistic designs.
This detailed comparison underscores how these two welding methods complement each other, offering unique advantages suited to different welding challenges and environments. Adding this section enhances the article by providing actionable insights for welders evaluating their options.
Additional Resources
Get your welding gear here.
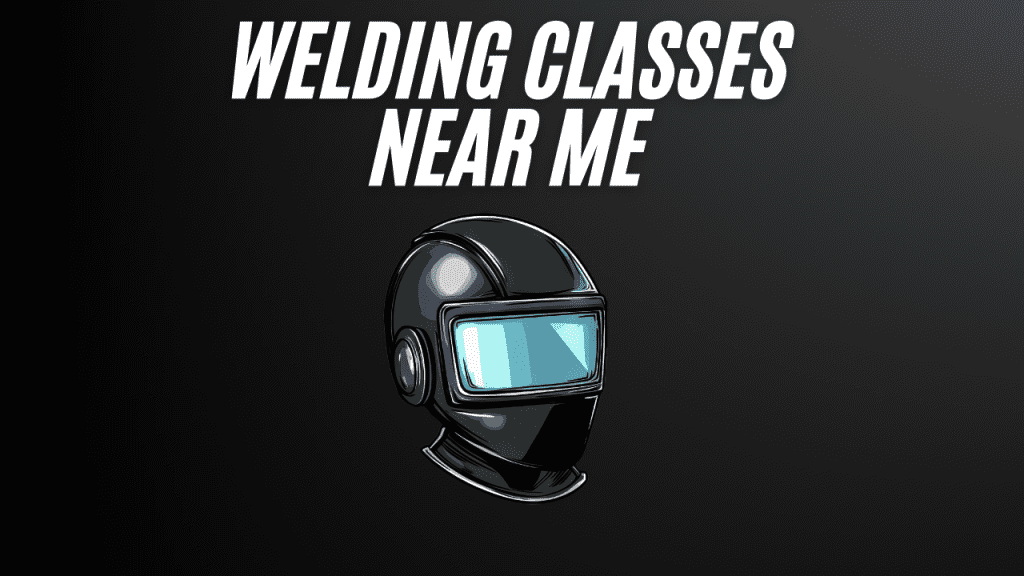