Table of Contents
What Is Solid State Welding?
Solid-state welding refers to a group of welding processes where the base materials are joined without melting. Unlike fusion welding, where materials are liquefied, solid-state welding relies on heat, pressure, or a combination of both to create a bond. The materials may be heated to a high temperature, but not to the melting point. This unique characteristic makes solid-state welding ideal for applications requiring strong, distortion-free joints.
Key Characteristics of Solid State Welding
- No Melting Required
The base materials are joined below their melting points, preserving their original properties. - Pressure Welding
Heat and pressure are applied to create the bond, hence its alternate name, “pressure welding.” - Minimal Heat-Affected Zone (HAZ)
The process avoids extensive thermal damage, reducing the risks of distortion and weakening in the surrounding areas. - Flexibility for Dissimilar Metals
Solid-state welding is especially effective for joining metals that are otherwise difficult to weld using conventional fusion methods.
Types of Solid State Welding Processes
Solid-state welding encompasses a variety of techniques, each suited for specific materials and applications. These methods prioritize strength and precision by avoiding the melting of materials, often making them ideal for specialized and high-performance applications.
Forge Welding
Forge welding, one of the oldest known welding techniques, involves heating metals to a pliable temperature and then hammering them together. This technique is often used in blacksmithing and for joining materials like iron and steel. The process relies on precise temperature control and skillful hammering to create a durable bond.
- Applications: Commonly used in traditional metalworking, knife-making, and artistic forging.
- Advantages: Simple tools and techniques, strong joints for thick materials.
- Limitations: Requires significant manual labor and skill, challenging for complex geometries.
Ultrasonic Welding
Ultrasonic welding uses high-frequency acoustic vibrations to generate localized heat through friction, bonding materials under pressure. This technique is widely employed in the automotive, aerospace, and electronics industries for joining thin metals and plastics.
- Applications: Ideal for welding delicate components like microcircuits, plastic casings, and medical devices.
- Advantages: No need for additional materials or adhesives, minimal waste, and rapid processing.
- Limitations: Limited to thin materials and small-scale applications.
Friction Welding
Friction welding generates heat through mechanical friction between two surfaces, which are then pressed together to form a strong bond. This method is particularly effective for cylindrical components like rods, pipes, and shafts.
- Applications: Used in the automotive and aerospace industries for creating drive shafts, engine parts, and hydraulic systems.
- Advantages: High joint strength, excellent for dissimilar materials, and produces defect-free welds.
- Limitations: Requires specific geometries for the materials being welded, high initial equipment costs.
Roll Welding
In roll welding, a stack of metal sheets or plates is passed through rollers under high pressure, causing the materials to bond without melting. This process is ideal for ductile materials such as aluminum, copper, and steel.
- Applications: Often used in the production of clad metals, electrical components, and industrial laminates.
- Advantages: Produces strong, uniform bonds, suitable for large-scale production.
- Limitations: Requires ductile materials, limited to flat or sheet-like geometries.
Cold Welding
Cold welding, also known as contact welding, bonds metals without the application of heat. This method relies on clean, oxide-free surfaces and high pressure to create a molecular bond.
- Applications: Commonly used in aerospace and electrical applications for joining non-ferrous metals like aluminum and copper.
- Advantages: No heat-affected zones (HAZ), ideal for sensitive materials, and creates parent metal-like bonds.
- Limitations: Difficult to achieve perfect surface preparation, limited to specific materials and geometries.
Explosion Welding
Explosion welding uses the force of controlled chemical explosions to create a high-velocity impact, bonding metals together. This process is particularly effective for cladding dissimilar metals.
- Applications: Used in the production of corrosion-resistant materials, heat exchangers, and bimetallic components.
- Advantages: Capable of joining metals that cannot be welded by conventional methods, produces molecular bonds with exceptional strength.
- Limitations: Requires expertise in handling explosives, challenging to perform in small-scale setups.
Diffusion Welding
Diffusion welding involves applying heat and pressure over a prolonged period, allowing atoms from two surfaces to diffuse into each other. This technique is used for high-precision applications requiring flawless joints.
- Applications: Often employed in the aerospace and medical industries for components like turbine blades and surgical instruments.
- Advantages: Produces high-quality, defect-free joints, suitable for both similar and dissimilar metals.
- Limitations: Time-consuming, requires precise temperature and pressure control, and can be expensive.
Summary
Each solid-state welding technique offers unique advantages and challenges, making them suitable for specific materials and applications. From traditional methods like forge welding to advanced techniques like diffusion welding, these processes emphasize precision and strength, ensuring their place in modern manufacturing and engineering.
Advantages of Solid State Welding
Solid state welding offers several key benefits that make it a preferred choice for various high-precision and critical applications:
Minimal Distortion
Since the materials are joined without melting, there is significantly less thermal stress and distortion compared to fusion welding. This makes it ideal for applications where dimensional accuracy is critical.
Example: In aerospace components, where exact specifications are vital, minimal warping ensures proper fit and function.
Strong Bonds
Solid-state welding produces joints with strength often comparable to or exceeding the base materials. The absence of melting and resolidification leads to bonds with fewer structural weaknesses.
Example: Diffusion welding creates seamless joints with excellent load-bearing capacity, perfect for turbine blades.
Versatility
This welding method is effective for joining dissimilar metals and materials with varying thicknesses. Processes like friction welding or explosion welding excel in combining metals that are difficult to join using traditional fusion methods.
Example: Joining aluminum to steel in automotive applications enhances strength while maintaining lightweight properties.
Improved Aesthetics
Solid-state welding produces clean and seamless joints, often eliminating the need for post-weld finishing like grinding or polishing.
Example: Ultrasonic welding in electronics ensures visually appealing finishes for connectors and casings.
Reduced Defects
The absence of melting avoids common defects like porosity, cracking, or contamination, leading to higher-quality welds.
Example: In packaging, ultrasonic welding ensures airtight seals without introducing contaminants into the weld.
Disadvantages of Solid State Welding
While solid-state welding offers numerous benefits, it also has some significant challenges and limitations that must be considered for specific applications:
Complex Joint Preparation
Achieving a successful weld requires meticulous preparation of the joint surfaces. This includes cleaning, aligning, and ensuring the absence of contaminants like oxides, grease, or dirt.
- Challenge: In diffusion welding, even minor surface roughness or oxide layers can inhibit atomic diffusion, leading to weak or incomplete joints. This level of preparation increases labor and time requirements, particularly for complex assemblies.
- Impact: Projects requiring quick turnaround may face delays due to the time-intensive nature of joint preparation.
Specialized Equipment
Solid-state welding methods often demand sophisticated and expensive machinery, such as high-pressure systems, friction welding tools, or acoustic vibration generators. These machines require proper calibration and skilled operators to ensure optimal performance.
- Challenge: Ultrasonic welding systems, for example, need precise tuning of frequency and amplitude, which may be beyond the capabilities of small-scale manufacturers.
- Impact: The high initial cost and operational complexity can be prohibitive for smaller businesses or niche applications.
Limited Gap Bridging
Solid-state welding techniques do not involve the use of filler materials, which limits their effectiveness in joining components with large root gaps or poorly fitting surfaces. The materials being joined must have minimal irregularities to achieve a strong bond.
- Challenge: Cold welding, for instance, requires perfectly clean and flat surfaces to bond effectively. This restricts its applicability in structural or large-scale projects where precise machining is impractical.
- Impact: Poorly prepared joints can result in weak bonds, making solid-state welding unsuitable for certain types of structural work.
Cost
Certain solid-state welding processes, such as diffusion welding or explosion welding, can be costly due to the specialized equipment, high energy demands, and skilled labor required. These costs can outweigh the benefits in some cases, particularly for projects with tight budgets or less demanding performance requirements.
- Challenge: Explosion welding, while highly effective for bonding dissimilar metals, involves the use of chemical explosives and precise detonation setups, which can drive up costs and necessitate compliance with strict safety regulations.
- Impact: The high cost of setup and operation makes some solid-state processes viable only for specialized, high-value applications like aerospace or defense.
Limited Flexibility in Design
The nature of solid-state welding often imposes restrictions on joint design and geometry. Techniques like roll welding or friction welding may not accommodate intricate shapes or varying thicknesses as easily as fusion welding.
- Challenge: Friction stir welding, for example, requires consistent material thickness and uniform joint preparation, limiting its use in projects with complex geometries.
- Impact: Designers may need to modify component designs to suit the welding process, potentially increasing overall project costs and complexity.
Incompatibility with Certain Materials
Some solid-state welding methods may struggle with specific material combinations, particularly those with vastly different thermal or mechanical properties.
- Challenge: Welding metals with widely varying melting points or thermal expansion rates can lead to residual stresses or weak joints.
- Impact: This incompatibility restricts the application of solid-state welding for certain advanced materials or composites.
Summary
Solid-state welding, while offering precision and strength, is not without its challenges. The need for rigorous joint preparation, specialized equipment, and precise control makes it less accessible for some applications. Additionally, limitations in gap bridging and material compatibility further restrict its use in certain industries. Despite these drawbacks, when applied to the right projects, solid-state welding remains an invaluable process for achieving high-quality, defect-free joints.
Applications of Solid State Welding
Solid-state welding is a versatile process, widely adopted across various industries where precision, durability, and material compatibility are essential. Here’s a closer look at its applications:
Aerospace
In aerospace, where lightweight and high-strength materials are critical, solid-state welding is a preferred choice for joining components such as turbine blades, fuselage panels, and engine parts. The ability to join dissimilar materials with minimal distortion ensures that components meet the stringent safety and performance standards of the industry.
Example: Friction stir welding is commonly employed to fabricate fuel tanks for spacecraft, as it produces defect-free welds that can withstand extreme temperatures and pressures.
Automotive
The automotive industry benefits significantly from solid-state welding techniques, which enable the production of durable yet lightweight parts. This balance is crucial for improving fuel efficiency and safety while maintaining structural integrity. Components such as drive shafts, gear assemblies, and chassis structures are often produced using solid-state welding.
Example: Friction welding is widely used to join aluminum and steel in car bodies, reducing weight while maintaining the strength required for crash safety.
Electronics
In the electronics sector, solid-state welding facilitates the precise bonding of delicate components such as microcircuits, connectors, and sensors. The absence of excessive heat in processes like ultrasonic welding ensures that sensitive materials are not damaged, making this technique indispensable for compact and reliable designs.
Example: Ultrasonic welding is extensively used in the production of lithium-ion batteries, which power smartphones, laptops, and electric vehicles, ensuring efficient energy transfer and durability.
Packaging
The packaging industry relies on solid-state welding for creating airtight seals, particularly for food, beverages, and medical products. These seals ensure hygiene, preserve product quality, and extend shelf life. The non-invasive nature of ultrasonic welding makes it ideal for applications requiring sterile and tamper-proof packaging.
Example: Ultrasonic welding is used to create seamless seals for sterile medical containers, ensuring that the contents remain uncontaminated during transportation and storage.
Oil and Gas
In the oil and gas sector, solid-state welding techniques like explosion welding are used to clad pipelines, storage tanks, and other critical infrastructure with corrosion-resistant materials. This enhances the durability and longevity of components exposed to harsh environmental conditions and corrosive substances.
Example: Explosion welding is employed to bond steel pipes with corrosion-resistant alloys, significantly extending the operational lifespan of oil and gas pipelines in offshore and onshore environments.
Medical Devices
The medical industry utilizes solid-state welding for creating precision components that meet strict hygiene and safety standards. The process is used to bond surgical instruments, diagnostic equipment, and prosthetics with minimal thermal distortion or contamination.
Example: Diffusion welding is often used to join biocompatible metals like titanium in prosthetic implants, ensuring a strong and durable bond suitable for long-term use.
Energy
In renewable and traditional energy sectors, solid-state welding is applied to manufacture critical components for turbines, generators, and reactors. Its ability to join dissimilar and high-strength materials ensures reliability under demanding operational conditions.
Example: Friction stir welding is utilized in the assembly of wind turbine blades, providing robust connections that can endure high wind loads and variable stresses.
Summary
Solid-state welding’s ability to produce high-strength, defect-free joints with minimal distortion makes it an essential process across industries. From aerospace and automotive to electronics, packaging, and energy, its applications showcase its versatility and importance in modern manufacturing. By enabling the efficient joining of both similar and dissimilar materials, solid-state welding continues to drive innovation and quality in engineering and design.
Conclusion
Solid-state welding represents an innovative approach to joining materials without melting. Its ability to preserve the mechanical properties of base materials while creating strong, reliable joints makes it a preferred choice for industries demanding high precision and minimal distortion. Understanding the advantages, limitations, and various processes under this umbrella enables engineers and welders to select the best method for their specific needs.
Additional Resources
Get your welding gear here.
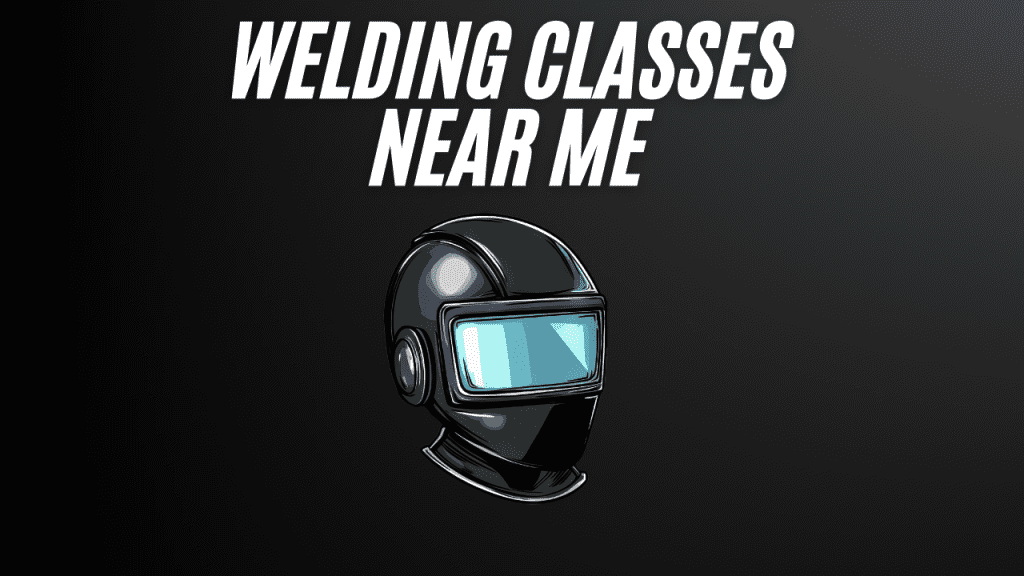