Table of Contents
What is Laser Beam Welding?
Laser beam welding (LBW) is a precise and high-energy welding process that joins two or more materials using a laser beam. The term “laser” stands for Light Amplification by Stimulated Emission of Radiation. This non-contact method requires access to the weld zone from only one side, making it suitable for intricate and hard-to-reach areas. The laser’s concentrated energy melts the metal upon impact, and as the material cools, a strong, solid weld is formed.
The Principle of Laser Beam Welding
Laser beam welding works on the principle of stimulated emission of radiation. Electrons in the lasing medium absorb energy, becoming excited. When these electrons return to their ground state, they release photons. This chain reaction of photon emission amplifies the light, creating a highly concentrated laser beam capable of melting metals with pinpoint precision.
Types of Lasers Used in Laser Beam Welding
Types of Lasers Used in Laser Beam Welding
Laser beam welding utilizes various types of lasers, each with unique characteristics and applications tailored to specific industrial needs.
Solid-State Lasers
Solid-state lasers employ a solid gain medium, such as glass or crystalline material doped with rare-earth elements like neodymium, erbium, or ytterbium. These lasers are highly efficient and versatile, operating at wavelengths around 1 micrometer, which is shorter than that of gas lasers, offering increased precision.
Examples: Nd:YAG (Neodymium-doped Yttrium Aluminum Garnet) lasers are the most common type of solid-state lasers used in welding.
Features:
- Operates in both continuous and pulsed modes, making it adaptable for a wide range of applications.
- Produces intense, focused energy capable of precision welding.
- A typical setup includes a rod-shaped gain medium surrounded by a flash tube filled with krypton or xenon to pump the laser.
- These lasers require safety precautions, such as special eyewear or screens, to protect operators from retinal damage due to their high energy density.
Solid-state lasers are ideal for delicate welding tasks requiring accuracy and are widely used in industries like aerospace, medical device manufacturing, and electronics.
Gas Lasers
Gas lasers use a gas mixture, such as carbon dioxide (CO₂), as the lasing medium. The gas is energized using low-current, high-voltage power sources to produce a high-energy laser beam. Operating at a wavelength of 10.6 μm, gas lasers are known for their capability to deliver significant power output, making them ideal for high-intensity welding tasks.
Features:
- Operates in pulsed or continuous mode, providing flexibility for various applications.
- Produces deep penetration welds, particularly useful for thick materials and large-scale industrial applications.
- A high power-to-cost ratio makes gas lasers effective for heavy-duty welding.
Limitations:
- The 10.6 μm wavelength cannot be transmitted through fiber optic cables, requiring mirror-based beam delivery systems and rigid lenses.
- Cooling and alignment systems are needed to manage the high energy and maintain precision.
Gas lasers are widely used in heavy industries such as shipbuilding, automotive manufacturing, and construction for welding thick plates and structural components.
Fiber Lasers
Fiber lasers use an optical fiber as the gain medium, doped with elements such as ytterbium to amplify the light. These lasers have revolutionized the welding industry due to their compact size, high efficiency, and low maintenance requirements.
Applications:
- Fiber lasers are extensively used in robotic welding systems, enabling automation and precision in large-scale industrial operations.
- Suitable for intricate tasks requiring precision, such as micro-welding and welding in confined spaces.
Advantages:
- Power Efficiency: Fiber lasers achieve high energy efficiency, reducing operational costs.
- High Power Output: Capable of producing power levels up to 50 kW, making them suitable for demanding welding tasks.
- Compact Design: The small footprint allows for easy integration into existing production lines.
- Versatility: Can weld a wide variety of metals and alloys with precision, including reflective materials like aluminum and copper.
- Minimal Maintenance: The all-fiber design minimizes the need for regular maintenance, ensuring high uptime and reliability.
Fiber lasers are increasingly becoming the preferred choice in industries prioritizing efficiency and automation, such as automotive manufacturing, electronics, and medical device production.
Comparison of Laser Types
Laser Type: Solid-State Lasers
Medium: Solid (e.g., Nd:YAG)
Wavelength: ~1 μm
Power Output: Moderate
Applications: Precision tasks in aerospace, medical, and electronics
Key Features: Operates in pulsed and continuous modes; requires special safety measures
Laser Type: Gas Lasers
Medium: Gas mixture (CO₂)
Wavelength: 10.6 μm
Power Output: High
Applications: Heavy-duty welding in automotive, shipbuilding, and construction
Key Features: Deep penetration welds; uses mirror systems for energy delivery
Laser Type: Fiber Lasers
Medium: Optical fiber
Wavelength: ~1 μm
Power Output: Up to 50 kW
Applications: Robotic and automated welding, intricate micro-welding
Key Features: Compact, efficient, and low-maintenance
Each laser type brings distinct advantages, allowing manufacturers to choose the best solution based on material, application, and project requirements.
Modes of Laser Beam Welding
Modes of Laser Beam Welding
Laser beam welding offers multiple operational modes, each designed for specific applications and material characteristics. These modes determine the energy input, heat distribution, and resulting weld geometry.
Conduction Mode Welding
Process: Conduction mode welding utilizes a low energy density laser beam, which heats the material’s surface and transfers the heat inward through thermal conduction. This results in shallow and wide weld profiles.
Mechanism: The heat spreads from the laser’s point of contact across the material’s surface and into the material itself without causing significant penetration. The process relies heavily on the thermal conductivity of the base material.
Applications:
- Best suited for thin materials or components where limited penetration is required.
- Commonly used for welding metals and alloys in delicate assemblies, such as in the electronics industry.
- Ideal for applications prioritizing cosmetic welds, such as decorative seams, where the appearance is crucial.
Conduction/Penetration Mode Welding
Process: Conduction/penetration mode welding operates at a medium energy density, providing a balance between surface heating and material penetration. It combines features of both conduction and keyhole welding.
Mechanism: The laser’s energy partially penetrates the material, creating a moderately deep weld with a relatively wide profile. This mode achieves a balance between shallow conduction and the deeper penetration of keyhole welding.
Applications:
- Suitable for moderate thickness materials where a balance between heat input and weld depth is necessary.
- Used in general-purpose welding tasks, such as sheet metal fabrication, automotive assemblies, and small structural components.
- Often employed in projects requiring a combination of aesthetic finish and structural integrity.
Penetration/Keyhole Welding
Process: Penetration or keyhole welding uses high energy density to focus the laser beam into a small area, generating intense heat that creates a “keyhole” or deep cavity in the material. This keyhole is filled with molten metal, which solidifies as the laser progresses, forming a deep and narrow weld.
Mechanism: The concentrated energy of the laser vaporizes the material at the focal point, creating the keyhole. Surrounding molten metal flows around and seals the cavity as the laser advances, ensuring a strong and continuous weld.
Applications:
- Ideal for deep and narrow welds, making it a preferred choice for high-strength materials like titanium, stainless steel, and aluminum alloys.
- Widely used in aerospace, automotive, and shipbuilding industries, where strong, precise joints are critical.
- Common in thick material welding where deep penetration is required without excessive heat input to surrounding areas.
Comparison of Laser Welding Modes
Mode | Energy Density | Weld Profile | Applications |
---|---|---|---|
Conduction | Low | Shallow and wide | Thin materials, decorative welds, electronics |
Conduction/Penetration | Medium | Moderate depth and width | General-purpose welding, sheet metal, automotive |
Penetration/Keyhole | High | Deep and narrow | High-strength materials, aerospace, shipbuilding |
Selecting the Right Mode
Choosing the optimal laser welding mode is critical to achieving desired results, as each mode offers unique benefits suited to specific applications. The decision depends on several key factors:
Material Thickness
The thickness of the material being welded is one of the primary considerations in mode selection:
- Conduction Mode: Ideal for thin materials due to its low energy density, which prevents excessive heat penetration. This minimizes the risk of burn-through or warping, making it suitable for delicate components like electronics and thin sheet metals.
- Keyhole Welding: The high energy density in this mode makes it suitable for thick or high-strength materials. It ensures deep penetration and strong bonds, especially for applications in aerospace or shipbuilding, where weld integrity is critical.
Required Weld Strength
The strength of the joint needed plays a significant role in determining the welding mode:
- Keyhole Welding: Known for producing the strongest bonds, this mode is ideal for structural applications requiring high tensile and shear strength. The deep weld penetration ensures durability and load-bearing capacity in critical infrastructure projects.
- Conduction Mode: While not as strong as keyhole welds, conduction welds are sufficient for non-structural applications where strength is less critical but appearance is important.
Heat Sensitivity
Heat sensitivity of the base material can influence the choice of mode:
- Conduction Mode: Generates less heat, resulting in a narrow heat-affected zone (HAZ). This minimizes distortion, making it perfect for materials prone to warping, such as aluminum or high-precision alloys.
- Keyhole Welding: Although more heat is concentrated in the keyhole mode, the precision of the laser minimizes overall heat input compared to traditional welding methods. Still, it’s better suited for materials that can withstand higher thermal loads.
Aesthetic Requirements
When the visual quality of the weld is a priority, conduction mode is often preferred:
- Conduction Mode: Produces smooth and clean welds with minimal spatter, making it the go-to option for decorative or exposed seams in applications such as consumer electronics or automotive panels.
- Keyhole Welding: While excellent for strength, it may require post-weld finishing to achieve a polished look, particularly for highly visible applications.
Additional Considerations for Mode Selection
- Welding Speed: Keyhole welding allows faster processing for thick materials, reducing production time in large-scale manufacturing. Conduction mode, while slower, ensures precision and surface quality.
- Material Compatibility: Some materials, like highly reflective metals (e.g., copper), may require specific lasers and welding modes to optimize absorption and efficiency.
- Joint Design: Conduction mode is best for lap joints and thin-sheet welding, while keyhole welding is better suited for butt joints and deep penetrations in thicker materials.
- Cost Efficiency: Conduction mode typically requires less energy and equipment, making it more cost-effective for projects where high weld strength is not a priority.
By carefully evaluating these factors, welders can select the most effective mode for their specific application, ensuring high-quality, reliable, and visually appealing results.
Applications of Laser Beam Welding
Laser beam welding is widely used in industries requiring precision and high-speed production. Common applications include:
- Automotive Industry: Welding body panels, gears, and transmission components.
- Aerospace Industry: Fabricating lightweight components like titanium parts and fuel tanks.
- Electronics Industry: Joining delicate components such as microcircuits and battery cells.
- Medical Devices: Assembling surgical instruments and implants.
- Manufacturing: High-volume production of metal enclosures, stainless steel tubing, and complex assemblies.
Materials commonly used with laser beam welding include:
- Carbon Steels
- High-Strength Low-Alloy Steels
- Aluminum
- Stainless Steel
- Titanium
Advantages of Laser Beam Welding
Laser beam welding offers numerous benefits, including:
- No Filler Metals: Welds are formed without the need for additional filler material.
- High Accuracy: The focused laser beam ensures precise welds with minimal error.
- Minimal Distortion: The narrow heat-affected zone reduces warping and stress.
- No Secondary Finishing: Welds are smooth and require little to no post-weld processing.
- Versatility: Suitable for welding high-alloy metals and thin components.
- Power Efficiency: The laser can be transmitted over long distances while maintaining power.
- Safety: Does not emit harmful x-rays during operation.
Limitations of Laser Beam Welding
Despite its advantages, laser beam welding has some challenges:
- High Equipment Costs: The initial investment for laser systems is significant, making it less accessible for smaller operations.
- Maintenance Requirements: Lasers require regular maintenance to ensure optimal performance.
- Cooling Speed: The rapid cooling of the weld can lead to cracks in certain materials.
- Surface Sensitivity: Metals must be clean and free from oxidation to avoid defects.
Conclusion
Laser beam welding is a cutting-edge technique that combines precision, efficiency, and versatility. While it requires significant investment and expertise, its ability to produce high-quality, distortion-free welds makes it indispensable in industries like automotive, aerospace, and electronics. By understanding the principles, types, and applications of laser beam welding, manufacturers can leverage its capabilities to achieve superior results.
Additional Resources
Get your welding gear here.
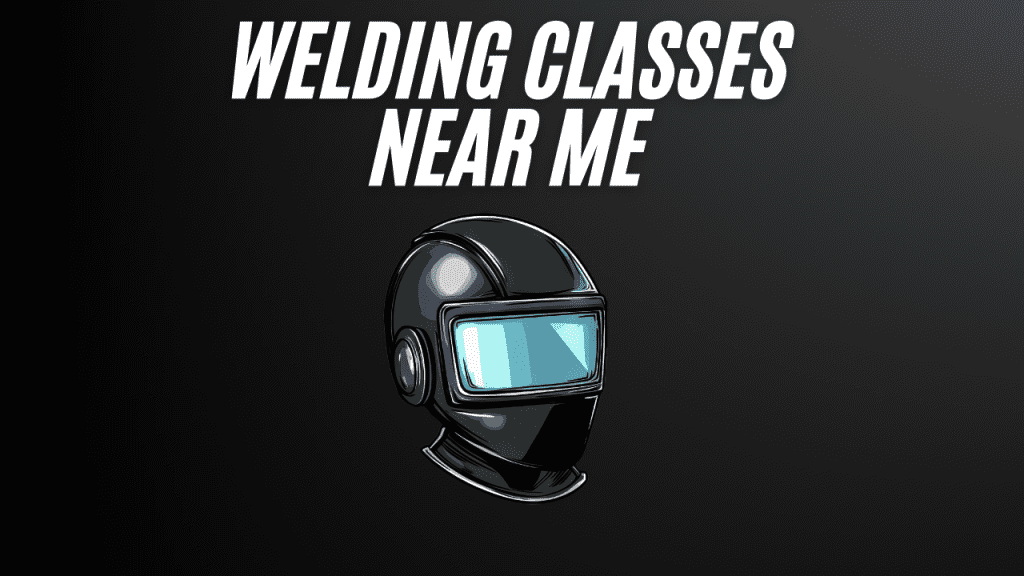