Table of Contents
What is Fiber Reinforced Concrete?
Introduction
Concrete has long been a cornerstone of construction due to its strength, durability, and versatility. However, traditional concrete has its limitations, particularly when it comes to resisting cracking under tensile stress. Fiber reinforced concrete (FRC) addresses these challenges by integrating fibrous materials into the mix, enhancing its structural integrity and expanding its range of applications.
This article explores fiber reinforced concrete, how it works, the fibers it uses, and its advantages, limitations, and applications.
What is Fiber Reinforced Concrete?
Fiber reinforced concrete is a composite material consisting of traditional concrete combined with fibrous materials to improve its overall performance. Unlike regular concrete, which relies solely on cement and aggregate for strength, FRC uses fibers to resist cracking, increase tensile strength, and improve durability.
These fibers are distributed throughout the concrete mix, allowing the material to maintain integrity even under significant stress. Common fiber types include steel, glass, synthetic materials like polypropylene, and natural fibers such as coconut or jute.
How Does Fiber Reinforced Concrete Work?
The fibers in FRC act as crack arrestors, preventing the propagation of micro-cracks that naturally form as concrete cures or experiences stress. When tensile forces are applied to traditional concrete, it can crack and lose structural integrity. In FRC, the fibers absorb and redistribute these stresses, allowing the concrete to remain intact.
The effectiveness of FRC depends on factors like fiber type, size, shape, and distribution within the mix. Uniform distribution of fibers ensures consistent performance and prevents weak spots.
Types of Fibers Used in Fiber Reinforced Concrete (FRC)
Fiber reinforced concrete owes its enhanced performance to the inclusion of various fibers, each offering unique properties tailored to specific applications. Below is an expanded look at the types of fibers commonly used in FRC:
Steel Fibers
Steel fibers are among the most robust options for reinforcing concrete. Their high tensile strength and ability to enhance load-bearing capacity make them indispensable in heavy-duty applications.
- Applications: Steel fibers are widely used in industrial flooring, airport runways, tunnel linings, and precast concrete products. They provide resistance to heavy dynamic loads and impact forces.
- Benefits: These fibers significantly improve the concrete’s ability to resist cracking and deformation under stress. They also enhance the structure’s durability in high-traffic or industrial environments.
- Challenges: Steel fibers can add to the weight of the mix and may require specialized mixing techniques to ensure uniform distribution.
Glass Fibers
Glass fibers are known for their corrosion resistance and aesthetic appeal, making them ideal for decorative and architectural uses.
- Applications: These fibers are commonly used in architectural cladding panels, decorative precast concrete, and facade systems.
- Benefits: Glass fibers are lightweight, non-corrosive, and offer excellent resistance to environmental factors like UV radiation and chemical exposure. Their inclusion allows for intricate designs and smooth finishes in construction projects.
- Challenges: While resistant to environmental degradation, glass fibers may not provide the same tensile strength as steel fibers, limiting their use in high-load applications.
Synthetic Fibers
Synthetic fibers, including polypropylene, nylon, and polyethylene, offer an economical and versatile solution for concrete reinforcement.
- Applications: Synthetic fibers are frequently used in residential construction, commercial flooring, and infrastructure projects to minimize shrinkage cracks.
- Benefits: These fibers are lightweight, affordable, and easy to mix into the concrete. They provide excellent crack resistance during the curing phase and improve the concrete’s resistance to wear and tear over time.
- Challenges: Synthetic fibers may not offer the same load-bearing capabilities as steel fibers, making them less suitable for heavy-duty applications.
Natural Fibers
Natural fibers, such as coconut coir, jute, hemp, and sisal, are a sustainable choice for environmentally conscious construction projects.
- Applications: These fibers are used in low-cost housing, temporary structures, and projects emphasizing sustainability. They are particularly valuable in regions where natural fibers are readily available.
- Benefits: Natural fibers are biodegradable, renewable, and provide a low-cost alternative to synthetic or steel fibers. They can also enhance the thermal insulation properties of concrete.
- Challenges: These fibers are less durable than synthetic or steel fibers and may degrade over time if not properly treated. They are best suited for applications where long-term durability is not a primary concern.
Emerging Fiber Technologies
Innovations in fiber technology are constantly expanding the possibilities for FRC. Hybrid fibers, which combine the properties of multiple fiber types, are gaining popularity for their ability to optimize both strength and flexibility. Additionally, advancements in carbon fiber technology are introducing ultra-lightweight and high-strength options for specialized applications, such as aerospace and high-performance structures.
By carefully selecting the appropriate fiber type based on the project’s needs, engineers and builders can leverage FRC’s full potential to create resilient, sustainable, and versatile structures.
Advantages of Fiber Reinforced Concrete
- Crack Resistance
FRC significantly reduces the formation and propagation of micro-cracks, improving the material’s lifespan and structural performance. - Enhanced Durability
With added resistance to wear, impact, and environmental factors, FRC is ideal for high-stress environments like industrial flooring or marine structures. - Improved Toughness
The inclusion of fibers allows FRC to absorb more energy under stress, making it tougher and more resilient than traditional concrete. - Versatility
FRC’s ability to adapt to various construction needs makes it a preferred material for a wide range of projects, from architectural finishes to heavy infrastructure.
Limitations of Fiber Reinforced Concrete
Despite its many benefits, FRC has some drawbacks:
- Fiber Distribution
If not mixed properly, fibers can cluster, leading to uneven performance across the structure. - Cost
FRC is more expensive than traditional concrete due to the additional cost of fibers and the mixing process. - Technical Expertise
Designing FRC for specific applications requires careful consideration of fiber type, dosage, and placement, demanding more technical knowledge than standard concrete.
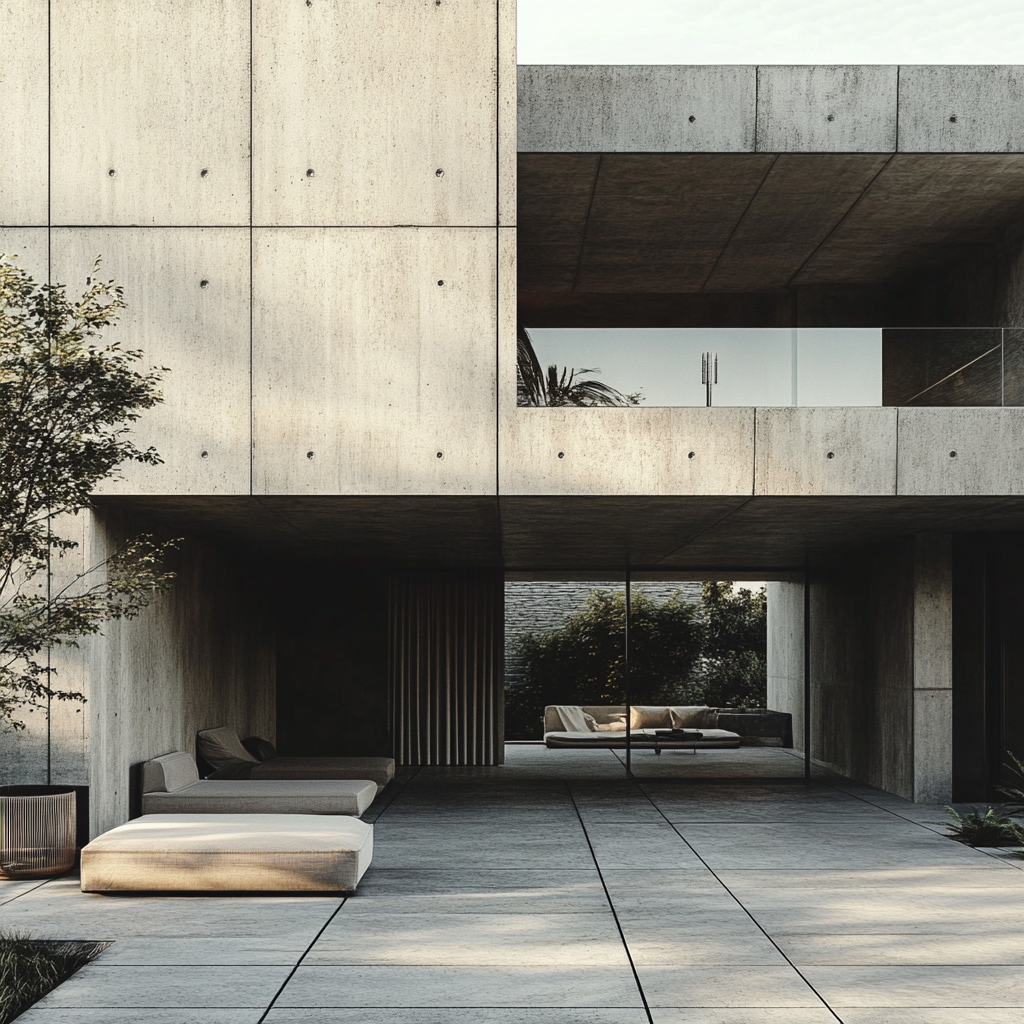
Applications of Fiber Reinforced Concrete
Fiber reinforced concrete’s (FRC) superior performance in terms of strength, durability, and crack resistance has led to its widespread use across various industries. Below is an expanded overview of its key applications:
Industrial Flooring
Industrial floors in warehouses, factories, and distribution centers must endure high foot traffic, heavy machinery, and dynamic loads. FRC’s ability to resist wear and minimize cracking makes it an ideal material for these demanding environments.
- Benefits: FRC enhances the durability and lifespan of floors, reducing maintenance costs and downtime for repairs. Its crack control properties help maintain a smooth surface even under continuous stress.
- Additional Uses: Commonly applied in workshops, storage facilities, and parking garages.
Bridges and Pavements
The load-bearing requirements and environmental exposure faced by bridges and pavements make FRC a valuable material in infrastructure projects.
- Benefits: FRC provides superior tensile strength and impact resistance, ensuring structural integrity under heavy vehicular loads. Its resistance to freeze-thaw cycles and de-icing chemicals enhances longevity in harsh climates.
- Applications: FRC is used in bridge decks, approach slabs, sidewalks, and airport runways.
Precast Products
Precast concrete products like pipes, panels, and manhole covers benefit significantly from the incorporation of fibers.
- Benefits: FRC enhances the durability, reduces the likelihood of cracking during transportation and installation, and improves resistance to impact forces. Its versatility allows for the creation of lightweight, strong, and easily maneuverable components.
- Common Precast Uses: Utility vaults, retaining walls, and modular construction elements.
Marine Structures
Marine environments pose unique challenges due to constant exposure to water, salt, and chemicals. FRC is particularly well-suited to these conditions.
- Benefits: The low permeability of FRC prevents water ingress, while its resistance to chloride-induced corrosion ensures the longevity of structures. It also withstands dynamic forces from waves and tidal movements.
- Applications: Docks, piers, seawalls, underwater pipelines, and harbor facilities.
Residential Projects
FRC has found a place in residential construction due to its affordability, versatility, and aesthetic appeal.
- Benefits: Homeowners and builders leverage FRC’s ability to resist wear and cracking for long-lasting, low-maintenance surfaces. Its flexibility in shaping and finishing allows for creative designs in driveways, patios, and garden paths.
- Applications: Decorative concrete walls, countertops, sidewalks, and flooring in modern homes.
Tunnels and Underground Structures
Underground construction often involves significant structural and environmental pressures. FRC provides the strength and resilience necessary for these applications.
- Benefits: FRC enhances the load-bearing capacity and resistance to deformation under ground pressure. Its ability to control cracking is crucial for maintaining structural integrity in tunnels and subways.
- Applications: Tunnel linings, underground parking lots, and utility conduits.
Defense and Blast-Resistant Structures
In applications where resilience against blasts and impacts is critical, such as military facilities and embassies, FRC provides an added layer of protection.
- Benefits: Fibers improve energy absorption and minimize the propagation of cracks during high-impact events. This ensures structural safety and minimizes damage.
- Applications: Security barriers, fortified walls, and protective shelters.
Architectural Elements
FRC is also valued for its aesthetic potential in architectural projects, where it combines strength with design flexibility.
- Benefits: Its ability to be molded into intricate shapes and textures makes it ideal for creative designs. FRC maintains durability without compromising the visual appeal of structures.
- Applications: Sculptures, facades, ornamental panels, and decorative columns.
Future Applications
As advancements in fiber technology continue, FRC is being explored for cutting-edge applications such as 3D-printed structures, eco-friendly construction, and high-performance sports facilities. By offering enhanced durability, sustainability, and versatility, FRC is poised to play a key role in shaping modern infrastructure and architecture.
Fiber Reinforced Concrete vs Traditional Concrete
Strength and Durability
One of the primary distinctions between fiber reinforced concrete (FRC) and traditional concrete lies in their strength and durability.
- Crack Resistance: Traditional concrete is prone to cracking under tensile stress, which can compromise the structural integrity over time. FRC, on the other hand, incorporates fibers—such as steel, glass, or synthetic materials—that distribute stress more evenly, reducing the likelihood of cracks forming and propagating.
- Impact Resistance: FRC is better equipped to handle dynamic and impact loads, making it ideal for applications such as industrial flooring and pavements subjected to heavy traffic. Traditional concrete, while strong in compression, lacks the tensile strength and flexibility provided by the fibers in FRC.
- Durability: FRC’s enhanced resistance to environmental factors like freeze-thaw cycles, chemical attacks, and abrasion gives it a longer lifespan compared to traditional concrete. This makes it particularly advantageous in marine structures, bridges, and other high-stress environments.
Cost
The cost difference between FRC and traditional concrete can influence project budgets, but a broader perspective reveals significant advantages for FRC in the long run.
- Initial Costs: Traditional concrete is more economical upfront, as it relies solely on standard materials like cement, aggregates, and water. The addition of fibers in FRC increases material costs, making it more expensive initially.
- Long-Term Savings: Despite its higher initial cost, FRC often proves to be more cost-effective over the lifecycle of a project. Its reduced need for repairs and maintenance offsets the initial investment. For instance, in industrial or marine applications where durability is critical, the extended lifespan of FRC reduces the frequency of replacements and associated downtime costs.
Applications
The choice between FRC and traditional concrete often depends on the demands of the specific application.
- Low-Stress Projects: Traditional concrete is sufficient for applications that do not experience significant tensile stress or require enhanced durability. Examples include residential sidewalks, patios, and non-load-bearing structures.
- High-Stress Environments: FRC excels in projects where structural integrity is paramount. It is the preferred choice for demanding applications such as:
- Bridges and Tunnels: Where heavy loads and environmental wear demand high tensile and compressive strength.
- Industrial Flooring: To withstand the impact of heavy machinery and dynamic loads.
- Marine Structures: Where resistance to waterborne chemicals and abrasion is critical.
- Architectural Elements: To achieve complex designs while maintaining durability.
Flexibility in Design
FRC provides enhanced design flexibility compared to traditional concrete. The fibers allow for thinner sections without compromising strength, enabling architects and engineers to experiment with innovative shapes and textures. Traditional concrete lacks this level of versatility, making it less ideal for projects requiring intricate details or lightweight designs.
Environmental Impact
- Traditional Concrete: Producing traditional concrete has a significant environmental footprint due to the high energy consumption and CO₂ emissions associated with cement manufacturing.
- Fiber Reinforced Concrete: While FRC shares these environmental challenges, its longer lifespan and ability to incorporate recycled materials (e.g., waste glass, fly ash, or synthetic fibers) make it a more sustainable choice in many projects.
Choosing the Right Option
The decision to use FRC or traditional concrete should consider project requirements, budget constraints, and long-term performance goals. For projects prioritizing strength, durability, and sustainability, FRC offers clear advantages. For less demanding applications, traditional concrete remains a cost-effective and practical solution. By weighing these factors, builders and engineers can select the material best suited to their specific needs.
The Future of Fiber Reinforced Concrete
Fiber reinforced concrete is at the forefront of innovation in construction. Engineers are increasingly looking to nature for inspiration, drawing on the structure of bones and shells to develop more efficient fiber patterns. Advances in materials science, such as biodegradable fibers and self-healing concrete, promise to make FRC even more sustainable.
Additionally, technologies like 3D printing and AI-driven design are enabling the creation of custom fiber-reinforced patterns tailored to specific applications. These advancements will expand the possibilities for FRC, ensuring it remains a key material in modern construction.
Conclusion
Fiber reinforced concrete represents a significant advancement in construction technology, offering improved strength, durability, and versatility over traditional concrete. While it comes with higher upfront costs and technical requirements, its long-term benefits make it a worthwhile investment for demanding applications. As innovations continue to emerge, FRC is set to play an even greater role in shaping the future of sustainable and resilient infrastructure.
Additional Resources
Get your welding gear here.
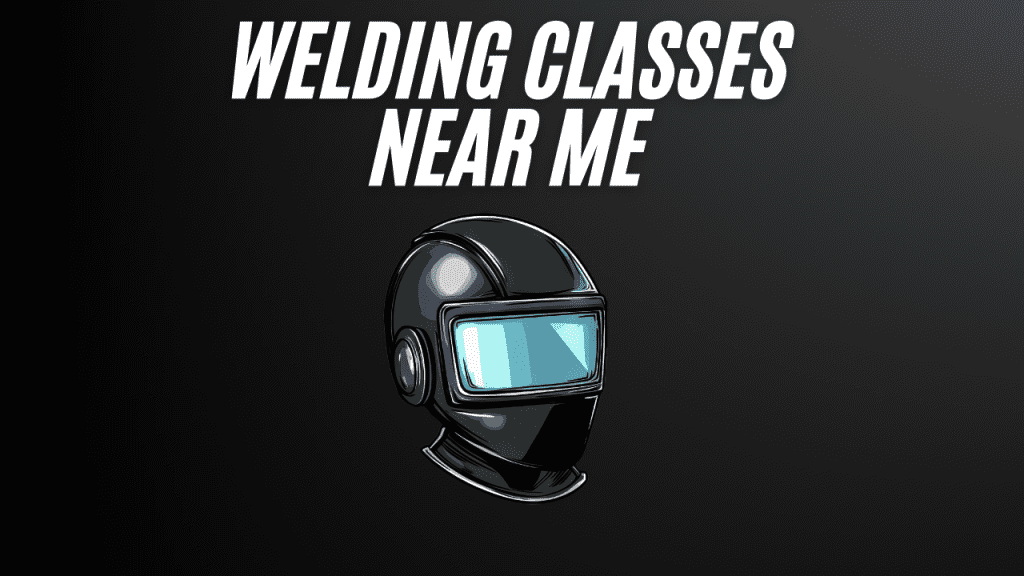