Table of Contents
What Gas Should You Use for MIG Welding Mild Steel?
When welding mild steel, the choice of shielding gas plays a critical role in determining the quality, strength, and appearance of the weld. Among various options, a 75% argon and 25% carbon dioxide (C25) mix is a popular and effective choice, but other gases, such as 100% carbon dioxide, also have their advantages. Here’s a detailed guide to selecting the right gas for MIG welding mild steel and understanding the underlying reasons for their suitability.
The Purpose of Shielding Gas in MIG Welding
Shielding gas is a critical component in the MIG (Metal Inert Gas) welding process, serving both protective and functional roles. Its primary function is to protect the molten weld pool from atmospheric contaminants like hydrogen, nitrogen, and oxygen. These gases, when introduced into the weld pool, can cause defects such as porosity, which weakens the weld and leaves it riddled with tiny holes upon solidification. The shielding gas creates a protective “blanket” over the weld pool, preventing exposure to air and ensuring the weld’s integrity and strength.
However, the role of shielding gas extends beyond mere protection. The type of gas used has a direct impact on several key aspects of the welding process:
Arc Performance
The stability of the electric arc is crucial for achieving consistent and high-quality welds. Shielding gases influence the arc’s stability and behavior, which in turn affects penetration depth and the smoothness of the weld. For example:
- Argon-rich gases provide a smoother and more stable arc, especially in spray transfer mode.
- Carbon dioxide creates a more aggressive arc with deeper penetration, suitable for heavy-duty applications.
Spatter Levels
Spatter refers to small molten metal droplets that are expelled during the welding process. Excessive spatter not only wastes material but also increases cleanup time. The choice of shielding gas plays a significant role in controlling spatter levels:
- Argon-based mixtures typically produce less spatter, resulting in cleaner welds.
- 100% carbon dioxide may lead to higher spatter levels, requiring more post-weld cleaning.
Weld Appearance
The appearance of the finished weld, including its smoothness and bead profile, is heavily influenced by the shielding gas. Argon-rich gases contribute to aesthetically pleasing welds with minimal discoloration, making them ideal for projects where visual quality is a priority.
Transfer Modes
The type of shielding gas determines the welding transfer mode, which affects the weld’s characteristics and efficiency. Common transfer modes include:
- Short Circuit Transfer: Achieved with carbon dioxide or argon-CO₂ mixtures, this mode is suitable for thinner materials and provides excellent control.
- Spray Transfer: Requires argon-rich gases and is ideal for thicker materials and high-speed welding.
- Globular Transfer: Typically associated with pure CO₂, this mode creates larger droplets and is less efficient than spray transfer.
The Bigger Picture: Shielding Gas as a Welding Variable
Selecting the right shielding gas is not just about protecting the weld pool; it is a strategic decision that impacts the overall welding process. From ensuring strong, defect-free welds to optimizing productivity and minimizing cleanup, the shielding gas is a vital factor in achieving professional-grade results. By understanding the effects of different gases on arc stability, spatter, appearance, and transfer modes, welders can tailor their choice to specific materials, techniques, and project requirements.
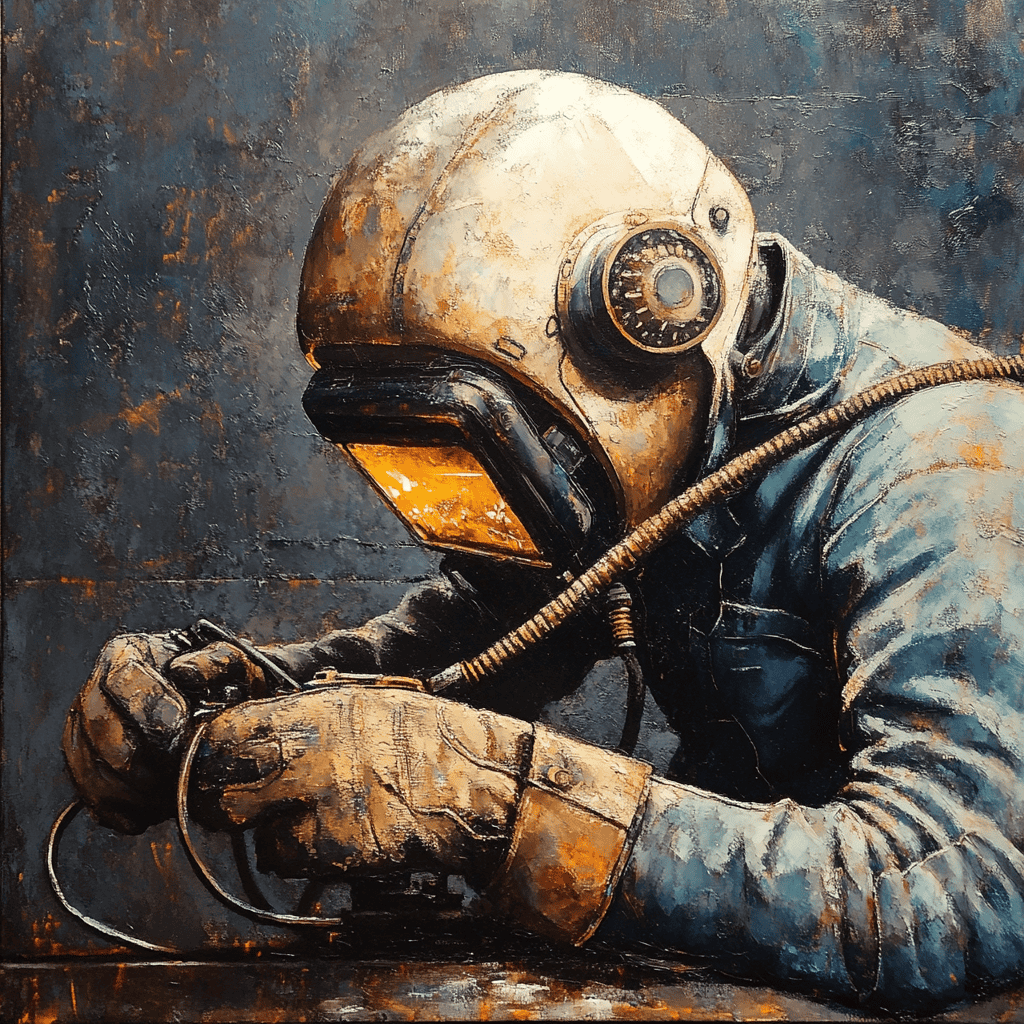
Common Shielding Gases for MIG Welding Mild Steel
The choice of shielding gas for MIG welding mild steel significantly impacts the quality, efficiency, and cost of your welds. Here’s a closer look at the most commonly used gases and their advantages and limitations:
75% Argon / 25% Carbon Dioxide (C25 Mix)
Why Choose C25?
The C25 mix is the gold standard for welding mild steel, striking an ideal balance between performance and cost. This blend is particularly popular because it:
- Produces a stable arc, leading to consistent weld quality.
- Minimizes spatter, reducing cleanup time and improving efficiency.
- Creates clean welds with smooth bead profiles, making it suitable for projects requiring aesthetic finishes.
- Works exceptionally well in short circuit transfer mode, providing excellent control and ease of use.
C25 is highly versatile and is used by both professionals and hobbyists for a wide range of applications, from automotive repairs to general fabrication.
Drawbacks:
The main drawback of C25 is its cost. It is more expensive than pure carbon dioxide, which might deter budget-conscious welders. However, the reduction in spatter and cleanup time often justifies the higher price.
100% Carbon Dioxide (C100)
Why Choose C100?
For those seeking a budget-friendly option, 100% carbon dioxide is an excellent choice. This shielding gas provides:
- Deep penetration, making it suitable for thicker materials and structural welding.
- Cost savings, as carbon dioxide is cheaper and more readily available than argon-based mixes.
- Improved performance thanks to advancements in welding machine technology, which have mitigated some of its traditional drawbacks, such as spatter.
Drawbacks
While C100 is economical, it does come with some trade-offs:
- It produces more spatter than C25, requiring additional post-weld cleanup.
- The arc is slightly less stable, which can affect weld quality, particularly for less experienced welders.
- It is less suited for thin materials, where excessive heat can cause burn-through.
Despite these challenges, C100 remains a solid choice for heavy-duty and cost-sensitive projects.
90% Argon / 10% Carbon Dioxide (C10 Mix)
Why Choose C10?
C10 is a premium choice for welders aiming for high-quality results, especially in spray transfer mode. Its benefits include:
- Smooth and visually appealing welds with minimal spatter.
- A highly stable arc, which is essential for precision work.
- Excellent for professional applications where appearance and performance are prioritized.
C10 is often used in industries like manufacturing and construction, where high-performance welding is critical.
Drawbacks
The higher cost of C10 compared to C25 or C100 makes it less practical for hobbyists or welders on a tight budget. It is also more specialized, meaning it may not be as versatile for general-purpose welding.
Why Not Use 100% Argon for Mild Steel?
While 100% argon is a top choice for welding non-ferrous metals like aluminum or stainless steel, it is unsuitable for mild steel. Pure argon:
- Results in poor penetration, which can compromise the strength of the weld.
- Produces an unstable arc, leading to inconsistent welds.
- Often creates weak and brittle welds, making it impractical for structural applications.
Its role in MIG welding is specialized for spray transfer mode with materials like aluminum, where its low ionization energy helps achieve smooth, high-quality welds.
The right shielding gas for MIG welding mild steel depends on your specific needs, including budget, material thickness, and project requirements. C25 is the most versatile and user-friendly choice for most applications, while C100 offers a cost-effective solution for heavy-duty work. For professional-grade results and specialized techniques like spray transfer, C10 is an excellent option. Understanding these options ensures you select the best gas for your welding needs, delivering strong, clean, and efficient welds every time.
Advanced Shielding Gas Mixtures for Specialized Applications
For welders seeking to optimize performance or tackle unique challenges, advanced shielding gas mixtures offer tailored solutions. These mixes enhance specific aspects of the welding process, such as bead aesthetics, weld strength, or arc stability, making them invaluable for certain industries and applications.
Argon-Helium Mixes
Applications: Ideal for aluminum and stainless steel welding, especially in spray transfer mode.
- Benefits: Helium enhances heat input, improving weld penetration and wetting action. This is particularly useful for thick materials or when working in colder environments.
- Drawbacks: The cost of helium is significantly higher than other gases, limiting its use for budget-conscious welders.
Argon-Carbon Dioxide-Oxygen Mixes
Applications: Used in structural steel welding and automotive manufacturing for robust and clean welds.
- Benefits: Adding a small percentage of oxygen (1–2%) to argon-CO₂ blends stabilizes the arc and reduces spatter. This mix produces a clean bead profile with excellent fusion.
- Drawbacks: Oxygen may not be suitable for stainless steel or materials prone to oxidation, as it can compromise corrosion resistance.
Helium-TriMix (Helium, Argon, Carbon Dioxide)
Applications: Commonly used for stainless steel in high-performance applications, such as chemical plants or food-grade equipment.
- Benefits: Helium enhances arc energy, while argon ensures smooth welds, and CO₂ promotes fusion. The combination creates a versatile mix for challenging projects.
- Drawbacks: High cost and limited availability make it less practical for non-industrial use.
Specialty Gases for MIG Brazing
Applications: Used for joining dissimilar metals or delicate components in automotive or artistic projects.
- Recommended Gas: 100% argon is typically the best choice for brazing with silicon bronze filler materials.
- Benefits: This setup creates smooth and visually appealing joints with minimal heat distortion.
By exploring these advanced gas mixtures, welders can fine-tune their setups for specific requirements, achieving superior results in specialized welding scenarios.
Best Practices for Using Shielding Gas in MIG Welding
Achieving optimal results in MIG welding requires careful attention to shielding gas management. Following these best practices ensures strong, clean welds and minimizes defects.
1. Proper Setup and Flow Rate
A proper shielding gas setup is critical to achieving consistent weld quality.
- Purge Before Connection: Before attaching the regulator, briefly open the gas valve to release a small amount of gas and purge any contaminants like dust or moisture from the connection. This simple step prevents impurities from entering the system.
- Set the Right Flow Rate: The recommended flow rate for short circuit MIG welding is 25–35 cubic feet per hour (CFH). Adjust the rate based on the welding environment; for example, higher flow rates might be needed in outdoor or breezy conditions. However, excessive flow can create turbulence, drawing in atmospheric contaminants that lead to porosity in the weld.
2. Check Connections
Secure and accurate connections are essential to maintain proper shielding gas flow.
- Verify Regulator and Gun Connections: Ensure all connections, including the regulator, hose, and MIG gun, are tightly sealed. Loose fittings can cause gas leaks, reducing effectiveness and increasing waste.
- Correct Port Selection: On multi-process welding machines, ensure the gas hose is connected to the proper port. Many machines have separate ports for MIG and TIG welding, so double-check to avoid misconfiguration.
- Use an External Flow Meter: An external flow meter attached to the MIG gun allows you to measure the gas flow directly at the weld. This ensures precise adjustments, especially when troubleshooting issues with gas coverage.
3. Clean Your Consumables
Consumables play a vital role in directing shielding gas over the weld pool. Dirty or clogged consumables can disrupt gas flow and compromise weld quality.
- Inspect Regularly: Check the nozzle, contact tip, and diffuser for spatter buildup or blockages after each welding session.
- Clean Effectively: Use pliers or specialized cleaning tools to remove debris from the nozzle and diffuser. Ensuring these components are clean helps maintain consistent gas coverage and reduces the risk of porosity.
4. Adjust Contact Tip to Work Distance (CTWD)
The distance between the contact tip and the workpiece significantly impacts shielding gas coverage and weld quality.
- Maintain Optimal CTWD: Keep the contact tip 1/4 to 5/8 inches from the work surface. This range ensures proper shielding gas coverage while maintaining arc stability.
- Avoid Excessive Distance: Welding too far from the surface can cause the shielding gas to dissipate before it fully covers the weld pool, leading to porosity and defects. Conversely, being too close can restrict gas flow and increase spatter.
Additional Tips for Effective Gas Management
- Wind Blocks for Outdoor Welding: When welding outdoors, use physical barriers like screens or tents to protect the shielding gas from being blown away by wind.
- Check for Leaks: Periodically inspect hoses and fittings for cracks or leaks. Gas leaks not only waste shielding gas but also reduce weld protection.
- Store Gas Cylinders Safely: Keep shielding gas cylinders upright and secured in a well-ventilated area to prevent accidents and maintain gas quality.
By implementing these best practices, welders can maximize the effectiveness of their shielding gas, resulting in cleaner, stronger welds and minimizing the risk of defects. Proper gas management not only improves weld quality but also ensures efficient use of resources, saving time and cost in the long run.
Conclusion
For MIG welding mild steel, a 75% argon and 25% carbon dioxide mix (C25) is the most versatile and effective choice, providing clean, strong, and aesthetically pleasing welds. However, budget-friendly options like 100% carbon dioxide are suitable for less critical applications. For specialized tasks, consider mixes like 90% argon and 10% carbon dioxide. Ultimately, the right gas depends on your specific project requirements, budget, and desired weld quality. By understanding the role of shielding gas and following best practices, you can achieve professional-grade results in your welding projects.
Additional Resources
Get your welding gear here.
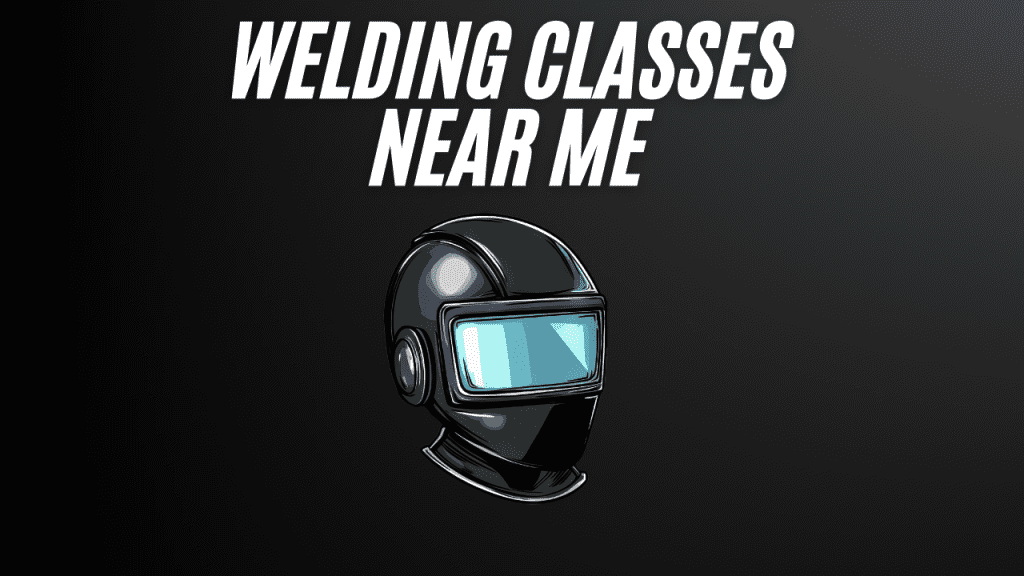