Table of Contents
What Do Plastic Workers Do?
Introduction
Plastic is an essential part of modern life, found in everything from packaging and automotive parts to medical devices and electronics. Behind these products are skilled professionals known as plastic workers, whose expertise drives the production, repair, and innovation of plastic components. This article explores the roles, responsibilities, and importance of plastic workers in today’s industries.
What Do Plastic Workers Do?
Overview of Plastic Workers’ Responsibilities
Plastic workers are at the core of the plastic manufacturing and repair industries, contributing to the creation, maintenance, and recycling of a vast array of products that are integral to modern life. Their responsibilities involve shaping, joining, and assembling plastic materials into functional components and finished goods. From designing new items to repairing damaged parts and reducing waste through recycling, plastic workers play a vital role in ensuring the functionality, durability, and quality of plastic products across industries.
Key Responsibilities of Plastic Workers
1. Fabrication of Plastic Products
Plastic workers use specialized techniques to cut, mold, and shape plastic materials into desired forms. This involves processes like thermoforming, injection molding, and extrusion to produce items ranging from simple containers to complex industrial components. Their precision and expertise ensure the final product meets design specifications and functional requirements.
2. Repair and Maintenance
In addition to creating new items, plastic workers are often called upon to repair damaged or worn plastic components. This could involve welding cracks in plastic tanks, fixing broken automotive parts, or restoring structural integrity to industrial equipment. Repairing rather than replacing items helps reduce costs and supports sustainability efforts.
3. Assembly of Plastic Components
Plastic workers are responsible for assembling various plastic parts into finished products. This may involve joining multiple pieces using techniques such as welding, adhesives, or mechanical fasteners. Their work is essential for creating items like automotive interiors, medical devices, and consumer goods.
4. Recycling and Reprocessing
Sustainability is becoming an increasingly important aspect of the plastic industry. Plastic workers play a critical role in recycling by sorting, cleaning, and reprocessing used plastics into raw materials that can be reused. This helps reduce environmental impact and supports circular economy initiatives.
5. Quality Control
Ensuring the quality of plastic products is a significant responsibility for plastic workers. They conduct inspections and tests to verify that products meet industry standards, are free of defects, and are safe for use. This involves checking dimensions, strength, and visual appearance to guarantee customer satisfaction.
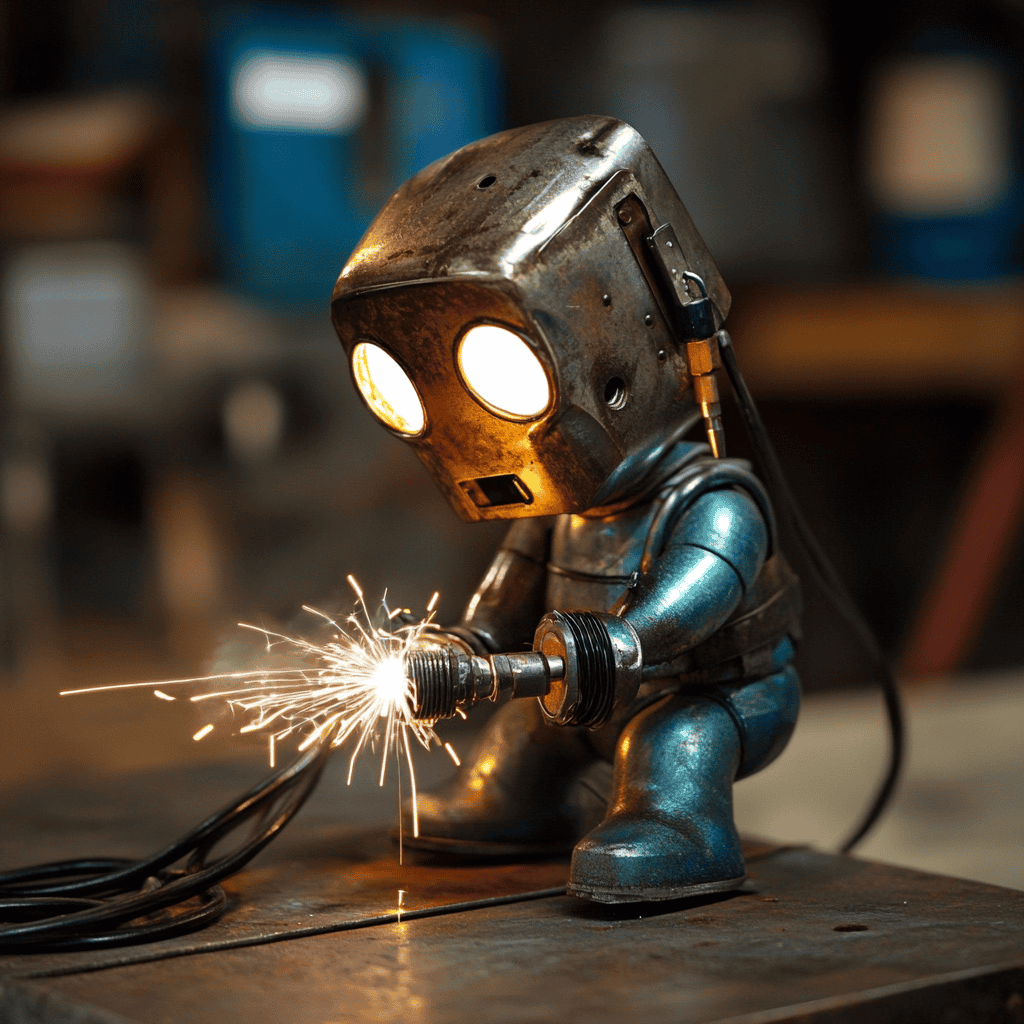
Industries Employing Plastic Workers
Automotive Industry
Plastic workers contribute to the production and maintenance of vehicle components such as dashboards, bumpers, and fuel tanks. Their work enhances vehicle safety, durability, and performance while reducing weight for improved fuel efficiency.
Construction Industry
In construction, plastic workers fabricate and assemble items like pipes, insulation materials, roofing membranes, and window frames. These components are essential for building durable and energy-efficient structures.
Healthcare Industry
Plastic workers produce critical medical devices and equipment, including syringes, prosthetics, and surgical instruments. Their precision ensures these products meet strict safety and hygiene standards.
Packaging Industry
In packaging, plastic workers create items like bottles, containers, and wrapping materials. Their efforts ensure products are securely stored and transported, reducing spoilage and waste.
Electronics Industry
Plastic workers fabricate housings, connectors, and other components for electronic devices. Their work supports the production of durable, lightweight, and aesthetically pleasing consumer electronics.
The Impact of Plastic Workers
Plastic workers are essential for maintaining the functionality and efficiency of countless industries. By fabricating durable products, repairing damaged parts, and contributing to recycling efforts, they help industries operate more sustainably. Their role in ensuring the quality and reliability of plastic components supports innovation and enhances the products we use every day.
Types of Plastic Work
Plastic workers engage in various specialized tasks that cater to the needs of industries reliant on plastic materials. These tasks include fabrication, welding, mold making, casting, and recycling, each requiring unique skills and techniques. Here’s a deeper dive into these key areas of plastic work:
Plastic Fabrication
Plastic fabrication is the process of cutting, shaping, and assembling plastic materials to meet specific design requirements. It involves various techniques, such as:
- Thermoforming: Heating plastic sheets until they are pliable and then molding them into specific shapes using molds or vacuum pressure. This technique is commonly used for packaging, trays, and lightweight structural components.
- Extrusion: Forcing melted plastic through a shaped die to create continuous profiles, such as pipes, tubes, and sheets. This method is widely used in the construction and plumbing industries.
- Injection Molding: Injecting molten plastic into a mold to create complex and detailed components. Injection molding is used extensively in industries like automotive, electronics, and medical device manufacturing.
Plastic fabrication produces a wide range of products, including panels, containers, structural components, and decorative items. This work is integral to industries ranging from construction to consumer goods, where precision and durability are paramount.
Plastic Welding
Plastic welding is a vital technique for joining and repairing plastic components. Unlike metal welding, plastic welding uses heat and pressure to fuse materials without altering their chemical composition. Common methods include:
- Hot Air Welding: Directing a stream of hot air onto plastic surfaces to melt and join them. This technique is widely used for repairing items like tanks, linings, and ducts.
- Ultrasonic Welding: Using high-frequency vibrations to generate heat at the interface of two plastic parts. This method creates strong, seamless bonds and is commonly used in electronics, medical devices, and automotive components.
- Extrusion Welding: Melting and depositing plastic filler material to join parts, ideal for larger components such as pipes or tanks in the construction industry.
Plastic welding is crucial for industries such as automotive, construction, and manufacturing, where strong, reliable joints are essential for product performance and safety.
Mold Making and Casting
Mold making and casting are foundational processes for mass-producing plastic products. This work involves creating molds, which serve as templates for shaping plastic into specific forms. The process typically includes:
- Creating Molds: Using materials like silicone, resin, or metal to design molds that replicate the desired product shape.
- Casting: Pouring or injecting molten plastic into molds to form components such as medical devices, packaging, and industrial parts.
Precision is critical in mold making, as any flaws in the mold can result in defects in the final product. Plastic workers in this field ensure that molds are accurate, durable, and suitable for repeated use in high-volume production.
Recycling and Reprocessing
As sustainability becomes a global priority, plastic workers are increasingly involved in recycling and reprocessing tasks. These efforts focus on reducing plastic waste and creating reusable materials, which is essential for promoting environmental conservation. Key activities include:
- Breaking Down Used Plastics: Sorting and shredding waste materials into smaller pieces for easier processing.
- Cleaning and Processing: Removing contaminants and preparing recycled plastics for reuse in manufacturing.
- Creating New Products: Using recycled plastics to produce items like containers, building materials, and textiles.
Recycling and reprocessing not only help minimize environmental impact but also reduce the need for virgin plastic, lowering production costs and resource consumption.
Each type of plastic work—fabrication, welding, mold making, and recycling—plays a critical role in creating, maintaining, and repurposing plastic materials. These specialized tasks ensure that industries can rely on durable, functional, and sustainable plastic products for a variety of applications. As technology advances and the focus on sustainability grows, the scope and impact of plastic work continue to expand.
Tools and Equipment Used by Plastic Workers
Plastic workers rely on a diverse array of tools and machinery, ranging from basic hand tools to advanced automated systems, to fabricate, assemble, and repair plastic components. The choice of tools depends on the specific task, the type of plastic being worked on, and the desired outcome. Proper safety gear is equally important to ensure a safe working environment when handling hazardous materials and processes.
Basic Tools
Basic tools are essential for everyday tasks and allow plastic workers to shape, cut, and manipulate plastic materials with precision. These include:
- Heat Guns: Used to soften plastic for bending, shaping, or welding. Heat guns are adjustable for different temperatures, making them versatile for various types of plastics.
- Utility Knives and Saws: Tools like rotary cutters, hacksaws, and fine-toothed saws are used for cutting plastic sheets, pipes, and other components.
- Hand Sanders and Files: Used to smooth rough edges, finish surfaces, and prepare materials for assembly or welding.
Welding Machines
Plastic welding machines are specialized tools for joining plastic components. Common types include:
- Hot Air Welders: Direct a stream of hot air to melt plastic surfaces, often used for repairs and lightweight materials.
- Ultrasonic Welders: Employ high-frequency vibrations to fuse materials, ideal for small, intricate components like electronic casings or medical devices.
- Extrusion Welders: Combine molten plastic filler material with the base material for durable, high-strength welds in large-scale projects such as tanks and pipelines.
Extrusion Equipment
Extrusion equipment is critical for creating continuous shapes like pipes, tubes, and profiles. It forces melted plastic through a shaped die, forming consistent cross-sections. Extrusion machines are widely used in industries like construction and automotive for fabricating structural components.
Advanced Machinery
Advanced tools and machinery enhance efficiency, precision, and scalability in plastic work. These include:
- CNC Machines: Computer-controlled cutting and shaping tools that provide unmatched accuracy for intricate designs and components.
- 3D Printers: Enable rapid prototyping and the creation of complex parts using additive manufacturing techniques.
- Robotic Systems: Automate repetitive tasks like welding and assembly, ensuring consistency and speed in high-volume production environments.
Safety Gear
Safety gear is crucial for protecting plastic workers from hazardous materials, high temperatures, and sharp tools. Essential items include:
- Gloves: Heat-resistant or cut-resistant gloves safeguard hands during cutting, welding, or handling hot materials.
- Respirators: Protect against harmful fumes and particles generated during processes like welding or cutting.
- Protective Clothing: Flame-resistant jackets, aprons, and boots shield workers from burns, sparks, and chemical exposure.
- Eye Protection: Safety goggles or face shields guard against flying debris, sparks, and harmful radiation from welding arcs.
Skills and Qualifications
To excel in their roles, plastic workers need a combination of technical expertise and soft skills, along with appropriate education and training.
Technical Skills
Technical skills are fundamental for operating machinery, handling materials, and ensuring precision in production processes. These include:
- Machinery Operation: Proficiency with tools like CNC machines, 3D printers, and welding equipment.
- Material Knowledge: Understanding the properties of different plastics, including their melting points, flexibility, and strength, to select the appropriate techniques and tools.
- Cutting and Shaping Precision: The ability to measure and execute detailed cuts, bends, and assemblies for high-quality outcomes.
- Welding Expertise: Skills in various welding methods, such as hot air, ultrasonic, and extrusion welding, to join or repair plastic components effectively.
Soft Skills
Soft skills are equally important, enabling workers to solve problems, collaborate with teams, and maintain attention to detail. These include:
- Problem-Solving Abilities: Diagnosing issues, such as material defects or equipment malfunctions, and identifying effective solutions.
- Attention to Detail: Ensuring accuracy in measurements, cuts, and assemblies to meet design specifications and quality standards.
- Teamwork: Collaborating with colleagues and supervisors to complete complex projects on time and within budget.
Education and Training
Educational requirements for plastic workers can vary depending on the role and industry. Many positions require at least a high school diploma, but additional training can significantly enhance career prospects.
- Vocational Training: Programs in plastic fabrication, welding, or machining provide hands-on experience with tools and techniques.
- Apprenticeships: Combine on-the-job training with classroom instruction, offering real-world experience and mentorship.
- Certifications: Specialized certifications in areas like plastic welding, mold making, or extrusion signal expertise to employers and improve job opportunities.
Career Development
For those seeking advancement, additional education in fields such as mechanical engineering, materials science, or industrial design can open doors to roles in management, research, or product development. Continuous learning is crucial, as the plastic industry evolves with new technologies and sustainability practices.
Plastic workers rely on a comprehensive toolkit of basic and advanced equipment to perform their duties efficiently and safely. Combined with technical proficiency, soft skills, and ongoing training, these tools enable workers to meet the demands of industries ranging from automotive to healthcare. By mastering their equipment and honing their expertise, plastic workers contribute to the creation, maintenance, and innovation of products that are integral to modern life.
Challenges Faced by Plastic Workers
Plastic workers face an array of challenges that stem from the demanding nature of their work, the materials they handle, and the evolving expectations of industries and society. These challenges highlight the complexity of their roles and the necessity for adaptability, technical expertise, and a commitment to safety and environmental responsibility.
Handling Hazardous Materials
Dealing with hazardous materials is one of the most pressing concerns for plastic workers. Adhesives, solvents, and fumes generated during processes like welding and molding can pose significant health risks, including respiratory issues, skin irritation, and long-term exposure hazards. To mitigate these risks, strict safety protocols must be followed, including the use of personal protective equipment (PPE) such as gloves, respirators, and flame-resistant clothing. Ensuring workers consistently adhere to these measures requires continuous training, robust workplace policies, and investment in high-quality safety gear. The challenge is magnified in smaller operations or DIY settings where safety resources may be limited.
Environmental Responsibilities
The growing global awareness of plastic pollution has placed intense scrutiny on the industry, making environmental sustainability a key challenge. Workers are now tasked not only with traditional manufacturing duties but also with adopting and implementing sustainable practices. Recycling and reprocessing have become integral parts of the job, requiring workers to sort, clean, and repurpose used plastics into reusable materials. This shift demands new skills, such as operating specialized recycling equipment, understanding different plastic types, and ensuring compliance with environmental regulations. The push toward sustainability also places workers at the forefront of efforts to develop and handle new materials, such as biodegradable plastics, which come with their own unique challenges.
Keeping Up with Technological Advancements
The rapid pace of technological innovation in the plastic industry adds another layer of complexity. Modern plastic work increasingly relies on cutting-edge technology, from CNC machining to 3D printing and robotic automation. For workers, this means continually updating their knowledge and skills to keep up with these innovations. Learning to operate new machinery, interpret digital designs, and integrate automation into workflows requires time, resources, and access to ongoing education. Additionally, the introduction of advanced materials, such as bioplastics and high-performance polymers, demands an understanding of their properties and the ability to adapt traditional techniques for these new materials.
Career Opportunities for Plastic Workers
Despite these challenges, the career opportunities for plastic workers remain diverse and promising. Their skills are versatile, allowing them to thrive in multiple industries, each offering unique pathways for growth.
Traditional Roles
Plastic workers have long found opportunities in roles such as:
- Production Technicians: Oversee the operation of sophisticated machinery, ensuring efficiency and quality in manufacturing processes.
- Mold Designers: Create precise and durable molds essential for mass-producing components in industries ranging from automotive to consumer goods.
- Quality Inspectors: Maintain high standards by ensuring every product meets rigorous specifications and is free from defects.
Emerging Fields
New technologies and materials have created exciting avenues for plastic workers, including:
- Bioplastics: As eco-friendly alternatives to traditional plastics gain traction, skilled workers are needed to handle these innovative materials. Bioplastics are increasingly used in packaging, automotive, and medical devices, offering roles in both production and research.
- 3D Printing: Additive manufacturing has revolutionized how plastic components are designed and fabricated. Workers with expertise in 3D printing can create intricate and custom parts for industries like aerospace, healthcare, and prototyping.
Sustainability-Focused Roles
With industries prioritizing environmentally responsible practices, sustainability-focused roles are growing rapidly:
- Recycling Specialists: Develop and implement efficient systems for processing and repurposing plastic waste, requiring knowledge of traditional and advanced recycling methods.
- Eco-Friendly Material Fabricators: Create sustainable products, from biodegradable containers to components made entirely from recycled materials, addressing environmental concerns and aligning with consumer demand for greener alternatives.
Opportunities for Growth
Plastic workers also benefit from opportunities for upward mobility. With additional education and training, they can transition into roles such as project managers, research and development specialists, or technical consultants. These positions allow workers to influence the direction of the industry, contribute to technological advancements, and promote sustainability on a larger scale.
Summary
Plastic workers face challenges related to hazardous materials, environmental responsibilities, and technological advancements, but these hurdles also drive innovation and growth within the industry. The diverse career opportunities available, from traditional manufacturing roles to cutting-edge positions in sustainability and technology, reflect the importance and adaptability of plastic workers in meeting the demands of an evolving world. Their contributions not only shape the products and materials we rely on daily but also help build a more sustainable and technologically advanced future.
Importance of Plastic Workers in Society
Plastic workers play an indispensable role in shaping modern society through their expertise in producing, repairing, and innovating plastic components. Their contributions extend across a wide range of industries, ensuring that essential products and systems function efficiently and meet the demands of a rapidly evolving world.
Healthcare
In healthcare, plastic workers are pivotal in the creation of medical devices, tools, and equipment essential for patient care. They fabricate items like syringes, prosthetics, surgical instruments, and sterile packaging, all of which are critical to the delivery of effective medical treatments. Additionally, they contribute to the development of advanced materials for implants and biocompatible components, improving the quality of life for countless individuals. Without their expertise, the medical field would lack many of the vital tools needed for diagnostics, surgeries, and long-term care.
Automotive and Aerospace
In the automotive and aerospace industries, plastic workers produce lightweight, durable components that are essential for safety, efficiency, and performance. In cars, plastic parts such as bumpers, dashboards, and fuel tanks reduce vehicle weight, enhancing fuel efficiency and lowering emissions. Similarly, in aerospace, lightweight polymers and composites are used to fabricate parts like fuselage panels and interior components, reducing the overall weight of aircraft and improving fuel economy. These contributions not only make transportation more sustainable but also enhance safety by using materials that are both resilient and adaptable to extreme conditions.
Construction
In construction, plastic workers create materials and components that support modern infrastructure. Items like pipes, insulation, roofing membranes, and window frames are essential for building energy-efficient and durable structures. Plastic’s versatility allows it to be used in innovative ways, such as in 3D-printed building components or sustainable materials that reduce construction waste.
Consumer Goods and Electronics
Plastic workers contribute significantly to the production of consumer goods and electronics. From durable household items to lightweight electronic casings, their work ensures that products are functional, affordable, and aesthetically appealing. Their expertise in molding and assembling plastics allows manufacturers to meet the growing demand for reliable, cost-effective products in everyday life.
Sustainability and Innovation
Plastic workers are at the forefront of efforts to make the industry more sustainable. By developing and implementing recycling and reprocessing techniques, they help reduce plastic waste and support the creation of eco-friendly products. Their role in advancing biodegradable plastics and other sustainable materials ensures that industries can adapt to increasing environmental regulations and consumer preferences for greener solutions.
The Future of Plastic Work
The future of plastic work is dynamic and shaped by the intersection of technological innovation and environmental priorities. Plastic workers will continue to be vital in addressing the challenges and opportunities presented by these changes.
Technological Advancements
Automation and robotics are revolutionizing plastic production processes. Robotic systems are streamlining tasks like welding, molding, and assembly, ensuring greater consistency, efficiency, and safety. Advanced machinery such as CNC machines and 3D printers are enabling the creation of complex, high-precision components, opening new possibilities for customization and rapid prototyping. Plastic workers skilled in operating and maintaining these technologies will be in high demand as industries adopt increasingly sophisticated systems.
Digital tools are also enhancing quality control and production planning. With real-time monitoring and data analytics, plastic workers can ensure that manufacturing processes are optimized and products meet stringent standards. These technologies not only improve efficiency but also reduce waste, making production more sustainable.
New Materials and Applications
The development of new materials, such as biodegradable plastics and high-performance polymers, is reshaping the industry. Biodegradable plastics offer an eco-friendly alternative to traditional plastics, reducing the environmental impact of packaging, single-use items, and disposable goods. Plastic workers play a crucial role in handling these materials, from understanding their properties to adapting manufacturing processes for their use.
High-performance polymers are expanding the applications of plastics in industries like aerospace, medical devices, and renewable energy. These materials offer exceptional strength, heat resistance, and durability, allowing plastic workers to create components for advanced technologies like wind turbines, solar panels, and space exploration equipment.
Sustainability Initiatives
The push for sustainability is a driving force in the evolution of plastic work. Recycling and reprocessing technologies are advancing, enabling the industry to recover and reuse more plastic waste. Plastic workers are integral to these efforts, operating specialized recycling equipment and developing innovative methods for creating high-quality products from recycled materials.
Circular economy practices are gaining momentum, emphasizing the reuse and repurposing of materials to minimize waste. Plastic workers will be at the forefront of implementing these practices, from designing products that are easier to recycle to creating closed-loop systems that keep materials in use for longer.
Global and Environmental Challenges
As industries face increasing pressure to reduce their carbon footprint, plastic workers will need to adapt to stricter environmental regulations and shifting consumer expectations. Their expertise in sustainable materials and processes will be crucial for helping companies meet these demands while maintaining quality and profitability.
Evolving Roles and Skills
The future will require plastic workers to continuously upgrade their skills to keep pace with new technologies and materials. Training programs and certifications in areas like advanced machinery operation, bioplastics, and sustainable manufacturing will become essential. Plastic workers who embrace lifelong learning and adaptability will have a significant advantage in a competitive and rapidly changing industry.
Summary
Plastic workers are indispensable to the industries that power modern society, from healthcare and transportation to construction and consumer goods. Their contributions to innovation, sustainability, and efficiency are essential for meeting the challenges of today and the demands of tomorrow. As technological advancements and environmental priorities reshape the industry, skilled plastic workers will remain at the forefront, driving progress and building a more sustainable future. Their expertise ensures that plastic continues to be a versatile and valuable material, supporting the growth and evolution of countless sectors.
Conclusion
Plastic workers are the unsung heroes of industries that rely on durable, versatile, and innovative plastic components. From fabricating and welding to recycling and reprocessing, their skills ensure that modern products meet the highest standards of quality and sustainability. For individuals interested in a dynamic and impactful career, plastic work offers endless opportunities to contribute to essential industries while shaping a more sustainable future.
Additional Resources
Get your welding gear here.
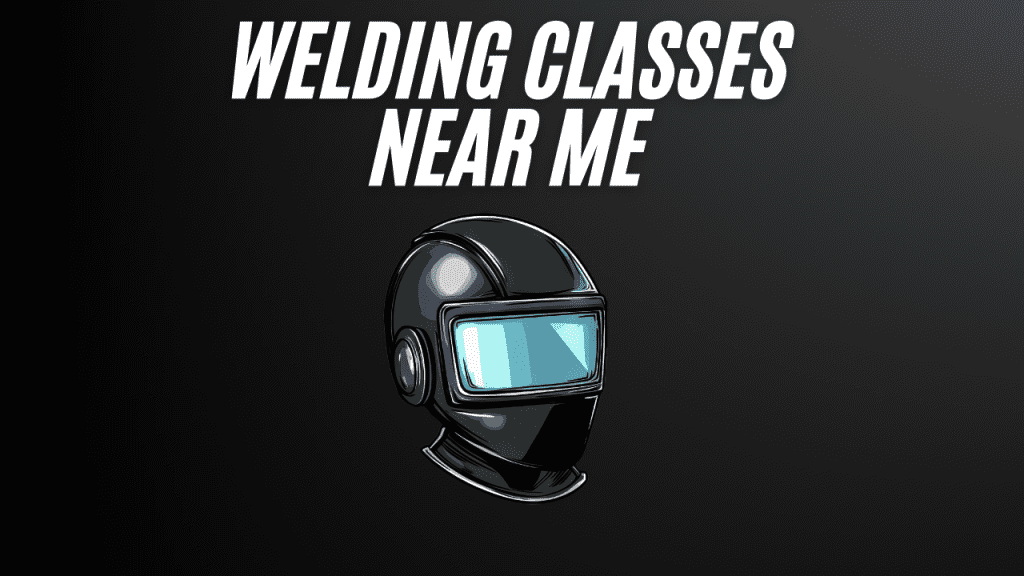