Table of Contents
What Are the Types of Welding Machines?
Introduction
When asking about welding machines, most answers seem to focus on the types of welding processes (MIG, TIG, stick, etc.). However, understanding the specific types of welding machines is equally important because each machine offers unique advantages, capabilities, and applications for different projects. Here’s an in-depth look at the most common welding machines and what they bring to the table.
What Are the Types of Welding Machines?
1. Inverter Welding Machines: Compact, Versatile, and Efficient
Inverter welding machines have revolutionized the welding industry with their advanced technology and unmatched portability. Unlike traditional transformer-based welders, inverter welders use silicon-based electronic components to efficiently convert alternating current (AC) into direct current (DC). This innovation provides greater control, reduced energy consumption, and a wide range of applications, making these machines a favorite among professionals and hobbyists alike.
What Sets Inverter Welding Machines Apart?
Inverter welders stand out for their ability to pack powerful performance into a compact design. Here’s a closer look at their unique features:
- Compact and Portable: Inverter welders are significantly smaller and lighter than traditional welding machines. Their portability makes them ideal for working in tight spaces, remote locations, or areas with limited access. Many models weigh under 20 pounds, making them easy to transport and store.
- Energy Efficiency: Inverter technology consumes less electricity compared to transformer-based machines, resulting in lower operating costs. They achieve high power output with reduced energy input, making them eco-friendly and cost-effective.
- Precise Control: Equipped with digital interfaces, inverter welders allow users to fine-tune welding parameters such as current, voltage, and arc force. This precision ensures cleaner welds and reduces material waste.
- Wide Voltage Compatibility: Many inverter welders operate on standard 110-volt outlets, making them accessible for home use without requiring high-voltage connections or industrial generators.
Advantages of Inverter Welding Machines
- Versatility
Inverter welders are compatible with multiple welding processes, including TIG, MIG, and stick welding. This versatility allows users to tackle a variety of projects, from light repairs to complex fabrications. - Reliability
Built with solid-state electronics, inverter welders are durable and require less maintenance than traditional machines. Their stable arc performance ensures consistent weld quality, even in challenging conditions. - Adaptability
Inverter welders are suitable for both small-scale and professional applications. Their ability to run on household power outlets and generators makes them a practical choice for workshops, construction sites, and fieldwork. - Cost-Effective
While the initial cost of an inverter welder may be higher than that of a traditional machine, the long-term savings in energy consumption and maintenance make it a worthwhile investment.
Applications of Inverter Welding Machines
Inverter welding machines excel in a variety of settings, including:
- Home Workshops: Perfect for DIY enthusiasts working on small-scale repairs or custom projects.
- Construction Sites: Lightweight and portable, they are ideal for welding in hard-to-reach areas or elevated locations.
- Automotive Repairs: Provide precise control needed for welding car panels, exhaust systems, and other delicate components.
- Maintenance and Repairs: Frequently used for fixing machinery, metal structures, and equipment in industrial settings.
Advanced Features in Modern Inverter Welders
Modern inverter welders often come with innovative features that enhance usability and performance:
- Pulse Welding: Allows precise heat control, reducing distortion and making it suitable for thin materials.
- Hot Start Function: Provides an extra boost of current during arc initiation, ensuring a smooth start.
- Anti-Stick Technology: Prevents the electrode from sticking to the workpiece, improving ease of use and efficiency.
- Dual Voltage Capability: Some models can switch between 110V and 220V, providing flexibility for different power sources.
Considerations When Choosing an Inverter Welding Machine
- Project Requirements: Assess whether the welder’s capabilities align with your projects, including the type of materials and welding processes needed.
- Power Availability: Check if your workspace has the appropriate outlets or if you’ll need a generator.
- Durability: Look for models with a robust build and reliable cooling systems to handle extended use.
- Budget: While inverter welders offer long-term savings, consider your upfront investment and ensure it fits your needs.
Inverter welding machines have transformed the welding industry with their compact size, energy efficiency, and versatility. Whether you’re a professional welder or a DIY enthusiast, these machines offer the precision, reliability, and portability needed to tackle a wide range of projects. From home workshops to industrial job sites, inverter welders are a game-changing tool for modern welding applications.
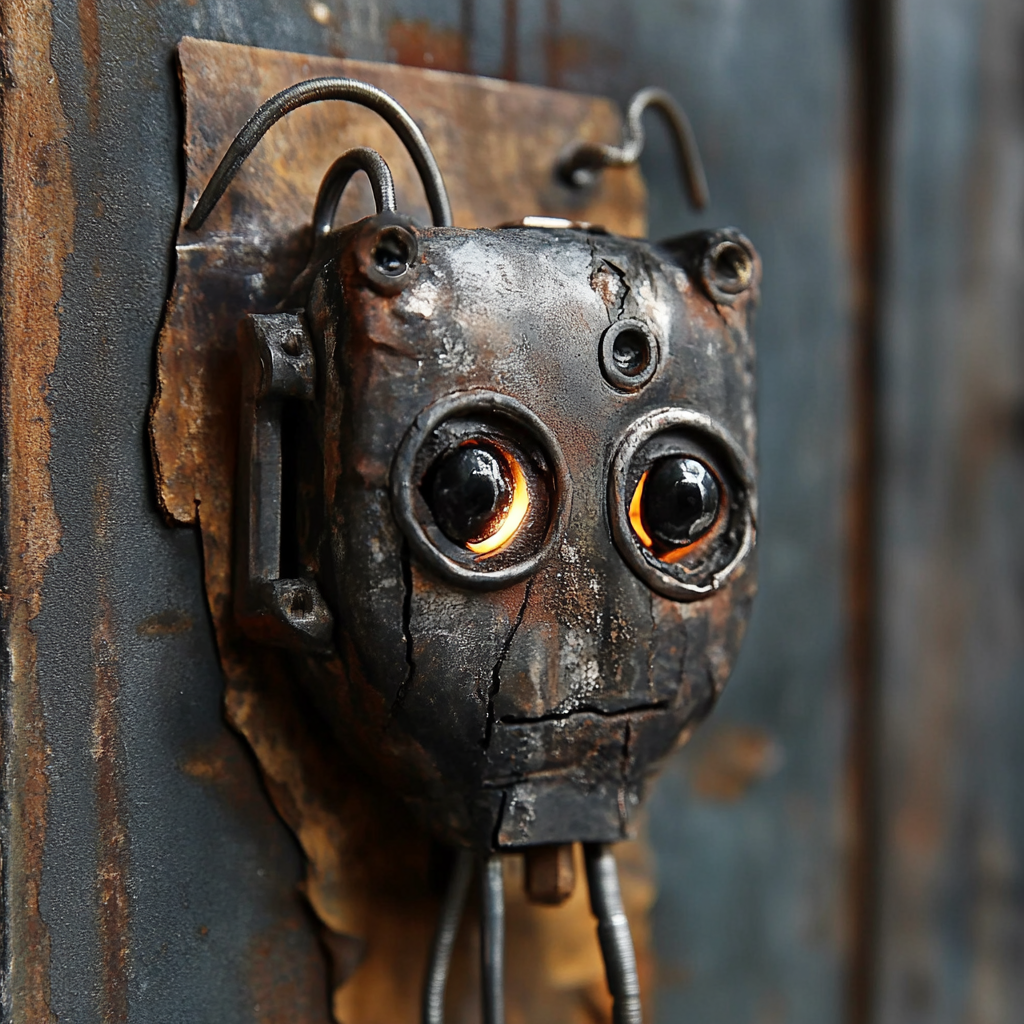
2. MIG Welding Machines: Versatile and Beginner-Friendly
MIG (Metal Inert Gas) welding machines are among the most popular and widely used welding tools, valued for their versatility, ease of use, and efficiency. Whether you’re a novice welder or a seasoned professional, a MIG welder is often the first choice for tackling a broad range of projects, from small repairs to large-scale fabrications.
What Makes MIG Welding Machines Unique?
MIG welding machines simplify the welding process by automating the feeding of a continuous wire electrode through the welding gun into the weld pool. A shielding gas, typically argon, CO₂, or a mix of the two, protects the weld from atmospheric contamination, ensuring clean, high-quality results.
Key features that set MIG welders apart include:
- Ease of Use: Designed to be user-friendly, making them ideal for beginners.
- Speed: MIG welding is faster than many other welding processes, boosting productivity.
- Versatility: Suitable for welding a wide variety of metals, including aluminum, stainless steel, and mild steel.
- Clean Welds: Produces minimal spatter and requires less cleanup compared to stick welding.
Advantages of MIG Welding Machines
- Beginner-Friendly
- MIG welders are relatively easy to learn, requiring less skill and precision than TIG or stick welding.
- They offer a smooth learning curve, allowing new welders to achieve professional results with minimal training.
- Fast and Efficient
- The continuous wire feed ensures a consistent arc and minimizes downtime.
- MIG welding is especially efficient for long seams and repetitive welding tasks, saving time and effort.
- Versatility in Materials
- Can weld various metals and alloys, including aluminum, mild steel, stainless steel, and even some non-ferrous materials.
- Suitable for thin sheet metal as well as thicker materials, depending on the machine’s settings.
- Minimal Cleanup
- Produces less spatter than stick welding, resulting in cleaner welds that require little post-weld cleanup.
Applications of MIG Welding Machines
MIG welders are widely used across industries and projects of all sizes. Some of their most common applications include:
- Automotive Repairs: Ideal for welding car panels, exhaust systems, and other components that require precision and speed.
- Metal Fabrication: Used in creating and repairing metal structures, furniture, and decorative items.
- General Home Projects: Perfect for DIY tasks like fixing gates, fences, or making custom metalwork.
- Industrial Applications: Frequently employed in manufacturing, construction, and shipbuilding for medium-duty tasks.
Features to Look for in a MIG Welding Machine
When choosing a MIG welding machine, consider the following features to ensure it meets your project requirements:
- Adjustable Settings: Look for machines with adjustable voltage and wire feed speed to handle different materials and thicknesses.
- Dual Voltage Capability: Some models can switch between 110V and 220V, providing flexibility for home and industrial use.
- Spool Gun Compatibility: For welding aluminum, a spool gun attachment ensures smoother wire feeding and better results.
- Built-In Gas Regulators: Simplifies the use of shielding gas by providing precise flow control.
- Portability: Lightweight models with carrying handles or wheels are easier to transport between workspaces.
Shielding Gas for MIG Welders
Shielding gas is a critical component of MIG welding, protecting the weld pool from oxidation and ensuring a strong, clean bond. The type of gas used depends on the material and desired weld characteristics:
- Pure Argon: Best for welding aluminum and non-ferrous metals.
- CO₂: Cost-effective and commonly used for mild steel, though it may produce more spatter.
- Argon-CO₂ Mix: A popular choice for balancing arc stability, penetration, and weld quality.
Limitations of MIG Welding Machines
While MIG welders offer many advantages, they also have some limitations to consider:
- Not Ideal for Outdoor Use: Shielding gas can be disrupted by wind, making MIG welding less effective in outdoor settings without proper wind protection.
- Higher Equipment Costs: The need for shielding gas, wire, and additional accessories increases the initial investment compared to stick welding.
- Limited for Thick Metals: Although versatile, MIG welders may struggle with very thick materials unless paired with a powerful machine.
Modern Innovations in MIG Welding Machines
Advanced MIG welders now include features that enhance performance and usability:
- Synergic Controls: Automatically adjust settings based on the material and thickness, simplifying operation for beginners.
- Multi-Process Capability: Some MIG welders also offer TIG or stick welding functionality, providing versatility in one machine.
- Digital Displays: Allow precise adjustments and real-time monitoring of parameters.
- Spool Gun Integration: Ensures smooth feeding of softer wires like aluminum for consistent welds.
MIG welding machines are a versatile and efficient choice for welders of all experience levels. Their ease of use, speed, and ability to handle a variety of metals make them a staple in workshops, construction sites, and home garages. Whether you’re repairing a car, fabricating metal structures, or tackling DIY projects, a MIG welder is a reliable tool that delivers professional-quality results with minimal effort. By choosing a machine with the right features for your needs, you can enjoy the many benefits of MIG welding and achieve exceptional results in your work.
3. TIG Welding Machines: Precision Tools for High-Quality Welds
TIG (Tungsten Inert Gas) welding machines, also known as Gas Tungsten Arc Welding (GTAW) machines, are the pinnacle of welding technology for producing clean, precise, and aesthetically superior welds. Designed for tasks that require meticulous attention to detail, TIG welders are ideal for joining delicate or exotic materials where precision is paramount.
What Makes TIG Welding Machines Unique?
TIG welders stand out because of their ability to provide exceptional control over the welding process. Unlike other welding methods, TIG welding uses a non-consumable tungsten electrode to create the arc. This allows the operator to focus entirely on the weld pool and filler material (if required) for maximum accuracy. Shielding gas, typically argon or helium, is used to protect the weld pool from oxidation and contamination.
Key characteristics include:
- Precise Heat Control: Enables welding of thin or intricate materials without distortion.
- Clean Welds: Produces smooth, spatter-free results that require minimal post-weld cleanup.
- Versatility in Materials: Can weld a wide range of metals, including aluminum, copper, titanium, stainless steel, and nickel alloys.
Advantages of TIG Welding Machines
- Unmatched Weld Quality
- TIG welds are aesthetically superior, producing smooth, clean seams that meet high standards for both strength and appearance.
- These welds are free from defects such as spatter, porosity, or cracking, making them ideal for structural and artistic applications.
- Exceptional Control
- TIG welders allow operators to precisely control heat input, arc stability, and filler deposition, providing maximum accuracy for detailed projects.
- Foot pedals or fingertip controls enable real-time adjustments, ensuring optimal performance during the welding process.
- Versatility in Applications
- Suitable for welding a variety of materials, including thin sheets, delicate components, and exotic metals that are challenging for other methods.
- Can perform autogenous welds (without filler material) on certain projects for seamless joints.
- Cleaner Work Environment
- TIG welding generates minimal fumes and sparks, making it a cleaner and safer option for indoor work environments.
Applications of TIG Welding Machines
TIG welding machines are widely used in industries that demand precision and quality. Common applications include:
- Aerospace: Welding components such as turbine blades, fuel tanks, and airframes that require exceptional strength and accuracy.
- Automotive: Ideal for custom fabrication, repairing exhaust systems, and welding thin or intricate car parts.
- Artistic and Ornamental Work: Frequently used for creating sculptures, jewelry, and decorative metal pieces due to the clean, seamless finishes.
- Medical Equipment: Essential for welding stainless steel and other materials used in surgical tools and medical devices.
- Pipe Welding: Commonly used in industries like chemical processing and food production for welding thin-walled piping systems.
Features to Look for in a TIG Welding Machine
Choosing the right TIG welder ensures you can handle a variety of projects with ease. Consider the following features:
- AC/DC Compatibility
- AC is necessary for welding aluminum and magnesium, while DC is used for harder metals like steel. A machine with both capabilities provides maximum flexibility.
- Pulse Welding Options
- Pulse welding allows for better heat control, reducing distortion and improving weld quality, particularly on thin materials.
- High-Frequency Start
- Ensures easy arc ignition without contaminating the tungsten electrode, making it ideal for precision work.
- Foot Pedal or Finger Controls
- Enables real-time adjustments to amperage, giving the operator full control over heat input and arc stability.
- Water Cooling Systems
- For extended welding sessions or high-amperage tasks, water-cooled torches prevent overheating and extend the life of the equipment.
Shielding Gas for TIG Welding
The choice of shielding gas is crucial to achieving clean and defect-free welds. Common options include:
- Argon: The most widely used shielding gas, providing excellent arc stability and weld quality across a variety of materials.
- Helium: Enhances heat input, making it ideal for welding thicker materials or improving weld penetration.
- Argon-Helium Mix: Offers a balance between arc stability and heat for challenging applications.
Limitations of TIG Welding Machines
While TIG welding machines offer unparalleled precision, they also come with certain limitations:
- Skill Requirement: TIG welding demands a high level of expertise, as it requires the operator to coordinate the torch, filler material, and controls simultaneously.
- Slower Speed: TIG welding is time-intensive compared to other methods like MIG or stick welding, making it less suitable for high-volume production.
- Higher Costs: TIG welders, along with the necessary shielding gas and filler rods, tend to be more expensive than other welding systems.
Modern Innovations in TIG Welding Machines
Modern TIG welders incorporate advanced technology to enhance performance and usability:
- Digital Displays: Provide precise control over settings and parameters, allowing for easy adjustments and repeatable results.
- Multi-Process Capability: Some TIG machines now include MIG or stick welding functions, offering greater versatility in a single unit.
- Lightweight and Portable Designs: Compact TIG welders are available for on-site work or tight spaces without compromising performance.
TIG welding machines are the go-to choice for welders who prioritize precision, cleanliness, and superior quality. While they require a higher skill level and more time than other welding methods, their ability to produce flawless results makes them indispensable in industries such as aerospace, automotive, and artistic metalworking. Whether you’re crafting intricate designs or repairing delicate components, a TIG welding machine offers unmatched control and craftsmanship to achieve the best possible results.
4. Stick Welding Machines
Stick welding machines, also known as Shielded Metal Arc Welding (SMAW) machines, are a cornerstone of welding technology, prized for their durability, simplicity, and versatility. These machines excel in outdoor and industrial settings, making them a favorite for heavy-duty projects and environments where other welding methods might falter.
What Makes Stick Welding Machines Unique?
Stick welding uses a consumable electrode (or “stick”) coated in flux. When the electrode melts, the flux coating burns to create a shielding gas and slag layer that protect the weld pool from atmospheric contamination. This self-contained process eliminates the need for external shielding gas, making stick welding highly portable and cost-effective.
Key characteristics of stick welding machines include:
- Robust Design: Built to withstand tough working conditions, including wind, rain, and uneven surfaces.
- Simplicity: Easy to set up and operate, making it a reliable option for both professionals and beginners.
- Wide Material Compatibility: Suitable for welding a variety of metals, including steel, cast iron, and stainless steel.
Advantages of Stick Welding Machines
- Weather Resistance
- Unlike other methods, stick welding performs well in adverse weather conditions, such as wind or rain, where shielding gases might be disrupted.
- This makes it ideal for outdoor projects like pipeline construction and structural repairs.
- Cost-Effective
- Stick welding does not require external shielding gas or complex equipment, reducing setup and operational costs.
- Electrodes are relatively inexpensive and available in a variety of sizes and types to suit different projects.
- Versatility
- Stick welders can handle a wide range of materials and thicknesses, from thin sheet metal to thick steel plates.
- They are compatible with different electrode types, allowing for various weld characteristics and applications.
- Portability
- Stick welding machines are compact and lightweight, making them easy to transport to remote job sites.
- Their independence from external shielding gas adds to their portability and convenience.
Applications of Stick Welding Machines
Stick welding is widely used in industries and projects that demand durability and flexibility. Common applications include:
- Construction: Welding structural steel beams, reinforcements, and heavy-duty equipment.
- Pipeline Welding: Ideal for joining pipes in oil, gas, and water distribution systems.
- Maintenance and Repairs: Frequently used for repairing farm equipment, machinery, and metal structures.
- Industrial Work: Suitable for fabrication and assembly in manufacturing plants.
- Shipbuilding: Used for welding ship hulls and other components exposed to harsh marine environments.
Features to Look for in a Stick Welding Machine
When selecting a stick welding machine, consider the following features to ensure it meets your needs:
- Amperage Range
- Machines with a wide amperage range can handle both thin and thick materials, providing greater versatility.
- Duty Cycle
- Choose a machine with a duty cycle that matches your workload. A higher duty cycle is essential for extended welding sessions.
- Portability
- Look for lightweight models with carrying handles for ease of transport, especially if you’ll be working in multiple locations.
- Multi-Process Capability
- Some stick welders also support TIG or MIG welding, adding flexibility for different types of projects.
- Advanced Features
- Hot Start: Provides a surge of current at the start of the weld to prevent sticking.
- Anti-Stick Technology: Automatically reduces amperage if the electrode sticks to the workpiece, making it easier to detach.
- Arc Force Control: Allows fine-tuning of the arc to improve performance on different materials and positions.
Electrode Selection for Stick Welding
The choice of electrode plays a critical role in the quality and characteristics of the weld. Common electrode types include:
- 6010: Provides deep penetration, making it ideal for root passes in pipe welding.
- 6013: Produces smooth welds with moderate penetration, suitable for thin materials.
- 7018: Delivers high-strength welds with a smooth finish, often used in structural welding.
Each electrode type has specific applications and amperage requirements, so selecting the right one is essential for achieving optimal results.
Limitations of Stick Welding Machines
While stick welding machines are versatile and robust, they do have some limitations:
- Less Aesthetic Welds: Stick welds may require more cleanup due to slag and spatter compared to TIG or MIG welding.
- Slower Process: Stick welding is generally slower than MIG or flux-cored welding, especially for long welds.
- Skill Requirement: While relatively straightforward, stick welding requires practice to master electrode control and arc stability.
Modern Innovations in Stick Welding Machines
Advancements in stick welding technology have enhanced usability and performance:
- Inverter-Based Stick Welders: Compact and energy-efficient, these machines offer precise control and are easier to transport.
- Digital Interfaces: Provide real-time monitoring and fine-tuning of welding parameters.
- Multi-Voltage Options: Machines that can operate on 110V or 220V provide flexibility for home and industrial use.
Stick welding machines are a reliable and cost-effective choice for heavy-duty welding tasks in challenging environments. Their simplicity, durability, and adaptability make them a staple in construction, maintenance, and industrial applications. Whether you’re welding pipelines in adverse weather or repairing machinery on a farm, stick welders deliver the strength and versatility needed to get the job done. With the right machine, electrodes, and technique, stick welding remains one of the most robust and dependable welding methods available.
5. Multi-Purpose Welding Machines: Versatility and Cost-Effectiveness
Multi-purpose welding machines are game-changers in the welding industry, offering the ability to perform multiple welding processes with a single unit. Designed to save time, space, and money, these machines are ideal for welders who need versatility across a variety of projects without the hassle of switching between different machines.
What Are Multi-Purpose Welding Machines?
Multi-purpose welding machines combine several welding processes, such as MIG, TIG, stick, and flux-cored welding, into one compact and portable unit. This flexibility allows operators to handle a wide range of welding tasks, making these machines a practical choice for small workshops, construction sites, and even DIY enthusiasts.
Key features include:
- Versatility: Switch between welding methods seamlessly to suit different materials and applications.
- Cost-Efficiency: Eliminates the need to purchase multiple machines for different processes.
- Compact Design: Lightweight and portable, making them easy to move and store.
Advantages of Multi-Purpose Welding Machines
- Adaptability
- Multi-purpose machines can handle a variety of tasks, from delicate TIG welds on thin materials to heavy-duty stick welding for thick steel.
- This versatility makes them suitable for projects in automotive repair, construction, manufacturing, and home workshops.
- Space-Saving Design
- A single machine capable of multiple welding processes reduces clutter in your workspace.
- Perfect for small workshops or job sites where space is limited.
- Cost-Effective
- Investing in a multi-purpose welder is often more affordable than buying separate machines for MIG, TIG, and stick welding.
- Lower maintenance costs, as only one machine requires upkeep.
- Convenience
- Switching between welding processes is simple and efficient, saving time during multi-step projects.
- Many models come with user-friendly interfaces, making them accessible for both professionals and beginners.
Applications of Multi-Purpose Welding Machines
Multi-purpose welding machines are widely used in various industries and settings due to their versatility:
- Automotive Repairs: Ideal for welding car panels, exhaust systems, and structural components.
- Construction: Suitable for structural welding, pipe welding, and on-site repairs.
- Manufacturing: Commonly used for fabricating metal products and prototypes in factories.
- Home Workshops: Perfect for DIY enthusiasts tackling a range of projects, from metal furniture to machinery repair.
Features to Look for in a Multi-Purpose Welding Machine
When selecting a multi-purpose welder, consider the following features to ensure it meets your needs:
- Supported Welding Processes
- Ensure the machine includes the processes you need, such as MIG, TIG, stick, and flux-cored welding.
- Some advanced models also support plasma cutting, adding even more functionality.
- Amperage Range
- A wide amperage range allows for greater flexibility, enabling the machine to handle thin materials and heavy-duty tasks.
- Voltage Compatibility
- Dual-voltage machines (110V/220V) provide the flexibility to work in various environments, from home workshops to industrial sites.
- Digital Controls
- Digital interfaces simplify the setup process and allow for precise adjustments to welding parameters.
- Portability
- Look for lightweight models with carrying handles or wheels for easy transport between job sites.
- Duty Cycle
- A higher duty cycle ensures the machine can handle extended welding sessions without overheating.
Limitations of Multi-Purpose Welding Machines
While multi-purpose welders offer many advantages, they do have some limitations:
- Complexity: The versatility of these machines may come with a steeper learning curve for beginners.
- Cost: While cost-effective compared to buying multiple machines, multi-purpose welders can be more expensive upfront than single-process machines.
- Performance Trade-Offs: Some models may not perform as well as dedicated machines for specific welding processes.
Modern Innovations in Multi-Purpose Welding Machines
Advancements in welding technology have made multi-purpose machines more efficient and user-friendly:
- Inverter Technology: Modern multi-purpose welders use inverter technology, making them lighter, more energy-efficient, and capable of precise adjustments.
- Synergic Settings: Automatically adjust parameters like voltage and wire feed speed based on the material and thickness, simplifying operation.
- Advanced Cooling Systems: Prevent overheating during prolonged use, increasing the machine’s lifespan.
Comparison of Common Multi-Purpose Models
Model | Processes Supported | Voltage | Key Features |
---|---|---|---|
Everlast PowerMTS | MIG, TIG, Stick, Flux-Cored | 110V/220V | Digital display, pulse TIG, dual voltage |
Lincoln Electric MP | MIG, TIG, Stick | 120V/230V | Lightweight, intuitive controls |
Forney Easy Weld | MIG, Stick, Flux-Cored | 120V | Beginner-friendly, portable |
Multi-purpose welding machines are an excellent investment for anyone who needs flexibility and efficiency in their welding projects. By combining multiple welding processes into one unit, these machines save space, reduce costs, and streamline operations. Whether you’re a professional welder tackling diverse industrial tasks or a DIY enthusiast working on various home projects, a multi-purpose welding machine offers the versatility and performance you need to get the job done.
6. Spot Welding Machines: Precision Tools for Sheet Metal Assembly
Spot welding machines are specialized devices designed to join sheet metal by applying heat and pressure at precise points. Known for their efficiency and reliability, these machines are indispensable in industries where speed, precision, and strength are paramount. Spot welding’s unique approach to joining materials makes it a staple in automotive manufacturing, industrial production, and various applications requiring clean, strong welds.
What Are Spot Welding Machines?
Spot welding machines focus heat and pressure on a small, localized area using two copper electrodes. The heat generated by electrical resistance between the electrodes melts the material, and pressure is applied to fuse the sheets together. This process eliminates the need for filler material, making spot welding efficient, cost-effective, and clean.
Key characteristics include localized heat that minimizes distortion to surrounding areas, no filler material needed which simplifies the process and reduces material costs, and repetitive precision perfect for tasks that require consistent, repetitive welds, such as in mass production.
Advantages of Spot Welding Machines
High efficiency as spot welding is a fast process, capable of producing multiple welds in seconds, making it ideal for high-volume production environments. Cost-effective as it eliminates the need for filler material, reducing overall costs, and has low energy consumption compared to other welding methods. Creates strong welds that withstand significant mechanical stress, ideal for load-bearing assemblies.
Produces clean and neat welds with minimal spatter or residue, requiring little to no post-weld cleanup, and leaves a small, uniform weld mark, maintaining the aesthetics of the workpiece. Environmentally friendly with fewer emissions compared to other welding processes, making it a greener choice for manufacturers.
Applications of Spot Welding Machines
Spot welding is widely used in industries that require fast, reliable, and consistent welds. Common applications include the automotive industry for welding body panels, brackets, and frames, ensuring structural integrity in vehicles while maintaining a sleek finish. Manufacturing is used in the production of household appliances, industrial equipment, and furniture, such as washing machines, refrigerators, and filing cabinets.
Electronics use spot welding to join thin metal components in batteries, circuit boards, and other electronic devices. Aerospace applies it in the assembly of lightweight aluminum or titanium components to ensure strong, reliable bonds. Construction uses it for welding thin sheet metal in architectural applications, including HVAC systems and ductwork.
Features to Look for in a Spot Welding Machine
Electrode design is important, and machines with adjustable electrode tips can accommodate different material thicknesses. Control options in advanced models offer programmable settings for controlling heat, pressure, and weld duration, ensuring precision and consistency. Power capacity ensures the machine has sufficient power to handle the materials you plan to weld, from thin sheets to thicker panels. Portability is ideal for smaller, lightweight models suitable for on-site repairs, while larger machines are better for production lines. Cooling systems, such as integrated water-cooling, prevent overheating during prolonged use, improving efficiency and extending machine life.
Types of Spot Welding Machines
Manual spot welders are operated by hand and are ideal for small-scale projects and repairs, often used in workshops and by hobbyists. Pneumatic spot welders use pneumatic pressure to automate the welding process, ensuring consistent force and weld quality, commonly found in manufacturing facilities. Portable spot welders are lightweight and compact, designed for on-site welding and repairs. Robotic spot welders are integrated into automated production lines and provide unmatched precision and speed for large-scale manufacturing.
Limitations of Spot Welding Machines
Material thickness is a limitation as spot welding is primarily suited for thin sheets of metal, and welding thicker materials may require additional equipment or alternative methods. It is limited to overlapping joints as spot welding works best for lap joints where one piece overlaps the other, making it not ideal for other joint configurations. High initial cost as advanced spot welding machines, especially robotic models, can be expensive, though the investment is offset by efficiency and durability.
Modern Innovations in Spot Welding Machines
Advancements in spot welding technology have enhanced efficiency and broadened applications. Programmable Logic Controllers (PLCs) allow operators to set precise welding parameters, ensuring consistent quality across multiple welds. Servo-controlled spot welders provide accurate control of pressure and heat for intricate welding tasks. Advanced cooling systems, such as water-cooled electrodes and systems, reduce downtime caused by overheating.
Spot welding machines are an essential tool for industries that rely on fast, efficient, and precise welding of sheet metal. Their ability to produce strong, clean welds without filler material makes them a cost-effective choice for automotive, manufacturing, and electronics applications. Whether you need a compact portable unit for repairs or a robotic welder for mass production, spot welding machines offer unparalleled efficiency and reliability for repetitive tasks. With the right machine and setup, spot welding delivers exceptional results in any application requiring precision and speed.
7. Plastic Welding Machines
Plastic Welding Machines: Specialized Tools for Plastic Fabrication
Plastic welding machines are uniquely designed to join and repair plastic materials. Unlike traditional metal welding, plastic welding involves processes tailored to the unique properties of plastics, using heat, pressure, or ultrasonic vibrations to create strong, seamless bonds. These machines are essential for industries where plastic materials play a critical role, such as automotive, packaging, and construction.
What Are Plastic Welding Machines?
Plastic welding machines utilize various techniques to fuse plastic parts by melting the base material and sometimes adding filler material. These processes are precise, efficient, and versatile, enabling seamless repairs and the fabrication of custom plastic components. The primary methods include hot air welding which uses a jet of hot air to soften the plastic surfaces for bonding, extrusion welding which combines heated plastic filler material with the softened base material to create strong welds for larger components, and ultrasonic welding which applies high-frequency vibrations to melt and bond plastics at the molecular level without requiring external heat.
Advantages of Plastic Welding Machines
Plastic welding machines offer versatility as they can weld various types of plastics, including PVC, polyethylene, polypropylene, and acrylics. They are suitable for a wide range of tasks, from repairing plastic tanks to fabricating complex components. They provide precision and seamless results by producing clean, uniform welds that often require no additional finishing. They offer precise control over heat and pressure for delicate or intricate applications.
They are environmentally friendly as they allow for the repair of damaged plastic parts, reducing waste and the need for new materials, and use less energy compared to traditional metal welding. They are cost-effective by reducing the need for adhesives or mechanical fasteners, lowering material costs, and durable welds minimize the need for frequent replacements or repairs.
Applications of Plastic Welding Machines
Plastic welding machines are indispensable in industries that rely heavily on plastic materials. Common applications include the automotive industry for repairing plastic bumpers, dashboards, and fuel tanks and fabricating lightweight, durable components for vehicles. The packaging industry creates airtight seals for plastic packaging, containers, and films, and produces custom designs for branding and product protection.
The construction and infrastructure industry joins plastic pipes and fittings for water, gas, and chemical distribution systems, and repairs or fabricates large plastic tanks, liners, and roofing membranes. The medical industry fabricates medical devices and equipment from biocompatible plastics and ensures seamless, hygienic bonds for sterile environments. Consumer goods involve repairing household items like plastic furniture, appliances, and toys and crafting custom parts for DIY projects and hobbyists.
Features to Look for in a Plastic Welding Machine
Consider the welding method and determine the appropriate method based on your application, such as hot air, extrusion, or ultrasonic welding. Some machines combine multiple techniques for added versatility. Temperature control is essential, and machines with precise temperature settings can handle different types of plastics without overheating or distortion.
Portability is important, and lightweight, compact models are ideal for on-site repairs or mobile work environments. Power and speed matter, as machines with higher power output and faster operation are suitable for industrial applications requiring quick turnaround times. Attachments and nozzles are important, and ensuring compatibility with a variety of nozzles and attachments is necessary for different welding tasks.
Types of Plastic Welding Machines
Hot air welders use a stream of hot air to soften and bond plastic materials and are ideal for small to medium-sized repairs and fabrication. Extrusion welders combine heated filler material with the base material for strong, durable welds and are suitable for large-scale or industrial projects like tank repairs. Ultrasonic welders use high-frequency vibrations to create precise, clean bonds without external heat and are commonly used in electronics, medical devices, and high-precision applications. Infrared welders employ infrared radiation to melt plastic surfaces for a contact-free bonding process and are useful for sensitive applications where contamination must be avoided.
Limitations of Plastic Welding Machines
While plastic welding machines are highly versatile and efficient, they have certain limitations. Material compatibility can be an issue as not all plastics are weldable, and some may burn or degrade under heat. Always confirm the plastic type before welding. Achieving strong, clean welds requires training and practice, especially for intricate tasks. Equipment cost can be high, especially for advanced machines like ultrasonic or infrared welders, though they provide unmatched precision and reliability.
Modern Innovations in Plastic Welding Machines
Advancements in plastic welding technology have expanded their capabilities and improved user experience. Automated systems like robotic plastic welders ensure consistent, high-quality welds for large-scale manufacturing. Digital interfaces offer precise control over temperature, pressure, and timing for repeatable results. Eco-friendly designs incorporate energy-saving features and recyclable components to reduce environmental impact.
Plastic welding machines are essential tools for industries and applications that rely on strong, seamless bonds in plastic materials. Their versatility, precision, and cost-effectiveness make them invaluable for automotive, packaging, construction, and medical applications, among others. Whether you’re repairing a plastic tank, fabricating custom parts, or creating airtight seals, a plastic welding machine provides the technology and functionality needed to achieve professional-grade results. By choosing the right machine and mastering its operation, you can tackle any plastic welding project with confidence and efficiency.
Evolution of Welding Machines: From Blacksmithing to Modern Technology
Welding technology has evolved dramatically over the centuries, transforming from simple manual processes into advanced, precision-driven techniques that cater to the demands of modern industries. The journey from blacksmiths hammering heated metals together to today’s sophisticated welding machines highlights the continuous innovation that has shaped the welding industry.
The Origins of Welding
Welding dates back thousands of years to when blacksmiths used basic tools to heat and hammer metals into shapes and bonds. This early form of welding relied entirely on manual labor and high-temperature heat sources, such as forge fires. While effective for its time, this process was labor-intensive and lacked precision, making it unsuitable for complex or large-scale applications.
The Industrial Revolution: Advancing Welding Techniques
The industrial revolution in the 18th and 19th centuries brought significant advancements in welding. The development of oxyfuel welding introduced the use of a controlled flame to melt and join metals. This method marked the transition from manual heating to more precise and efficient processes, enabling faster production in industries like construction, railroads, and shipbuilding.
Oxyfuel welding combined a mixture of oxygen and fuel gases, such as acetylene, to create a high-temperature flame. Arc welding, invented in the late 1800s, used an electric current to create an arc between an electrode and the workpiece, generating intense heat for melting metals.
The 20th Century: The Rise of Specialized Welding Machines
The 20th century saw the emergence of specialized welding machines tailored for specific applications. Advancements during this period included shielded metal arc welding (stick welding) introduced in the early 1900s, using a flux-coated electrode to shield the weld pool from contamination. MIG welding, developed in the 1940s, enabled faster welding with a continuous wire electrode and shielding gas, revolutionizing automotive and industrial manufacturing.
TIG welding, also developed in the 1940s, provided greater precision and control, ideal for welding thin materials and exotic metals like aluminum and magnesium. Spot welding was developed for high-speed production, particularly in the automotive and electronics industries.
Modern Innovations in Welding Machines
In recent decades, welding technology has continued to evolve with the integration of advanced materials, digital systems, and innovative processes. Modern welding machines offer unparalleled precision, efficiency, and versatility, enabling welders to tackle increasingly complex projects.
Inverter technology introduced lightweight, energy-efficient welding machines with precise digital controls. Multi-purpose welders combined multiple welding processes, such as MIG, TIG, and stick welding, into a single unit for greater versatility. Robotic welding systems are used in automated production lines for consistent, high-quality welds at scale. Advanced cooling systems improved durability and efficiency for extended welding sessions.
The Role of Welding in Modern Industries
Today, welding machines are indispensable tools in industries such as aerospace, automotive, construction, shipbuilding, and manufacturing. The ability to weld diverse materials with precision and speed has expanded the scope of what can be created, repaired, or fabricated. From delicate medical devices to large-scale infrastructure projects, welding technology continues to shape the world we live in.
Choosing the Right Welding Machine
Selecting the right welding machine is crucial for achieving optimal results in your projects. The choice depends on various factors, including the type of materials you’ll work with, your skill level, and the specific applications you need to address.
Factors to Consider
Project requirements involve determining the type of welding best suited for your projects. For example, MIG welding is ideal for fast, efficient tasks, while TIG welding is better for precision work. Material type is important to consider since metals like aluminum and stainless steel may require specialized machines like TIG welders, while thicker steel plates might benefit from stick welding.
Skill level matters as beginners may prefer MIG or multi-purpose welders for their ease of use, while professionals might opt for advanced TIG machines or robotic systems. Portability is necessary for lightweight and portable models if you need to work on-site or in tight spaces. Budget and cost efficiency are essential as inverter-based and multi-purpose machines often provide excellent value due to their versatility and energy efficiency.
Matching Welding Machines to Applications
MIG welding is ideal for automotive repairs, general fabrication, and light to medium-duty tasks. TIG welding is best for precision work on thin materials or exotic metals, such as aluminum and magnesium. Stick welding is suitable for outdoor and heavy-duty applications, such as pipeline and structural welding. Spot welding is perfect for joining thin sheet metal in high-volume production settings. Multi-purpose machines provide flexibility for workshops or professionals handling diverse projects.
The Future of Welding Machines
As technology advances, welding machines are becoming more intelligent, efficient, and adaptable. Innovations such as artificial intelligence, machine learning, and enhanced automation are likely to redefine welding processes, enabling even greater precision and efficiency. Sustainable practices, such as energy-efficient designs and reduced emissions, will also play a critical role in the evolution of welding technology.
Conclusion
The evolution of welding machines showcases the industry’s ability to adapt and innovate to meet the demands of an ever-changing world. From traditional blacksmithing methods to today’s advanced digital systems, welding has become an integral part of modern manufacturing and construction. Choosing the right welding machine for your needs ensures you can tackle any project with confidence, precision, and efficiency. By understanding the history, capabilities, and applications of welding machines, you can make informed decisions that lead to successful and professional-grade results.
Additional Resources
Get your welding gear here.
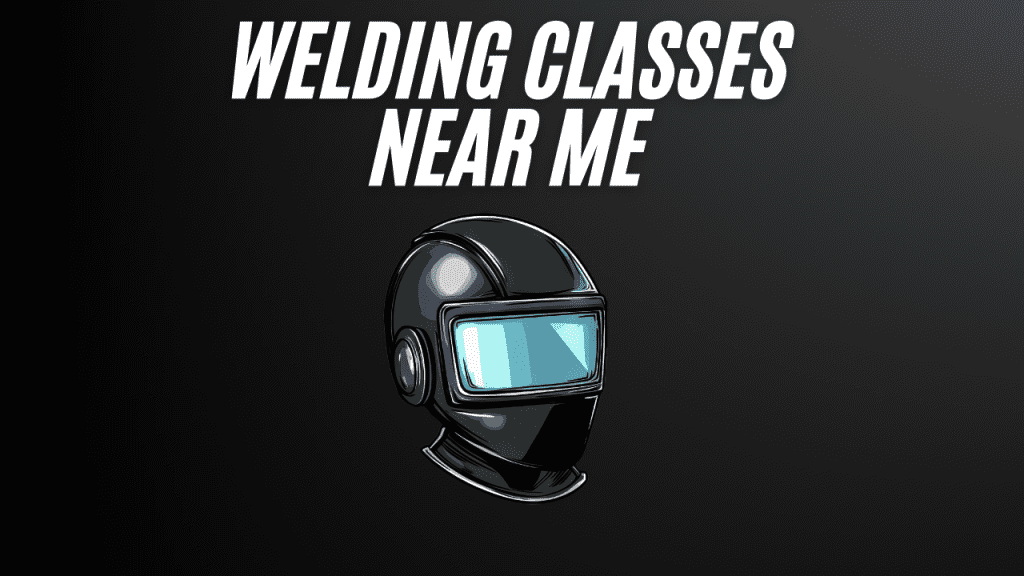