Table of Contents
The Role of the Arc and Argon Gas in Welding
Welding is a precise process that relies on two fundamental components: the arc and shielding gas. Together, they create the conditions necessary for forming strong, durable welds. Here’s a closer look at their roles and how they contribute to the welding process.
The Arc: Generating Heat for Welding
The welding arc is the core mechanism in most welding processes, providing the intense heat necessary to melt both the base metal and filler material. This heat forms a molten weld pool, allowing metals to fuse seamlessly. Understanding how the arc functions and its impact on the welding process is key to producing strong and high-quality welds.
Heat Generation
The welding arc is essentially a concentrated electrical discharge between the electrode and the workpiece. This electric arc produces temperatures that can exceed 5,000°F, high enough to melt most metals. The extreme heat facilitates:
- Metal Fusion: The base metal and filler material merge to create a solid joint upon cooling.
- Consistent Molten Pool: A stable arc ensures a uniform weld pool, critical for structural integrity and appearance.
- Adaptability: Welders can adjust the arc to accommodate various metals, joint designs, and thicknesses.
For applications requiring deep penetration, such as structural welding, the heat produced by the arc must be carefully controlled to achieve optimal results.
Precision Control
The arc’s intensity and stability directly impact the quality of the weld. Precise control of the arc allows welders to tailor the process to the specific requirements of a project. Key aspects include:
- Arc Length: A short arc provides better penetration and minimizes spatter, while a longer arc offers more flexibility but risks instability.
- Current and Voltage: Adjusting these parameters can fine-tune the arc for different materials and welding positions. For example, higher current increases penetration but may lead to overheating thin materials.
- Electrode Type: The composition and size of the electrode influence the arc’s behavior, with certain types offering better performance for specific applications.
Mastering arc control is particularly important in advanced techniques like TIG welding, where the welder must manually manage the arc’s position and intensity.
Transfer Modes
The arc also determines the transfer mode used in welding, which affects how the filler metal is deposited and the characteristics of the weld. Common transfer modes include:
- Spray Transfer:
- Produces a fine, stable spray of molten metal droplets.
- Offers smooth welds with deep penetration and minimal spatter.
- Requires higher current settings and argon-rich shielding gas.
- Ideal for thick materials and high-speed applications.
- Globular Transfer:
- Creates larger, less consistent droplets of molten metal.
- Can lead to more spatter and requires additional cleanup.
- Typically used with pure carbon dioxide shielding gas.
- Suitable for thicker materials but less efficient than spray transfer.
- Short Circuit Transfer:
- The electrode wire touches the weld pool, creating a short circuit and depositing the filler material.
- Provides excellent control for thin materials and out-of-position welding.
- Operates at lower heat, reducing the risk of burn-through.
By understanding and leveraging these transfer modes, welders can optimize the arc for different applications, from delicate automotive repairs to heavy-duty structural projects.
The Arc’s Role in Welding Efficiency
A well-maintained and stable arc not only enhances weld quality but also improves efficiency. A stable arc minimizes defects like porosity and spatter, reducing post-weld cleanup time and material wastage. Additionally, the ability to adjust arc parameters for specific needs ensures versatility, making the welding process adaptable to a wide range of industries and materials.
In conclusion, the arc is the powerhouse of welding, delivering the heat, precision, and versatility needed to create strong and reliable welds. Mastery of arc dynamics allows welders to produce professional-grade results across various applications, from intricate artistic designs to demanding industrial projects.
The Role of Argon Gas in Shielding
Shielding gas, with argon being a common choice, is indispensable in the welding process. Its primary function is to shield the molten weld pool and arc from atmospheric contaminants, such as oxygen, nitrogen, and hydrogen. These contaminants can react with the molten metal, leading to defects like porosity, weak bonds, and surface discoloration. Argon’s unique properties make it one of the most effective shielding gases, especially in processes like GTAW (TIG) and GMAW (MIG) welding.
How Argon Protects the Weld
- Prevention of Oxidation and Contamination: By creating an inert atmosphere around the weld, argon prevents oxidation and other chemical reactions with airborne gases. This ensures that the weld pool solidifies without impurities, resulting in a stronger and more reliable weld. Without proper shielding, contaminants can cause pinholes, cracks, and structural weaknesses, compromising the weld’s integrity.
- Consistent Coverage: Argon envelops the weld pool like a protective blanket, maintaining a controlled environment even during high-temperature welding. This consistency is particularly beneficial when working with metals prone to contamination, like aluminum and stainless steel.
Benefits of Argon in Welding
- Protection Against Contaminants:
- Argon acts as a barrier against atmospheric gases that can lead to weld defects. For example, oxygen can cause oxidation, while nitrogen and hydrogen can lead to porosity or embrittlement. Argon’s inert nature ensures that these unwanted reactions are kept at bay.
- Welders working without adequate shielding often face issues like discoloration and weak welds, which are costly to repair or redo.
- Arc Stability:
- Argon contributes to a stable and concentrated arc, which is critical for precision welding. A stable arc allows for consistent heat distribution, making it easier to control the weld pool and achieve uniform penetration.
- Stability is particularly important for processes like spray transfer, where a steady arc ensures the smooth deposition of molten metal.
- Temperature Tolerance:
- Argon’s non-flammable and non-toxic properties make it a safe and efficient choice for handling extreme welding temperatures. This capability is vital when welding materials like titanium or magnesium, which require high heat levels and a non-reactive atmosphere.
- Improved Weld Appearance:
- One of argon’s standout benefits is the quality of the weld’s appearance. By minimizing spatter and oxidation, argon helps produce smooth, clean welds with uniform bead profiles. This is particularly advantageous for projects where aesthetics are important, such as automotive bodywork or architectural metalwork.
- Versatility Across Metals:
- Argon is compatible with a wide range of metals, from aluminum and stainless steel to exotic alloys. Its adaptability makes it a preferred choice for many industries, including aerospace, automotive, and construction.
Argon Blends and Applications
While pure argon is commonly used in TIG welding and for aluminum in MIG welding, it is also blended with other gases to enhance specific welding properties:
- Argon-Carbon Dioxide Mix (C25): Often used for welding mild steel, this blend combines argon’s arc stability with CO₂’s deeper penetration capabilities.
- Argon-Helium Mix: For thick materials or high-speed welding, helium is added to argon to increase heat input and improve weld fluidity.
- Argon-Oxygen Mix: A small percentage of oxygen is added for improved wetting and bead shape in certain applications.
By selecting the right blend, welders can tailor the shielding gas to suit their specific material and process requirements.
The Importance of Proper Gas Flow
To maximize the benefits of argon, maintaining the correct gas flow rate is crucial. Too little flow can expose the weld pool to contaminants, while too much flow can cause turbulence, drawing in atmospheric gases. Monitoring and adjusting the flow rate ensures that the weld remains protected and the arc stable throughout the process.
Argon gas is more than just a shielding gas—it is a critical component in producing strong, clean, and visually appealing welds. Its inert nature, combined with its ability to stabilize the arc and protect against contaminants, makes it an invaluable asset in welding. Whether used pure or in blends, argon plays a pivotal role in achieving high-quality results, making it a staple in welding across various industries and applications.
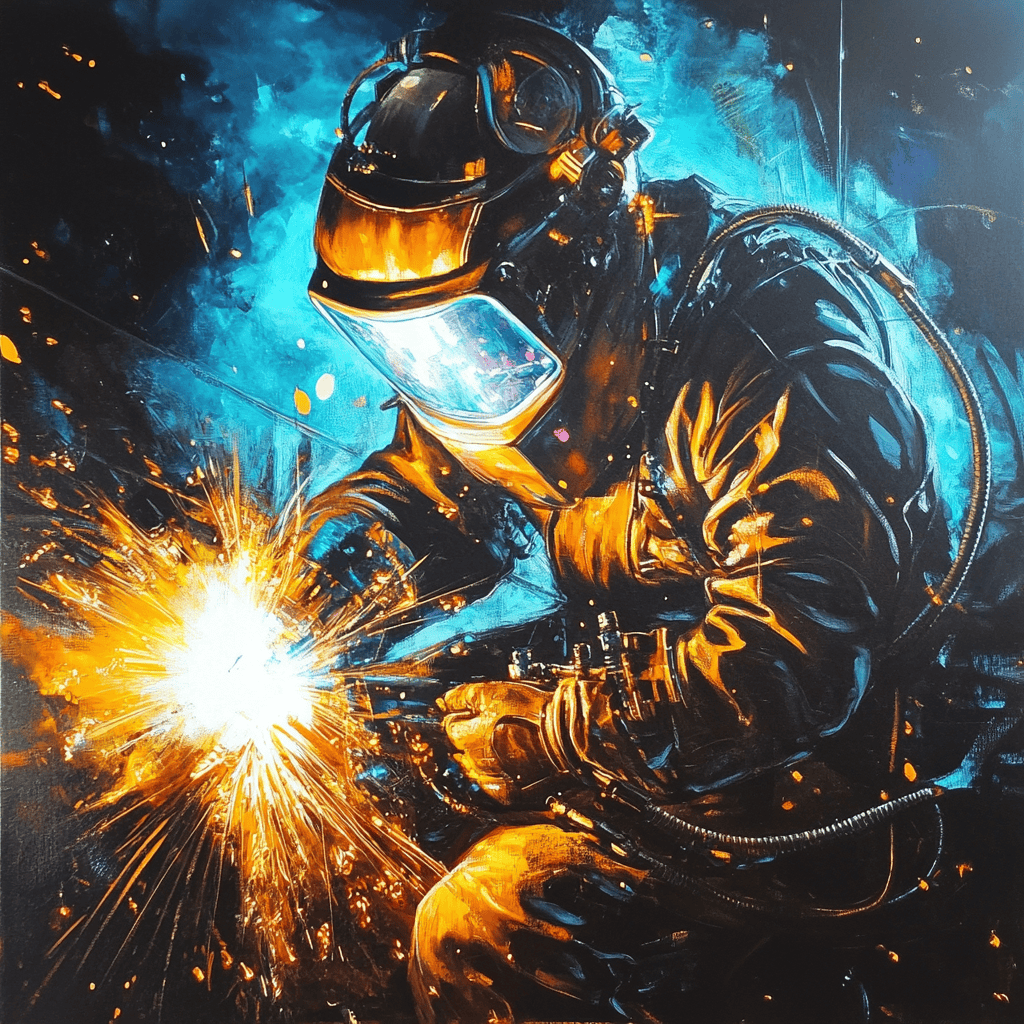
Shielding Gas in Welding Methods: GTAW vs GMAW
Shielding gas plays a vital role in both Gas Tungsten Arc Welding (GTAW) and Gas Metal Arc Welding (GMAW), protecting the weld pool and stabilizing the arc. While both methods use shielding gas, their processes, equipment, and gas requirements vary significantly based on the materials and applications involved.
GTAW (TIG Welding)
- Electrode Type:
GTAW relies on a non-consumable tungsten electrode to create the arc. The tungsten electrode does not melt during the process, allowing for precise control over the weld pool. This method is particularly valued for its ability to deliver high-quality, defect-free welds. - Argon Use:
Pure argon is the standard shielding gas for GTAW. Its inert nature prevents chemical reactions in the weld pool, ensuring clean and strong welds. Argon’s ability to stabilize the arc makes it ideal for precision work, particularly with non-ferrous metals. - Application:
GTAW is commonly used for thin metals and non-ferrous materials such as aluminum, magnesium, and titanium. It is a preferred choice in industries requiring intricate and high-quality welds, such as aerospace, automotive, and medical equipment manufacturing. - Advantages of Argon in GTAW:
Control and Precision: Argon facilitates a stable arc, enabling precise heat control for delicate materials.
Minimal Contamination: The inert properties of argon prevent weld defects like oxidation and porosity, which are crucial when working with reactive metals like titanium.
Versatility: Argon can be used across a variety of materials and thicknesses, making it a reliable choice for TIG welding.
GMAW (MIG Welding)
- Electrode Type:
GMAW uses a continuously fed wire electrode that serves as both the arc conductor and filler material. This consumable wire is fed automatically through the welding gun, enabling faster and more efficient welding compared to GTAW. - Argon Use:
In GMAW, argon is often blended with active gases like carbon dioxide (CO₂) or helium to enhance specific welding properties.
Argon-CO₂ Mixes: Commonly used for welding mild steel, offering a balance of arc stability, penetration, and reduced spatter.
Argon-Helium Mixes: Preferred for thicker materials or applications requiring increased heat input, such as aluminum welding. - Application:
GMAW is suitable for thicker metals and high-speed welding projects. It is widely used in construction, automotive manufacturing, and industrial fabrication, where efficiency and productivity are critical. - Advantages of Argon in GMAW:
Improved Arc Performance: Argon-rich mixes provide a stable arc, enhancing weld quality and consistency.
Versatility in Blends: By combining argon with other gases, welders can tailor the shielding environment to suit specific materials and project requirements.
High-Speed Capability: The automatic feeding of the electrode, combined with argon’s arc stability, enables faster welding speeds, making GMAW a time-efficient process.
Key Differences Between GTAW and GMAW Shielding Gas Use
- Gas Purity:
GTAW almost exclusively uses pure argon for its inert properties and ability to create clean, precision welds. GMAW often utilizes gas blends (e.g., argon-CO₂, argon-helium) to optimize penetration, spatter levels, and arc behavior. - Applications:
GTAW is ideal for precision work on thin or delicate materials. GMAW excels in high-speed, high-volume applications with thicker metals. - Cost Considerations:
GTAW’s reliance on pure argon can make it more expensive for larger projects. GMAW’s flexibility in using gas blends allows welders to balance cost and performance. - Complexity:
GTAW requires more skill and control, making it a slower but more precise process. GMAW, with its continuous wire feed and broader gas options, is more accessible for high-speed production.
By understanding the distinct roles of shielding gas in GTAW and GMAW, welders can choose the most suitable method and gas type for their specific projects. Whether prioritizing precision or productivity, shielding gas is a crucial element in achieving strong, clean, and reliable welds.
Active vs Inert Shielding Gases: A Closer Look
Shielding gases are essential in the welding process, protecting the weld pool from atmospheric contaminants while influencing weld quality and characteristics. These gases are categorized as active or inert, each serving distinct purposes based on the material being welded and the specific welding application.
Active Shielding Gases
Examples:
- Carbon dioxide (CO₂)
- Oxygen (O₂)
Characteristics:
Active gases chemically react with the molten weld pool, impacting the penetration, arc behavior, and overall weld characteristics. This chemical interaction can enhance certain properties of the weld but may also introduce challenges, such as increased spatter and oxidation.
- Deep Penetration: Active gases, particularly CO₂, promote deeper penetration, making them suitable for thicker materials.
- Cost-Effective: These gases are often less expensive, making them popular in industrial and heavy-duty welding applications.
- Increased Spatter: The chemical reactions involved can produce more spatter, requiring additional cleanup.
Applications:
Active gases are widely used for structural welding and heavy-duty applications, where penetration and strength are critical. For example:
- Carbon dioxide (CO₂): Commonly used for welding mild steel due to its affordability and ability to achieve deep weld penetration.
- Oxygen (O₂): Often added in small percentages to argon to stabilize the arc and improve bead wetting on stainless steel and other alloys.
Inert Shielding Gases
Examples:
- Argon (Ar)
- Helium (He)
Characteristics:
Inert gases are chemically non-reactive, creating a stable and clean environment around the weld pool. This lack of reactivity ensures that the weld remains uncontaminated, leading to high-quality results.
- Clean Welds: Inert gases prevent oxidation and porosity, producing visually appealing and structurally sound welds.
- Arc Stability: These gases stabilize the arc, making them ideal for precision welding.
- Higher Cost: Inert gases are generally more expensive than active gases, which can increase the overall cost of the welding process.
Applications:
Inert gases are preferred for precise, high-quality welds in non-ferrous materials and thin metals. Examples include:
- Argon (Ar): Widely used for TIG (GTAW) and MIG (GMAW) welding aluminum, stainless steel, and other non-ferrous metals.
- Helium (He): Often blended with argon for applications requiring high heat input, such as welding thick materials or improving arc stability in challenging conditions.
Choosing Between Active and Inert Gases
The decision to use active or inert shielding gases depends on several factors:
- Material Type:
- Ferrous Metals: Active gases like CO₂ or argon-CO₂ blends are often used for welding steel and other ferrous materials.
- Non-Ferrous Metals: Inert gases like pure argon or argon-helium blends are ideal for welding aluminum, magnesium, and other non-ferrous materials.
- Weld Characteristics:
- For deep penetration and strength, active gases are the go-to choice.
- For clean, precise, and aesthetic welds, inert gases are preferred.
- Cost Considerations:
- Active gases are generally more economical, making them suitable for large-scale or high-volume projects.
- Inert gases, while costlier, are worth the investment for applications requiring high-quality welds.
- Welding Process:
- Processes like MIG (GMAW) often use a mix of active and inert gases to balance cost and performance.
- TIG (GTAW) relies almost exclusively on inert gases to ensure precision and cleanliness.
By understanding the roles and benefits of active and inert shielding gases, welders can make informed decisions that optimize both performance and cost-efficiency, ensuring the best results for their specific welding projects.
Argon Blends: Customizing Shielding for Specific Welding Needs
Argon, a versatile and inert shielding gas, is frequently blended with other gases to enhance its performance for specific welding applications. These blends allow welders to tailor the shielding environment, optimizing the welding process for different materials, techniques, and desired outcomes. Here’s a deeper dive into common argon blends and their benefits:
Argon-CO₂ Blends (e.g., 75% Argon, 25% CO₂)
This is the most commonly used blend for Gas Metal Arc Welding (GMAW) on mild steel. It strikes a balance between cost, performance, and versatility, making it a favorite among both hobbyists and professionals.
Benefits:
- Stable Arc: The addition of carbon dioxide enhances arc stability, leading to consistent performance even during longer welding sessions.
- Deeper Penetration: This blend allows for effective penetration into the base material, making it suitable for medium-thickness steel.
- Clean Bead Profile: Produces smooth and visually appealing welds, with minimal spatter compared to using pure CO₂.
- Versatility: Well-suited for short circuit transfer, commonly used in automotive repairs, general fabrication, and structural welding.
Drawbacks:
While highly effective, this blend is more expensive than pure CO₂. However, the reduced cleanup time and improved weld quality often offset the higher cost.
Argon-Helium Blends (e.g., 70% Argon, 30% Helium)
Ideal for both Gas Tungsten Arc Welding (GTAW) and GMAW, this blend excels in industrial applications where high heat input and enhanced arc performance are essential. It is particularly effective for welding thicker materials.
Benefits:
- Increased Heat Input: Helium’s high thermal conductivity increases the heat of the weld pool, enabling better penetration and faster welding speeds, especially on thicker metals.
- Enhanced Arc Characteristics: Helium adds energy to the arc, making it more focused and intense. This is beneficial for achieving deeper fusion in challenging applications.
- Versatility: Suitable for non-ferrous metals like aluminum and magnesium as well as certain stainless steel grades.
Drawbacks:
Helium is more expensive and less readily available than other gases, making this blend a premium option reserved for demanding projects.
Pure Argon
Pure argon is the standard shielding gas for GTAW and is commonly used in GMAW for non-ferrous materials like aluminum, magnesium, and titanium alloys.
Benefits:
- Clean Welds: Argon provides a chemically inert environment, preventing oxidation and ensuring defect-free welds.
- Arc Stability: Delivers a smooth and stable arc, which is essential for precision welding, particularly with thin materials.
- Compatibility: Pure argon is highly versatile and can be used across a wide range of metals and welding techniques.
Argon blends provide welders with the flexibility to adapt to specific project requirements, optimizing the welding process for efficiency, quality, and cost-effectiveness. By selecting the right mix, welders can achieve professional-grade results across various materials and applications.
Why Shielding Gas Choice Matters
Selecting the right shielding gas is one of the most critical decisions in welding. The shielding gas directly impacts the quality, strength, and appearance of the weld, making it more than just a protective element—it’s a key driver of welding performance. The gas serves multiple purposes, including shielding the molten weld pool from atmospheric contaminants, influencing arc stability, and shaping the weld’s final characteristics.
For instance, argon blends are particularly effective for improving arc performance and penetration. Argon’s inert nature ensures a clean welding environment, reducing the risk of porosity and defects that weaken the weld. Blending argon with gases like carbon dioxide or helium allows welders to tailor the welding process to specific materials and techniques, enhancing results. For mild steel, an argon-CO₂ mix like C25 (75% argon, 25% carbon dioxide) strikes a balance between spatter reduction and cost efficiency. On the other hand, pure argon is indispensable for non-ferrous metals like aluminum, ensuring smooth and defect-free welds.
The wrong shielding gas choice can lead to significant issues, such as weak welds, excess spatter, or inconsistent arc stability, ultimately compromising the project. By understanding the properties and applications of different shielding gases, welders can optimize their workflow, reduce costs, and ensure their welds meet both structural and aesthetic standards.
Conclusion
In the world of welding, the interplay between the arc and shielding gas, particularly argon, is fundamental to success. The arc generates the intense heat required for metal fusion, while shielding gas provides essential protection and stability. Argon, whether used alone or in blends, ensures welds are strong, clean, and free from defects, making it a versatile choice across various welding methods, including Gas Tungsten Arc Welding (GTAW) and Gas Metal Arc Welding (GMAW).
The choice of shielding gas is not merely a technical detail—it’s a strategic decision that can elevate the quality of a project. Welders who understand the roles of these components and make informed choices about gas blends can achieve professional-grade results, whether working on precision aerospace components, robust structural steel, or intricate aluminum designs. By tailoring gas selection to the material and welding process, welders can enhance performance, optimize costs, and deliver durable, visually appealing welds that stand the test of time.
Additional Resources
Get your welding gear here.
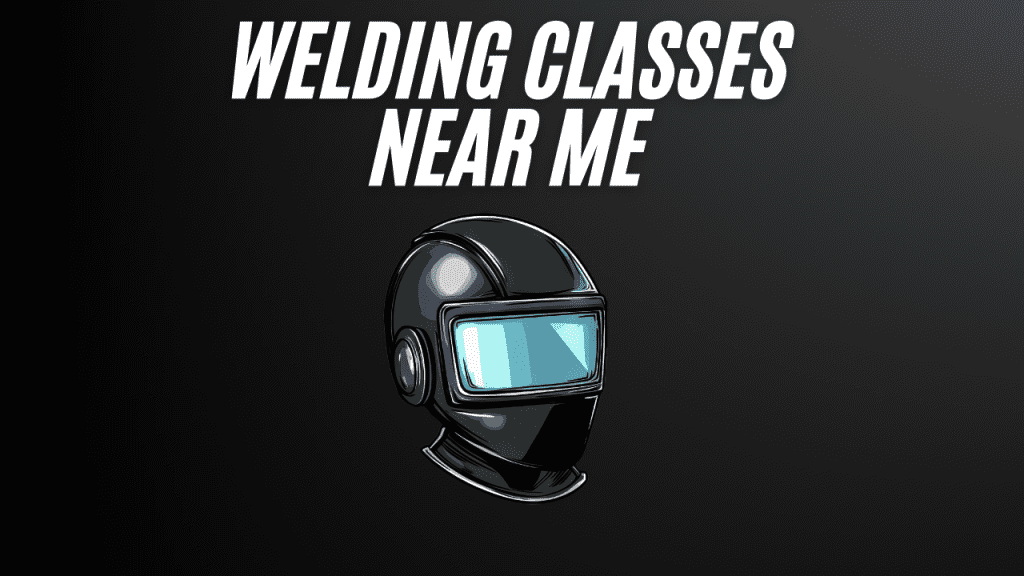