Table of Contents
Riveted Joints vs Welded Joints
In construction and engineering, joining materials is a fundamental task. Riveted joints and welded joints are two widely used techniques, each with its own strengths and limitations. Understanding their differences, applications, and suitability is essential for selecting the right method for a given project.
What Are Riveted Joints?
Riveted joints involve the use of mechanical fasteners, called rivets, to join two or more components. The rivet is inserted into pre-drilled holes and then deformed to hold the pieces together firmly. This method is one of the oldest joining techniques and remains popular in certain applications.
Advantages of Riveted Joints
Strength and Reliability
Riveted joints are renowned for their exceptional strength and reliability. They distribute loads evenly across the connected components, reducing the likelihood of failure. Unlike welded joints, riveted connections are less susceptible to fatigue caused by repeated stress or dynamic loads. This makes them particularly valuable in applications where durability and long-term performance are crucial.
Disassembly
One of the key advantages of riveted joints is their ability to be disassembled and reassembled. This makes them ideal for structures that may require future repairs, modifications, or inspections. Rivets can be removed and replaced without compromising the integrity of the entire structure, which is a significant advantage over permanent welded joints.
Heat Resistance
Riveting does not involve the application of heat, making it a preferred choice for joining materials that are heat-sensitive or prone to warping, such as aluminum alloys. This eliminates the risks associated with heat-affected zones (HAZ) found in welding, ensuring that the base materials retain their original properties.
Consistency
Riveted joints offer uniform strength across the connection, even under dynamic or fluctuating load conditions. This consistency ensures that all parts of the structure can withstand similar stresses, improving overall stability and reliability.
Disadvantages of Riveted Joints
Labor-Intensive
The process of creating riveted joints involves multiple steps, including precise drilling, alignment of components, and the installation of rivets. Each step demands careful attention to detail, making riveting more labor-intensive and time-consuming compared to welding.
Material Overlap
Riveted joints require overlapping materials to accommodate the rivets, which can reduce structural efficiency. This overlap increases the weight of the joint and may limit design flexibility, particularly in lightweight or space-constrained applications.
Weight
The addition of rivets and the requirement for overlapping materials result in heavier joints compared to welded connections. In applications where minimizing weight is critical, such as aerospace or automotive design, this added weight can be a disadvantage.
Applications of Riveted Joints
Aircraft Manufacturing
Rivets are a cornerstone of aircraft construction due to their unmatched reliability and ability to withstand dynamic loads. They perform exceptionally well in environments subject to vibration and fluctuating stresses, making them ideal for securing aircraft skins and structural components.
Bridges
Historical and modern bridges often incorporate riveted joints for their robustness and longevity. Rivets provide the strength and durability needed to support heavy loads and endure environmental factors like wind, temperature changes, and vibration.
Shipbuilding
Rivets are widely used in shipbuilding for sections exposed to dynamic stresses, such as hulls and decks. Their ability to handle fluctuating loads and resist fatigue makes them a reliable choice for maritime applications.
Riveted joints offer distinct advantages that make them indispensable in certain industries and applications. Their strength, reliability, and ability to be disassembled provide flexibility and durability, while their heat resistance ensures compatibility with sensitive materials. However, their labor-intensive nature, material overlap requirements, and added weight highlight the importance of evaluating project-specific needs before choosing riveting over other joining methods like welding.
What Are Welded Joints?
Welded joints are a permanent method of joining materials, typically metals, by melting the base material and, in many cases, adding a filler material to create a strong bond upon cooling. The welding process uses heat, pressure, or a combination of both to fuse materials together, forming a cohesive joint. Welded joints are foundational to modern construction, manufacturing, and industrial applications due to their strength and versatility. They offer seamless and durable connections, making them suitable for projects requiring robust structural integrity.
Advantages of Welded Joints
Material Efficiency
Welded joints do not require overlapping materials as riveted joints do, which reduces both material usage and overall weight. This efficiency is especially beneficial in industries like aerospace and automotive manufacturing, where minimizing weight is critical for performance and cost-effectiveness.
Strength
When executed correctly, welded joints can be as strong as or stronger than the base material. The strength of a weld is highly dependent on the welding technique, materials used, and environmental factors during the process. Properly welded joints are capable of withstanding significant loads and stresses, making them ideal for structural applications.
Seamless Appearance
Welding creates a smooth and continuous surface that is both functional and aesthetically pleasing. This seamless appearance is crucial for applications where design and aerodynamics are priorities, such as in automotive bodies, aircraft, and architectural structures.
Versatility
Welding can join a wide range of materials, including ferrous and non-ferrous metals, as well as thermoplastics. It is also capable of connecting materials of various shapes and thicknesses, from thin sheets to heavy plates, making it a versatile choice for numerous applications.
Disadvantages of Welded Joints
Heat Effects
The intense heat involved in welding can alter the properties of the materials near the joint, creating heat-affected zones (HAZ). These zones are often weaker and more prone to cracking or corrosion than the base material, especially if proper cooling techniques are not followed.
Inspection Challenges
Assessing the quality of a weld often requires specialized non-destructive testing methods, such as X-rays, ultrasonic testing, or dye penetrant inspections. These inspections can be costly and time-consuming but are essential for ensuring the integrity of critical joints.
Skill Dependency
The quality of a welded joint is heavily reliant on the expertise of the welder. A poorly executed weld can compromise the strength and durability of the joint, leading to potential failures. This dependency highlights the need for skilled labor and proper training in welding techniques.
Limited Disassembly
Welded joints are permanent, meaning they cannot be easily disassembled or modified without damaging the materials. This limitation can be a drawback in applications where flexibility or future adjustments may be required.
Applications of Welded Joints
Construction
Welded joints are indispensable in constructing buildings, bridges, and infrastructure. They provide the necessary strength and durability for frameworks, beams, and trusses, ensuring the structural integrity of large-scale projects.
Automotive Manufacturing
Welding is a key process in the automotive industry, used for creating lightweight yet strong vehicle frames and body panels. The seamless nature of welded joints contributes to both safety and performance in modern vehicle designs.
Pipeline Systems
Welded joints are critical in pipeline systems used for transporting liquids, gases, and other substances. They ensure leak-proof connections and can withstand high pressures, making them essential for industries like oil and gas.
Welded joints combine strength, efficiency, and versatility, making them a cornerstone of modern engineering. While they offer numerous advantages, such as reduced material use and seamless finishes, their reliance on skilled execution and permanent nature requires careful consideration during design and fabrication. Despite these challenges, welded joints remain one of the most effective and widely used methods for creating durable and reliable connections in various industries.
Comparative Analysis Riveted Joints vs Welded Joints
Strength and Durability
Riveted Joints
Riveted joints excel in applications involving dynamic or fluctuating loads, such as in bridges or aircraft, where their ability to distribute stress evenly makes them highly reliable. However, they are more prone to failure under shear stresses, as the rivets themselves can deform or break if the forces exceed their capacity. While durable, riveted joints may loosen over time due to vibration or wear, requiring periodic inspection and maintenance.
Welded Joints
Welded joints provide superior strength and rigidity, often matching or exceeding the base material’s strength. This makes them ideal for high-stress applications, such as pipelines and structural frameworks. However, welded joints are more susceptible to fatigue cracks over time, particularly in heat-affected zones (HAZ). Proper welding techniques and post-weld treatments can mitigate these issues, but fatigue remains a concern in cyclic loading conditions.
Weight and Material Usage
Riveted Joints
Riveted joints necessitate overlapping materials to accommodate rivet placement, increasing the overall weight of the structure. The additional fasteners also contribute to material usage, which can be a disadvantage in industries like aerospace, where weight reduction is critical. While the added weight might enhance durability in some cases, it often results in inefficiency.
Welded Joints
Welded joints eliminate the need for overlapping materials, reducing both weight and material costs. This efficiency is particularly advantageous in industries requiring lightweight designs, such as automotive and aerospace. By fusing materials directly, welding achieves a streamlined structure without the bulk associated with rivets, enhancing overall performance.
Cost
Riveted Joints
The labor-intensive nature of riveting, which involves precise drilling, alignment, and fastening, makes it a more expensive option. Additionally, the material costs associated with rivets and overlapping components further increase expenses. While riveted joints may offer long-term reliability, their initial cost can be a barrier for large-scale projects.
Welded Joints
Welding is typically faster and more cost-effective, especially in mass production settings. The streamlined process reduces labor and material costs, particularly for large-scale or automated applications. However, the cost of skilled labor and specialized equipment can offset these savings in smaller projects or where precision welding is required.
Inspection and Maintenance
Riveted Joints
Riveted joints are relatively easy to inspect visually, as issues such as loose or deformed rivets are readily apparent. They are also easier to maintain, as individual rivets can be replaced without dismantling the entire joint. This makes riveted joints advantageous in applications requiring frequent inspections, such as in bridges or airplanes.
Welded Joints
Welded joints often require advanced non-destructive testing (NDT) methods, such as X-rays, ultrasonic testing, or magnetic particle inspection, to identify internal flaws or cracks. These techniques can be costly and time-consuming. Additionally, repairing welded joints is more challenging, as the process typically involves grinding out the existing weld and re-welding, which may weaken the surrounding material.
Aesthetic Considerations
Riveted Joints
Riveted joints tend to have a bulkier appearance, which can detract from the visual appeal of certain structures. While this may not be a concern in industrial or utilitarian applications, it is a disadvantage for projects where aesthetics are important, such as modern architectural designs.
Welded Joints
Welded joints provide a smooth and seamless finish, making them the preferred choice for visible or decorative structures. The lack of protruding fasteners enhances both the aesthetics and aerodynamics of the design, making welding the go-to option for sleek and polished appearances in automotive, aerospace, and architectural projects.
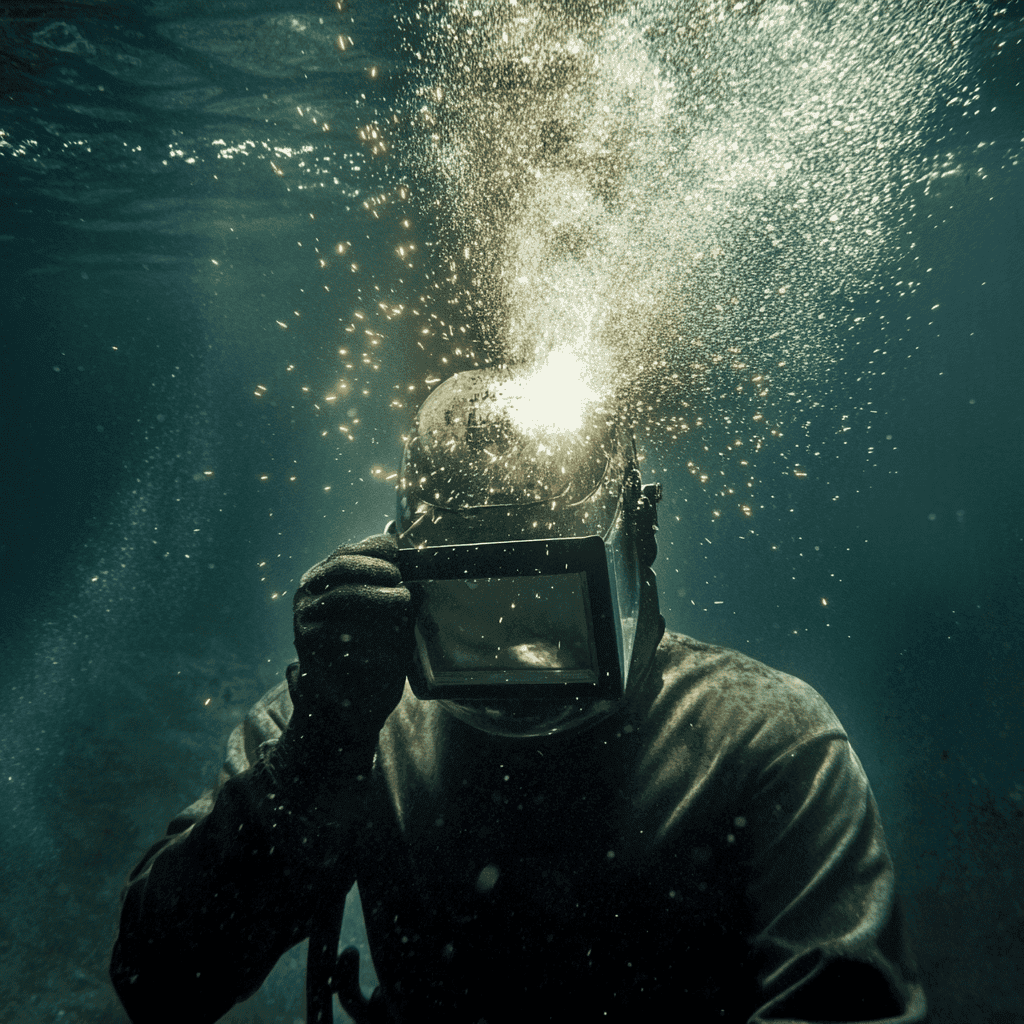
Environmental and Longevity Considerations
Riveted Joints
Corrosion Resistance
Riveted joints can be prone to corrosion in the areas where the rivets meet the base materials, especially in environments with high moisture or salinity, such as coastal regions. However, using corrosion-resistant materials like stainless steel rivets can mitigate this issue.
Longevity
Riveted joints are durable over time, especially in applications like bridges or historical buildings. Many riveted structures from the early 20th century remain functional today, demonstrating their reliability and longevity.
Environmental Impact
The production and installation of rivets involve higher material use and labor, potentially increasing the overall environmental footprint compared to welding. However, the ability to disassemble riveted structures makes them more sustainable for projects requiring future modifications or repairs.
Welded Joints
Corrosion Challenges
Welded joints are particularly vulnerable in the heat-affected zones (HAZ), where the metal’s properties can be altered during the welding process. If not treated properly, these areas may corrode faster than the surrounding material, especially in harsh environments.
Longevity
Welded joints offer excellent durability when properly executed and maintained. Advanced welding techniques and post-weld treatments, such as stress relieving or coating, can enhance the joint’s resistance to environmental factors and extend its lifespan.
Environmental Impact
Welding generally uses fewer materials compared to riveting, which can reduce the environmental footprint. However, the energy-intensive nature of welding processes and the reliance on shielding gases like argon or CO₂ may contribute to higher energy consumption and emissions.
Comparison Summary
Riveted joints are advantageous in applications requiring long-term reliability in fluctuating load conditions and environments where disassembly or retrofitting is anticipated. Welded joints, while slightly more prone to environmental challenges in the HAZ, offer greater efficiency and durability when proper materials and techniques are applied. By incorporating environmental and longevity factors into the analysis, both methods demonstrate unique advantages suited to specific applications and project requirements.
Conclusion
The choice between riveted and welded joints depends on the project’s specific needs, including load conditions, material properties, cost constraints, and aesthetic preferences. Riveted joints are ideal for dynamic loads and situations requiring disassembly, while welded joints offer strength, material efficiency, and a sleek finish. Understanding the strengths and limitations of each method ensures optimal performance and longevity in engineering applications.
Additional Resources
Get your welding gear here.
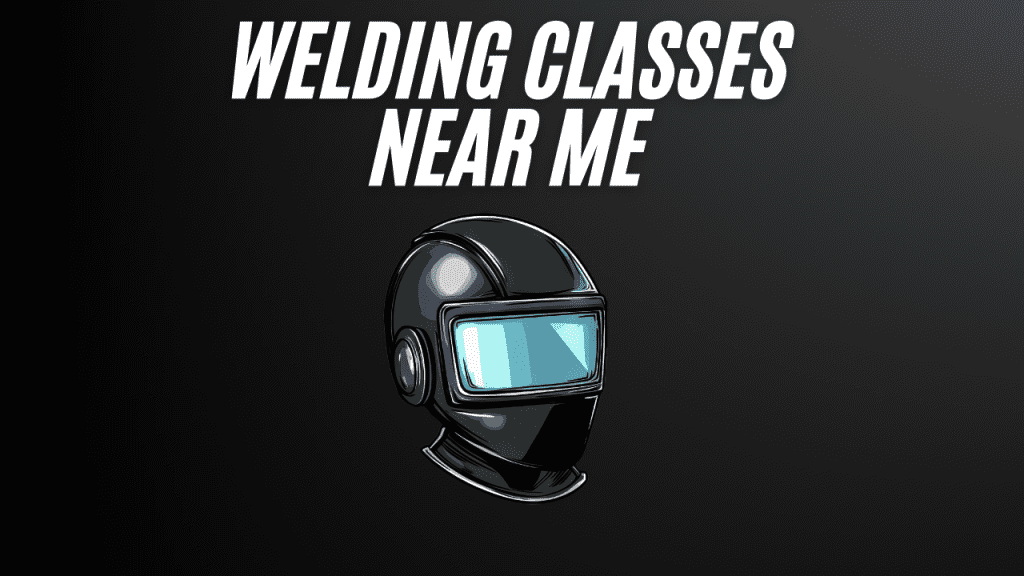