Table of Contents
Reinforced Concrete Explained: Pros and Cons
Introduction: What is Reinforced Concrete?
Reinforced concrete is a construction material made by combining traditional concrete with reinforcing steel cables or bars. The addition of steel enhances the concrete’s tensile strength, making it suitable for structures that need to withstand both compressive and tensile forces. Proper engineering is critical when using reinforced concrete, as insufficient reinforcement can lead to structural failure.
This material offers unique benefits, including its ability to be molded and shaped into various forms, allowing for creative and innovative architectural designs. Reinforced concrete is widely used in construction projects due to its strength, durability, versatility, and cost-effectiveness. It is commonly applied in everything from foundations to building roofs.
Reinforced Concrete Explained: Pros and Cons
Pros of Reinforced Concrete
1. Strength
Reinforced concrete is prized for its exceptional ability to combine tensile strength (resistance to stretching forces) and compressive strength (resistance to squeezing forces). While concrete alone excels in compression, it is weak in tension. Steel reinforcement compensates for this weakness, allowing structures to withstand a variety of forces effectively. This synergy makes reinforced concrete ideal for high-load applications such as bridges, skyscrapers, and industrial facilities. Its ability to handle dynamic loads, such as those from vehicles or natural forces, ensures structural integrity under challenging conditions.
2. Economical
The affordability of reinforced concrete is one of its greatest advantages. The raw materials—cement, sand, aggregates, and water—are readily available worldwide and cost-effective compared to other construction materials like steel. The steel reinforcement, while adding to the cost, is used in relatively small quantities and enhances the material’s value. Additionally, the durability and low maintenance of reinforced concrete result in significant long-term savings. Structures made from this material often have a lifespan of 100 years or more, reducing the need for frequent repairs or replacements. The relatively low energy consumption during production compared to alternative materials further enhances its cost-efficiency.
3. Versatility
Reinforced concrete’s liquid state when fresh makes it incredibly versatile. It can be poured into molds or formworks of any shape or size, enabling architects and engineers to create innovative and aesthetically pleasing designs. This adaptability is why reinforced concrete is used for everything from curved bridges and artistic facades to industrial tanks and domes. The ability to incorporate various textures, colors, and finishes also makes it a preferred choice for architectural projects where aesthetics and functionality go hand in hand.
4. Durability
When properly designed and constructed, reinforced concrete structures exhibit remarkable durability. The material’s low permeability prevents water and chemical penetration, protecting it from damage caused by chlorides, sulfates, and other corrosive substances. This makes it especially suitable for submerged or marine applications, such as dams, canals, and seawalls, where constant exposure to water and chemicals is a concern. Additionally, its resistance to weathering ensures longevity in environments with extreme temperatures, freeze-thaw cycles, or heavy precipitation. With appropriate maintenance, reinforced concrete can withstand the test of time, often surpassing a century of service.
5. Fire Resistance
Concrete’s non-combustible nature gives it a significant edge in fire safety. Reinforced concrete structures can withstand temperatures of up to 1,100°C (2,012°F) for extended periods (typically 2–6 hours), providing critical time for evacuation and emergency response during a fire. This makes it a preferred material for high-rise buildings, tunnels, and industrial facilities where fire safety is a top priority. Unlike steel, which can weaken at high temperatures, reinforced concrete retains its structural integrity, making it a more reliable choice for blast-proof and fireproof applications.
6. Ductility
The addition of steel reinforcement imparts ductility, or the ability to bend or deform without immediate failure, to reinforced concrete. This feature allows structures to exhibit warning signs such as cracking or deflection under excessive loads, enabling engineers to take corrective actions before catastrophic failure occurs. Ductility also enhances the material’s ability to absorb and dissipate energy, making it suitable for applications where flexibility under stress is critical, such as bridges and seismic zones.
7. Seismic Resistance
Reinforced concrete is inherently well-suited to withstand earthquake forces, provided it is properly designed. The combination of steel’s flexibility and concrete’s mass allows the material to absorb and dissipate seismic energy effectively. Engineers can further enhance its performance by incorporating techniques such as reinforced shear walls and dampers. Reinforced concrete’s seismic resistance makes it a preferred material for constructing buildings, dams, and bridges in earthquake-prone regions, ensuring both safety and durability.
8. Ease of Construction
Compared to steel or other specialized construction materials, reinforced concrete is easier to work with on-site. The need for less skilled labor to prepare and assemble reinforced concrete structures reduces construction costs and project timelines. Its flexibility in placement methods, such as pouring, pumping, or spraying, allows it to adapt to various site conditions, including tight spaces or complex geometries. This ease of use makes it particularly advantageous for large-scale infrastructure projects.
9. Sustainability
Reinforced concrete has become an increasingly sustainable choice for modern construction. By incorporating recycled materials, such as fly ash, slag (GGBFS), or crushed glass, it is possible to reduce the environmental footprint of its production. These substitutes not only decrease reliance on virgin materials but also enhance the material’s strength and durability. For example, fly ash improves workability and resistance to chemical attacks. Using waste products in concrete production also addresses global challenges like industrial waste management, aligning with sustainable construction practices.
10. Multi-Mode Application
One of the key advantages of reinforced concrete is its ability to be used in various application methods. Depending on the project requirements, reinforced concrete can be:
- Poured for slabs and foundations.
- Pumped for high-rise construction.
- Grouted for filling voids or repairing structures.
- Sprayed as shotcrete for tunnels and slope stabilization.
- Precast into modular units for bridges, walls, and columns.
This adaptability ensures that reinforced concrete can meet the demands of a wide range of construction scenarios, from routine buildings to advanced engineering applications like underwater tunnels or blast-resistant bunkers.
Summary
The advantages of reinforced concrete—its strength, durability, versatility, fire resistance, and adaptability—make it one of the most widely used and trusted materials in construction. Its ability to combine functionality with sustainability ensures that it remains a cornerstone of modern infrastructure, capable of meeting the demands of safety, efficiency, and innovation. With proper design and execution, reinforced concrete continues to be a resilient and cost-effective choice for both architectural and structural projects.
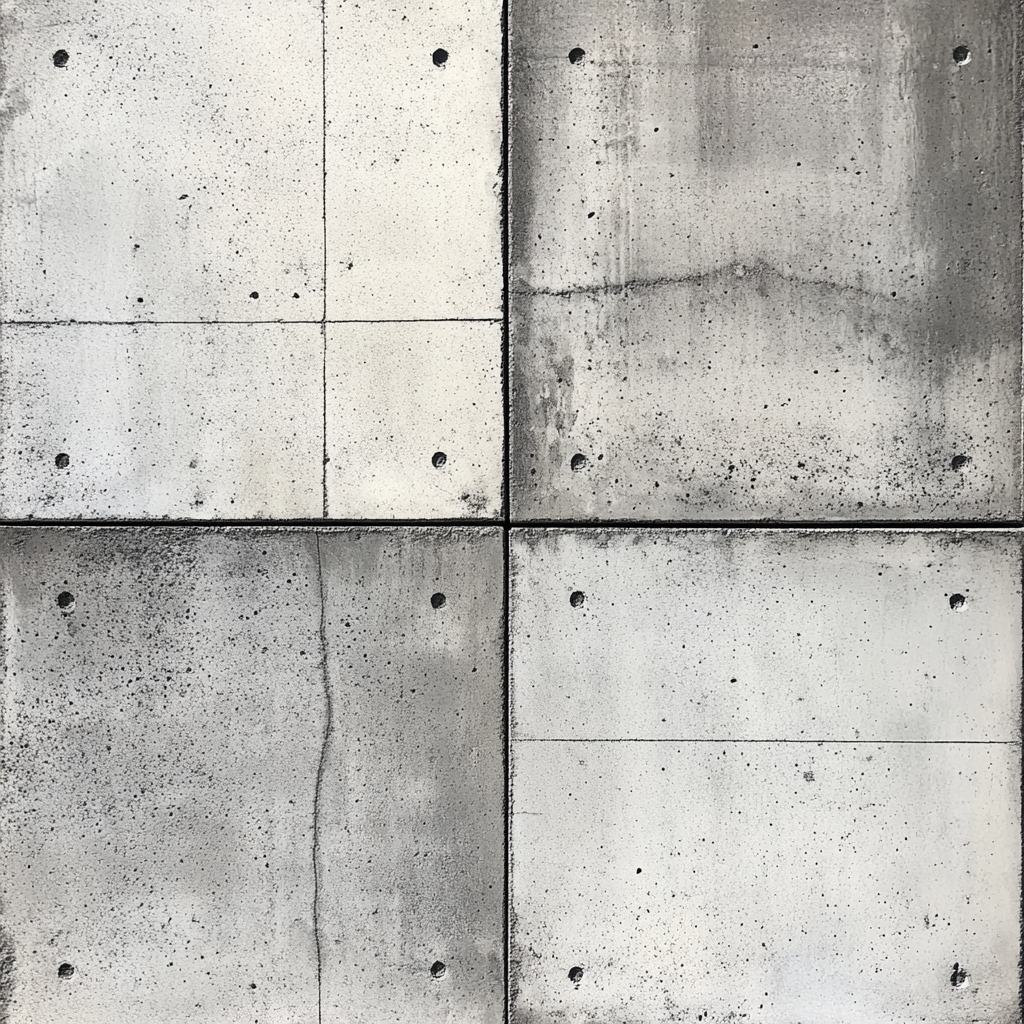
Cons of Reinforced Concrete
While reinforced concrete offers numerous advantages, it is not without its challenges. Understanding these drawbacks is crucial for engineers, architects, and builders to make informed decisions and mitigate potential issues during construction and use.
1. Forms and Molds for Casting Can Be Expensive
Reinforced concrete requires formwork or molds to shape and hold the concrete until it cures and hardens. These molds can be made of wood, steel, or plastic and are essential for achieving the desired shape and surface finish. However, creating and maintaining these molds adds significant costs to the construction process, especially for projects with complex shapes or unique architectural designs.
- High Initial Investment: Custom molds for specialized structures can be costly to fabricate and install.
- Labor-Intensive Process: Setting up, aligning, and dismantling the formwork requires skilled labor, adding to construction expenses.
- Reusability Concerns: While some molds can be reused, frequent use can lead to wear and tear, requiring replacement or repairs, further increasing costs.
To minimize expenses, engineers often use modular or prefabricated formwork systems, but this may not always be feasible for highly customized designs.
2. Shrinkage During Curing Can Lead to Cracks
One of the inherent challenges of concrete is shrinkage, which occurs as the material dries and cures. This shrinkage is caused by the evaporation of water used during mixing, and if not properly managed, it can result in cracks that compromise the structural integrity and aesthetics of the finished product.
- Thermal Cracking: Differences in temperature during curing can create stress within the concrete, leading to cracks.
- Drying Shrinkage: Excessive evaporation of water from the surface can cause the concrete to contract unevenly, forming small or large cracks.
- Prevention Costs: Mitigating shrinkage requires techniques such as adding control joints, curing compounds, or shrinkage-reducing admixtures, all of which can increase project costs.
Cracks not only affect the durability of reinforced concrete but also provide entry points for water, chemicals, and air, potentially leading to corrosion of the steel reinforcement and accelerated deterioration over time.
3. Tensile Strength is Only About 1/10th of Its Compressive Strength
Concrete alone is inherently weak in tension, with tensile strength being only about 1/10th of its compressive strength. While steel reinforcement improves the tensile properties, the disparity between tension and compression can still pose challenges.
- Need for Reinforcement: Steel bars or cables must be added to address this weakness, which increases construction costs and complexity.
- Crack Development: Despite reinforcement, tensile forces may still cause cracks to develop in areas with high stress, such as beams, slabs, or foundations.
- Limited Applications Without Reinforcement: In scenarios where steel reinforcement cannot be used—such as budget constraints or temporary structures—reinforced concrete may not be the best choice.
For structures subjected to significant tensile forces, alternative materials like steel or pre-stressed concrete may be more suitable. Additionally, modern techniques like fiber-reinforced concrete (using synthetic, glass, or carbon fibers) are being explored to improve tensile properties without relying solely on steel.
Addressing the Cons of Reinforced Concrete
While reinforced concrete has certain drawbacks, many of these can be effectively mitigated through thoughtful planning, advanced technologies, and best practices during construction. Here’s how professionals address some of the key challenges:
1. Managing the Costs of Forms and Molds
The high cost of formwork and molds can be a significant challenge, especially for large-scale or complex projects. However, there are several strategies to minimize expenses:
- Reusable Formwork Systems: Investing in high-quality reusable forms made of durable materials like steel or aluminum can lower costs over time. These forms can be used for multiple projects with minimal wear and tear.
- Prefabricated Formwork: Modular formwork systems can be prefabricated off-site and quickly assembled on-site, reducing labor costs and construction time.
- Efficient Design: Engineers can design structures to minimize the need for custom molds. For instance, using standard shapes and dimensions simplifies formwork requirements.
- Rental Options: For short-term or one-time projects, renting formwork is a cost-effective alternative to purchasing custom molds.
2. Preventing Shrinkage and Cracking During Curing
Shrinkage is a natural process in concrete curing, but proactive measures can greatly reduce the risk of cracking:
- Proper Curing Techniques: Ensuring consistent moisture levels during the curing process helps prevent excessive drying. Techniques such as water spraying, wet coverings, or curing compounds maintain the necessary humidity levels.
- Control Joints: Introducing control joints at strategic points in the structure allows for controlled cracking along predetermined lines, preserving the structural integrity of the concrete.
- Shrinkage-Reducing Admixtures: Chemical admixtures can be added to the concrete mix to minimize shrinkage. These additives reduce water loss and control the internal stresses that cause cracks.
- Fiber Reinforcement: Incorporating synthetic or steel fibers into the concrete mix enhances its resistance to shrinkage and minimizes the development of surface cracks.
- Temperature Management: Maintaining a stable temperature during curing can prevent thermal stresses, particularly in massive concrete pours where internal heat generation can lead to cracking.
3. Improving Tensile Strength
The inherent weakness of concrete in tension is addressed through reinforcement and emerging technologies:
- Steel Reinforcement: Proper placement of steel reinforcement bars (rebar) ensures that tensile forces are effectively managed. Adequate overlap, spacing, and anchorage of rebar improve tensile performance.
- Pre-Stressed Concrete: Pre-stressing involves applying tension to the reinforcement before the concrete sets. This technique creates compressive stress within the concrete, counteracting tensile forces and increasing overall strength. It is commonly used in bridge construction and large-span structures.
- Fiber-Reinforced Concrete (FRC): Adding synthetic, glass, or carbon fibers to the concrete mix improves tensile strength and controls crack propagation. FRC is particularly useful for slabs, overlays, and structures with high tensile stress.
- High-Performance Concrete: Advanced concrete formulations, such as ultra-high-performance concrete (UHPC), offer improved tensile properties and are ideal for demanding applications like high-rise buildings and long-span bridges.
4. Enhancing Efficiency and Sustainability
Many of the cons associated with reinforced concrete can be addressed through sustainable and efficient practices:
- Recycled Materials: Using supplementary materials like fly ash, slag, and recycled aggregates reduces costs and environmental impact while improving the concrete’s performance.
- Lean Construction Techniques: Adopting lean construction principles minimizes waste, optimizes material use, and reduces the environmental footprint of concrete production.
- Advanced Construction Technologies: Innovations such as 3D concrete printing and robotic placement techniques improve accuracy and reduce labor costs, making reinforced concrete more cost-effective and efficient.
5. Regular Maintenance and Inspection
Ongoing maintenance can mitigate long-term issues such as cracks or corrosion of reinforcement:
- Sealants and Coatings: Applying protective coatings to concrete surfaces prevents water and chemical penetration, reducing the risk of corrosion.
- Routine Inspections: Periodic checks help identify early signs of wear or damage, allowing for timely repairs before problems escalate.
- Corrosion-Resistant Materials: Using epoxy-coated or stainless-steel reinforcement reduces the risk of rust and extends the lifespan of the structure.
6. Leveraging Modern Design Practices
Designing reinforced concrete structures with potential drawbacks in mind can lead to better performance and cost savings:
- Structural Optimization: Engineers can optimize designs to balance strength, weight, and cost, ensuring efficient use of materials without compromising safety.
- Integrated Design Approaches: Collaborating across disciplines (architecture, engineering, and construction) during the design phase minimizes the need for costly modifications and enhances structural efficiency.
Summary
While reinforced concrete has some inherent challenges, these can be effectively addressed through innovation, proper design, and adherence to best practices. By leveraging advanced techniques, sustainable materials, and preventive measures, construction professionals can maximize the benefits of reinforced concrete while minimizing its limitations. This adaptability ensures that reinforced concrete remains a cornerstone of modern infrastructure and architecture.
Applications of Reinforced Concrete
Reinforced concrete’s unique combination of strength, durability, and versatility makes it indispensable in modern construction. Its adaptability to various environments and structural requirements ensures its use across a broad spectrum of applications. Below is a detailed exploration of the key uses of reinforced concrete:
1. Foundations
Reinforced concrete is the material of choice for building foundations, as it provides the strength and stability required to support heavy loads. Its resistance to compressive forces and ability to distribute weight evenly across the soil make it ideal for various foundation types, such as:
- Strip Foundations: Commonly used for walls and lightweight structures.
- Raft Foundations: Suitable for large buildings where soil conditions are uneven.
- Pile Foundations: Essential for high-rise buildings and structures in areas with weak or unstable soil.
The durability of reinforced concrete foundations ensures a long lifespan, even in harsh environmental conditions.
2. Water Tanks
Reinforced concrete is widely used for constructing water tanks due to its resistance to water and chemical corrosion.
- Underground Tanks: Ideal for storing water in areas with limited space.
- Overhead Tanks: Elevated tanks provide water pressure for residential and industrial use.
- Septic Tanks: Used for wastewater management in residential and commercial properties.
The material’s low permeability prevents water seepage and protects against chemical damage, ensuring long-term performance.
3. Roads and Bridges
Reinforced concrete is extensively used in transportation infrastructure because of its ability to withstand heavy loads and harsh environmental conditions.
- Roads: Provides durable surfaces that resist wear and tear from vehicles and weather.
- Bridges: Ideal for constructing long-span and high-traffic bridges, as reinforced concrete can handle dynamic loads and resist seismic forces.
Reinforced concrete bridges and roads also benefit from minimal maintenance requirements, making them cost-effective over their lifecycle.
4. Buildings
From residential homes to skyscrapers, reinforced concrete is a staple in building construction.
- Residential Buildings: Provides strong and durable structures that are fire and weather-resistant.
- High-Rise Buildings: Reinforced concrete’s ability to support heavy loads and withstand wind and seismic forces makes it essential for tall structures.
- Industrial Facilities: Used for warehouses and factories, where durability and strength are paramount.
The material’s flexibility in design allows for architectural creativity while maintaining structural integrity.
5. Marine Structures
The durability and corrosion resistance of reinforced concrete make it ideal for marine applications, including:
- Docks and Piers: Withstand constant exposure to water and salt.
- Seawalls: Provide protection against coastal erosion.
- Offshore Platforms: Essential for oil and gas extraction operations.
Reinforced concrete’s ability to resist sulfates and chlorides ensures long-term performance in submerged environments.
6. Towers and Chimneys
Vertical structures, such as towers and chimneys, benefit from the high compressive strength of reinforced concrete.
- Communication Towers: Provides stability for radio and cell towers.
- Industrial Chimneys: Can withstand high temperatures and chemical exposure, making them ideal for factories and power plants.
Reinforced concrete’s resistance to environmental stressors ensures the safety and longevity of these structures.
7. Bunkers and Silos
Reinforced concrete is commonly used for bunkers and silos due to its durability and strength.
- Military Bunkers: Provide blast resistance and long-lasting protection.
- Agricultural Silos: Used to store grains and other materials, ensuring they remain protected from the elements.
These structures benefit from reinforced concrete’s ability to withstand extreme conditions and heavy loads.
8. Pipes and Conduits
Reinforced concrete pipes are integral to modern infrastructure for transporting fluids and managing drainage.
- Water Supply Systems: Used for large-scale municipal water distribution.
- Sewer Systems: Durable and resistant to chemical erosion, making them ideal for wastewater management.
- Conduits: Provide a protective path for cables and utility lines.
Reinforced concrete pipes are highly durable and require minimal maintenance, ensuring long-term functionality.
Other Notable Applications of Reinforced Concrete
In addition to its primary uses in foundations, buildings, bridges, and marine structures, reinforced concrete is indispensable for various specialized applications. These other notable uses demonstrate its adaptability and resilience in diverse construction and infrastructure projects.
Retaining Walls
Reinforced concrete retaining walls are critical for stabilizing slopes and preventing soil erosion.
- Landscaping: Commonly used to create terraced gardens or support sloped terrains in residential and commercial properties.
- Road Construction: Stabilizes embankments along highways and protects against landslides.
- Waterfront Projects: Retaining walls help manage water levels and prevent shoreline erosion.
These walls must withstand significant lateral pressure from soil or water, making reinforced concrete an ideal material due to its compressive strength and durability.
Flyovers and Overpasses
Reinforced concrete is extensively used in the construction of flyovers and overpasses to manage traffic in urban areas and improve connectivity.
- Traffic Management: Helps alleviate congestion by allowing vehicles to bypass busy intersections or cross highways.
- Durability: These structures can withstand heavy vehicle loads and environmental stressors, such as extreme weather conditions and seismic activity.
Reinforced concrete ensures the longevity and low maintenance of these structures, making it a cost-effective choice for public infrastructure projects.
Tunnels
Reinforced concrete is essential in the construction of tunnels, which require materials that can handle high pressure and adverse conditions.
- Transportation Tunnels: Used for subways, highways, and railways to connect urban centers or navigate through mountains.
- Utility Tunnels: Protects and houses pipelines, power cables, and communication lines.
- Mining Tunnels: Provides structural integrity and safety in mining operations.
Reinforced concrete’s ability to resist compression, water infiltration, and chemical corrosion makes it a reliable choice for tunneling projects.
Cooling Towers
Reinforced concrete is a preferred material for cooling towers, which are vital components of industrial and power plants.
- Power Plants: Used in thermal, nuclear, and geothermal plants to dissipate heat efficiently.
- Durability: Withstands high temperatures, humidity, and chemical exposure from cooling water or emissions.
- Structural Stability: The height and shape of cooling towers require a material that can handle wind loads and thermal expansion, making reinforced concrete ideal.
Its resistance to environmental and operational stressors ensures these structures remain functional and safe for decades.
Industrial Flooring
Reinforced concrete is commonly used for industrial floors, especially in warehouses, factories, and distribution centers.
- Load-Bearing Capacity: Can withstand the weight of heavy machinery, forklifts, and stored goods.
- Durability: Resists wear and tear from constant use and chemical spills.
- Customization: Floors can be reinforced and polished for specific industrial needs, such as smooth surfaces for robotics or high friction for safety.
Reinforced concrete floors provide a long-lasting, low-maintenance solution for demanding industrial environments.
Parking Structures
Reinforced concrete is extensively used in parking garages and multi-level parking structures due to its strength, versatility, and fire resistance.
- Load Support: Handles the weight of multiple vehicles and the dynamic forces of moving cars.
- Design Flexibility: Allows for ramps, columns, and cantilevered sections to optimize space and accessibility.
- Fire Resistance: Protects vehicles and infrastructure in case of fire incidents.
Its durability and low maintenance needs make it an economical choice for public and private parking facilities.
Waterfront and Submerged Structures
Reinforced concrete plays a significant role in creating structures designed to withstand marine environments.
- Breakwaters and Seawalls: Protect shorelines from waves and erosion.
- Ports and Jetties: Provide durable docking and loading areas for ships.
- Underwater Tunnels: Connect islands or cross water bodies while resisting water pressure and chemical erosion.
Special concrete mixes and coatings can further enhance resistance to saltwater and other corrosive elements, ensuring long service life.
Precast Concrete Elements
Reinforced concrete is frequently used in precast elements, which are manufactured off-site and assembled on-site for faster construction.
- Beams and Columns: Provide structural support for buildings and bridges.
- Wall Panels: Used in both residential and commercial construction for quick installation.
- Drainage Pipes: Precast pipes handle stormwater, wastewater, and irrigation systems efficiently.
Precasting reduces construction time, minimizes waste, and ensures consistent quality, making it an attractive option for large-scale projects.
Blast-Resistant Structures
In areas where safety and security are paramount, such as military installations or high-risk industrial facilities, reinforced concrete is used to create blast-resistant structures.
- Military Bunkers: Protect personnel and equipment from explosions.
- Industrial Facilities: Safeguard critical components and workers in explosive environments like chemical plants.
The material’s ability to absorb and dissipate energy makes it ideal for these high-stakes applications.
Summary
The wide range of applications for reinforced concrete highlights its versatility, durability, and cost-effectiveness. From foundational infrastructure to specialized industrial and marine projects, reinforced concrete provides reliable solutions for modern construction challenges. Its adaptability and ability to withstand diverse environmental and structural demands make it an indispensable material for shaping the built environment.
Conclusion
Reinforced concrete is a cornerstone material in modern construction due to its unique combination of strength, durability, versatility, and affordability. While it has its limitations, such as susceptibility to cracking and relatively low tensile strength, its benefits far outweigh its drawbacks. With proper engineering and application, reinforced concrete can provide long-lasting, cost-effective solutions for a wide range of construction projects, from infrastructure to innovative architectural designs.
Additional Resources
Get your welding gear here.
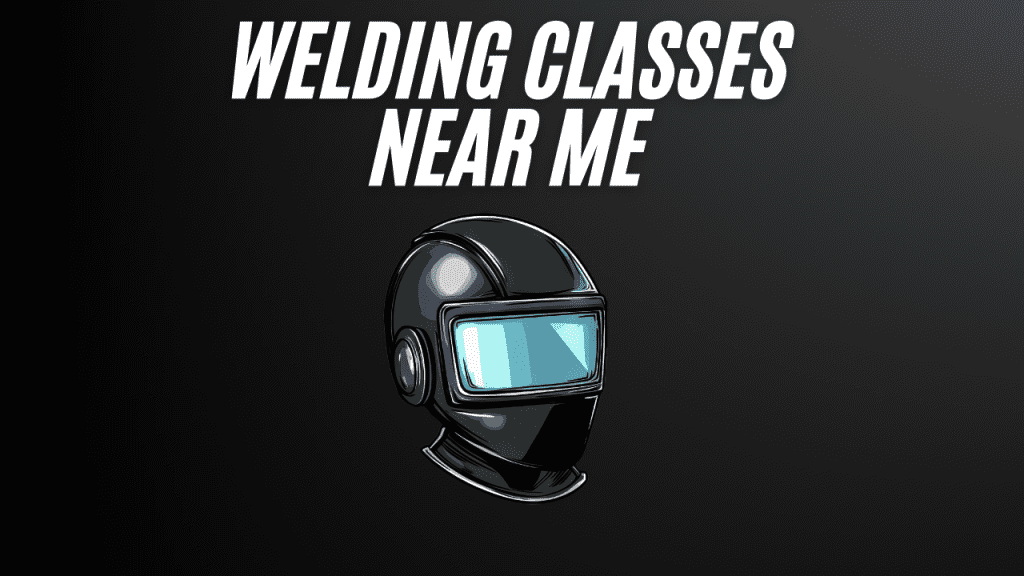