Table of Contents
Is MIG Welding Easier Than Stick Welding?
When comparing MIG (Metal Inert Gas) welding and stick welding, a common question arises: which is easier to learn and perform? While both methods are versatile and widely used, their learning curves and practical applications differ significantly. MIG welding is often seen as the easier option, especially for beginners, but both techniques have their own set of advantages and challenges. Below, we delve into the details to help you decide which method might suit your needs.
Ease of Learning: MIG vs Stick
MIG welding is often considered the easier of the two methods to learn due to its straightforward setup and operation. Beginners can typically grasp basic MIG welding techniques within one to two weeks of practice. This accessibility stems from MIG welding’s semi-automated process, where a wire electrode feeds continuously through the MIG gun. This automatic feeding allows the welder to focus primarily on maintaining a steady hand and proper positioning, reducing the need for intricate manual coordination.
The simplicity of MIG welding also lies in its forgiving nature for beginner mistakes. The clean and consistent wire feed minimizes interruptions during the welding process, helping novices build confidence. Additionally, the use of shielding gas ensures a clean weld pool, which further reduces potential errors caused by environmental contamination. For these reasons, MIG welding is frequently the starting point for welding students and hobbyists.
Stick welding, by contrast, demands more skill and practice to master, making it a steeper learning curve for beginners. While some may learn basic stick welding techniques in as little as 12 minutes, this often involves just striking an arc rather than producing high-quality welds. The real challenge of stick welding lies in mastering the finer details: maintaining a stable arc, controlling the heat input, and managing the weld puddle. These tasks require a higher degree of manual dexterity and real-time adjustments.
Another difficulty in stick welding is handling the flux-coated electrode, which burns away during welding to generate shielding gas. Beginners often struggle to strike the arc without sticking the electrode to the workpiece, a common problem that can disrupt the process and frustrate new welders. Furthermore, the slag that forms as a byproduct of the flux must be chipped away after welding, adding an extra layer of complexity compared to MIG welding’s relatively clean finish.

Similarities Between MIG and Stick Welding
Despite their differences in learning difficulty, MIG and stick welding share foundational similarities that make them essential arc welding techniques:
- Arc Welding Processes: Both methods rely on an electric arc to generate the heat needed to melt the base material and filler metal. This shared principle makes them effective for a wide range of welding applications.
- Shielding Mechanism: Each method employs a shielding gas to protect the weld pool from atmospheric contaminants like oxygen and nitrogen, which can cause porosity or weaken the weld. MIG welders use a gas tank to supply this shielding, while stick welders rely on the flux coating of the electrode to produce gas during welding.
- Material Compatibility: Both techniques can be used to weld various metals, including stainless steel, mild steel, aluminum, and cast iron. This versatility ensures that welders trained in either method have a broad range of applications to work with.
Key Differences in Mechanics and Applications
Understanding the mechanics and applications of MIG and stick welding underscores their distinct advantages and limitations. These differences highlight why each method is better suited for specific environments, materials, and skill levels.
Shielding Mechanisms
- MIG Welding: The shielding gas in MIG welding—typically argon or a mix of argon and CO₂—is delivered from a gas tank. This creates a stable protective barrier over the weld pool, ensuring a clean weld by preventing atmospheric contaminants like oxygen and nitrogen from interfering. However, this reliance on an external gas supply makes MIG welding highly susceptible to environmental factors. Even a light breeze can disrupt the shielding gas, leading to porosity and weakened welds. As a result, MIG welding is best suited for indoor or controlled environments where the gas shield remains undisturbed.
- Stick Welding: Unlike MIG welding, stick welding generates its shielding gas through the flux coating on the electrode. As the flux burns, it forms both a gas shield and a layer of slag over the weld, providing dual protection against contamination. This self-contained shielding mechanism makes stick welding more robust in outdoor settings, even in windy conditions of up to 35 mph. The added resilience to environmental factors makes stick welding a preferred choice for construction sites, pipelines, and other outdoor projects.
Portability
- MIG Welders: The need for a gas tank in MIG welding reduces portability, as the equipment becomes bulkier and more cumbersome to transport. This limitation is particularly noticeable in remote or on-site jobs where mobility is a priority.
- Stick Welders: Compact and self-contained, stick welders are highly portable. They don’t rely on external gas tanks, making them easier to move and set up in various locations. This portability is a significant advantage for welders working on large-scale construction sites or in rugged terrains where accessibility is a concern.
Weld Quality
- MIG Welds: MIG welding produces clean, aesthetically pleasing welds with minimal spatter and no slag. This reduces the need for post-weld cleanup, saving time and effort, particularly in applications where visual appeal is important, such as automotive bodywork or furniture fabrication. However, MIG welding’s effectiveness can be compromised on dirty or rusty surfaces, as contaminants may weaken the weld.
- Stick Welds: Known for their strong penetration, stick welds excel in joining thicker materials and creating durable bonds. However, the process generates slag, which must be chipped away after welding. While this additional cleanup step can be time-consuming, the ability to weld through rust, dirt, or paint makes stick welding ideal for projects involving less-than-pristine surfaces.
Indoor vs Outdoor Use
- MIG Welding: The reliance on shielding gas limits MIG welding’s effectiveness in outdoor environments. Wind can easily blow away the protective gas, exposing the weld pool to contamination and compromising its quality. While wind shields or enclosures can mitigate this issue, such solutions add complexity and are not always feasible for large outdoor projects.
- Stick Welding: With its flux-based shielding system, stick welding thrives in outdoor conditions. The combination of slag and gas generated by the flux ensures weld integrity, even in challenging environments. This makes stick welding an excellent choice for infrastructure projects, farm equipment repairs, and other outdoor applications where weather conditions may be unpredictable.
By understanding these differences, welders can choose the appropriate method based on their project requirements, environment, and skill level. While MIG welding offers ease of use and clean welds, stick welding provides unmatched resilience and adaptability in outdoor and heavy-duty applications.
Applications Based on Material
Cast Iron
Stick welding is the go-to method for welding cast iron. The variety of electrodes available for stick welding ensures strong, durable bonds, even with the challenging nature of cast iron. Stick welding’s ability to handle impurities and surface imperfections is a key advantage in working with this brittle material. MIG welding, on the other hand, often struggles to achieve reliable welds with cast iron, frequently resulting in weaker joints and less durable repairs.
Aluminum
For aluminum, MIG welding is the clear choice. The wire-fed system of MIG welding allows for smooth, consistent welds without the complications introduced by flux. Additionally, the absence of flux in MIG welding eliminates issues with moisture absorption, which can cause problems in stick welding. MIG welding is particularly advantageous for aluminum applications requiring precision and clean aesthetics, such as manufacturing or automotive projects. Stick welding, while capable of welding aluminum, presents challenges such as difficulty maintaining arc stability and the need for rapid execution to prevent oxidation.
Thin Metal Stock
MIG welding shines when working with thin metals, such as 24-gauge sheets. Its precise control over heat and the ability to adjust settings for minimal burn-through make it ideal for delicate applications like automotive bodywork and duct fabrication. Stick welding, in contrast, is less effective for thin materials due to its higher heat input and tendency to burn through the metal. This limitation makes stick welding less suitable for projects involving lightweight or thin materials.
Thick Metal Stock
When it comes to thick metal—materials over 3/8 inch—stick welding is the superior choice. Its ability to achieve deep penetration ensures robust and long-lasting welds. This makes stick welding ideal for heavy-duty applications such as structural steel fabrication, pipeline welding, and large-scale construction projects. MIG welding, while versatile, typically struggles with thicker metals unless advanced techniques or specialized equipment, like dual-shield flux-cored setups, are used. Even then, it may not match the penetration strength of stick welding.
Ease of Use
Both MIG and stick welding have their own learning curves, but MIG welding is often seen as easier for beginners:
- MIG Welding: While it requires setting up components like a gas tank, spool wire, and machine settings, once the equipment is prepared, operating a MIG welder is straightforward. Beginners benefit from the simple “pull the trigger and weld” approach, which minimizes errors and boosts confidence.
- Stick Welding: Stick welding involves fewer equipment variables, making setup quicker. However, it demands greater skill to start and maintain a stable arc. Beginners often struggle with electrode sticking and controlling the weld puddle, making it more challenging to master initially.
Cost Comparison
- MIG Welders: The complexity of MIG welding equipment—such as the integrated gas handling systems and wire feeders—makes it more expensive upfront. Additionally, ongoing costs for shielding gas and consumables like wire spools can add to the long-term expense. This makes MIG welding a more significant financial investment, particularly for hobbyists or small-scale operators.
- Stick Welders: Stick welding equipment is simpler, with fewer components to purchase and maintain. The absence of a gas tank or wire feeder contributes to its affordability. For welders on a budget or those seeking a cost-effective option for heavy-duty work, stick welding offers an economical solution. Moreover, the electrodes used in stick welding are often less expensive and easier to store than MIG wire and shielding gas.
By understanding these differences in material applications, ease of use, and cost, welders can make informed decisions about which method suits their needs, whether they’re tackling lightweight aluminum or heavy structural steel.
Safety Considerations
Safety Considerations for MIG and Stick Welding
Welding, regardless of the method, comes with inherent risks that require careful attention to safety protocols. Understanding the specific hazards associated with MIG and stick welding can help welders take appropriate precautions to ensure their safety and the safety of those around them.
Electric Shock Risks
Electric shock is one of the most serious dangers in welding. Both MIG and stick welders use high electrical currents to create the arc, posing a risk if the equipment is improperly handled. Stick welding, in particular, operates at higher voltages and amperages, increasing the likelihood of electric shock if proper precautions aren’t taken. Welders should always wear dry, insulated gloves, avoid touching live electrical components, and ensure their work area is free of moisture. Proper grounding of equipment is also crucial to minimize risks.
Fumes and Ventilation
Welding produces hazardous fumes and gases that can pose health risks if inhaled over extended periods. Stick welding generates more fumes and slag due to the flux coating on the electrodes. These fumes often contain harmful particulates and gases like manganese and hexavalent chromium, which can cause respiratory issues or long-term health effects if ventilation is inadequate.
MIG welding, while producing fewer fumes, can still release dangerous gases, especially when welding certain metals or using shielding gas mixtures. Welders should ensure their workspace is well-ventilated, using exhaust systems or fans to direct fumes away from their breathing zone. For enclosed or poorly ventilated spaces, respirators or supplied-air systems may be necessary to provide adequate protection.
Spatter and Slag Hazards
Both MIG and stick welding produce molten metal spatter, which can cause burns or ignite nearby flammable materials. Stick welding also creates slag as a byproduct of the flux, which requires chipping and grinding after welding. This process can result in flying debris that poses a risk to the eyes and skin.
Welders should always wear flame-resistant clothing, leather gloves, and protective footwear to shield themselves from sparks and hot metal. A welding helmet with appropriate eye protection is essential to guard against spatter and the intense light produced by the welding arc, which can cause eye damage (arc flash) if not properly shielded.
Compressed Gas Handling
In MIG welding, compressed gas cylinders are used to supply the shielding gas needed for clean welds. Mishandling these cylinders can result in accidents, such as leaks or explosions. Cylinders should always be stored upright, secured to prevent tipping, and kept away from heat sources. Welders must also regularly check connections and hoses for leaks, using soapy water to identify any escaping gas.
Fire Hazards
Both welding methods pose fire risks due to the heat, sparks, and molten metal they produce. Stick welding, with its higher spatter levels, increases the likelihood of nearby materials catching fire. Welders should ensure their workspace is free of flammable materials, such as sawdust, paper, or chemical containers. Fire extinguishers or fire blankets should be kept nearby as a precaution.
Ergonomic Considerations
Prolonged welding sessions can strain the welder’s posture, hands, and arms, especially in awkward positions. Stick welding often requires holding heavy electrodes and maintaining a steady hand, which can lead to fatigue. MIG welding, while generally lighter and easier to handle, can still cause repetitive strain injuries if proper ergonomics are not observed. Welders should take regular breaks, use adjustable equipment to suit their height and reach, and employ ergonomic aids like welding rests or clamps to reduce physical strain.
Key Safety Measures
- Proper Equipment: Always wear certified welding helmets, gloves, flame-resistant clothing, and safety boots.
- Inspection: Regularly check welding machines, cables, and gas connections for wear or damage.
- Training: Understand the specific hazards of the metals and gases being used. For example, welding galvanized steel produces toxic zinc fumes that require additional precautions.
- Emergency Preparedness: Keep fire extinguishers, first aid kits, and eye-wash stations within easy reach in case of accidents.
By understanding and mitigating these risks, welders can ensure a safer working environment while maintaining the high-quality welds that MIG and stick welding are known for.
Pros and Cons of MIG and Stick Welding
MIG Welding Pros
- Cleaner Welds with Minimal Spatter
MIG welding produces clean and aesthetically pleasing welds with minimal spatter. This makes it ideal for projects where appearance is critical, such as automotive bodywork or decorative metal structures. The lack of slag also reduces the need for post-weld cleanup, saving time and effort. - High Speed and Efficiency
The continuous wire feed in MIG welding allows for faster welding speeds compared to stick welding. This efficiency is particularly valuable for large-scale projects or production settings where time is of the essence. - Ideal for Thin Materials and Aluminum
MIG welding excels at joining thin-gauge materials, such as sheet metal, and is well-suited for welding aluminum. The precise control over heat and filler material ensures that delicate materials are not burned through, making it a preferred choice for automotive and aerospace applications.
MIG Welding Cons
- Requires Clean Surfaces for Effective Welding
MIG welding demands clean, rust-free, and debris-free surfaces for optimal results. Contaminants can compromise the quality of the weld, leading to defects such as porosity or weak joints. This necessitates additional surface preparation, which can be time-consuming. - Not Suitable for Windy Environments
The shielding gas used in MIG welding is easily disrupted by wind, making it less effective for outdoor applications. Even light breezes can blow away the protective gas, leading to weld defects and making MIG welding impractical for certain outdoor projects. - Higher Initial and Ongoing Costs
MIG welding machines are more complex and expensive than stick welders, requiring components like gas cylinders, regulators, and wire feeders. The ongoing costs of consumables, such as shielding gas and wire, also add to the expense, making it a pricier option overall.
Stick Welding Pros
- Works Well on Dirty or Rusty Metals
Stick welding is highly forgiving when it comes to surface conditions. It can create strong welds on metals that are dirty, rusty, or painted, making it ideal for repair work and environments where surface preparation is difficult or impractical. - Suitable for Outdoor and Windy Conditions
Unlike MIG welding, stick welding relies on flux-coated electrodes that generate their own shielding gas. This makes it highly effective in windy outdoor environments where traditional shielding gas would be blown away. - Affordable and Portable
Stick welding machines are simple, compact, and affordable, making them an excellent choice for hobbyists or welders on a budget. Their portability allows for easy transportation to different job sites, especially in remote or rugged locations.
Stick Welding Cons
- Produces Slag and Spatter That Require Cleanup
The flux coating on stick electrodes produces slag as a byproduct, which must be chipped away after welding. The process also generates more spatter, leading to additional cleanup and preparation for subsequent work or painting. - Difficult to Use on Thin Materials
Stick welding is less effective on thin materials, as the high heat and lack of fine control can easily cause burn-through. This makes it unsuitable for projects involving sheet metal or other delicate materials. - Harder to Master Due to Arc-Starting Challenges
Starting and maintaining a stable arc in stick welding can be challenging, especially for beginners. Factors such as electrode angle, distance, and consistency require practice and skill, making stick welding more difficult to learn compared to MIG welding.
By weighing these pros and cons, welders can determine the best method for their specific needs and applications, considering factors such as material type, project environment, budget, and desired weld quality.
Conclusion
While both MIG and stick welding have their strengths, MIG welding is generally considered easier to learn and use, especially for beginners. Its ability to produce clean, high-quality welds with minimal effort makes it a preferred choice for indoor projects and thin materials. Stick welding, on the other hand, excels in outdoor environments and with thicker materials, making it a valuable skill for heavy-duty applications.
The choice between MIG and stick welding ultimately depends on your project requirements, budget, and working conditions. Both methods are valuable, and mastering either will enhance your welding capabilities. For beginners, starting with MIG welding may offer a quicker path to proficiency, while stick welding remains a reliable option for those tackling rugged, outdoor tasks.
Additional Resources
Get your welding gear here.
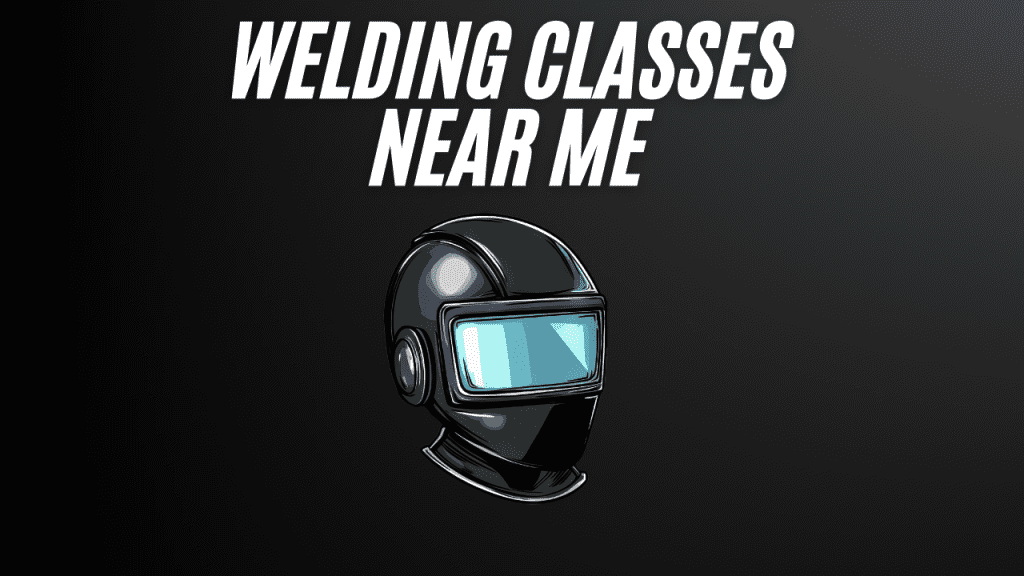