Table of Contents
How to Weld Copper
Copper welding can be a challenging but rewarding task. This guide covers essential techniques, safety tips, and methods to help you successfully weld copper using TIG and MIG welding processes.
TIG Welding Copper: Detailed Tips and Considerations
Copper welding requires specialized techniques due to the material’s unique properties, including its high thermal conductivity and susceptibility to warping. TIG welding (Tungsten Inert Gas welding) is particularly effective for copper, offering precision and control. Below are expanded tips for achieving successful results when TIG welding copper.
Use High Temperatures
Copper requires higher temperatures to weld effectively because of its ability to quickly absorb and dissipate heat. Set your TIG welder to approximately 300°F or 20–30°F higher than the settings you would use for stainless steel. This higher temperature ensures the weld pool forms correctly, allowing proper fusion of the base material and filler rod.
- Why it Matters: Copper’s high thermal conductivity can cause heat to dissipate rapidly, potentially leading to weak welds or incomplete fusion if insufficient heat is applied.
Consider Preheating
Preheating is essential, especially when working with thicker pieces of copper or copper alloys. By uniformly preheating the workpiece, you reduce the thermal gradient between the weld area and the surrounding material. This helps to:
- Minimize warping caused by uneven expansion and contraction.
- Maintain a stable weld pool, making it easier to achieve a clean and consistent weld.
- Reduce the risk of cracking in high-stress applications.
How to Preheat:
- Use a propane torch, induction heating, or an oven to gradually bring the copper to the desired temperature before welding.
De-Oxidized Copper
De-oxidized copper is preferred for TIG welding because it has been treated to remove impurities that can interfere with the welding process. Oxidized copper is prone to warping, cracking, and producing weak joints. De-oxidized copper improves weld quality by ensuring:
- A cleaner weld pool with fewer impurities.
- Reduced likelihood of porosity in the final weld.
- Enhanced durability and strength in the joint.
High Amperage Requirements
TIG welding machines used for copper must be capable of delivering 300-400 amps to provide sufficient heat for melting. This high amperage is necessary to overcome copper’s ability to conduct heat away from the weld area.
- Equipment Consideration: Ensure your TIG machine is rated for high amperage and has adequate cooling systems, as welding at these settings can generate significant heat.
Safety First
Copper welding generates toxic fumes, particularly when welding copper alloys containing zinc or other elements. Proper safety precautions are critical:
- Ventilation: Work in a well-ventilated area and use fume extraction equipment to remove harmful fumes.
- Personal Protective Equipment (PPE):
- Wear a welding helmet with appropriate lens shading to protect your eyes.
- Use a welding jacket, gloves, and leather boots to shield yourself from heat and sparks.
- Consider a respirator if welding indoors or in confined spaces.
- Workplace Preparation: Ensure flammable materials are cleared from the area to reduce fire risks.
Additional Tips for TIG Welding Copper
- Filler Rod Selection: Use a filler rod that matches the composition of the copper or copper alloy being welded. For example, when welding pure copper, choose a filler with a similar copper content to ensure compatibility.
- Electrode Choice: Use a tungsten electrode with a high melting point, such as thoriated or ceriated tungsten, to withstand the heat required for copper welding.
- Shielding Gas: Employ 100% argon or an argon-helium mixture for optimal shielding of the weld pool. Helium improves heat transfer and is particularly useful for thicker copper materials.
By following these detailed tips and precautions, TIG welding copper becomes a manageable process that yields high-quality, durable joints. Mastering these techniques ensures safe and successful welding of copper for various applications, from industrial projects to artistic designs.
MIG Welding Copper: Expanded Tips and Best Practices
MIG (Metal Inert Gas) welding, also known as GMAW (Gas Metal Arc Welding), can effectively join copper and copper alloys with proper preparation and technique. Below are expanded tips to help achieve successful results when MIG welding copper.
Preheat Small Pieces
Copper’s high thermal conductivity allows it to absorb and dissipate heat quickly, making preheating an essential step, especially for smaller workpieces. Preheating helps to:
- Reduce Thermal Gradients: By evenly distributing heat, preheating minimizes stress concentrations that can lead to warping or cracking.
- Stabilize the Weld Pool: Ensures the molten pool forms consistently, improving fusion and penetration.
- Facilitate Heat Retention: Maintains a steady welding temperature for smoother operation.
How to Preheat:
- Use a torch or heating device to bring the copper to a temperature of around 150–300°F, depending on the thickness and alloy composition.
- Preheat uniformly to avoid localized overheating, which can cause distortion.
Proper Shielding Gas
Shielding gas is critical in MIG welding copper, as it protects the weld pool from atmospheric contamination and influences the weld’s heat profile. Selecting the right shielding gas ensures high-quality results:
- 100% Argon: A common choice for copper MIG welding, providing stable arc characteristics and clean welds.
- Argon-Helium Mixtures: Adding helium enhances heat transfer, making it ideal for thicker copper materials or alloys that require deeper penetration.
- Avoid Carbon Dioxide: While CO₂ is often used for steel welding, it is less effective for copper, as it can cause excessive oxidation and spatter.
Gas Flow Rate:
- Adjust the flow rate to maintain a consistent gas shield over the weld pool, typically 20–30 CFH (cubic feet per hour), depending on the welding environment.
Settings and Technique
Fine-tuning your MIG machine settings is vital for adapting to copper’s unique properties:
- Voltage and Amperage:
- Use higher voltage and amperage settings compared to those for steel or aluminum. Copper requires more heat input due to its high thermal conductivity.
- Wire Feed Speed:
- Adjust the wire feed speed to match the copper thickness and desired deposition rate. Start with moderate speeds and increase as needed to avoid burn-through on thinner materials.
- Electrode Selection:
- Choose a wire electrode specifically designed for copper or copper alloys. For example:
- ERCuSi-A: Suitable for copper-silicon alloys and general-purpose copper welding.
- ERCuNi: Ideal for copper-nickel alloys, offering excellent corrosion resistance.
- Choose a wire electrode specifically designed for copper or copper alloys. For example:
- Welding Technique:
- Use a push technique (angled forward) for better visibility and to maintain a stable weld pool.
- Maintain a consistent contact tip-to-work distance (around 1/4 to 3/8 inches) to ensure steady arc performance.
- Travel Speed:
- Move the gun at a controlled pace to allow sufficient heat penetration. Slower speeds provide better fusion but may increase the risk of warping, so balance is key.
Additional Tips for MIG Welding Copper
- Base Metal Preparation:
- Clean the copper thoroughly to remove contaminants like oil, grease, or oxide layers, which can weaken the weld and cause porosity.
- Post-Weld Treatment:
- Inspect the weld for defects and apply finishing techniques, such as grinding or polishing, to enhance the weld’s appearance and structural integrity.
- Use of Backing Plates:
- For thin copper sheets, use a backing plate made of aluminum or copper to prevent burn-through and ensure a consistent weld pool.
- Cooling Control:
- Allow the workpiece to cool gradually to prevent thermal shock, which can cause cracking or warping.
MIG welding copper requires a combination of precise machine settings, proper shielding gas, and sound technique. By following these tips, welders can effectively handle copper’s unique challenges, producing strong, clean, and reliable joints suitable for various applications, including electrical components, piping, and decorative work.
General Tips for Welding Copper
Welding copper presents unique challenges due to its high thermal conductivity and susceptibility to oxidation. Following these expanded general tips ensures a safer and more effective welding process.
Prioritize Safety
- Personal Protective Equipment (PPE)
- Use a welding helmet with an appropriate shade lens to protect your eyes from the intense arc.
- Wear insulated leather gloves to guard against heat and UV radiation.
- Opt for flame-resistant welding jackets and leather boots to protect against sparks and molten metal.
- Ventilation and Fume Management
- Copper welding produces toxic fumes that can be harmful when inhaled. Ensure your workspace is well-ventilated or use mechanical ventilation systems.
- Employ a smoke extractor gun or fume extraction hood to remove harmful particles from the breathing zone.
- Fire Safety
- Clear the area of flammable materials like paper, sawdust, or chemicals.
- Keep a fire extinguisher nearby and ensure all personnel know its location and usage.
Select the Right Filler Material
- Material Strength and Compatibility
- Choose a filler material that is stronger than the base metal to ensure weld durability. For instance:
- Use 30-70 nickel-copper filler when the alloy contains at least 70% copper for improved strength and corrosion resistance.
- Choose a filler material that is stronger than the base metal to ensure weld durability. For instance:
- Tailored Filler for Alloys
- Match the filler material to the copper alloy being welded. For example:
- Use a silicon-bronze filler for copper alloys with high silicon content.
- Opt for aluminum-bronze fillers for copper-aluminum alloys in high-strength applications.
- Match the filler material to the copper alloy being welded. For example:
Prepare the Base Metal
- Cleanliness is Key
- Thoroughly clean the surface to remove contaminants like oil, grease, paint, or oxides. Use a wire brush, degreaser, or solvent for optimal results.
- Contaminants can introduce porosity and weaken the weld joint.
- Material Compatibility
- Understand the composition of the materials being joined. For instance:
- Avoid welding copper-zinc-tin alloys with nickel-copper alloys, as their differing thermal and chemical properties can result in weak or brittle welds.
- Understand the composition of the materials being joined. For instance:
Follow Basic Welding Procedures
- Preparation Based on Thickness
- For copper materials less than 3 mm thick, use a square butt joint with squared edges for ease of fusion.
- For thicker materials, employ a beveled edge with an angle between 60° and 90° to ensure adequate penetration.
- Adapting Welding Techniques
- Adjust your welding technique according to the copper thickness. This includes using slower travel speeds and preheating for thicker materials to manage heat dissipation effectively.
Optimize Welding Position
- Down-Hand Welding
- Down-hand welding (flat position) is ideal for copper as it simplifies the process and ensures better control over the molten pool.
- This position also minimizes the risk of warping caused by copper’s high thermal expansion.
- Design for Accessibility
- When dealing with complex or multi-position designs, assemble the workpiece strategically to allow for as much down-hand welding as possible. This approach reduces the difficulty of managing heat and arc stability in vertical or overhead positions.
- Welding for Thin Sheets
- For thin copper sheets, use a forehand welding method (pushing the torch forward) to provide better visibility and control over the weld pool.
- Switch to backhand welding (pulling the torch) for sheets over 1/4 inch thick to enhance penetration and weld stability.
By adhering to these expanded tips, you can handle the challenges of welding copper effectively, ensuring strong, clean, and reliable joints. Proper safety measures, material preparation, and process adjustments are key to achieving high-quality welds that stand the test of time.
Welding Thin Copper Sheets
- Forehand Method: Use this technique for thin sheets up to 1/4 inch in thickness.
- Backhand Method: Best suited for thicker sheets over 1/4 inch.
- Joint Selection:
- Use plain butt joints with squared edges for sheets up to 1/8 inch thick.
- For thicker sheets, bevel the edges with an included angle of 60-90° to ensure deep penetration and even fusion.
- Scarf, Butt, and Lap Joints: Frequently used in brazing operations, with tight clearances to allow optimal penetration of filler metal.
Challenges in Welding Copper
Welding copper presents several unique challenges due to its distinct physical and chemical properties. Understanding and addressing these challenges is essential for achieving successful welds.
High Thermal Conductivity
- Heat Absorption
Copper’s high thermal conductivity means it absorbs and disperses heat rapidly. This characteristic requires higher heat input compared to other metals like steel, as the heat dissipates quickly away from the weld zone.- Impact: The rapid heat dissipation can make it difficult to maintain a stable molten pool, leading to incomplete fusion or weak welds.
- Solution: Use welding equipment capable of delivering high amperage (300-400 amps for TIG welding) and consider preheating the copper to reduce heat loss.
- Energy Demands
The additional energy needed to weld copper can strain equipment and increase operational costs, making it necessary to invest in high-performance welding machines and accessories.
Warping
- Thermal Expansion
Copper’s high coefficient of thermal expansion makes it prone to significant dimensional changes when exposed to heat.- Impact: This expansion can cause warping or distortion of the material, especially in thin sheets or complex structures.
- Solution: Preheat the material uniformly to reduce the temperature gradient and control cooling rates to minimize warping.
- Post-Weld Distortion
Improper heat management can result in residual stresses that deform the copper after welding, affecting its dimensional stability and alignment.- Solution: Use clamps or fixtures during welding to hold the material in place and employ controlled cooling techniques to reduce stress.
Filler Metal Selection
- Material Compatibility
The choice of filler metal is crucial for ensuring joint strength and corrosion resistance. Using incompatible fillers can lead to defects such as cracking, porosity, or weak bonds.- Impact: Incompatible fillers may react with the base metal, creating brittle or porous welds that compromise the joint’s integrity.
- Solution: Match the filler material to the copper alloy being welded. For example, a 30-70 nickel-copper filler is ideal for alloys with high copper content.
- Weld Properties
The filler material must have properties that align with the intended application of the welded component, such as electrical conductivity, thermal stability, or mechanical strength.- Solution: Consult material specifications and standards, such as AWS classifications, to select the appropriate filler.
Safety Concerns
- Toxic Fumes
Welding copper produces fumes that contain harmful substances, including copper oxides, which can be toxic when inhaled.- Impact: Prolonged exposure to these fumes can lead to serious health issues, including respiratory irritation and metal fume fever.
- Solution: Ensure proper ventilation in the workspace by using fume extraction systems or smoke extractor guns. Always wear appropriate respiratory protection.
- Arc Flash and Heat Risks
The intense heat and brightness of the arc used in copper welding pose additional safety risks, such as burns or eye damage.- Solution: Use a high-quality welding helmet with the appropriate shade filter and wear flame-resistant clothing, gloves, and boots to protect against sparks and molten metal.
- Flammability and Fire Hazards
The high heat required for welding copper increases the risk of igniting nearby flammable materials.- Solution: Clear the welding area of flammable objects and have a fire extinguisher readily available.
By addressing these challenges with the proper techniques, equipment, and safety measures, welders can overcome the complexities of working with copper. This preparation not only ensures high-quality welds but also enhances safety and efficiency during the welding process.
Final Thoughts
Welding copper requires a specialized approach, considering its unique properties like high thermal conductivity and susceptibility to warping. By following these tips, ensuring proper preparation, and understanding the type of copper alloy being used, you can achieve strong, clean welds. Before tackling a significant project, practice on smaller, disposable pieces to refine your technique. With proper tools and methods, copper welding can be a highly rewarding skill.
Additional Resources
Get your welding gear here.
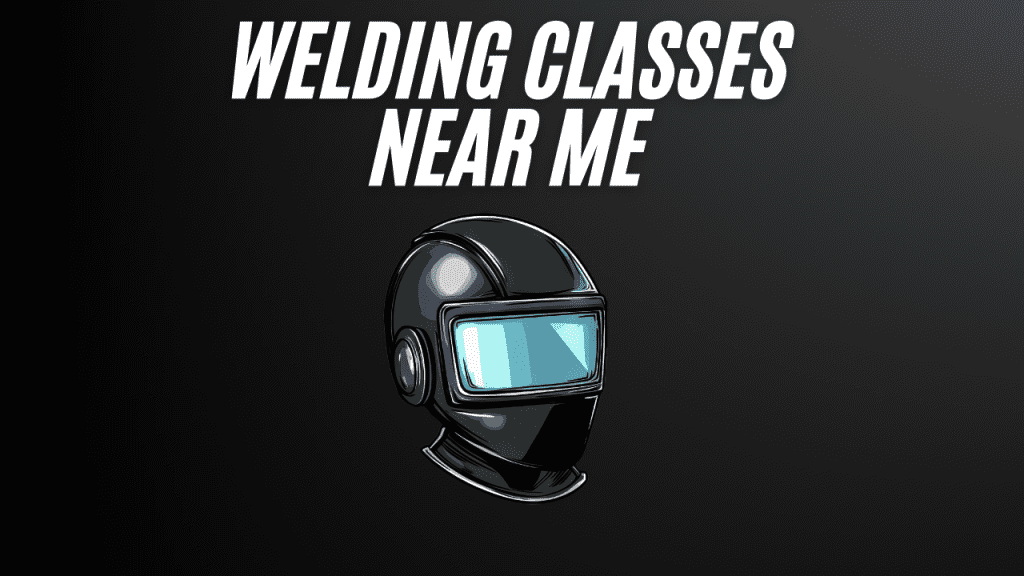