Table of Contents
How Thick Can a 180 Amp MIG Weld?
A 180 amp MIG welder is a versatile tool that can handle a range of metal thicknesses, making it a popular choice for hobbyists and professionals alike. Understanding the welder’s capacity is essential for achieving optimal results in your welding projects. Here’s what you need to know about how thick a 180 amp MIG welder can weld and the factors that influence its performance.
Basics of MIG Welding and Amperage
The MIG Welding Process in Detail
MIG welding involves feeding a wire electrode through a welding gun while simultaneously supplying a shielding gas to protect the weld from atmospheric contamination. The electric arc created between the wire and the base material generates heat, melting the metals and allowing them to fuse. This process is praised for its simplicity and efficiency, making it accessible even to beginners. It is commonly used in automotive repairs, manufacturing, and construction projects where speed and versatility are critical.
- Shielding Gas: Argon or an Argon/CO2 mix is typically used for its ability to produce clean, controlled welds. Pure CO2 is an alternative for deeper penetration but may cause more spatter.
- Electrode Wire: The electrode acts as both the heat source and the filler material, making wire selection essential for weld quality.
- Applications: MIG welding is ideal for welding thin to medium-thickness metals, including steel, stainless steel, and aluminum.
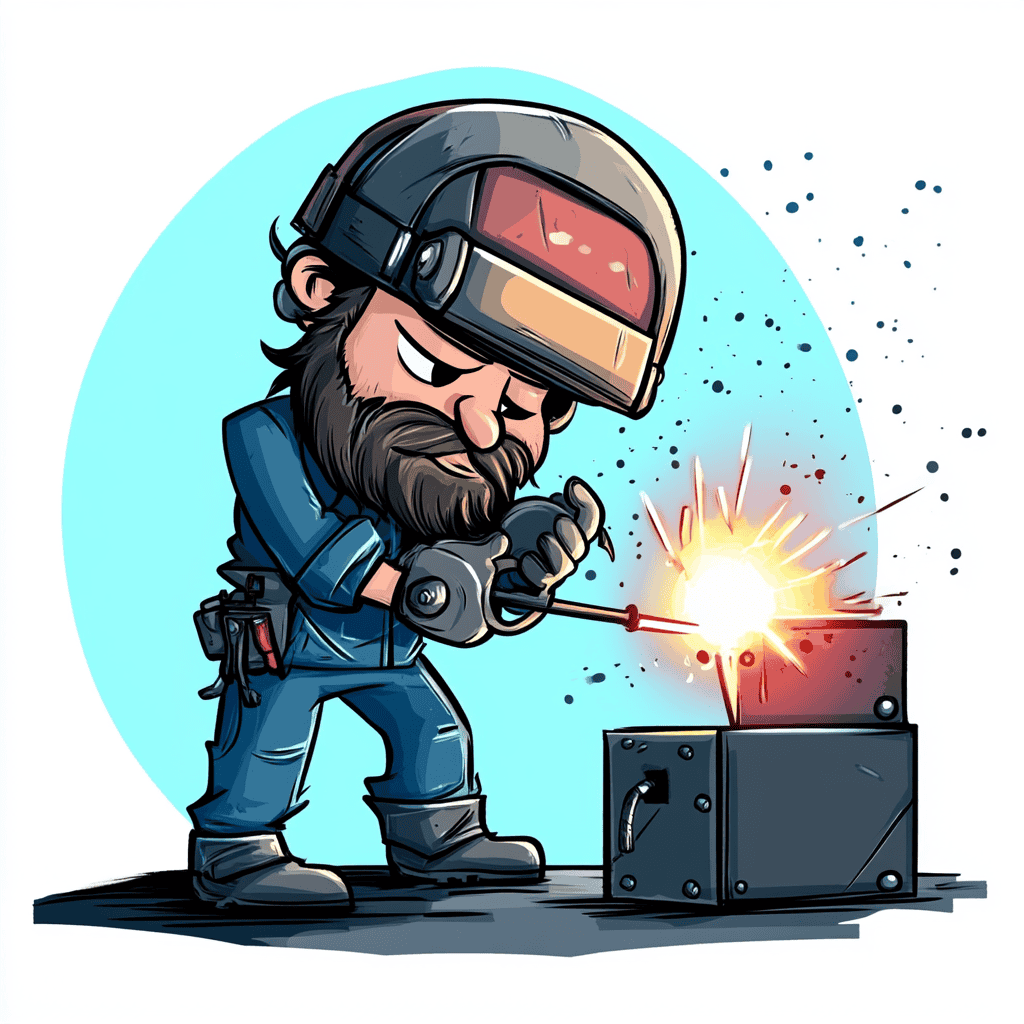
The Impact of Amperage on Welding Performance
Amperage plays a crucial role in determining the depth of weld penetration and the thickness of materials that can be welded effectively. Higher amperage increases heat output, allowing for deeper and stronger welds. However, excessive amperage can lead to overheating and weld defects, such as warping or burn-through.
- Amperage Range for a 180 Amp MIG Welder:
- Lower amperage settings are suitable for thin materials like sheet metal.
- Higher amperage settings enable welding of thicker metals, up to 3/8 inch in a single pass for mild steel.
- Balancing Power and Precision: A 180 amp MIG welder offers enough power for most medium-duty tasks while maintaining ease of operation, making it an excellent choice for general fabrication and repair work.
- Adjusting Amperage for Materials: Proper settings depend on the metal type, thickness, and desired weld quality. Fine-tuning amperage ensures optimal penetration and minimal defects.
Advantages of MIG Welding with Controlled Amperage
- Efficiency: The continuous wire feed and fast welding speeds make MIG welding highly productive.
- Versatility: Suitable for a variety of metals and thicknesses, it adapts to diverse project requirements.
- Ease of Use: The straightforward setup and operation allow beginners to achieve professional-quality welds with minimal training.
- Consistent Results: Controlled amperage settings ensure uniform weld penetration and appearance.
This expanded understanding of MIG welding and amperage highlights why this method remains a favorite for both professionals and hobbyists alike.
What is MIG Welding?
MIG (Metal Inert Gas) welding is a process where a continuous wire electrode is fed through a welding gun, melting and joining the base materials. It’s known for its ease of use, speed, and versatility, making it ideal for a wide variety of applications, from automotive repairs to metal fabrication.
Role of Amperage in Welding
Amperage determines the amount of heat generated during welding, directly influencing penetration depth. Higher amperage allows for deeper penetration, enabling the welder to handle thicker materials. A 180 amp MIG welder strikes a balance between power and usability, making it suitable for medium-duty projects.
Thickness Capabilities of a 180 Amp MIG Welder
Single-Pass Welding in Detail
Single-pass welding with a 180 amp MIG welder is highly effective for mild steel up to 3/8 inch thick. The process offers:
- Efficiency: By completing the weld in one pass, the process minimizes time and energy expenditure, making it ideal for projects requiring speed.
- Quality: Single-pass welds produce clean joins with fewer chances of defects like slag inclusions or incomplete fusion.
- Material-Specific Adjustments:
- Aluminum: With its higher thermal conductivity, aluminum may require adjustments in travel speed and gas composition to maintain weld quality within the 1/4-inch range.
- Stainless Steel: Slightly lower thermal conductivity compared to mild steel allows welding up to 5/16 inch, but shielding gas composition (e.g., Argon/CO2 blends) plays a critical role.
Multi-Pass Welding Techniques
When welding materials thicker than 3/8 inch, multi-pass welding becomes necessary. Key aspects include:
- Layered Approach: Each pass builds upon the previous one, gradually increasing the weld’s depth and strength.
- Preparation and Execution: Proper edge preparation, such as beveling and cleaning, ensures better fusion between passes.
- Examples of Application:
- Fabricating heavy-duty equipment frames.
- Repairing thick structural steel components.
Material-Specific Capabilities Explored
- Mild Steel
- Up to 3/8 inch in a single pass, mild steel’s lower thermal conductivity makes it the most accommodating material for 180 amp MIG welders.
- Multi-pass welding extends capabilities up to 1/2 inch, depending on technique and joint design.
- Stainless Steel
- Achieving up to 5/16 inch in a single pass requires precise control of heat input and a stable arc.
- For thicker sections, multiple passes with a controlled interpass temperature prevent warping and maintain structural integrity.
- Aluminum
- Welding up to 1/4 inch in a single pass necessitates rapid travel speeds to counteract aluminum’s high heat dissipation.
- Multi-pass welding may be viable with preheating to reduce the required amperage and improve penetration.
Practical Considerations
- Shielding Gas: The choice of shielding gas affects the depth and quality of penetration. For example:
- Pure CO2: Offers deeper penetration but may increase spatter.
- Argon Blends: Preferred for stainless steel and aluminum for cleaner welds.
- Wire Selection: Wire diameter and composition must align with the material and thickness to optimize arc stability and deposition rate.
By understanding these capabilities and tailoring techniques to material properties, welders can maximize the performance of a 180 amp MIG welder across a variety of applications.
Wire Size and Type
The diameter and composition of the welding wire play a crucial role in determining penetration. Larger-diameter wires provide deeper penetration, making them suitable for thicker materials. The wire’s material (e.g., steel, aluminum) should also match the base metal for optimal results.
Shielding Gas
The shielding gas mixture affects weld quality and depth. Pure CO2 provides deeper penetration but may result in more spatter. Argon/CO2 blends are preferred for cleaner welds and better control, especially for stainless steel and aluminum.
Material Preparation
Clean, beveled edges on the metal ensure better penetration and a stronger weld. Removing rust, paint, or contaminants is essential for consistent performance.
Welding Technique
The angle of the welding gun, travel speed, and steady hand control all influence penetration depth. A slower travel speed allows for more heat input, which can improve weld quality on thicker materials.
Recommended Practices for Welding at 180 Amps
- Select the appropriate wire size and shielding gas combination for your material.
- Set the correct voltage and wire feed speed for the thickness being welded.
- Use proper joint preparation techniques, including beveling and cleaning.
- Employ multi-pass welding for thicker materials, ensuring consistent overlap and heat distribution.
Limitations and Alternative Approaches
Expanded Challenges with Thicker Materials
Welding thicker materials presents unique challenges that require careful preparation and adjustments to achieve successful results. These challenges include:
- Incomplete Penetration:
- Thicker materials require higher heat input for adequate penetration. With a 180 amp MIG welder, insufficient heat can lead to weak welds that do not fully fuse the base metals. This is especially problematic in structural or load-bearing applications.
- Mitigation: Proper edge preparation, such as grinding or beveling, combined with preheating, can help improve penetration.
- Heat Distortion:
- The concentrated heat during welding can cause the metal to warp or distort, particularly if the weld is not applied evenly or if excessive heat builds up.
- Mitigation: Using a staggered welding pattern or allowing cooling intervals between passes can minimize distortion. Clamping the workpiece securely also helps maintain alignment.
- Increased Risk of Cracking:
- Thicker materials are more prone to thermal stresses, which can result in cracking, especially in metals like stainless steel or aluminum.
- Mitigation: Controlled cooling and post-weld heat treatments, such as annealing, can relieve residual stresses and reduce cracking risk.
- Excessive Spatter:
- Working near the welder’s amperage limits may increase spatter, resulting in lower weld quality and more cleanup time.
- Mitigation: Fine-tuning the voltage and wire feed settings can help optimize arc stability and reduce spatter.
When using a 180 amp MIG welder, attempting to weld materials thicker than its optimal range can present several challenges:
- Incomplete Penetration: The welder may struggle to generate sufficient heat to fully fuse the joint, leading to weak or incomplete welds. This can compromise the structural integrity of the workpiece.
- Heat Distortion: Excessive heat from multiple passes may cause the metal to warp, especially in thinner sections surrounding the weld area.
- Increased Spatter: Lower penetration efficiency can result in excessive spatter, requiring more cleanup and reducing overall weld quality.
Mitigation Strategies
- Preheating:
- Preheating the base metal helps reduce the temperature difference between the arc and the workpiece, improving penetration.
- It also minimizes thermal stress and reduces the likelihood of cracking.
- Multi-Pass Techniques:
- Employing multiple weld passes allows for deeper penetration in thick materials. Proper edge preparation, such as beveling, ensures effective fusion between passes.
- Joint Design:
- Using designs like V-groove or U-groove joints helps concentrate heat and ensures better weld fusion in thicker sections.
Expanded Guidance on Upgrading or Adding Equipment
For projects requiring the welding of materials thicker than 1/2 inch, additional tools or techniques may be necessary:
- Higher-Amperage Welders:
- Upgrading to a welder with higher amperage output (e.g., 250 amps or more) provides the power needed for thicker materials, enabling better penetration and reducing the number of passes required. Alternative Welding Methods
- Stick Welding
- Ideal for heavy-duty applications, stick welding offers deeper penetration and works well on thicker materials.
- TIG Welding
- Provides precision and clean welds, especially for non-ferrous metals or projects requiring high-quality finishes.
- Submerged Arc Welding (SAW)
- For industrial-scale projects, SAW offers efficient and deep penetration for thick sections.
Complementary Techniques
- For industrial-scale projects, SAW offers efficient and deep penetration for thick sections.
- Preheating with an Oxy-Acetylene Torch: Ensures the metal reaches a consistent temperature before welding, aiding in penetration.
- Post-Weld Heat Treatment: Reduces residual stresses and minimizes distortion, particularly in critical structural applications.
By understanding and addressing these limitations, welders can achieve better results with a 180 amp MIG welder or determine when to explore alternative solutions to meet the demands of thicker material welding projects.
Challenges with Thicker Materials
Welding thicker materials with a 180 amp MIG welder can lead to issues like incomplete penetration or heat distortion if not done properly. These limitations can be mitigated with preheating or by using multiple passes.
When to Upgrade or Add Equipment
For projects involving materials thicker than 1/2 inch, consider upgrading to a higher-amperage welder or using alternative methods such as stick or TIG welding. Preheating the metal can also help improve penetration and reduce strain on the welder.
Conclusion
A 180 amp MIG welder is capable of welding materials up to 3/8 inch thick in a single pass and can handle thicker materials with multi-pass techniques. Factors such as wire size, shielding gas, material preparation, and welding technique all influence its performance. By understanding its capabilities and limitations, you can make the most of this versatile tool for a wide range of welding applications. For thicker projects, consider alternative welding methods or equipment upgrades to achieve the desired results.
Additional Resources
Get your welding gear here.
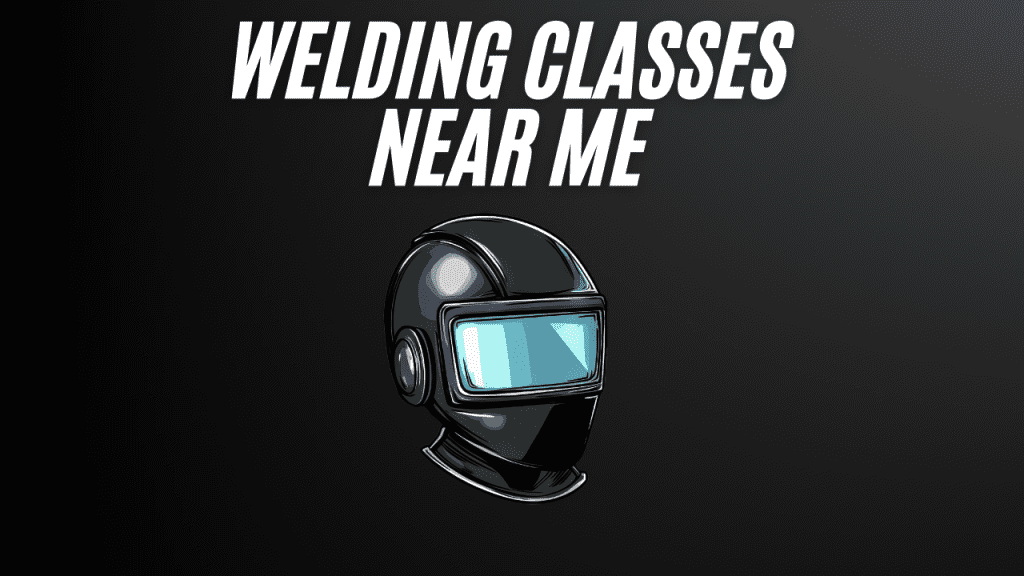