Table of Contents
How Big of a Generator Do I Need to Run a Welder?
Selecting the right generator to power your welder is critical for ensuring seamless performance and avoiding damage to your equipment. The size of the generator you need depends on several factors, including the welder’s input requirements, the type of welding you’ll be doing, and the generator’s specifications. This guide will help you determine the appropriate generator size for your needs.
Understanding Welder Power Requirements
To choose the right generator, it’s essential to understand the power requirements of your welder. Welders vary in their voltage and amperage needs, which directly affect their power consumption.
Voltage and Amperage
Most welders operate on either 120V or 240V power supplies. Some models are dual-voltage, allowing them to switch between the two depending on the task. Voltage determines the power flow to the welder, while amperage indicates the current it requires. Higher amperage means higher power demands, particularly when welding thicker materials or working on industrial-scale projects.
For example:
- A small 120V welder might require only 20 amps to function effectively, equating to 2400 watts.
- A larger 240V industrial welder can demand 30–50 amps or more, translating to 7200–12,000 watts.
Duty Cycle
The duty cycle of a welder refers to the percentage of time it can operate within a 10-minute period without overheating. A welder with a higher duty cycle will require more sustained power, placing a greater demand on the generator.
For instance:
- A welder with a 60% duty cycle at 200 amps must receive consistent, reliable power for extended periods.
- A generator unable to match this demand may result in overheating, frequent interruptions, or damage to the equipment.
Types of Welders and Their Requirements
Different types of welders have varying power needs based on their design, purpose, and the nature of the welding task. Understanding these differences is essential for selecting a generator that can meet your welder’s requirements effectively.
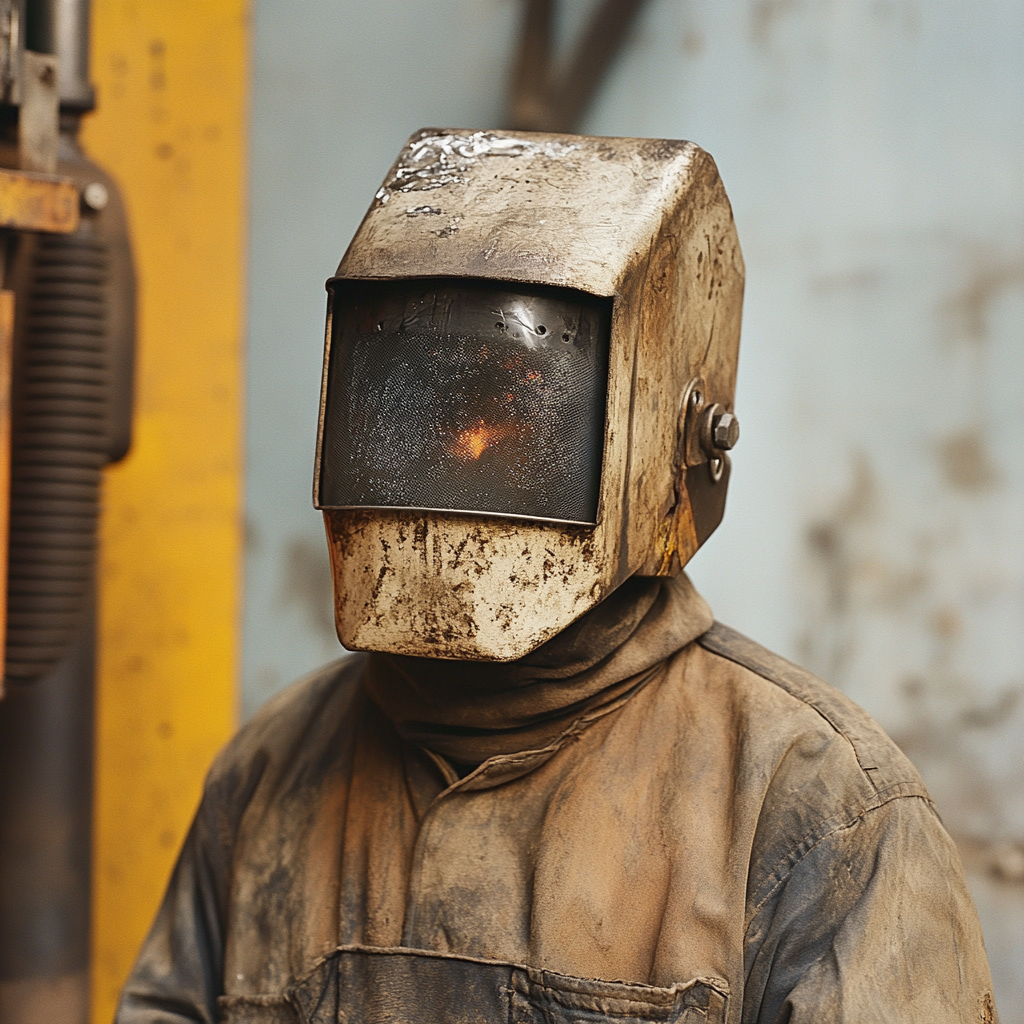
Stick Welders (SMAW)
Stick welders, also known as Shielded Metal Arc Welders (SMAW), are among the most rugged and versatile types of welders. They are widely used for heavy-duty tasks such as structural welding, construction, and repair work. These welders excel in outdoor environments and on thicker materials, where a strong, durable weld is required.
- Power Requirements: Stick welders require higher wattage because of the intense current needed to melt the electrode and sustain the arc. Generators providing 8000 watts or more are typically required for most stick welding applications. For larger stick welders with higher amperage needs (e.g., above 200 amps), you may need a generator with at least 10,000 watts.
- Duty Cycle Considerations: Stick welders often have demanding duty cycles, especially in industrial settings. A generator must be capable of delivering continuous power for prolonged periods without fluctuations.
- Application Versatility: Stick welders can handle a wide range of metals, including steel, stainless steel, and cast iron. They are particularly suitable for outdoor or windy conditions since the process is less affected by external factors.
MIG Welders (GMAW)
MIG welders, or Gas Metal Arc Welders (GMAW), are popular for their ease of use, speed, and ability to create clean, precise welds. They are often favored in automotive repair, manufacturing, and light to medium-duty fabrication tasks. MIG welding uses a continuous wire feed and shielding gas, making it suitable for a wide range of materials, including thin metals.
- Power Requirements: MIG welders have moderate power needs, generally ranging from 5000 to 10,000 watts, depending on the material thickness and welding intensity. For light-duty MIG welding, such as on thin sheet metal, a generator rated at 5000 watts may suffice. However, for heavy-duty applications, you’ll need a generator on the higher end of the spectrum.
- Startup Surges: Like all welders, MIG welders require additional wattage during startup. Ensure your generator’s surge capacity can handle this demand.
- Gas Dependency: Since MIG welding relies on shielding gas to protect the weld pool, a generator powering a MIG welder must also account for additional equipment, such as gas regulators or heaters.
- Versatility: MIG welders are well-suited for projects requiring clean, aesthetically pleasing welds, such as custom fabrication and bodywork.
TIG Welders (GTAW)
TIG welders, or Gas Tungsten Arc Welders (GTAW), are the most precise of the welding types. They are often used for applications requiring clean, high-quality welds on thinner materials like aluminum, stainless steel, and titanium. TIG welding provides unmatched control, making it ideal for delicate or artistic projects.
- Power Requirements: TIG welders are generally more energy-efficient compared to stick and MIG welders. They can operate effectively with smaller generators, particularly for light-duty tasks. For most TIG welders, a generator with a capacity of 4000 to 6000 watts is sufficient. For industrial TIG welding with high amperage requirements, consider a generator rated at 8000 watts or higher.
- Precision Welding: TIG welding is commonly used in aerospace, automotive, and manufacturing industries where precision is critical. The process requires a steady and consistent power supply to maintain an arc without fluctuations.
- Additional Equipment: TIG welding often requires accessories like foot pedals for amperage control and water-cooled torches. These additional components might slightly increase power demands.
- Low Duty Cycle Requirements: TIG welding typically involves shorter duty cycles, especially for intricate or low-amperage tasks, which can further reduce the generator’s workload.
Comparison of Power Needs Across Welding Types
Welder Type | Primary Applications | Wattage Range | Key Considerations |
---|---|---|---|
Stick (SMAW) | Structural welding, repair work | 8000–12,000+ watts | High wattage for heavy-duty tasks; excellent for outdoor and rugged environments. |
MIG (GMAW) | Automotive, light fabrication | 5000–10,000 watts | Moderate wattage; clean welds for thin to medium materials; requires additional power for gas systems. |
TIG (GTAW) | Precision work, thin materials | 4000–8000+ watts | Energy-efficient; precise welds for delicate projects; additional equipment may slightly increase demand. |
By understanding the unique power requirements and characteristics of each welding type, you can ensure that your generator is appropriately matched to your specific welding needs.
Generator Wattage Basics
Generator Wattage Basics
Choosing the correct generator wattage is essential for ensuring reliable performance and protecting both your generator and welder from potential damage. Generators are rated based on two critical metrics—rated wattage and surge wattage—and understanding these is key to making an informed decision.
Rated vs. Surge Wattage
Generators have two primary wattage ratings.
- Rated Wattage (Continuous Power) is the amount of power a generator can deliver consistently over an extended period. Rated wattage ensures that all equipment connected to the generator operates without interruption. For welders, this is the power required during normal operation.
- Surge Wattage (Peak Power) refers to the additional power a generator can provide momentarily, typically for startup surges. Welders, like other electrical equipment, often require an initial burst of energy to initiate the welding arc. This surge can exceed the welder’s operating wattage by 30–50%.
For example:
- A welder operating at 3000 watts may need up to 5000 watts during startup.
- If the generator cannot handle this temporary surge, it may trip the circuit breaker, cause voltage fluctuations, or fail to start the welder altogether.
Selecting a generator that matches both the rated and surge wattage requirements of your welder ensures smooth operation. Always check the welder’s manual or specifications for these values.
What Happens If Surge Requirements Are Overlooked
- Generator Overload can damage internal components and shorten the generator’s lifespan.
- Welder Malfunction occurs when insufficient power leads to weak or inconsistent welds.
- Circuit Breaker Trips may happen frequently if the generator’s surge capacity is inadequate.
To avoid these issues, choose a generator with surge wattage at least 25–30% higher than the welder’s rated wattage.
General Wattage Guidelines
When selecting a generator for your welder, the voltage and amperage of the welder play a significant role in determining the required wattage. Below are general guidelines based on welder specifications.
- 120V Welders
- Typically used for light-duty tasks, such as home repairs or hobby projects.
- Generators with a rated output of 5000 to 7000 watts are sufficient for most 120V welders. This provides enough capacity for both operation and startup surges.
- 240V Welders
- Designed for more demanding tasks, 240V welders are common in industrial, construction, and automotive applications.
- These welders require generators rated between 8000 and 12,000 watts, depending on the welder’s amperage and the type of welding being performed.
Breaking Down Wattage Needs by Welder Type
- Light-Duty Welders (120V)
- Usually draw less current and are designed for thin materials and DIY projects.
- A generator rated at 5000–6000 watts is typically enough to handle operation and startup requirements.
- Example: A 120V welder drawing 20 amps needs 2400 watts during operation, but with a 30% surge allowance, a 5000-watt generator is ideal.
- Medium-Duty Welders (120V or 240V)
- Used for tasks such as automotive repairs or moderate fabrication, these welders may demand higher wattage.
- A generator with a capacity of 7000–10,000 watts is usually sufficient.
- Heavy-Duty Welders (240V)
- High-amperage welders used in industrial or structural projects often require robust generators.
- These welders can draw 30–50 amps or more, necessitating a generator rated at 10,000–12,000 watts or higher.
Factors That Affect Wattage Requirements
- Material Thickness
- Welding thicker materials typically requires higher amperage, increasing power needs.
- Type of Welding Process
- Different welding types (stick, MIG, TIG) have varying power demands. For example, stick welding often requires higher wattage than TIG welding.
- Accessories and Tools
- If you use additional equipment like grinders, lighting, or ventilation fans alongside the welder, you’ll need to account for their wattage as well.
Planning for Additional Power Needs
When calculating generator wattage requirements, start with the welder’s rated wattage and add an additional 25–30% for startup surges. Factor in any other tools or accessories you may use simultaneously. Consider future needs—if you plan to upgrade your welder or use other high-power tools, it’s wise to choose a generator with extra capacity.
By carefully evaluating both rated and surge wattage requirements, you can select a generator that ensures your welder performs efficiently and reliably, whether for hobby projects or industrial applications.
Calculating Generator Size for Your Welder
To ensure the generator meets your needs, calculate its size based on your welder’s requirements:
- Determine Voltage and Amperage:
- Locate this information on the welder’s manual or nameplate.
- Example: A 120V welder drawing 20 amps requires 2400 watts (120V × 20A).
- Account for Surge Requirements:
- Add 25–30% overhead to the calculated wattage to accommodate surges.
- Example: For a 2400-watt welder, select a generator rated at ~3000 watts minimum.
- Consider Additional Equipment:
- If you’re using tools like grinders, lights, or fans, factor their power needs into the total wattage.
Example Calculations
- 120V Welder
- Operating Wattage: 2400 watts (120V × 20A).
- Recommended Generator Size: 5000 watts (to allow for surges and additional equipment).
- 240V Welder
- Operating Wattage: 7200 watts (240V × 30A).
- Recommended Generator Size: 8000–10,000 watts.
Factors to Consider When Choosing a Generator
Selecting the right generator for your welder involves more than just matching the power output. Key factors like the type of generator, portability, noise levels, fuel efficiency, and runtime play crucial roles in determining which generator is best suited for your needs.
Type of Generator
The type of generator you choose can significantly impact performance, efficiency, and compatibility with your welding equipment. The two main types are conventional generators and inverter generators.
- Conventional Generators
- These are high-output models designed to handle heavy-duty tasks and provide robust power, making them suitable for large, industrial welders or environments where high wattage is needed.
- Conventional generators are often less expensive than inverter models and can easily meet the power requirements of stick and MIG welders.
- Drawback: They produce “dirty” power, characterized by fluctuations in voltage and frequency, which can damage sensitive electronics in modern welders. This is especially important for TIG welders or advanced machines with digital controls.
- Conventional generators are bulkier and tend to consume more fuel compared to inverter models.
- Inverter Generators
- These generators deliver clean, stable power by using advanced electronics to regulate voltage and frequency. This makes them ideal for modern welders with electronic components and delicate circuits.
- Inverter generators are lightweight, compact, and portable, making them a great choice for remote welding projects or situations requiring frequent transportation.
- They are more fuel-efficient and quieter than conventional generators, reducing operational costs and noise pollution.
- Drawback: They typically have lower power capacities and may not be suitable for high-amperage welders unless paired with a high-end model.
Portability and Noise
These factors are especially important for welders who work in multiple locations or in environments where noise levels must be minimized.
- Portability
- If you’ll be welding in remote or hard-to-reach areas, a lightweight and portable generator is essential.
- Features such as wheels, foldable handles, and compact designs make it easier to transport and set up the generator on job sites.
- Inverter generators are generally more portable than conventional models due to their lighter construction.
- Noise
- Conventional generators tend to be louder, often exceeding 70–80 decibels, which can be disruptive in residential or urban settings.
- Inverter generators are designed with noise-reduction technology and typically operate at 50–60 decibels, making them a quieter and more neighbor-friendly option.
- If noise is a concern, look for generators with enclosures or mufflers to further reduce sound levels.
Fuel Efficiency and Runtime
The generator’s fuel efficiency and runtime determine how long it can power your welder without interruption. This is especially important for long welding sessions or job sites where refueling may be inconvenient.
- Fuel Efficiency
- Inverter generators are more fuel-efficient due to their ability to adjust engine speed based on power demand. This reduces fuel consumption and minimizes operating costs.
- Conventional generators run at a constant speed regardless of load, leading to higher fuel usage.
- Runtime
- For extended welding projects, choose a generator with a large fuel tank or one that offers excellent fuel economy. A generator with a longer runtime reduces the need for frequent refueling and improves productivity.
- Diesel Generators: Diesel models are generally more fuel-efficient than gasoline generators and are better suited for industrial use. They offer longer runtimes and greater durability, making them a good choice for high-demand tasks.
Additional Considerations
- Durability and Build Quality
- If your generator will be exposed to harsh environments or heavy use, choose a model with a durable frame and protective casing to prevent damage.
- Maintenance
- Inverter generators typically require less maintenance than conventional models due to their advanced design. However, regular checks of oil levels, air filters, and spark plugs are essential for any generator.
- Power Outlets and Compatibility
- Ensure the generator has the correct type and number of outlets to match your welder’s plug and any additional equipment you plan to use. Some generators come with dual-voltage options (120V and 240V), providing greater versatility.
When choosing a generator for your welder, consider the type of generator that best suits your welding tasks. Inverter generators are ideal for portability, quiet operation, and compatibility with modern welders, while conventional generators are better for heavy-duty, high-output needs. Additionally, evaluate fuel efficiency, runtime, and noise levels to ensure the generator meets the demands of your projects. Taking the time to assess these factors will help you make an informed choice and ensure reliable, efficient welding operations.
Recommended Generator Sizes for Common Welding Applications
Selecting the right generator size depends on the specific welding application, as different types of tasks require varying levels of power. Here’s a closer look at the generator sizes suitable for light-duty, medium-duty, and heavy-duty welding needs.
Light-Duty Welders
Light-duty welders are typically 120V models used for smaller-scale projects such as hobby work, DIY tasks, or minor home repairs. These welders are designed to handle thinner materials like sheet metal or aluminum, making them ideal for beginners or occasional users.
- Power Needs: These welders usually draw between 20 to 50 amps, requiring an operating wattage of 2000 to 4000 watts. However, startup surges may push the power demand closer to 5000 watts, necessitating a generator with extra capacity.
- Applications: Common uses include repairing small items, creating art pieces, or performing basic fabrication tasks. They are often used in home garages or workshops where heavy-duty performance isn’t required.
- Generator Size: A generator rated at 5000–6000 watts is sufficient to power light-duty welders, ensuring smooth operation and startup without risking overload.
- Why This Size Works: This range provides enough capacity for the welder and additional tools like grinders, lights, or fans, which are often used alongside the welder.
Medium-Duty Welders
Medium-duty welders are commonly used for tasks that require more power, such as automotive repairs, construction work, or moderate fabrication projects. These welders are often dual-voltage models capable of operating on both 120V and 240V power supplies, giving them more versatility for a wider range of applications.
- Power Needs: Medium-duty welders typically draw 30 to 80 amps, with an operating wattage ranging from 4000 to 7000 watts. Surge requirements can exceed 8000 watts, especially when welding thicker materials or working at higher amperages.
- Applications: These welders are suitable for tasks such as repairing vehicle frames, fabricating structural components, or building equipment. They are often used in professional workshops or on construction sites where durability and performance are essential.
- Generator Size: A generator rated at 7000–9000 watts is ideal for medium-duty welders. This range accommodates both the welder’s operational needs and startup surges while leaving some overhead for additional equipment.
- Why This Size Works: Medium-duty tasks often require tools like cutting torches, ventilation systems, or compressors, all of which can increase the overall power demand. A 7000–9000-watt generator ensures sufficient power for these extras.
Heavy-Duty Welders
Heavy-duty welders are high-amperage machines designed for industrial-scale applications or structural welding projects. They are typically 240V models capable of delivering significant power for welding thick materials like steel beams, pipelines, or large machinery.
- Power Needs: Heavy-duty welders often draw 80 to 150 amps or more, with operating wattage requirements starting around 8000 watts and surging well beyond 10,000 watts. Continuous operation at high amperage levels places substantial demands on the generator.
- Applications: These welders are used for projects like constructing bridges, welding industrial equipment, or performing large-scale repairs. They are essential for professional welders working in shipyards, factories, or on major construction sites.
- Generator Size: A generator rated at 10,000–12,000+ watts is necessary for heavy-duty welders. For extremely high-power welders or jobs requiring additional tools, even larger generators may be required.
- Why This Size Works: Industrial projects often involve multiple pieces of equipment running simultaneously, such as plasma cutters, fans, or auxiliary lighting. A generator in this range provides ample power for the welder and any additional gear.
Additional Considerations for Generator Sizing
When selecting a generator for your welding needs, it’s important to think beyond the immediate wattage requirements of your equipment. Factors like buffer capacity, versatility, and future expansion can make a significant difference in your generator’s overall performance and usability. Here’s a detailed look at these considerations.
Buffer Capacity
- Why Buffer Capacity Matters: Generators often need to handle more than the steady operational wattage of a welder. Startup surges, which occur when the welder first initiates the arc, can require 25–50% more power than normal operation. Additionally, if you’re using other tools or equipment simultaneously, such as grinders, lights, or fans, these can add to the total power draw.
- Recommended Buffer: To avoid overloading the generator, choose a model with 25–30% more capacity than the welder’s operational wattage. For example, if your welder requires 5000 watts to run, select a generator rated at least 6500 watts to accommodate surges and auxiliary devices.
- Benefits
- Prevents generator overload, which can damage both the generator and connected equipment.
- Ensures smooth, uninterrupted operation even during power spikes.
- Provides flexibility for unexpected additional power needs.
Versatility
- Dual-Voltage Options: Welders can vary in their voltage requirements, with many smaller models operating on 120V and larger, more industrial machines requiring 240V. Some welders are dual-voltage, meaning they can switch between 120V and 240V based on the task. A generator with dual-voltage capabilities allows you to use a wide range of welding machines and tools without needing multiple generators.
- Support for Other Tools: Beyond welding, you might need power for accessories such as:
- Angle grinders for finishing welds.
- Air compressors for pneumatic tools.
- Plasma cutters for precision cutting.
- Worksite lighting or ventilation systems.
- A versatile generator with sufficient outlets and wattage ensures compatibility with all your tools, making it a multipurpose solution.
- Portability and Use in Different Environments: If you work across various job sites or tackle a variety of projects, versatility becomes even more critical. Choose a generator that is easy to transport, durable, and adaptable to different tasks.
Future Expansion
- Anticipating Growth: If you plan to upgrade your welder to a higher-capacity model or take on larger projects in the future, it’s wise to invest in a generator that can handle increased power demands. Upgrading your generator later can be more costly and inconvenient than buying a higher-capacity model upfront.
- Catering to Industrial Needs: For those moving into industrial-scale welding, a generator rated at 10,000–12,000+ watts may be necessary. Opting for a generator with room to grow ensures you won’t need to replace your equipment as your needs expand.
- Flexibility for Non-Welding Applications: A high-capacity generator can also be used for other tasks, such as powering a workshop, backup power for a home or business, or running multiple tools simultaneously. This added utility enhances the generator’s value over time.
Practical Tips for Selecting the Right Generator
- Check Manufacturer Specifications: Always refer to your welder’s manual to determine its exact power requirements, including operational and surge wattage.
- Plan for Simultaneous Use: If you often run multiple tools or accessories alongside the welder, calculate their combined power requirements to avoid overloading the generator.
- Test for Real-World Scenarios: Whenever possible, test the generator with your equipment to ensure it performs reliably under load.
By factoring in buffer capacity, versatility, and future expansion, you can select a generator that not only meets your current welding needs but also adapts to your evolving projects and tools. A well-chosen generator ensures reliable, efficient, and safe operation while providing long-term value and flexibility.
Tips for Using a Generator with a Welder
Operating a generator with a welder requires careful attention to safety, compatibility, and maintenance to ensure smooth performance and protect your equipment. Here’s a detailed guide on best practices and common pitfalls to avoid.
Ensure Proper Grounding
- Why Grounding Matters: Grounding a generator reduces the risk of electrical shock, protects against power surges, and ensures the generator operates safely. Without proper grounding, stray currents can damage equipment or pose a safety hazard to the operator.
- How to Ground the Generator: Follow the manufacturer’s instructions, which typically involve connecting a grounding wire to the generator’s grounding terminal and securing it to a metal rod driven into the earth.
- Additional Tips: For portable generators used in remote locations, carry a grounding rod and clamp to ensure proper grounding wherever you set up.
Use Quality Extension Cords
- Importance of Heavy-Duty Cords: Using extension cords that are not rated for the welder’s voltage and amperage can lead to power loss, overheating, and even fire hazards.
- What to Look For: Choose cords labeled as “heavy-duty” or “industrial-grade” with ratings that meet or exceed the welder’s power requirements. Look for cords with thick insulation and high AWG (American Wire Gauge) ratings.
- Cord Length and Gauge: Minimize cord length whenever possible, as longer cords increase resistance and power loss. For higher amperage welders, use a lower-gauge cord (e.g., 10-gauge or thicker).
Regular Maintenance
- Why Maintenance Is Critical: Generators that are not properly maintained can suffer from decreased efficiency, unexpected breakdowns, and shorter lifespans. Regular maintenance ensures the generator delivers consistent power and operates safely.
- Maintenance Checklist:
- Check and replace engine oil as recommended by the manufacturer.
- Clean or replace air filters to prevent clogging and maintain proper airflow.
- Inspect and replace spark plugs if they show signs of wear.
- Test the generator periodically, especially if it has been idle for an extended period.
- Keep the generator clean and free of debris, which can cause overheating.
Match the Generator to the Environment
- Outdoor Use: For welding in outdoor or remote locations, choose a generator designed to handle environmental challenges such as rain, dust, or extreme temperatures. Look for weatherproof or enclosed models.
- Protective Covers: If your generator is not weatherproof, use a protective cover or shelter to shield it from rain, snow, and direct sunlight while maintaining proper ventilation.
- Noise Considerations: In residential or noise-sensitive areas, opt for a generator with noise-dampening features or use sound barriers to reduce disturbance.
Common Mistakes to Avoid
Avoiding these common mistakes can save you time, money, and potential damage to your equipment.
Undersizing the Generator
- The Problem: Using a generator with insufficient power can lead to frequent interruptions, poor weld quality, and damage to both the generator and the welder.
- Solution: Always calculate your welder’s operational and surge wattage requirements and select a generator with at least 25–30% additional capacity to handle startup surges and auxiliary tools.
Overlooking Surge Wattage
- The Problem: Failing to account for the welder’s higher power demand during startup can overload the generator, causing it to trip circuit breakers or fail to start the equipment.
- Solution: Choose a generator with surge wattage rated at least 30% higher than the welder’s steady-state wattage.
Ignoring Compatibility
- The Problem: Connecting a welder to a generator with mismatched voltage or amperage can damage the welder’s internal components and reduce its lifespan.
- Solution: Check your welder’s specifications and ensure the generator matches its voltage (e.g., 120V or 240V) and amperage requirements. Use adapters or voltage selectors only if they are explicitly supported by the equipment.
Neglecting Regular Testing
- The Problem: Generators that sit idle for long periods without testing or maintenance may fail when needed.
- Solution: Run the generator periodically, even when not in use, to ensure it remains in working condition. Test it with your welder to verify compatibility and performance.
Overloading the Generator with Additional Equipment
- The Problem: Adding multiple tools or devices to the generator’s output without accounting for their combined power draw can exceed the generator’s capacity.
- Solution: Create a power budget for all equipment connected to the generator and ensure the total wattage stays within the generator’s rated capacity.
By following these tips and avoiding common mistakes, you can ensure safe, efficient, and reliable operation of your generator and welder, whether you’re working on a small DIY project or a large-scale industrial task.
Conclusion
The size of the generator you need to run a welder depends on your specific equipment and use case. By understanding your welder’s power requirements, calculating the necessary wattage, and considering factors like portability, fuel efficiency, and generator type, you can make an informed choice. A properly sized generator ensures efficient, safe, and uninterrupted welding operations, whether for hobby projects or industrial applications. Always consult your welder’s manual and, if needed, seek expert advice to ensure compatibility and optimal performance.
Additional Resources
Get your welding gear here.
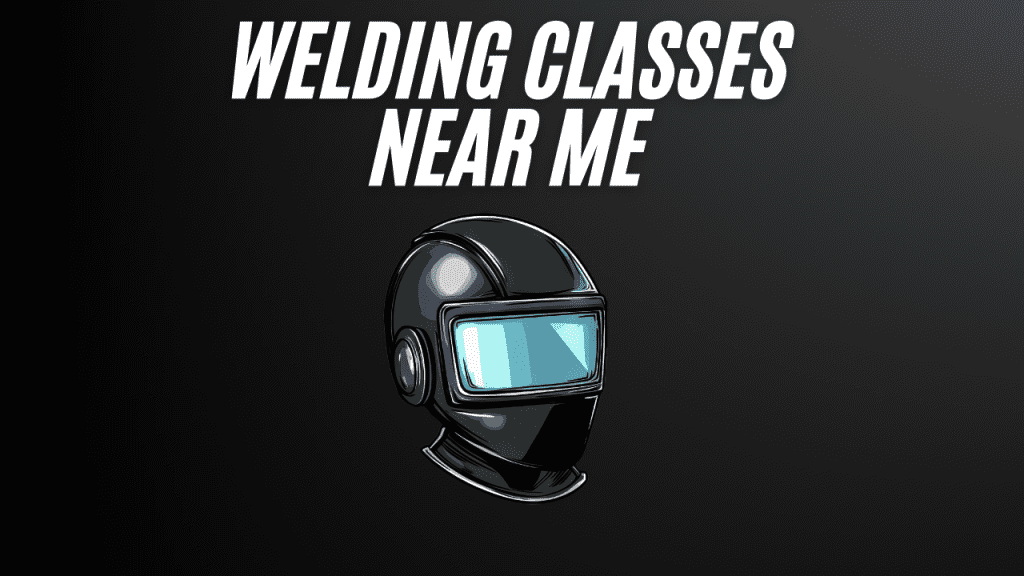