Table of Contents
Welding Through The Ages: A Brief History of Welding
Welding is the process of joining metal pieces together through the application of heat and pressure, creating functional pieces of art and durable tools. Its history dates back to 4000 B.C., showcasing humanity’s ingenuity and the evolution of metalworking technologies over millennia.
Known History of Welding in B.C.
Developments in 4000 B.C.
This period marks the earliest traces of welding, where civilizations began transitioning from copper to iron for toolmaking and artistic purposes. The shift from copper, which was widely used for simple tools and ornamental items, to iron represented a significant technological leap. Iron’s superior strength and availability made it more practical for crafting durable tools, weapons, and structures.
The Role of Copper in Early History of Welding
Copper, one of the first metals used by humans, was primarily employed for decorative items and basic tools. Artifacts such as jewelry, ceremonial masks, and small statues from this period often show evidence of primitive joining techniques, including brazing and hammering. For example, archaeological finds in Mesopotamia have revealed copper tools and ornaments that were joined using early heating and pressure techniques.
Transition to Iron
Iron’s adoption during this era revolutionized metalworking. Unlike copper, iron required higher temperatures to work with, leading to the development of rudimentary forge welding techniques. Early smiths would heat iron in charcoal furnaces until it became malleable, then hammer pieces together to create functional items. Examples include:
- Tools: Archaeological evidence from ancient Anatolia (modern-day Turkey) includes iron chisels and plows, demonstrating early forge welding used to combine and shape iron.
- Weapons: Iron spearheads and arrowheads, found in early settlements in the Middle East, illustrate the application of welding techniques to improve durability and performance.
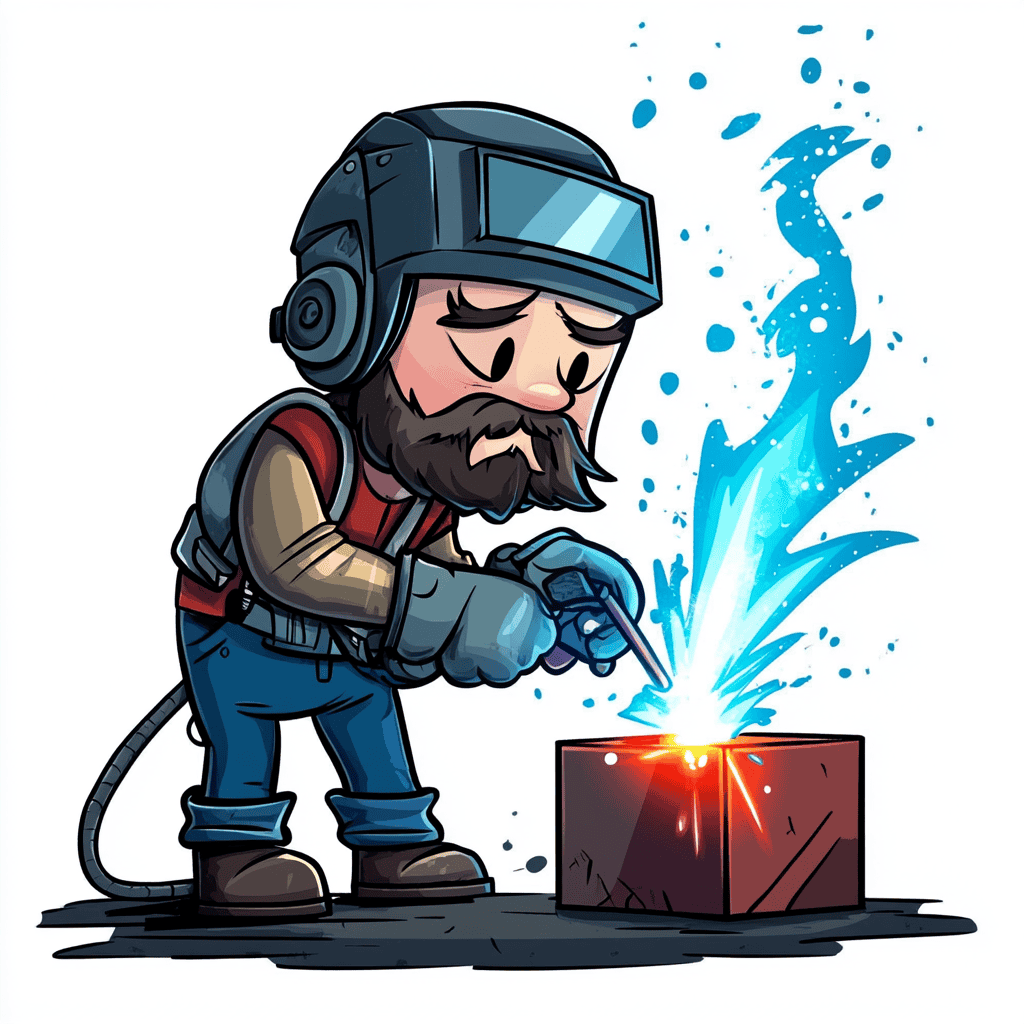
Forging Early Alloys
The understanding of metals advanced significantly during this period. Experimentation with combining copper and tin led to the creation of bronze, a superior alloy that marked the beginning of the Bronze Age. Though not welding in the modern sense, these experiments paved the way for more sophisticated metal-joining techniques:
- Bronze Artifacts: Early bronze swords and shields, found in ancient Mesopotamia and Egypt, were often shaped and reinforced using heat and hammering methods.
- Decorative Items: Ornamental bowls and figurines made of bronze and adorned with welded joints have been discovered in archaeological digs.
Advances in Heat Sources
To work with iron and later alloys, ancient civilizations began developing more efficient heat sources:
- Charcoal Furnaces: By increasing airflow with bellows, early smiths were able to achieve the higher temperatures necessary for working with iron.
- Kilns: Some early kilns were adapted to smelt and refine metals, setting the stage for more controlled metalworking processes.
Laying the Groundwork for Future Techniques
These developments during 4000 B.C. not only advanced the tools and weapons of the era but also laid the groundwork for innovations in welding. The rudimentary forge welding techniques of heating and hammering metals together were refined over time, evolving into more complex methods as civilizations learned to manipulate heat and pressure with greater precision.
This era was a turning point in human ingenuity, demonstrating the potential of metal as both a functional and artistic medium. The experimentation and discoveries made during this time became the foundation for the sophisticated welding practices we see today.
Developments in 3500 B.C.
The discovery of tin around 3500 B.C. marked a significant milestone in the history of metallurgy. Tin’s unique properties transformed the way ancient civilizations worked with metals, particularly through its role in creating bronze, a groundbreaking alloy that significantly surpassed copper in durability, hardness, and versatility.
The Role of Tin in Bronze Production
Bronze is an alloy made by combining copper and tin, typically in a ratio of 9:1. The addition of tin to copper addressed some of the limitations of pure copper, such as its softness and susceptibility to wear. Bronze became a preferred material for tools, weapons, and decorative items due to its superior properties:
- Durability: Bronze was harder and more resistant to corrosion than copper, making it ideal for long-lasting tools and weaponry.
- Malleability: The alloy was easier to cast into complex shapes, allowing for more intricate designs in both functional and artistic objects.
Early Uses of Bronze
With the advent of bronze, civilizations began producing items that were stronger, more effective, and often more ornate than their copper predecessors. Examples of early uses include:
- Tools: Bronze axes, chisels, and saws were more efficient and durable, revolutionizing construction and craftsmanship in ancient Mesopotamia and Egypt.
- Weapons: Bronze spearheads, swords, and shields became the standard in warfare, offering superior performance compared to copper-based weapons.
- Art and Ornaments: Bronze was used for statues, figurines, and ceremonial objects, many of which have been unearthed in archaeological excavations in Mesopotamia, the Indus Valley, and China.
Impact on Trade and Society
The discovery of tin and the production of bronze had profound societal and economic implications:
- Expansion of Trade Networks: Tin deposits were less common than copper, requiring long-distance trade to secure supplies. Early trade routes connecting regions rich in tin (such as modern-day Afghanistan and Cornwall in England) with copper-producing areas were established, fostering cultural and economic exchanges.
- Specialization of Labor: The complexity of alloy production led to the rise of specialized metalworkers, who became highly respected members of their communities.
- Advancements in Technology: The use of bronze spurred innovations in smelting and casting techniques, which were critical for large-scale production.
Archaeological Evidence
Artifacts from this period provide tangible evidence of tin’s impact on metallurgy:
- Bronze Tools: Excavations in Mesopotamia and Anatolia have revealed early bronze tools, such as hammers and sickles, that demonstrate advanced casting and finishing techniques.
- Weapons: Sites in ancient Egypt and the Indus Valley have yielded bronze daggers and axes, often elaborately decorated, indicating both functional and ceremonial uses.
- Bronze Artifacts: Items such as mirrors, bowls, and figurines found in tombs highlight the dual purpose of bronze in both daily life and religious or cultural practices.
The Legacy of Tin and Bronze
The development of bronze technology not only transformed metallurgy but also marked the beginning of the Bronze Age, a defining era in human history. This period saw the rise of complex societies and the construction of monumental structures, as bronze tools and weapons enabled more ambitious projects and conquests.
The discovery of tin and its application in alloying with copper laid the foundation for future advancements in metalworking, including the eventual transition to iron and steel. Its significance in the evolution of welding and metallurgy cannot be overstated, as it represents one of humanity’s earliest forays into material science and innovation.
Developments in 3000 B.C.
The period around 3000 B.C. was pivotal in the evolution of metalworking techniques, as civilizations began experimenting with more advanced methods of joining and shaping metals. Notable innovations during this time included the Sumerians’ use of hard soldering, the Egyptians’ development of pressure welding, and the early examples of brazing seen in artifacts like the golden goblet found in Queen Pu-abi’s tomb.
The Sumerians and Hard Soldering
The Sumerians, known for their advanced city-states and innovations in Mesopotamia, used hard soldering techniques to create swords. This process involved using a metal alloy with a higher melting point to join pieces of metal together, ensuring a strong and durable bond. Examples of their work demonstrate:
- Weapon Crafting: Hard soldering was used to attach blades to handles or strengthen decorative elements on swords. These techniques improved the functionality and aesthetics of their weaponry.
- Cultural Impact: The durability of hard-soldered items made them essential in both warfare and ceremonial displays, showcasing the Sumerians’ metallurgical expertise.
Egyptians and Pressure Welding
The Egyptians pioneered pressure welding, a method that involved heating iron ore using charcoal to produce sponge iron, which was then hammered into tools and weapons. This process marks one of the earliest instances of welding techniques being applied to functional items.
- Sponge Iron Production: The Egyptians used charcoal-fired furnaces to achieve the high temperatures required to reduce iron ore into sponge iron, a porous and malleable form of metal.
- Hammer Welding: Once heated, the iron particles were hammered together to form solid tools and weapons, such as sickles, chisels, and daggers.
- Advances in Metalworking: Pressure welding laid the foundation for later advancements in forging and blacksmithing, critical for the production of durable metal goods.
Early Brazing Techniques: Queen Pu-abi’s Golden Goblet
The discovery of a golden goblet with a braze fillet in the tomb of Queen Pu-abi, a Sumerian royal figure, provides one of the earliest examples of brazing as a metal-joining technique.
- Artifact Details: The goblet features a smooth, polished surface with joints created through brazing, where a filler metal with a lower melting point was used to bond the pieces together.
- Significance of Brazing: This technique allowed for the creation of complex and intricate designs, enhancing the aesthetic and functional properties of metal items.
- Cultural Context: Such artifacts highlight the Sumerians’ advanced craftsmanship and their use of metalwork for ceremonial and decorative purposes.
Broader Implications of These Developments
The techniques developed during 3000 B.C. not only advanced the functional applications of metalworking but also reflected the growing sophistication of early civilizations:
- Innovations in Weaponry: The ability to create stronger and more reliable weapons gave civilizations like the Sumerians and Egyptians a strategic advantage in conflicts.
- Cultural Legacy: Decorative and ceremonial items, such as Queen Pu-abi’s goblet, demonstrate the integration of metalworking into religious and social practices.
- Foundation for Future Methods: Techniques like hard soldering, pressure welding, and brazing provided the groundwork for the complex welding processes that would emerge in later centuries.
The advancements made during this period highlight the ingenuity and resourcefulness of early metalworkers, whose innovations have left an enduring impact on the history of welding and metallurgy.
Developments in 2250 B.C.
By 2250 B.C., the Persians demonstrated remarkable advancements in material manipulation through their use of cobalt to color glass. This innovation not only showcased their understanding of chemical processes but also reflected the growing sophistication of craftsmanship and artistic expression during this period.
The Use of Cobalt in Glass Coloring
Cobalt, a naturally occurring element, was discovered to produce vibrant blue hues when added to glass during the melting process. This discovery represented a significant leap in material science and artistic techniques:
- Chemical Properties of Cobalt: The inclusion of cobalt compounds, such as cobalt oxide, during the glass-making process caused chemical reactions that created striking blue tones, which were prized for their beauty and rarity.
- Techniques: Glassmakers would finely grind cobalt-containing minerals and mix them with silica and other materials before subjecting the mixture to high temperatures in kilns. The resulting colored glass could be shaped into beads, vessels, and decorative items.
Applications of Cobalt-Colored Glass
The vibrant blue glass created with cobalt became a highly sought-after material for both functional and decorative purposes:
- Jewelry and Beads: Small, intricately shaped beads were often used in necklaces, bracelets, and other adornments, signifying wealth and status.
- Ceremonial Items: Colored glass was used in religious and ceremonial contexts, with pieces crafted into vessels or inlays for ornate artifacts.
- Trade and Prestige: The unique cobalt-blue glass was traded across regions, elevating Persia’s influence in the ancient world and establishing it as a center of innovation.
Significance in Material Manipulation
The use of cobalt in glass coloring demonstrated the Persians’ advanced understanding of material properties and their ability to harness natural resources for creative expression:
- Chemical Innovation: The ability to achieve consistent and vivid colors indicated a sophisticated knowledge of chemical reactions and kiln technology.
- Cultural Impact: The vibrant blue glass became symbolic of wealth, artistry, and technological prowess, playing a prominent role in the art and culture of the time.
Influence on Future Developments
The techniques developed by the Persians in 2250 B.C. laid the groundwork for future advancements in glassmaking and material sciences:
- Expansion of Color Palettes: The successful use of cobalt inspired experiments with other minerals and compounds to create a broader range of colors in glass and ceramics.
- Legacy in Art: The methods pioneered by the Persians influenced subsequent civilizations, such as the Egyptians and Romans, who adopted and refined glass-coloring techniques.
- Early Chemistry Foundations: This period marked one of the earliest documented uses of chemistry to manipulate materials, a practice that would evolve into more complex metallurgical and welding processes.
The Persian innovation of using cobalt to color glass was more than a technical achievement; it was a reflection of their ability to blend science and art, leaving a lasting legacy in craftsmanship and material manipulation.
Developments in 1500 B.C.
The period around 1500 B.C. saw two significant advancements in history of welding: the discovery of mercury and the widespread adoption of iron smelting. These breakthroughs were pivotal in shaping early metallurgy, toolmaking, and weapon production, laying the groundwork for future technological advancements.
Discovery of Mercury
Mercury, a rare metal unique for its liquid state at room temperature, was discovered during this time. Its properties made it an essential material for early civilizations.
Chemical Properties
Mercury’s ability to amalgamate with other metals, such as gold and silver, revolutionized ore refining through the amalgamation process.
This technique enabled more efficient extraction of precious metals, advancing mining technologies.
Cultural and Medicinal Use
Mercury appeared in rituals and early medical practices. For instance, Egyptian and Mesopotamian texts mention mercury as both a mystical substance and a treatment for ailments, though its toxic effects were not yet understood.
Symbolic Significance
Due to its liquid state and rarity, mercury was often associated with alchemy and mysticism, symbolizing transformation and fluidity.
Iron Smelting Becomes Widespread
The increased prevalence of iron smelting in 1500 B.C. marked a turning point from the Bronze Age to the Iron Age, driven by iron’s superior qualities and availability.
Technological Advancements
Early smelting techniques involved charcoal-fired furnaces to separate iron from its ore.
The introduction of bellows increased airflow, allowing higher furnace temperatures and greater smelting efficiency.
Applications
- Tools: Durable iron tools, such as axes, plows, and sickles, improved agricultural and construction capabilities.
- Weapons: Iron swords, spears, and shields replaced bronze weapons, offering superior strength and durability in combat.
Economic and Cultural Impact
Iron’s widespread availability fueled trade networks, as communities sought raw materials and finished goods.
Societies that mastered iron smelting gained significant technological and military advantages, influencing the balance of power in the ancient world.
Broader Implications
These advancements in 1500 B.C. profoundly influenced material manipulation and resource utilization:
- Innovation in Metallurgy: Mercury amalgamation reflected early strides in chemical metallurgy, paving the way for future refining processes.
- Transition to the Iron Age: The proliferation of iron smelting marked a transformative era, driving economic and technological progress.
- Legacy in Welding and Material Science: The ability to work with iron and mercury contributed to the evolution of welding processes and early joining methods.
Influence on Future Advancements
The discoveries of 1500 B.C. set the stage for ongoing innovation:
- Refinement of Metallurgical Processes: Techniques for mercury amalgamation and iron smelting evolved, increasing efficiency and scalability.
- Foundation for Welding: The production and manipulation of iron laid the groundwork for early welding techniques, such as forge welding, which would develop into modern processes.
The advancements in mercury and iron smelting during this era showcase the ingenuity of ancient civilizations. These innovations not only shaped their immediate societies but also laid the foundation for future technological progress in metallurgy and welding.
Developments in 1330 B.C.
In 1330 B.C., the Egyptians took significant strides in advancing welding techniques by incorporating blowpipes and soldering methods into their metalworking practices. These innovations reflected a deep understanding of heat manipulation and material joining, paving the way for more intricate and durable metal creations.
Use of Blowpipes in Metalworking
Blowpipes, simple tools used to direct a focused stream of air onto a heat source, allowed the Egyptians to achieve higher temperatures than previously possible. This innovation was critical in working with metals that required precise and localized heating.
Increased Heat Efficiency
By directing airflow onto charcoal or other heat sources, blowpipes intensified combustion, enabling higher and more controlled temperatures for melting and joining metals.
This made it easier to work with alloys and harder metals that required elevated temperatures for manipulation.
Applications
Blowpipes were primarily used in the crafting of jewelry, ornaments, and ceremonial objects where intricate details were essential.
Artifacts such as gold amulets, inlaid decorations, and intricate bronze tools showcase the precision achieved through this method.
Advancements in Soldering Techniques
Soldering, a process that involves joining metals using a filler material with a lower melting point, became a vital technique during this period. The Egyptians refined this method to create durable and aesthetically pleasing metalwork.
Solder Materials
The filler materials typically consisted of alloys of gold, silver, or copper, chosen for their compatibility with the base metals and aesthetic qualities.
These solders melted at relatively low temperatures, preventing damage to delicate base metals while ensuring strong joints.
Applications
- Jewelry Making: Soldering allowed artisans to combine precious metals into intricate designs, including necklaces, bracelets, and rings.
- Religious Artifacts: Many ceremonial items, such as statuettes and ritual implements, were created using soldering techniques to attach decorative elements.
- Functional Tools: Soldering was also used to repair and reinforce tools, increasing their utility and lifespan.
Broader Impacts of These Techniques
The Egyptians’ use of blowpipes and soldering marked a significant technological advancement, with implications that extended beyond aesthetics:
- Improved Craftsmanship: The ability to achieve precise and durable joints allowed for more complex and intricate designs, setting new standards in metalworking.
- Cultural Significance: Many items created using these techniques were deeply tied to religious and social practices, symbolizing wealth, power, and spiritual beliefs.
- Technological Legacy: The innovations developed during this period influenced subsequent civilizations, including the Greeks and Romans, who adopted and enhanced these techniques in their own metalworking traditions.
Laying the Foundation for Modern Welding
The methods pioneered by the Egyptians in 1330 B.C. represent an early form of welding, as they involved the fundamental principles of heat and material joining. These advancements:
- Introduced Precision Heating: Blowpipes demonstrated the potential of focused heat in achieving specific metalworking goals.
- Enhanced Material Joining: Soldering showcased the importance of filler materials in creating strong and lasting bonds.
By mastering these techniques, the Egyptians not only elevated the art of metalworking but also contributed foundational knowledge that would evolve into modern welding practices. The artifacts they left behind continue to serve as a testament to their ingenuity and craftsmanship.
Developments in 1000 B.C.
The period around 1000 B.C. saw significant advancements in metalworking, particularly with the rise of pressure welding techniques. This process became increasingly prominent as civilizations sought to produce stronger and more reliable tools, weapons, and decorative items.
Rise of Pressure Welding
Pressure welding involved heating iron to a malleable state and then using mechanical force, such as hammering, to join pieces together. This technique allowed for the creation of durable and functional items, setting a foundation for modern forging and welding practices.
- Applications in Weaponry: Iron spearheads and swords produced using pressure welding were highly valued for their strength and durability. These weapons provided a critical advantage in warfare, helping civilizations like the Celts and early Greeks to dominate their adversaries.
- The use of pressure welding in weapon production marked a departure from bronze, as iron was more readily available and could be worked into sharper, more resilient blades.
- Decorative Uses: Artisans used pressure welding to create intricate patterns in ironwork, such as decorative hilts and handles for weapons and tools. Gold boxes found in Ireland, crafted with pressure welding techniques, illustrate the dual utility and artistic expression of this method.
- Advancement of Metalworking: Pressure welding allowed for more complex assemblies, enabling the creation of multi-part tools and weapons. It also introduced the concept of layered construction, where different types of metal could be combined to optimize durability and function.
Broader Impacts
- Technological Spread: The technique of pressure welding spread across Europe and the Mediterranean, influencing trade and cultural exchanges.
- Foundation for Smithing: The emphasis on hammering and heat laid the groundwork for the development of blacksmithing as a key trade in subsequent centuries.
Developments in 589 B.C.
In 589 B.C., during the Sui Dynasty in China, metallurgists achieved a groundbreaking milestone by developing techniques to produce steel from wrought iron. This innovation revolutionized toolmaking and structural applications, paving the way for more robust and versatile creations throughout the history of welding.
Transition from Wrought Iron to Steel
Steel, an alloy of iron and carbon, offered superior strength and flexibility compared to wrought iron. Chinese metallurgists discovered methods to introduce carbon into molten iron, creating a material that was more durable and less brittle.
Key Techniques
- Carbon Introduction: Charcoal was used as both a fuel source and a carbon provider, enriching molten iron during the smelting process.
- Quenching: Rapid cooling of heated steel in water or oil was introduced to harden the material and improve its wear resistance.
Applications of Steel
The creation of steel enabled the production of advanced tools, weapons, and infrastructure components:
- Tools: Steel plowshares and axes improved agricultural efficiency, enabling farmers to work tougher soils and expand cultivation. Durable chisels and saws enhanced construction and artistry, allowing for more ambitious projects.
- Weapons: Steel swords and armor provided a tactical advantage on the battlefield. These items were lighter yet stronger than their wrought iron counterparts.
- Infrastructure: Steel nails and fittings were used in construction, contributing to the development of larger and more stable structures.
Broader Impacts of Steel Production
- Technological Leadership: The ability to produce steel placed China at the forefront of metallurgical innovation, influencing neighboring regions and trade networks.
- Economic Growth: Steel production supported expanded agricultural and industrial capabilities, driving economic prosperity during the Sui Dynasty.
- Cultural Significance: The strength and versatility of steel reinforced its value in Chinese society, symbolizing progress and technological achievement.
Legacy
The techniques developed in 589 B.C. laid the foundation for future advancements in metallurgy and welding. The principles of carbon enrichment and heat treatment are still fundamental in modern steel production. This innovation marked the beginning of a new era in material science, shaping the course of human development for centuries to come.
History of Welding in the Middle Ages (401 A.D. – 1401 A.D.)
The Middle Ages saw significant refinement of welding techniques, primarily centered on hammering and blacksmithing. These methods demonstrated the growing expertise of artisans in shaping and joining metals. Artifacts from this era, such as welded golden boxes and functional tools, highlight the craftsmanship and technological advancements of the time.
Blacksmithing and Hammer Welding
Blacksmiths in the Middle Ages were central to the development of welding. Using forge welding techniques, they would heat metal pieces to a malleable state and hammer them together to create strong, cohesive bonds.
- Applications in Tools and Weapons: Tools such as plows, axes, and chisels were crafted through hammer welding, which enhanced their strength and durability.
- Blacksmiths produced swords, shields, and armor, ensuring these items could withstand the rigors of battle.
- Decorative Metalwork: Hammer welding allowed artisans to create intricate patterns and designs on ceremonial weapons and religious artifacts, blending functionality with aesthetic appeal.
Theophilus’ Contributions to Welding Knowledge
Theophilus, a medieval monk, documented several metallurgical techniques in his manuscript, On Diverse Arts. His writings provide valuable insight into the processes of the time.
- Flux for Silver Brazing: Theophilus described mixing flux using potassium tartrate and sodium chloride, which was used to facilitate silver brazing by cleaning metal surfaces and improving adhesion.
- This innovation improved the quality of joins, especially in decorative and delicate items.
- Practical Applications: Silver brazing was used in crafting ornate chalices, crosses, and reliquaries, many of which are preserved in museums today.
Discovery of Zinc
During this period, the discovery of zinc added a new dimension to metalworking. While not directly used in welding, zinc’s properties as an alloying element significantly impacted the metallurgical field.
- Role in Brass Production: Zinc was combined with copper to create brass, an alloy known for its corrosion resistance and workability. Brass became a popular material for tools, musical instruments, and decorative items.
- Advances in Metal Joining: Zinc’s inclusion in soldering alloys improved the strength and versatility of metal joins.
Broader Impacts of Welding in the Middle Ages
The welding techniques developed during this era had far-reaching implications:
- Foundation for Modern Welding: Hammer welding and brazing set the stage for more sophisticated joining methods, such as forge welding and early arc welding techniques.
- Economic and Social Significance: The production of durable tools and weapons supported agricultural growth and military expansion, shaping the economies of medieval societies.
- Cultural Legacy: Intricate welded artifacts from this period reflect the fusion of functionality and artistry, showcasing the high regard for skilled metalworkers.
Legacy of Middle Ages Welding
The welding practices of the Middle Ages demonstrated the ingenuity of artisans and their ability to innovate within the constraints of their time. By refining hammer welding and exploring the use of flux and new alloys, they laid the groundwork for future advancements in welding and metallurgy. Their contributions continue to inspire and inform modern techniques in the art and science of metal joining.
History of Welding in the 16th – 17th Centuries
The 16th and 17th centuries marked an era of significant intellectual and technological growth, reflected in the evolution of welding techniques. During this time, early scientific approaches to metalworking began to emerge, blending practical experience with documented processes.
Notable Advances
- 1540: “De la Pirotechnia” by Vannoccio Biringuccio
- This treatise provided detailed descriptions of forging operations and metallurgical techniques. As one of the earliest comprehensive works on metallurgy, it introduced systematic approaches to working with metals.
- Impact: Standardized knowledge among blacksmiths and metalworkers.
- Spread of consistent techniques across Europe.
- 1568: Benvenuto Cellini’s Contribution
- Renowned for his artistry, Cellini documented methods for brazing copper and silver alloys. His work demonstrated the use of heat and filler materials to create seamless joins in decorative and functional items.
- Applications: Jewelry and ornamental pieces, including intricate religious artifacts.
- 1599: The First Use of the Word “Weld”
- The term “weld” appeared for the first time, reflecting the formalization of the practice as a recognized technique.
- Significance: Established a linguistic foundation for future documentation and teaching of welding methods.
Broader Impacts
- Cultural Advancement: The documentation of techniques elevated metalworking from a craft to an applied science, influencing Renaissance artistry and engineering.
- Foundation for Innovation: These developments laid the groundwork for the scientific breakthroughs of the Industrial Revolution.
History of Welding in the 1800s
The 19th century brought numerous breakthroughs that transitioned welding from artisanal practices to scientific methods. This era witnessed the development of foundational techniques still in use today.
Key Innovations
- 1836: Discovery of Acetylene
- Acetylene, a highly flammable gas, was discovered and soon adopted for welding due to its ability to produce high temperatures when burned with oxygen.
- Impact: Enabled more precise and efficient welding processes.
Late 1800s: Rise of Carbon Arc Welding
Carbon arc welding uses an electric arc between a carbon electrode and the workpiece. It gained popularity during the late 1800s.
- Patents: C.L. Coffin patented metal electrode arc welding, advancing the technique for broader industrial use.
- 1881: Auguste De Meritens’ Arc Welding: De Meritens used arc welding to fuse lead plates, a technique later adapted for battery manufacturing.
- 1888: Carbon Arc Welding Patents: Patents by S. Olszewski and N. Bernardos refined carbon arc welding, enhancing its application in construction and repair.
Broader Impacts
- Industrial Growth: These innovations supported the expansion of railways, construction, and shipbuilding.
- Foundation for Modern Welding: The techniques developed during this time directly influenced 20th-century advancements.
History of Welding in the 1900s
The 20th century saw rapid innovation and widespread adoption of welding technologies across various industries, revolutionizing manufacturing and construction.
Major Developments
- 1900: Coated Metal Electrodes: A.P. Strohmenger introduced coated electrodes, which improved arc stability and weld quality.
- 1920: Automatic Welding: The introduction of automatic welding used arc voltage and electrode wires to streamline repair and fabrication processes.
- 1930s: Submerged Arc Welding and Stud Welding: Submerged arc welding, developed by the National Tube Company, revolutionized shipbuilding and heavy construction.
- Stud welding facilitated the rapid attachment of metal fasteners, particularly in construction.
- 1941: Heliarc Welding: Meredith developed Heliarc welding (a precursor to TIG welding) for aluminum and magnesium, which became vital for aviation and military applications.
- 1950s: CO2 Welding: CO2 welding gained popularity for its efficiency in welding steels, offering a cost-effective solution for mass production.
- 1960s: Diverse Welding Processes: The decade saw the introduction of electroslag welding, dual shield welding, and plasma arc welding, expanding the range of applications.
Broader Impacts
- Industrial Revolution: Welding became integral to the development of modern infrastructure, including bridges, skyscrapers, and vehicles.
- Technological Advancements: Innovations in welding facilitated advancements in aerospace, automotive, and energy sectors.
Recent Developments in Welding
In recent decades, welding technologies have continued to evolve, integrating precision, efficiency, and automation to meet modern industrial demands.
Key Innovations
- 1991: Friction Stir Welding: Developed by The Welding Institute (TWI), this solid-state joining process is used in aerospace and automotive applications for its precision and strength.
- 2000: Magnetic Pulse Welding: Combined with advancements in X-ray technology, this process enabled the welding of composite materials, expanding possibilities in lightweight construction.
- 2008: Laser Arc Welding: This high-speed precision welding technique is widely used in manufacturing for its ability to handle complex assemblies with minimal distortion.
- 2013: GMAW-Brazing: Gas Metal Arc Welding-Brazing became a standard for automotive steel welding, combining efficiency with durability.
Broader Impacts
- Automation and Robotics: Modern welding systems incorporate robotics for higher efficiency and accuracy, particularly in mass production.
- Environmental Considerations: Advances in welding aim to reduce waste and energy consumption, aligning with sustainable manufacturing practices.
Legacy
The continuous evolution of welding technologies underscores the adaptability and ingenuity of the field. Each new development builds upon centuries of innovation, driving progress across industries and shaping the modern world.
Conclusion
Welding has evolved from rudimentary heat and hammering techniques to highly advanced methods that incorporate robotics and automation. Each era throughout the history of welding reflects the ingenuity and adaptability of metalworkers, driving progress across industries and shaping modern manufacturing. The future of welding holds exciting possibilities as technology continues to push the boundaries of what is achievable.
Additional Resources
Get your welding gear here.
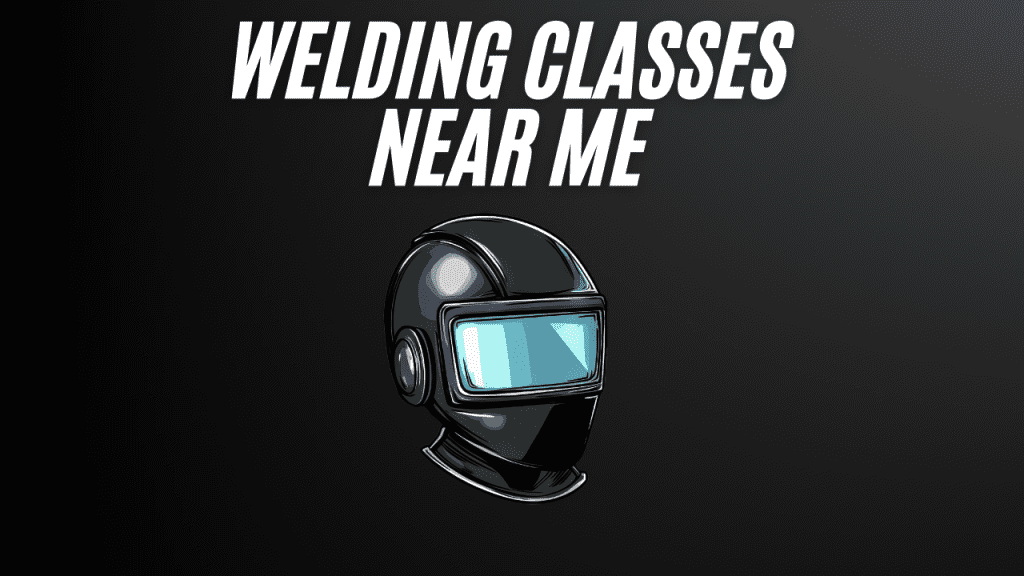