Table of Contents
What’s the Hardest Type of Welding?
Introduction
Among the various welding techniques, Tungsten Inert Gas (TIG) welding is often considered the most challenging to master. While TIG welding offers unmatched precision and quality, the complexities of the process make it a daunting skill to perfect. Below, we delve into why TIG welding is regarded as one of the hardest forms of welding.
Why is TIG Welding Considered the Hardest Form of Welding?
Complete Control Required
TIG welding requires welders to have unparalleled control over every aspect of the process. Unlike methods such as MIG welding, where many variables are automated, TIG welding puts the welder in charge of managing critical parameters like heating, current flow, and shielding gas delivery. For instance, the amount of heat applied must be adjusted constantly to ensure the weld pool stays consistent.
Similarly, the flow rate of the shielding gas—commonly argon or helium—must be carefully regulated to protect the weld pool from contamination. This level of control demands an in-depth understanding of the materials being welded and how they respond to heat and filler metals. Welders must also be able to react quickly to changes in the weld pool, adjusting their technique on the fly to prevent defects such as porosity or undercutting.
Use of Both Hands and Feet
TIG welding is one of the few welding processes that requires the use of both hands and one foot simultaneously. One hand operates the welding torch, which generates the arc, while the other hand feeds the filler rod into the weld pool. The foot controls the amperage via a foot pedal, allowing the welder to adjust the heat output in real-time.
This multi-tasking requirement demands exceptional coordination and concentration. Beginners often find it overwhelming to balance all these elements at once, as any misstep can lead to inconsistent welds or damage to the material. Even experienced welders must maintain steady hands and precise timing to ensure the filler rod is fed into the pool at the right moment and the heat is adjusted to match the material’s thickness and type.
Slow and Detailed Process
TIG welding prioritizes precision over speed, making it one of the slowest welding methods. Welders must move carefully and deliberately to ensure that the weld is uniform and free of defects. This level of detail is especially important for projects that require aesthetic finishes or structural integrity, such as aerospace components, automotive parts, or artistic metalwork.
While this meticulous approach produces superior results, it can be frustrating for welders accustomed to faster methods like MIG or stick welding. The slower pace also makes TIG welding less practical for large-scale projects with tight deadlines, adding another layer of complexity for professionals managing multiple tasks.
Cleanliness is Critical
TIG welding is unforgiving when it comes to surface preparation. The base material must be thoroughly cleaned of rust, paint, grease, or other contaminants before welding begins. Any impurities on the surface can compromise the quality of the weld, leading to issues such as porosity, weak joints, or unsightly finishes. To achieve the necessary cleanliness, welders often spend significant time preparing the surface with specialized tools like grinders, wire brushes, or chemical cleaners.
While this extra step adds time to the process, it is essential for ensuring a strong, durable weld. The requirement for pristine surfaces also means that TIG welding is best suited for controlled environments like workshops or manufacturing facilities, where conditions can be closely managed.
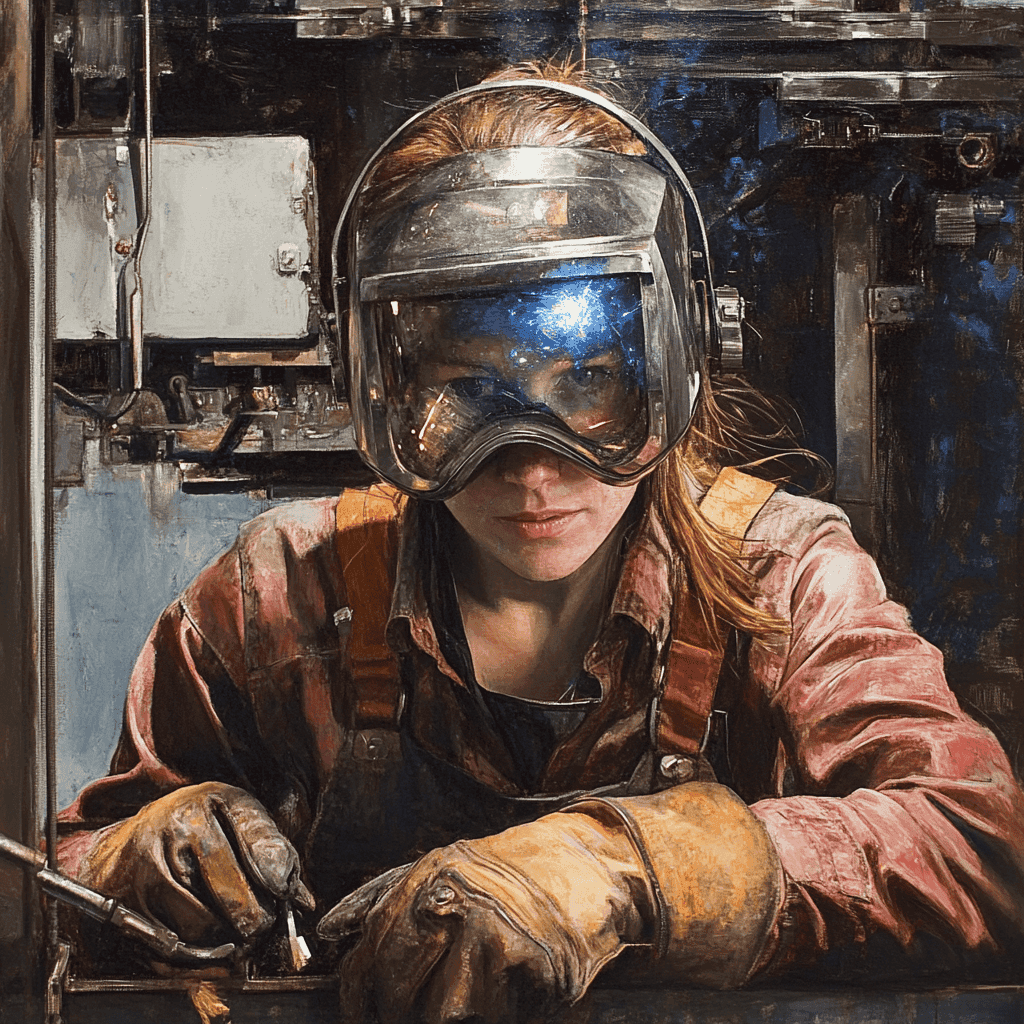
Additional Challenges of TIG Welding
Precision and Consistency
TIG welding is often used for projects that demand extreme precision, such as thin materials, intricate designs, or high-stakes applications like aerospace or medical equipment. Welders must maintain a steady hand and consistent technique to produce clean, even welds. This precision is particularly challenging when working on materials like aluminum or stainless steel, which require careful heat management to avoid warping or burn-through.
Limited Margin for Error
TIG welding offers little room for error. Even minor missteps in technique, such as holding the torch at the wrong angle or applying too much heat, can result in defects that compromise the weld’s strength and appearance. Beginners often struggle with the steep learning curve, as the process demands a high level of skill and experience to master.
Equipment Complexity
TIG welding equipment is more sophisticated than what is used for other methods like stick or MIG welding. Welders must understand how to set up and adjust various components, including the tungsten electrode, shielding gas system, and power source. Selecting the correct tungsten electrode type and size for the material being welded is critical, as is ensuring the proper flow rate of shielding gas. These technical requirements add to the complexity of the process, particularly for those new to welding.
Physical and Mental Demands
TIG welding can be physically and mentally exhausting. Welders often work in uncomfortable positions for extended periods, requiring steady hands and precise movements. The need for intense focus and attention to detail can lead to mental fatigue, especially during long or complex projects. Welders must also have the endurance to maintain their technique and avoid mistakes caused by fatigue.
Why TIG Welding is Worth the Challenge
Despite its challenges, TIG welding is highly regarded for the quality and precision of its results. The process produces clean, aesthetically pleasing welds with minimal spatter and distortion, making it ideal for high-stakes applications. Industries such as aerospace, automotive, and medical equipment manufacturing rely on TIG welding for its ability to create strong, defect-free joints.
For welders willing to invest the time and effort to master TIG welding, the rewards are significant. TIG welders are often in high demand and command higher salaries due to their specialized skills. Additionally, the versatility of TIG welding allows it to be used on a wide range of materials, from aluminum and stainless steel to exotic metals like titanium and magnesium.
Mastering TIG welding requires patience, practice, and dedication, but the ability to produce flawless welds and tackle complex projects makes it a valuable skill for any professional welder.
Common Mistakes to Avoid in TIG Welding
TIG welding demands exceptional precision and attention to detail. Even minor mistakes can compromise weld quality, lead to wasted materials, or damage the workpiece. By understanding and addressing these common errors, welders can improve their craft and achieve high-quality results every time. Below, we explore these mistakes in depth and provide practical tips to avoid them.
Incorrect Tungsten Selection
Selecting the wrong tungsten electrode is a common pitfall, especially for beginners. Tungsten electrodes come in various types, including pure tungsten, thoriated tungsten, ceriated tungsten, and lanthanated tungsten, each designed for specific materials and applications. For example, pure tungsten is ideal for AC welding on aluminum, while thoriated tungsten is better suited for DC welding on steel.
Using the wrong type or size of tungsten can cause unstable arcs, excessive electrode wear, and poor weld penetration. Additionally, incorrect preparation of the tungsten, such as improper grinding angle, can lead to arc instability. Welders should always consult the machine’s manual and material specifications to select and prepare the appropriate tungsten electrode.
Improper Shielding Gas Flow Rate
Shielding gas protects the weld pool from atmospheric contamination, ensuring a clean and strong weld. However, improper gas flow rates can undermine this protection. Too much gas flow creates turbulence, pulling in air that introduces contaminants, while too little flow leaves the weld vulnerable to oxidation.
The recommended shielding gas flow rate typically ranges between 15 and 20 cubic feet per hour (CFH), but environmental factors like wind or confined spaces may require adjustments. Welders should use a high-quality gas regulator to maintain consistent flow and ensure the gas nozzle is clean and free of obstructions.
Overheating the Base Material
Overheating the base material is a frequent issue in TIG welding, particularly when working with thin metals like aluminum or stainless steel. Excessive heat can lead to warping, burn-through, and discoloration, compromising the weld’s strength and appearance.
This problem often arises from holding the torch in one spot for too long or using an amperage setting that is too high for the material. To prevent overheating, welders should use a foot pedal to adjust heat input dynamically and maintain a steady pace to distribute heat evenly. Practicing on scrap materials can help develop the control needed to avoid this issue.
Lack of Surface Preparation
TIG welding demands an immaculate welding surface. Rust, grease, paint, or other contaminants on the workpiece can compromise the weld pool, leading to porosity, weak joints, or poor aesthetics. Despite its importance, surface preparation is often overlooked, especially when welders are pressed for time.
To ensure a clean surface, welders should use appropriate tools like grinders, wire brushes, or chemical cleaners to remove contaminants before welding. For materials prone to oxidation, such as aluminum, preparation should occur immediately before welding to prevent a layer of oxide from forming.
Inconsistent Arc Length
Maintaining a consistent arc length is critical to producing a strong and uniform weld. Holding the torch too far from the weld pool weakens the arc, resulting in poor penetration, while getting too close risks contaminating the tungsten electrode by dipping it into the pool.
Beginners often struggle with maintaining the ideal torch-to-workpiece distance, typically around 1/8 inch. Achieving consistent arc length requires steady hand movements and careful monitoring of the arc. Welders can improve this skill through practice and by using tools like a welding rest to stabilize their hand during work.
Avoiding These Pitfalls
Avoiding common TIG welding mistakes requires a combination of knowledge, preparation, and consistent practice. Welders should prioritize proper tungsten selection, accurate shielding gas management, and thorough surface preparation before starting any project. During welding, maintaining steady hand movements, controlling heat input with a foot pedal, and practicing on scrap material can help refine technique and build confidence.
Investing in high-quality equipment and taking the time to understand material-specific requirements will also significantly improve results. Over time, welders who focus on mastering these fundamentals will find TIG welding to be a highly rewarding and versatile skill that produces professional-grade results.
Conclusion
TIG welding stands out as one of the most challenging yet rewarding welding techniques. Its demand for precision, meticulous control, and attention to detail make it a true test of a welder’s skill. From managing heat input and gas flow to maintaining clean surfaces and consistent arc lengths, TIG welding requires a unique combination of technical expertise and physical coordination. These challenges, however, are balanced by the unmatched quality and precision of the welds it produces.
The applications of TIG welding in industries like aerospace, automotive, and construction underscore its importance in creating durable, high-performance components. Mastering this complex process not only enhances a welder’s craft but also opens doors to specialized, high-paying opportunities in industries where excellence is non-negotiable.
For welders willing to invest time and effort into learning and refining their TIG welding skills, the rewards go beyond financial gain. The ability to create flawless, intricate welds that meet the highest standards of quality and reliability is a source of pride and professional achievement. While TIG welding may be the hardest type of welding to master, its precision, versatility, and contribution to critical projects make it an invaluable skill in the world of welding.
Additional Resources
Get your welding gear here.
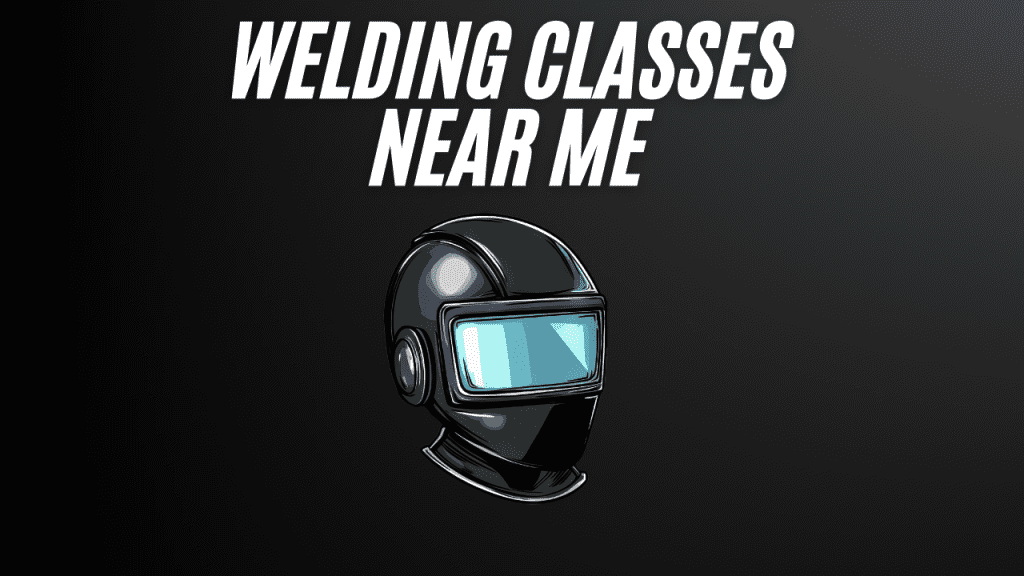