Table of Contents
Determining the Deposition Rate for Welding Wire
Introduction
In welding, the deposition rate is a critical measure that directly affects productivity, cost efficiency, and the quality of the final weld. Understanding and optimizing this rate can lead to faster project completion, better resource management, and superior results. This article explores what deposition rate is, the factors influencing it, how to calculate it, and tips for optimization.
How To Determine the Deposition Rate for Welding Wire
What Is Deposition Rate?
The deposition rate refers to the amount of filler material, usually welding wire, deposited into the weld joint over a given period. Measured in pounds per hour (lb/hr) or kilograms per hour (kg/hr), this metric is a key determinant of welding productivity. A higher deposition rate can reduce welding time and material costs, making it a crucial factor for industrial and commercial welding operations.
Key Factors Influencing Deposition Rate
Welding Wire Type
The type of welding wire used plays a significant role in determining the deposition rate, as different wires are designed for specific melting rates and applications:
- Solid Wires: These wires provide consistent deposition rates and are commonly used in MIG (GMAW) welding. They are ideal for applications requiring smooth welds and minimal cleanup but generally yield lower deposition rates compared to cored wires.
- Flux-Cored Wires: These wires contain a flux material within their core that enhances deposition rates and arc stability. They are well-suited for outdoor or heavy-duty applications and can achieve higher deposition rates than solid wires due to their increased melting efficiency.
- Metal-Cored Wires: These hybrid wires combine the benefits of solid and flux-cored wires, offering higher deposition rates while maintaining a clean weld appearance. They are commonly used in industries requiring high productivity and precision, such as automotive and construction.
The choice of wire type should align with project requirements, balancing factors like deposition rate, weld quality, and application environment.
Current and Voltage
The electrical settings of the welding machine directly influence how quickly the welding wire melts, thus affecting the deposition rate:
- Higher Current: Increases the energy delivered to the wire, leading to faster melting and a higher deposition rate. This is especially useful for thick materials requiring deep penetration.
- Higher Voltage: Provides a broader and more stable arc, which can enhance deposition efficiency. However, excessive voltage can cause arc instability, spatter, and poor bead quality.
Optimizing current and voltage settings ensures efficient material deposition while minimizing defects and waste.
Shielding Gas Composition
The shielding gas not only protects the weld pool but also influences the deposition rate and overall welding performance:
- Pure CO₂: Promotes deep penetration and is cost-effective, but it often produces more spatter, which can decrease effective deposition rates due to material loss.
- Argon-CO₂ Mixtures: Commonly used mixtures like 75% argon and 25% CO₂ provide a stable arc and reduced spatter, improving deposition efficiency.
- Argon-Helium Mixtures: Helium-rich blends are used for applications requiring higher heat input, such as thick materials, as they enhance the melting rate and deposition.
Selecting the right shielding gas for the material and welding process can significantly impact deposition rate and weld quality.
Travel Speed
Travel speed, or the rate at which the welding torch moves along the workpiece, must be carefully controlled to optimize deposition:
- Faster Travel Speed: Reduces the amount of filler material deposited per unit length, which can lead to insufficient penetration and weak welds.
- Slower Travel Speed: Allows more material to be deposited but risks overheating the weld area, causing burn-through or excessive bead buildup.
Balancing travel speed with other parameters ensures a consistent bead profile and adequate penetration while maximizing deposition efficiency.
Wire Feed Speed (WFS)
Wire feed speed is the most direct factor affecting deposition rate:
- Higher WFS: Increases the amount of wire fed into the weld pool, boosting deposition rate. However, excessively high speeds can lead to over-deposition, poor arc stability, and spatter.
- Lower WFS: Reduces the amount of material deposited, which can result in insufficient weld strength or coverage.
Adjusting WFS in conjunction with current, voltage, and travel speed helps achieve the desired deposition rate and ensures weld consistency.
Interaction of Factors
The key to optimizing deposition rate lies in understanding how these factors interact. For instance, increasing wire feed speed requires corresponding adjustments to current and voltage to maintain a stable arc. Similarly, selecting the right wire type and shielding gas for the material ensures the process is efficient and yields high-quality welds. Fine-tuning these parameters as a cohesive system is essential for achieving optimal deposition rates tailored to specific welding projects.
Methods to Calculate Deposition Rate
Basic Formula for Deposition Rate
A precise calculation of the deposition rate is crucial for optimizing welding productivity. The basic formula to determine the deposition rate is: Deposition Rate (lb/hr)=WFS (in/min)×Wire Density (lb/in³)×Cross-sectional Area (in²)×60\text{Deposition Rate (lb/hr)} = \text{WFS (in/min)} \times \text{Wire Density (lb/in³)} \times \text{Cross-sectional Area (in²)} \times 60
- Wire Feed Speed (WFS): The speed at which the wire is fed into the weld, measured in inches per minute (in/min).
- Wire Density: The material density of the welding wire, typically provided in pounds per cubic inch (lb/in³).
- Cross-sectional Area: Calculated based on the diameter of the wire, it represents the area of the wire’s cross-section in square inches (in²).
- 60: A conversion factor to extrapolate the rate from minutes to an hourly basis.
This formula provides an accurate measure of deposition rate, allowing welders to plan material usage and production timelines efficiently.
Example Calculation
For a 0.045-inch diameter steel wire with a density of 0.283 lb/in³ and a wire feed speed of 300 in/min:
-
Calculate the cross-sectional area:
Area = π × (Diameter / 2)² Area = 3.14 × (0.0225)² Area ≈ 0.00159 in²
-
Apply the formula:
Deposition Rate = WFS × Wire Density × Cross-sectional Area × 60 Deposition Rate = 300 × 0.283 × 0.00159 × 60 Deposition Rate ≈ 8.1 lb/hr
This calculation shows that the welding setup deposits approximately 8.1 pounds of material per hour.
Using Welding Charts or Manufacturer Data
Many welding equipment and wire manufacturers provide detailed charts and data sheets that correlate wire feed speeds, current settings, and wire types with expected deposition rates. These charts simplify the estimation process and reduce setup time.
- Benefits:
- Saves time by eliminating the need for manual calculations.
- Provides manufacturer-verified data for specific equipment and materials.
- Ensures consistency and accuracy in production planning.
Testing and Observation
Practical testing and direct observation remain essential for fine-tuning welding parameters and verifying deposition rates:
- Conduct Test Welds: Set up the welding equipment with the desired parameters and perform a short-duration weld.
- Measure the Deposited Material: Weigh the material deposited in a specific timeframe to determine the actual deposition rate.
- Adjust Parameters: Modify wire feed speed, current, or other settings to achieve the desired deposition rate based on test results.
Advantages of Testing:
- Accounts for real-world variables like arc stability, spatter, and material loss.
- Allows for immediate adjustments to optimize weld quality and efficiency.
Combination of Methods: For the best results, combine the theoretical formula with manufacturer data and practical testing. This approach ensures accuracy, considers real-world conditions, and aligns with production goals. By leveraging these methods, welders and engineers can optimize deposition rates, minimize waste, and enhance overall productivity.

Enhancing Deposition Rate
Optimizing Wire Feed Speed and Voltage
Achieving the optimal deposition rate begins with precise adjustments to wire feed speed and voltage settings. These parameters work in tandem to control the amount of material deposited and the quality of the weld.
- Wire Feed Speed (WFS): Increasing the wire feed speed raises the deposition rate by feeding more material into the arc. However, excessive WFS can cause burnback, spatter, or unstable arcs, while too low a speed may result in incomplete fusion.
- Voltage Adjustments: Voltage affects the arc length and stability. Proper voltage settings ensure consistent melting of the wire and smooth material transfer. Low voltage can create an erratic arc, while excessive voltage may lead to undercut or excessive spatter.
- Tailored Settings: Adjusting WFS and voltage according to material thickness, joint design, and welding position helps optimize productivity and ensures a strong, defect-free weld.
Selecting the Right Welding Process
Different welding processes yield varying deposition rates, each suited to specific applications and project demands.
- Gas Metal Arc Welding (GMAW or MIG): Known for versatility and ease of use, GMAW offers moderate deposition rates suitable for thin to medium-thickness materials.
- Flux-Cored Arc Welding (FCAW): With higher deposition rates than GMAW, FCAW is effective for thicker materials and outdoor welding, as the flux provides its own shielding.
- Submerged Arc Welding (SAW): Ideal for large-scale industrial projects, SAW delivers the highest deposition rates, often exceeding 25 lb/hr. Its automated nature and ability to handle thick sections make it a preferred choice for shipbuilding, pipelines, and structural fabrication.
- Manual Metal Arc Welding (MMAW or Stick Welding): While slower in deposition, stick welding excels in versatility and suitability for repair work and outdoor conditions.
Choosing the right process ensures efficiency and quality, aligning with project requirements and material properties.
Improving Operator Technique
Even with the best equipment, operator skill significantly influences deposition rate and weld quality. Techniques to enhance performance include:
- Consistent Travel Speed: Maintaining a steady hand and uniform travel speed prevents inconsistencies in deposition and avoids defects like undercut or overfill.
- Angle Control: Proper torch or electrode angle ensures even distribution of the weld pool and minimizes spatter. For example, a 10-15° push or drag angle is recommended for most applications.
- Stringer Beads vs. Weave Beads: Stringer beads are faster and suitable for high-deposition applications, while weave beads offer better penetration and are used for thicker joints.
- Practice and Training: Regular training and hands-on experience enable welders to fine-tune their technique, resulting in more efficient material use and higher-quality welds.
Combined Approach for Optimization
The interplay between machine settings, process selection, and operator skill creates the foundation for optimizing deposition rates. By focusing on these areas, welders can achieve maximum productivity, reduce material waste, and ensure the structural integrity of their welds.
Selecting the Right Welding Process
Different welding processes yield varying deposition rates, each suited to specific applications and project demands.
- Gas Metal Arc Welding (GMAW or MIG): Known for versatility and ease of use, GMAW offers moderate deposition rates suitable for thin to medium-thickness materials.
- Flux-Cored Arc Welding (FCAW): With higher deposition rates than GMAW, FCAW is effective for thicker materials and outdoor welding, as the flux provides its own shielding.
- Submerged Arc Welding (SAW): Ideal for large-scale industrial projects, SAW delivers the highest deposition rates, often exceeding 25 lb/hr. Its automated nature and ability to handle thick sections make it a preferred choice for shipbuilding, pipelines, and structural fabrication.
- Manual Metal Arc Welding (MMAW or Stick Welding): While slower in deposition, stick welding excels in versatility and suitability for repair work and outdoor conditions.
Choosing the right process ensures efficiency and quality, aligning with project requirements and material properties.
Improving Operator Technique
Even with the best equipment, operator skill significantly influences deposition rate and weld quality. Techniques to enhance performance include:
- Consistent Travel Speed: Maintaining a steady hand and uniform travel speed prevents inconsistencies in deposition and avoids defects like undercut or overfill.
- Angle Control: Proper torch or electrode angle ensures even distribution of the weld pool and minimizes spatter. For example, a 10-15° push or drag angle is recommended for most applications.
- Stringer Beads vs. Weave Beads: Stringer beads are faster and suitable for high-deposition applications, while weave beads offer better penetration and are used for thicker joints.
- Practice and Training: Regular training and hands-on experience enable welders to fine-tune their technique, resulting in more efficient material use and higher-quality welds.
Combined Approach for Optimization
The interplay between machine settings, process selection, and operator skill creates the foundation for optimizing deposition rates. By focusing on these areas, welders can achieve maximum productivity, reduce material waste, and ensure the structural integrity of their welds.
Challenges in Measuring Deposition Rate
Material Waste
Spatter, incomplete fusion, and other inefficiencies can reduce the actual deposition rate. Accounting for these factors is essential for accurate calculations.
Welding Position
The orientation of the weld—flat, horizontal, vertical, or overhead—affects how efficiently material is deposited. Flat welding generally yields the highest deposition rates.
Environmental Factors
Wind, humidity, and improper shielding gas coverage can disrupt the welding process, affecting deposition efficiency and weld quality.
Applications of Deposition Rate Data
Project Planning
Knowing the deposition rate helps estimate material needs, time requirements, and labor costs, leading to more accurate project planning.
Cost Management
By optimizing deposition rates, companies can reduce waste, improve efficiency, and control expenses.
Performance Metrics
Deposition rate data allows for benchmarking welder productivity and identifying areas for improvement.
Tools for Monitoring Deposition Rate
- Wire Feed Speed Calculators: Tools to quickly estimate deposition rates based on welding parameters.
- Advanced Welding Power Sources: Machines with built-in deposition monitoring capabilities for real-time adjustments.
- Welding Productivity Software: Applications for tracking and analyzing deposition rates across multiple projects.
Conclusion
Understanding and determining the deposition rate for welding wire is essential for achieving efficient and high-quality welds. By considering factors like wire type, current settings, and welding processes, and using tools like calculators and manufacturer data, welders can optimize deposition rates for their specific needs. Whether you’re planning a large-scale construction project or fine-tuning a production line, mastering this aspect of welding can significantly enhance outcomes and efficiency.
Additional Resources
Get your welding gear here.
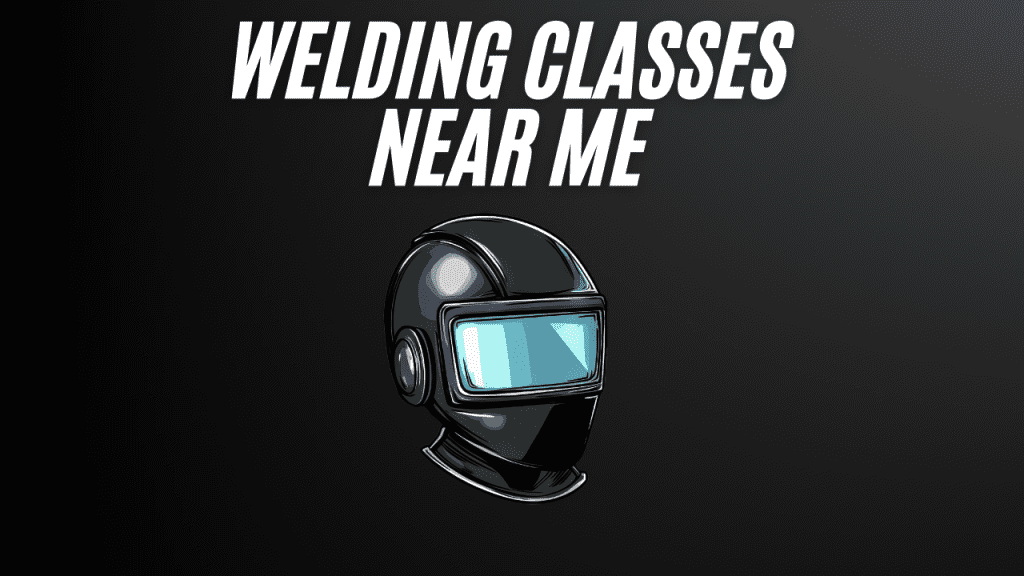