Table of Contents
What Are Consumables in Welding?
Consumables in welding refer to materials that are used up or need periodic replacement during the welding process. These include items like electrodes, wires, filler rods, and flux. Choosing the right consumables is essential to achieving strong, durable welds. While the variety of options may seem overwhelming, understanding their types and applications can simplify the selection process.
Consumables play a critical role in forming a strong bond between metals and are one of the four main components of welding, alongside the base material, shielding gas, and heat source.
Factors Influencing Consumable Choice
The choice of welding consumables depends on various factors, including:
- The type of metal being welded (e.g., steel, aluminum).
- The specific application (e.g., structural fabrication, pipe welding).
- Groove design and joint configuration.
- Welding code or standard requirements.
- Welding position (e.g., flat, vertical, overhead).
- Environmental conditions (e.g., indoors, high-wind areas).
Types of Welding Consumables
Welding consumables are essential components of the welding process, serving as electrodes, filler materials, or both. The choice of consumables depends on the welding process, material being joined, and specific project requirements. Here’s an expanded look at the main types of welding consumables.
Welding Wires
Welding wires play a dual role as the electrode and filler material in processes like MIG (Metal Inert Gas) welding and FCAW (Flux-Cored Arc Welding). Their consistent and controlled feed makes them ideal for efficient welding.
Solid Wire
- Use: Commonly employed in MIG welding for metals under 3/16 inches thick, such as thin steel sheets and aluminum.
- Advantages:
- Produces clean, smooth welds with minimal spatter.
- Provides consistent arc stability and a visually appealing bead profile.
- Limitations:
- Requires shielding gas to protect the weld pool, which may be ineffective in high-wind environments.
- Best suited for indoor applications or controlled environments.
Flux-Core Wire
Flux-core wires are optimized for versatility, making them suitable for a range of applications, including outdoor and heavy-duty welding.
- Use: Ideal for outdoor environments and thicker materials, where shielding gas may not be practical.
- Advantages:
- Comes in two types for added flexibility:
- Gas-Shielded (FCAW-G): Uses external shielding gas for better weld quality.
- Self-Shielded (FCAW-S): Eliminates the need for external gas, relying on its flux core for protection.
- Performs better than solid wire in vertical and overhead welding positions.
- Comes in two types for added flexibility:
- Examples:
- E71T-1: High-performance wire known for smooth arcs and minimal spatter, commonly used in shipbuilding and structural fabrication.
- E70T-4: Best for welding thick steel plates in outdoor settings, offering high deposition rates.
- E71T-14: Designed for welding galvanized or coated sheet steels, minimizes defects by vaporizing coatings in the arc.
Stick Electrodes
Stick electrodes are consumables used in SMAW (Shielded Metal Arc Welding). They are classified based on their coating and usability in different welding positions. These electrodes melt during the welding process, providing both the arc and filler material.
Bare Electrodes
- Characteristics:
- Have minimal coating, primarily used in submerged arc welding.
- Designed for applications where flux-coated electrodes are unnecessary or undesirable.
- Applications:
- Welding manganese steel.
- Situations requiring clean, slag-free welds or automated processes.
Covered Electrodes
Covered electrodes come with various coatings, each tailored for specific welding needs. The coating affects arc stability, shielding, and weld quality.
- Light-Coated Electrodes:
- Benefits:
- Help reduce impurities like oxides and phosphorous.
- Increase the surface tension of the molten metal, resulting in smaller, more controlled globules.
- Applications: Used for cleaner welds and improved arc stability in general welding.
- Benefits:
- Medium-Coated Electrodes:
- Provide enhanced control over the weld pool, making them suitable for more precise applications.
- Typically used for structural welding where additional weld strength is required.
- Heavily-Coated Electrodes:
- Benefits:
- Form a protective gas shield to prevent contamination from oxygen and nitrogen.
- Produce a slag layer that covers the molten weld pool, helping the weld solidify at a controlled rate.
- Minimize spatter and improve arc stability.
- Applications:
- Used in high-performance welds where reduced contamination and consistent arc performance are critical.
- Common in heavy structural and pipeline welding.
- Benefits:
Filler Rods
Filler rods are manually fed into the weld pool in processes like TIG (Tungsten Inert Gas) welding. They provide additional material to create strong, corrosion-resistant joints.
- Use: Essential for precision welding, especially for non-ferrous metals like aluminum and stainless steel.
- Advantages:
- Available in various compositions to match the base material.
- Provide excellent control over the weld pool, resulting in clean and precise welds.
- Applications:
- Aerospace, automotive, and industrial manufacturing where high-quality finishes are required.
By understanding the different types of welding consumables and their specific applications, welders can select the right materials for their projects. Whether it’s solid wire for a clean MIG weld or a heavily-coated electrode for a robust stick weld, choosing the appropriate consumables ensures strong, efficient, and high-quality welding results.
Advantages of Using the Correct Consumables
Selecting the appropriate welding consumables for a project offers numerous benefits that extend beyond just the quality of the weld. Here’s an expanded look at why using the right consumables is critical:
Stronger Bonds
Using the correct consumables ensures that welds are strong, durable, and capable of meeting the demands of the application.
- Material Compatibility: Properly chosen consumables match the base material’s properties, promoting optimal fusion and preventing issues like cracking or warping.
- Load-Bearing Capacity: For structural applications, correctly paired consumables ensure the weld can withstand the stresses it is subjected to, whether it’s static or dynamic loading.
- Corrosion Resistance: Specific consumables enhance resistance to environmental factors like moisture or chemicals, extending the lifespan of the weld.
Code Compliance
Many welding projects must adhere to strict industry standards, and using certified consumables is a key part of meeting these requirements.
- AWS Standards: Consumables classified by the American Welding Society (AWS) or equivalent standards ensure that the materials used are tested and reliable for specific applications.
- Safety Assurance: Compliant consumables minimize risks by guaranteeing weld integrity, particularly in critical industries like construction, aerospace, and shipbuilding.
- Simplified Inspection: Certified consumables streamline the inspection process, as regulatory bodies often recognize and trust standardized materials.
Improved Efficiency
Tailored consumables can significantly enhance the efficiency of the welding process, saving time and resources.
- Reduced Defects: Consumables optimized for the welding process and material type minimize issues like porosity, spatter, or incomplete fusion.
- Minimized Rework: Correct consumables result in fewer weld defects, reducing the need for repairs or adjustments.
- Ease of Use: Consumables designed for specific positions or techniques simplify the welder’s job, allowing for faster and more consistent results.
- Cost Savings: While high-quality consumables may initially seem more expensive, their ability to reduce waste and avoid rework often results in long-term cost savings.
Enhanced Aesthetics
In applications where visual appeal matters, such as automotive or architectural projects, the right consumables produce smooth, clean, and visually pleasing welds.
- Minimal Spatter: Solid wires or light-coated electrodes help achieve neat welds with minimal cleanup required.
- Uniform Beads: Proper consumables ensure consistent bead profiles, which are crucial for both structural integrity and aesthetics.
Versatility Across Applications
By selecting the appropriate consumables, welders can adapt to a variety of materials, environments, and welding positions.
- Custom Solutions: Consumables tailored for specific tasks, such as self-shielded flux-core wires for outdoor welding or low-hydrogen electrodes for critical structures, improve versatility and reliability.
- Adaptability to Conditions: Whether welding in high-wind environments, underwater, or in confined spaces, the right consumables ensure the process remains effective and efficient.
Using the correct consumables is not just about meeting technical requirements—it also contributes to the overall success of a project by ensuring safety, durability, efficiency, and compliance with industry standards.
AWS Standardized Classifications
The American Welding Society (AWS) has established standardized classifications to make the selection of welding consumables easier and to ensure consistent quality across industries. These classifications provide critical information about the composition, usability, and performance of consumables. Below are examples of common classifications:
E7018: Low-Hydrogen Electrode
- Description: A low-hydrogen electrode designed for structural steel welding.
- Key Features:
- Produces high-strength welds with excellent crack resistance.
- Suitable for welding in all positions, making it versatile for various applications.
- Generates minimal spatter, resulting in a cleaner finish.
- Applications:
- Used in construction projects like bridges, buildings, and heavy equipment.
- Ideal for joining high-stress steel structures.
ER70S-6: MIG Welding Wire for Mild Steel
- Description: A copper-coated solid wire designed for Gas Metal Arc Welding (MIG) of mild steel.
- Key Features:
- High silicon and manganese content enhances deoxidization, leading to cleaner welds.
- Suitable for welding materials with mill scale or surface rust.
- Delivers smooth arc performance and minimal spatter.
- Shielding Gas: Typically used with a 75% Argon / 25% CO₂ (C25) gas mix for optimal results.
- Applications:
- Automotive repairs and manufacturing.
- Fabrication of general steel components, including frames and structures.
Benefits of AWS Classifications
- Ease of Selection: Standardized labels provide welders with essential details, such as strength, usability, and composition, enabling informed decisions.
- Regulatory Compliance: Ensures consumables meet industry standards and codes, improving safety and reliability.
- Interchangeability: Allows welders to compare products across brands while maintaining consistency in performance.
By adhering to AWS classifications, welders can confidently select the right consumables for their projects, ensuring quality, safety, and efficiency.
Common Stick Electrode Classifications
Common Stick Electrode Classifications
Stick electrodes are classified using a standardized naming system that provides valuable information about their composition, strength, and usability. These classifications are crucial for welders to select the right electrode for their specific application. Below is a detailed breakdown of common stick electrode classifications and their meanings:
E: Electrode
- The “E” indicates that the material is designed for use as a welding electrode. It signifies the consumable’s role in conducting electrical current to create the arc and deposit filler material into the weld joint.
70: Tensile Strength
- The “70” in the classification refers to the tensile strength of the deposited weld metal. This strength is measured in thousands of pounds per square inch (PSI), indicating that this electrode produces welds capable of withstanding 70,000 PSI of pulling or stretching force.
- Applications:
- Structural steel fabrication.
- High-stress environments like bridges, buildings, and heavy machinery.
1: All-Position Usability
- The “1” denotes the electrode’s versatility in welding positions. It can be used effectively in flat, horizontal, vertical, and overhead welding positions.
- Importance:
- Provides flexibility for complex structures or jobs where multiple positions are required.
- Commonly used in pipe welding and structural applications where position changes are frequent.
8: Flux Type and Additional Properties
- The final digit specifies the type of flux coating on the electrode and its additional characteristics. For instance:
- Low-Hydrogen Coating: Reduces the risk of hydrogen-induced cracking, making it ideal for high-strength or thicker materials.
- Deoxidizers: Improve weld quality by minimizing impurities, such as oxides, in the weld pool.
- Smooth Arc Performance: Provides consistent arc stability, reducing spatter and ensuring a clean weld.
Example: E7018 Electrode
- E: Electrode for welding.
- 70: Produces a weld with 70,000 PSI tensile strength.
- 1: Suitable for all welding positions.
- 8: Low-hydrogen coating with excellent arc stability and reduced spatter.
Other Common Stick Electrodes
- E6010:
- Tensile Strength: 60,000 PSI.
- Usability: All positions.
- Flux: Cellulose-based coating, providing deep penetration and a strong arc. Ideal for root passes in pipe welding.
- E6013:
- Tensile Strength: 60,000 PSI.
- Usability: All positions.
- Flux: Produces a soft arc with minimal penetration. Often used for sheet metal welding and thin materials.
By understanding these classifications, welders can select the appropriate stick electrode to achieve optimal results, ensuring strong, durable, and defect-free welds tailored to the specific requirements of their projects.
Best Practices for Consumable Use
Best Practices for Consumable Use
Ensuring the correct use of consumables is critical for achieving high-quality welds, improving efficiency, and maintaining safety. Here are some expanded best practices to guide welders in optimizing consumable selection and use:
Know Your Material
- Importance of Compatibility: The chemical composition of the consumable must match or complement the base material. For instance:
- Use stainless steel electrodes for welding stainless steel to maintain corrosion resistance.
- For aluminum welding, select filler rods or wires specifically designed for aluminum alloys.
- Why It Matters:
- Using incompatible consumables can lead to weak bonds, cracking, or corrosion in the weld over time.
- Matching consumables to the base material ensures structural integrity and long-term durability.
Understand the Welding Environment
- Environmental Factors:
- Outdoor Welding: For windy conditions, opt for self-shielded flux-core wires or stick electrodes, as these do not rely on external shielding gas that could disperse.
- High-Temperature Environments: Use heat-resistant electrodes like those designed for high-strength steel in applications exposed to extreme heat, such as boilers or pipelines.
- Remote Locations: Stick electrodes are versatile and portable, making them ideal for field repairs where advanced equipment might not be available.
- Why It Matters:
- The environment directly impacts the effectiveness of consumables. Shielding gases, for example, may be compromised outdoors, while remote sites require simplicity and adaptability.
Follow Standards
- AWS Classifications:
- The American Welding Society (AWS) provides standardized classifications for consumables, such as electrodes, wires, and filler rods.
- Examples:
- E7018: A low-hydrogen stick electrode ideal for structural steel applications.
- ER70S-6: A common MIG wire for welding mild steel with C25 shielding gas.
- Benefits of Standards:
- Ensure that the consumable meets industry quality and safety requirements.
- Facilitate easier selection and replacement of consumables across different brands and suppliers.
- Why It Matters:
- Adhering to standards reduces the risk of weld failure and ensures that the final weld meets code requirements for structural integrity.
Inspect and Replace
- Inspection Routine:
- Electrodes: Check for moisture contamination, particularly in low-hydrogen electrodes like E7018, which can absorb moisture and cause hydrogen-induced cracking.
- Wires: Inspect for rust or dirt accumulation that can lead to weld defects.
- Filler Rods: Ensure they are clean and free from oxidation or oil residues.
- When to Replace:
- Replace consumables that show visible wear, contamination, or damage, such as cracked coatings or rusted wires.
- Why It Matters:
- Damaged or contaminated consumables compromise the quality of the weld, leading to defects like porosity, spatter, or weak joints.
Maintain Storage Conditions
- Proper Storage:
- Store consumables in dry, temperature-controlled environments to prevent contamination and degradation.
- Use sealed containers or moisture-proof storage cabinets for electrodes, especially low-hydrogen types.
- Why It Matters:
- Prevents moisture absorption, oxidation, and contamination that could affect weld quality.
Optimize Welding Parameters
- Match Settings to Consumables:
- Adjust amperage, voltage, and travel speed based on the specific consumable being used. For example:
- Use higher amperage for thick electrodes or wires to ensure adequate penetration.
- Reduce voltage for thin materials to prevent burn-through.
- Adjust amperage, voltage, and travel speed based on the specific consumable being used. For example:
- Why It Matters:
- Incorrect settings can result in poor arc stability, excessive spatter, or inadequate penetration, reducing weld quality.
By following these best practices, welders can maximize the performance of their consumables, reduce waste, and ensure strong, defect-free welds across various applications and environments. These steps not only improve efficiency but also enhance safety and compliance in welding operations.
Conclusion
Understanding welding consumables is essential for achieving high-quality welds. By selecting the appropriate electrodes, wires, or filler rods based on material, environment, and application, welders can ensure strong, compliant, and efficient results. Standardized classifications like those from AWS simplify the process, making it easier to match consumables to specific needs. With proper knowledge and practices, consumables become an asset rather than a challenge in welding projects.
Additional Resources
Get your welding gear here.
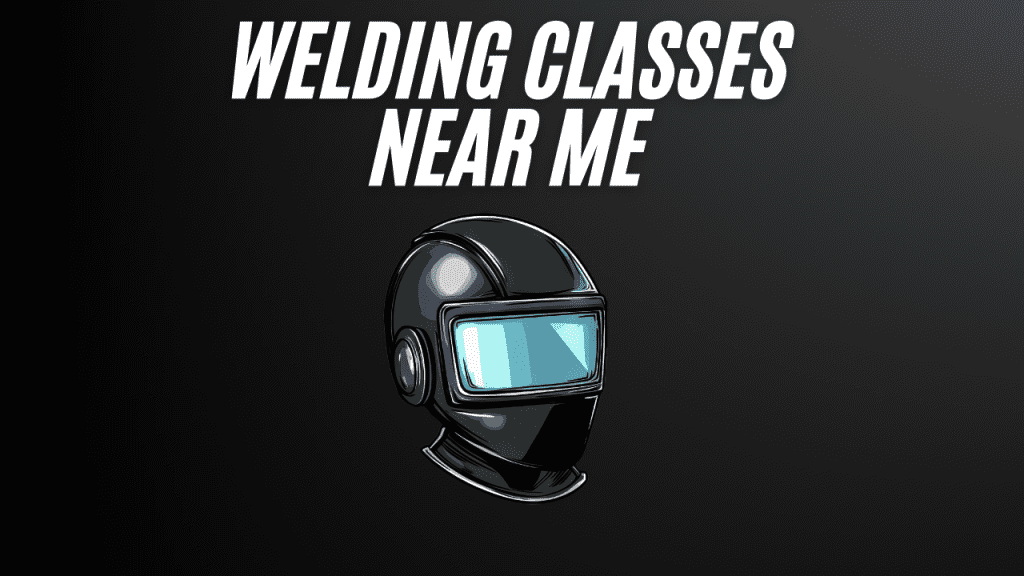