Table of Contents
TL;DR
Yes, generators can be used to run welders, but it’s essential to select the right generator to avoid damaging your equipment. Use generators with Total Harmonic Distortion (THD) rates of 6% or less to minimize the risk to your welder. Ensure the generator matches the welder’s wattage and power requirements and accounts for potential voltage fluctuations that can impact welding performance.
Can You Run a Welder Off Of A Generator?
Introduction
When welding, you may find yourself in situations where accessing your workshop’s reliable power supply isn’t feasible. Whether you’re working outdoors or in locations with limited electrical outlets, using a generator becomes a practical solution. However, before plugging in your welder, there are important factors to consider to ensure safe and efficient operation.
What to Know Before Running a Welder on a Generator
Essential Generator Features
For successful welding with a generator, it’s crucial to ensure that the generator meets these requirements:
- Sufficient Wattage: The generator’s output must match or exceed the welder’s input power needs, including both continuous and surge wattage requirements. A generator that’s too small will lead to inconsistent performance or damage to the equipment.
- Clean Power Delivery: Generators with Total Harmonic Distortion (THD) rates of 6% or lower provide stable power, reducing the risk of electrical surges or damage to sensitive welder components.
- Voltage Regulation: Stable voltage output is essential for maintaining consistent welding quality. Voltage fluctuations can lead to poor welds or damage to the welder.
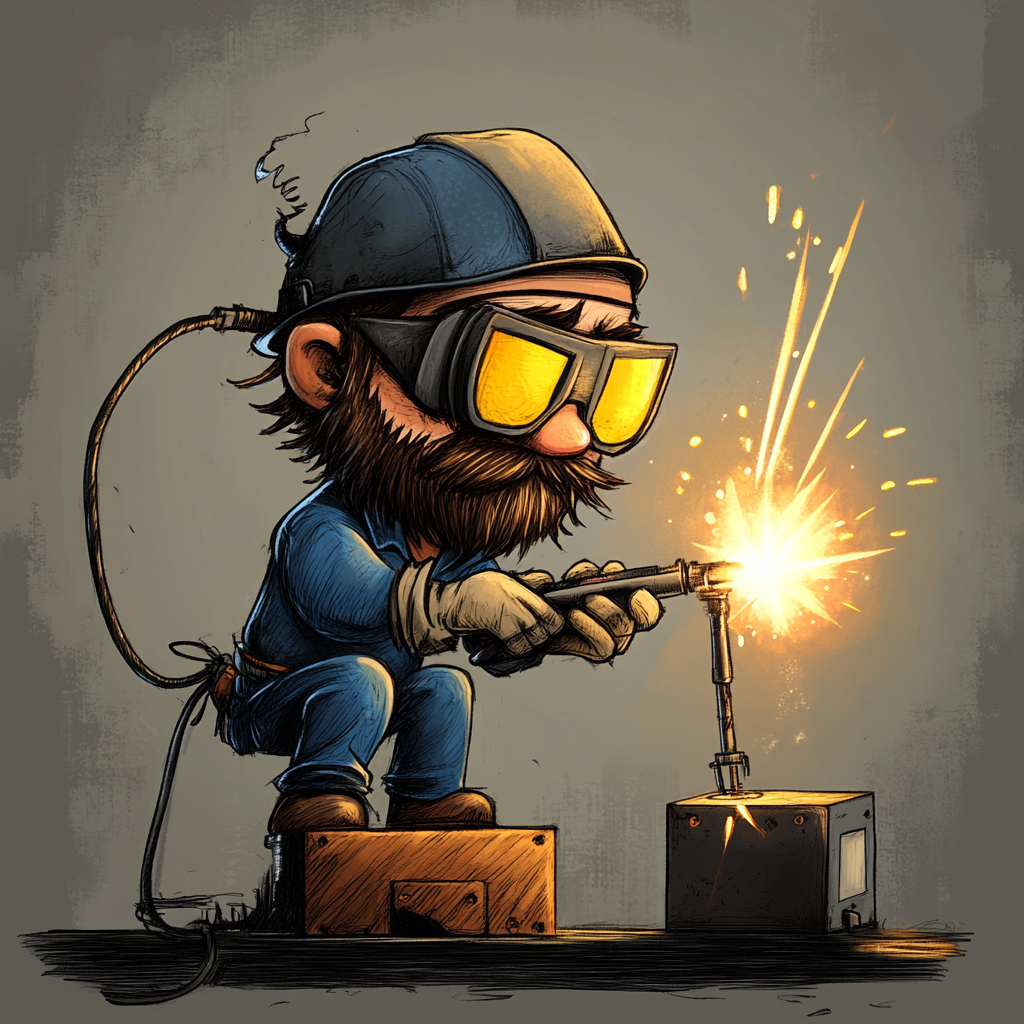
Why Generators Are Needed for Welding
Welders typically rely on steady electrical power to create a stable arc. However, there are many situations where access to a reliable power source is not available. These include:
- Outdoor Welding: Welding in remote or outdoor locations far from power outlets.
- Distant Power Sources: Workshops or setups where electrical outlets are out of reach, making standard connections impractical.
- Emergency Welding: During power outages, critical repairs may require immediate welding capabilities.
Scenarios Requiring Generators
When welding outside the comfort of a workshop, a generator provides mobility and independence. However, it’s important to recognize its limitations and plan accordingly:
- Long-Distance Projects: Generators allow you to weld on-site without relying on extension cords or temporary wiring, which may not always be practical or safe.
- Irregular Power Access: In industrial or construction environments, consistent and nearby power sources are not always guaranteed. Generators bridge this gap efficiently.
- Mobile Welding Businesses: Professionals who offer mobile welding services often depend on generators to power their equipment across various job sites.
Choosing the Right Generator for Welding Needs
To ensure your generator can handle the welder’s requirements:
- Assess Power Demands: Calculate your welder’s wattage requirements (both running and surge). For example, a 240V welder drawing 30 amps will need approximately 7,200 watts of continuous power.
- Generator Quality: Invest in a generator with features like low THD and voltage regulation to protect your equipment.
- Fuel Efficiency: Generators that balance power output with fuel consumption are better for long-term use, especially in remote locations where refueling may be challenging.
While generators are indispensable for mobile and emergency welding, choosing the right generator ensures safety, efficiency, and longevity for your equipment. Always prioritize compatibility and proper maintenance to avoid complications while working with welders powered by generators.
Types of Welders Compatible with Generators
Transformer Welders
Transformer welders are an excellent choice for use with generators due to their robust design and resilience to power fluctuations. These welders utilize a built-in transformer to adapt power from the generator into a suitable current for welding.
- Key Features:
- Durability: The internal transformer system is designed to handle inconsistent or fluctuating power levels without compromising performance.
- Versatility: Transformer welders can work well in various conditions, including outdoor or remote environments where generators are commonly used.
- Simplicity: These welders are mechanically straightforward, making them less prone to damage from surges or dirty power.
- Applications:
- Ideal for heavy-duty tasks such as structural welding, repairs, and industrial use.
- Frequently used by professionals who prioritize reliability over portability.
- Advantages When Paired with Generators:
- Better tolerance for Total Harmonic Distortion (THD) in the generator’s output.
- Can operate efficiently on generators with standard voltage regulation.
Inverter Welders
Inverter welders are lightweight, efficient, and compact, making them highly portable and suitable for modern welding applications. However, they are more sensitive to the quality of the power supply, which makes pairing them with generators more complex.
- Key Features:
- Compact Design: The absence of bulky transformers allows for a sleek, portable design that is easy to transport.
- Efficiency: Inverter technology allows these welders to use power more effectively, often requiring less input wattage for similar output compared to transformer welders.
- Advanced Electronics: These welders rely on electronic components to regulate and convert power.
- Challenges with Generators:
- Sensitivity to Power Fluctuations: Voltage surges and dirty power from generators can damage internal components, such as capacitors and control boards.
- THD Requirements: Inverter welders require generators with low THD (typically below 6%) to ensure stable and clean power.
- Recommendations for Use with Generators:
- Only pair inverter welders with generators explicitly designed for low THD and stable voltage output.
- Check the welder’s manual for compatibility with generator power.
Comparing Transformer and Inverter Welders for Generator Use
Feature | Transformer Welders | Inverter Welders |
---|---|---|
Durability | High (handles fluctuations well) | Medium (sensitive to power quality) |
Portability | Low (bulky and heavy) | High (lightweight and compact) |
Power Requirements | Less sensitive to THD | Requires low THD (<6%) |
Ideal Use Case | Heavy-duty, industrial tasks | Precision tasks, portability required |
Generator Compatibility | Works with standard generators | Requires high-quality generators |
Understanding the type of welder you have is critical when using a generator. Transformer welders are more forgiving of generator power inconsistencies, making them a safer choice for general use. In contrast, inverter welders require careful consideration of the generator’s power quality and THD. Select the right combination to ensure reliable performance and protect your equipment from damage.
Disadvantages of Using Generators as Power Sources
While generators are portable and convenient, they come with several challenges that can impact their use as a power source for welders. Understanding these disadvantages can help you make informed decisions about when and how to use generators.
Dirty Power
Generators often produce what is known as “dirty power,” which refers to electricity with significant fluctuations or distortions in its waveform.
Total Harmonic Distortion (THD)
- THD is a measure of the quality of the electrical output from a generator. High THD indicates more distortion, which can lead to power inconsistencies.
- Sensitive equipment, such as inverter welders, requires clean power with a THD of 6% or lower to operate safely and effectively.
- Generators with high THD can damage electronic components like capacitors and control circuits, resulting in costly repairs or replacements.
Mitigation Tips
- Invest in generators specifically designed to produce clean power, such as those with inverter technology.
- Check the generator’s specifications for its THD rating before pairing it with sensitive equipment.
Electrical Surges
Sudden power surges are another significant risk when using generators as a power source for welders. These surges can occur during startup or under fluctuating load conditions.
Impact on Welders
- Surges can overwhelm the welder’s internal components, leading to overheating or permanent damage.
- Inverter welders, in particular, are highly susceptible to surge damage due to their reliance on sensitive electronic systems.
Preventive Measures
- Use surge protectors or voltage stabilizers to mitigate the effects of electrical surges.
- Avoid overloading the generator, as this increases the likelihood of surges.
Noise and Pollution
Generators are not the most pleasant devices to work near due to their environmental and operational drawbacks.
Noise
- Generators can be extremely noisy, especially conventional models. This can make them disruptive in quiet environments or extended welding sessions.
- Noise levels vary by model, so consider generators with noise-reduction features for a more comfortable experience.
Pollution
- Generators emit exhaust fumes that contribute to air pollution. Prolonged exposure to these emissions can be harmful, particularly in enclosed or poorly ventilated spaces.
- The smell of exhaust can also be unpleasant, further detracting from the user experience.
Solutions to Minimize Impact
- Opt for generators that are designed to be quieter and more environmentally friendly, such as models with eco-mode or reduced emissions.
- Use generators in open, well-ventilated areas to disperse fumes effectively.
While generators offer flexibility and mobility for powering welders, their drawbacks—including dirty power, electrical surges, and noise/pollution—must be carefully managed. By investing in high-quality, low-THD generators and taking appropriate preventive measures, you can mitigate these disadvantages and ensure a safer, more efficient welding experience.
Selecting the Right Generator for Your Welder
Expanded Section: Selecting the Right Generator for Your Welder
Choosing the right generator for your welder is critical for ensuring smooth operation, protecting your equipment, and achieving consistent welding performance. Below are expanded details to help guide your selection process.
Consider the Wattage Requirements
The generator’s maximum output must align with the power needs of your welding equipment. This ensures that the welder receives sufficient power for both startup and continuous operation.
- For 130 Amp Welders:
- A generator rated at 7 kVA (kilovolt-amperes) is suitable for welders operating at this amperage. These smaller welders are ideal for light-duty applications, such as automotive repairs or hobby projects.
- Startup Consideration: Make sure the generator’s surge capacity exceeds the welder’s startup wattage to avoid tripping or overloading the generator.
- For 250 Amp Welders:
- Welders with higher amperage demands require a generator rated at 15 kVA or higher. These models are designed for heavy-duty tasks, such as industrial welding or structural repairs.
- Sustained Performance: A higher-rated generator reduces strain during prolonged operation, enhancing its lifespan and reliability.
Key Features to Look For
Selecting a generator with the right features can significantly impact its compatibility with your welder and overall performance.
- Low THD:
- Generators with Total Harmonic Distortion (THD) rates below 6% produce cleaner power, reducing the risk of damaging sensitive electronic components in your welder, particularly inverter models.
- Recommendation: Look for inverter generators, which often have low THD and provide stable, precise power.
- Voltage Regulation:
- Consistent voltage output ensures uniform welding quality. Voltage regulation helps prevent weld defects caused by fluctuations in power supply.
- Importance: Essential for precision welding tasks, especially when using TIG or MIG welders.
- High-Quality Components:
- A reliable generator with durable parts minimizes the likelihood of breakdowns or maintenance issues, ensuring long-term dependable performance.
- Example: Brands with established reputations for durability and customer support often provide better value over time.
Best Practices for Using Generators with Welders
Maximizing the lifespan and performance of your generator and welder requires proper setup and maintenance.
- Regular Maintenance:
- Inspect fuel lines, cables, and power extension leads for wear or damage. Replace any compromised parts to maintain optimal performance.
- Clean air filters and check oil levels regularly to prevent engine strain.
- Proper Grounding:
- Grounding the generator reduces the risk of electrical shocks and ensures safe operation. Always follow the manufacturer’s guidelines for grounding procedures.
- Cool-Down Periods:
- After extended use, allow the generator to run without load for a few minutes before shutting it off. This prevents overheating and extends its operational life.
- Storage Tips:
- Store the generator in a dry, well-ventilated area to protect it from moisture and dust. Drain fuel if it will not be used for an extended period to avoid clogging the fuel system.
Additional Considerations
When selecting a generator, consider:
- Fuel Type: Decide between gasoline, diesel, or dual-fuel generators based on availability, efficiency, and cost.
- Portability: If you need to move the generator frequently, opt for a lightweight model with wheels and a sturdy frame.
- Noise Levels: Generators with noise-reduction features are preferable for minimizing disruptions in quieter environments.
Selecting the right generator involves understanding your welder’s power requirements, choosing a model with the appropriate features, and adhering to best practices for usage and maintenance. By investing in a generator tailored to your needs, you can ensure reliable and efficient welding performance in any setting.
Conclusion
Using a generator to power a welder is possible and often necessary for remote or emergency welding. However, to avoid damaging your equipment, it’s crucial to use a generator that meets the welder’s power requirements, offers low THD, and ensures stable output. Whenever possible, prioritize transformer welders for generator use, but if you must use an inverter welder, ensure the generator is compatible and properly maintained. THD and is the correct size for your welder.
Additional Resources
Get your welding gear here.
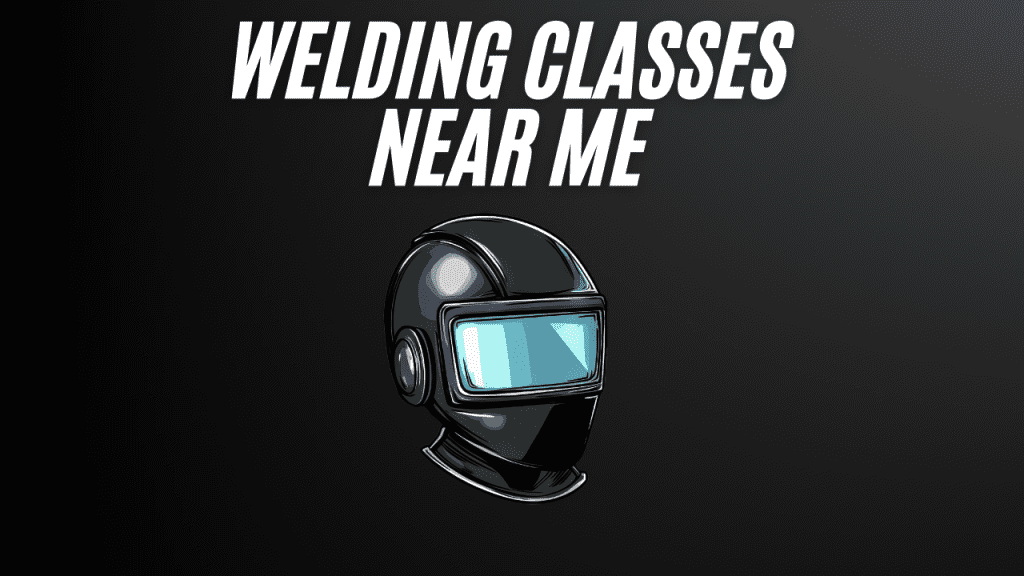