Table of Contents
Can I Plug a Welder into a Regular Outlet?
Introduction
Plugging a welder into a regular outlet is a common question for DIY enthusiasts and homeowners interested in tackling welding projects at home. While it is possible to use a standard 120V outlet for some welders, there are several factors to consider, including the type of welder, your home’s electrical capacity, and safety precautions. This guide will help you determine whether your setup can handle a welder and how to do so safely and effectively.
Can I Plug a Welder into a Regular Outlet?
Yes, but it depends on the welder and your home’s electrical setup. Some welders are designed to run efficiently on the standard 120V outlets found in most homes, while others may require higher voltage or dedicated outlets for optimal performance.
120V Welders: These welders are ideal for homeowners and DIY enthusiasts as they can plug directly into regular outlets. The Millermatic 141 MIG Welder is an excellent example, as it runs efficiently on 120V without requiring special modifications.
220V Welders: For heavier-duty tasks, a 220V welder may be required. In such cases, you’ll need to install a dedicated 220V outlet in your home to provide the necessary power. This modification can unlock the full potential of your welder for demanding projects.
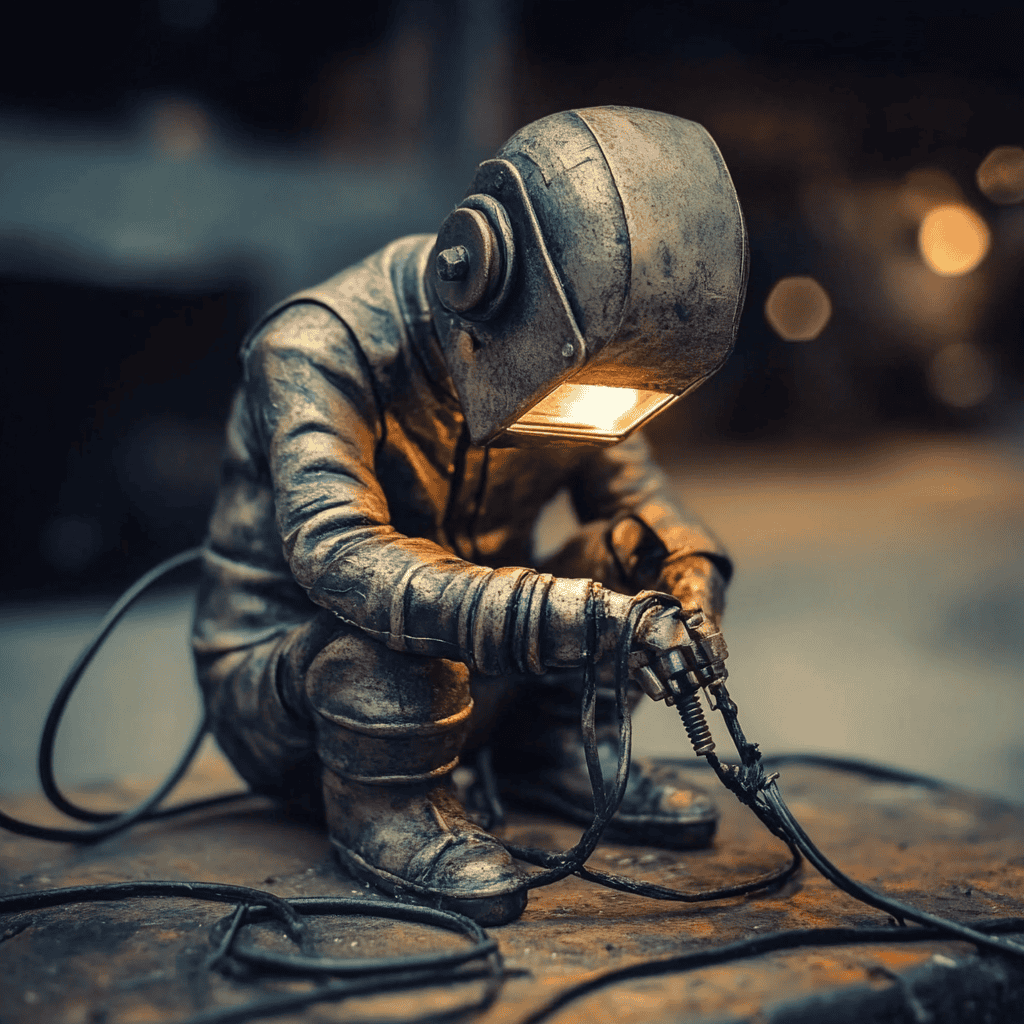
How to Set Up Your Home for Welding
Setting up your home for welding involves more than just plugging your welder into a socket. Proper preparation ensures safe operation, protects your equipment, and helps you achieve optimal performance. Key considerations include assessing your electrical system, taking necessary safety precautions, and having the right accessories on hand.
Electrical Setup
Your home’s electrical setup must meet the welder’s power requirements. Most welders designed for regular outlets need at least 120V and 20 amps to function effectively. To ensure a safe and reliable setup:
- Assess Your Outlets: Use a multimeter to check the voltage output of your outlets. Ensure they provide the required voltage and amperage for your welder.
- Upgrade Circuits if Needed: If your outlets cannot handle the necessary power, consider upgrading the circuit to accommodate the welder. This may involve increasing the amperage or adding a dedicated circuit for the welder.
- Use a Generator for Flexibility: If modifying your home’s wiring isn’t feasible, a generator can provide the required power. Look for a generator with at least 3000 watts to support most welders. Ensure it is properly grounded and compatible with your welder’s plug type.
- Inspect Wiring Regularly: Faulty wiring can lead to overheating, sparks, or even electrical fires. Periodically check the condition of your outlets and wiring, especially if you frequently use your welder. Replace any worn or damaged components immediately.
Installing a 220V Outlet
For welders requiring more power, a 220V outlet is essential. These outlets provide the additional amperage needed for heavy-duty welding projects, such as working with thick metals or performing long welding sessions. Here’s how to install a 220V outlet:
- Consult a Licensed Electrician: Installing a 220V outlet involves working with high voltage, which can be dangerous if not done correctly. A licensed electrician will ensure the installation meets local codes and is completed safely.
- Choose the Right Outlet: Common 220V outlet types for welders include NEMA 6-50R (for 50-amp machines) or NEMA 14-50R (for modern applications with grounding). Confirm compatibility with your welder’s plug.
- Run a Dedicated Circuit: A dedicated circuit ensures your welder doesn’t compete with other appliances for power, reducing the risk of overloading and tripping breakers.
- Select Proper Wire Gauge: The wire gauge depends on the welder’s amperage requirements. For example:
- 30-amp circuits: Use 10-gauge wire.
- 50-amp circuits: Use 6-gauge wire.
- Test the Setup: Once installed, use a multimeter to verify the voltage output and ensure the outlet is functioning correctly before plugging in your welder.
Additional Electrical Considerations
- Use the Correct Plug Adapter: If your welder’s plug doesn’t match the outlet, use a high-quality adapter rated for your welder’s amperage to ensure a secure connection.
- Grounding: Proper grounding is critical for safety. Ensure your outlets, wiring, and generator (if used) are correctly grounded to prevent electrical shocks.
- Circuit Breakers: Equip the circuit with a breaker appropriate for the welder’s amperage to protect against overloads. For instance, a 50-amp breaker is suitable for most 220V welders.
Setting Up Your Work Area
In addition to the electrical setup, ensure your workspace is well-prepared:
- Ventilation: Proper ventilation is crucial to remove welding fumes. Open windows or install fans to maintain airflow, especially in enclosed areas.
- Clear Workspace: Keep the area around your welder free of clutter, flammable materials, and unnecessary tools to minimize hazards.
- Lighting: Ensure your workspace is well-lit to help you see the weld pool clearly and work accurately.
Setting up your home for welding is an investment in safety, efficiency, and the quality of your work. By ensuring your electrical system is up to standard, installing a 220V outlet if necessary, and maintaining a clean and safe workspace, you can confidently take on welding projects at home.
Choosing the Right Welder for a Regular Outlet
Selecting the right welder for your home setup involves considering the type of projects you’ll undertake, your experience level, and your home’s electrical capacity. While some welders are better suited for light-duty work and standard 120V outlets, others may require modifications to your electrical setup. Below is an expanded guide to the most common welding types and their suitability for home use.
MIG Welding
MIG (Metal Inert Gas) welding is one of the most popular choices for home use due to its ease of operation and versatility.
- Ease of Use: MIG welders are highly beginner-friendly. The process involves feeding a continuous wire electrode through the welding gun, making it straightforward and efficient.
- Applications: Ideal for light to medium-duty projects, such as repairing fences, building metal furniture, or working on car panels.
- Power Requirements: Many MIG welders are designed to operate on 120V outlets, making them compatible with standard home electrical setups. Models like the Millermatic 141 are excellent examples of welders that perform well on regular outlets.
- Shielding Gas or Flux Core: MIG welding can use either shielding gas for cleaner welds or flux-cored wire, which eliminates the need for gas and is better for outdoor projects.
Stick Welding
Stick welding, also known as Shielded Metal Arc Welding (SMAW), is a versatile and robust option for a wide range of tasks.
- Versatility: Stick welding works well in various conditions, including outdoor environments and on dirty or rusty metals. This makes it ideal for DIY repairs, farm equipment maintenance, and heavy-duty fabrication.
- Applications: Commonly used for tasks like welding structural steel, fences, or heavy machinery.
- Power Requirements: While some stick welders can run on 120V outlets, they often require higher amperage or 220V circuits for more demanding projects.
- Skill Level: Stick welding can be more challenging for beginners due to the need for precise control over the electrode angle and arc length. However, with practice, it becomes a reliable and flexible welding method.
TIG Welding
TIG (Tungsten Inert Gas) welding offers the highest level of precision and is often used for intricate and high-quality work.
- Precision and Quality: TIG welding is known for producing clean, precise welds, making it suitable for aluminum, stainless steel, and other delicate metals.
- Applications: Commonly used for tasks like repairing bike frames, welding car exhaust systems, or creating artistic metalwork.
- Power Requirements: TIG welders typically require stable electrical support and may need 220V outlets for more advanced machines. While some lightweight models can run on 120V, they may be limited in output.
- Skill Level: TIG welding demands a higher level of skill, as it requires precise control of the torch, filler material, and foot pedal (for amperage adjustments). It is best suited for experienced welders or those willing to invest time in learning the technique.
Gas Welding
Gas welding, though less common in modern home setups, still has its place for certain applications.
- Process: Gas welding combines combustible gas (like acetylene) with oxygen to create a flame that melts the metal.
- Applications: Often used for pipe welding, small metal repairs, or in scenarios where electricity is not available.
- Power Requirements: Gas welding doesn’t require an electrical power source, making it useful in remote locations or situations where portability is key.
- Limitations: Compared to other methods, gas welding is slower and less precise, and it has largely been replaced by TIG and MIG welding for most applications.
Factors to Consider When Choosing a Welder for a Regular Outlet
- Project Type: Identify the materials and scale of your projects. For light-duty repairs, MIG or stick welders are sufficient. For intricate work or aluminum, TIG welding may be necessary.
- Power Compatibility: Confirm that the welder can run on 120V outlets if you don’t plan to modify your home’s electrical setup. Look for welders designed specifically for regular outlets.
- Skill Level: Beginners may prefer MIG welders due to their ease of use, while experienced welders might lean toward TIG for precision or stick welding for versatility.
- Environment: Consider the conditions in which you’ll be welding. Stick welders excel outdoors and on dirty materials, while MIG welders are better for clean, indoor environments.
Choosing the right welder for your home setup ensures you can complete your projects efficiently and safely. By understanding the strengths and requirements of each welding type, you can select a machine that fits your needs and works seamlessly with a regular outlet.
Accessories Needed to Run a Welder at Home
Operating a welder at home requires more than just plugging in the machine and getting to work. To ensure safety, efficiency, and quality welds, you need the right tools and protective equipment. Here’s a detailed guide to the essential accessories required for welding at home.
Welding Helmet
A welding helmet is one of the most critical pieces of safety equipment for any welder. It protects your face and eyes from harmful UV rays, sparks, and debris.
- Auto-Darkening Helmets: These automatically adjust the shade level when the arc is struck, allowing you to see the workspace clearly before and after welding.
- Fixed-Shade Helmets: Traditional helmets with a set shade level. They are less expensive but require you to lift the helmet frequently to see your work.
- Additional Features: Look for helmets with comfortable headgear, large viewing areas, and anti-fog coatings for maximum efficiency and comfort.
Protective Clothing
Welding generates extreme heat, sparks, and spatter that can cause serious injuries if you’re not properly protected. Invest in high-quality flame-resistant gear.
- Gloves: Welding gloves are designed to withstand heat and protect your hands. Choose heavy-duty leather gloves for stick and MIG welding, and thinner gloves for TIG welding, where dexterity is essential.
- Jackets and Aprons: Flame-resistant jackets or aprons provide full upper body protection. Leather jackets are ideal for heavy-duty welding, while lightweight flame-resistant cotton jackets are suitable for light-duty tasks.
- Pants and Shoes: Wear flame-resistant pants without cuffs to prevent sparks from getting trapped. Leather boots or shoes with non-slip soles and no exposed laces offer excellent foot protection.
Shielding Gas
For MIG and TIG welding, shielding gas is essential to protect the weld pool from contamination by atmospheric gases like oxygen and nitrogen.
- Types of Gas:
- Argon: Commonly used for TIG welding and light MIG welding tasks.
- CO₂: Cost-effective and widely used for MIG welding on thicker materials.
- Argon-CO₂ Mix: Provides better arc stability and cleaner welds than pure CO₂.
- Gas Cylinders: Purchase larger cylinders (80 or 125 cf) for cost efficiency, as smaller cylinders require frequent refills. Always secure cylinders upright to prevent tipping and store them in a well-ventilated area.
Welding Cart
A welding cart offers both convenience and safety by keeping your welder mobile and your workspace organized.
- Storage: Provides designated spaces for your welder, gas cylinder, and accessories like clamps, electrodes, and tools.
- Mobility: Equipped with wheels or casters, a cart allows you to move your welder easily around your workspace.
- Customization: Many welding carts include hooks or compartments for storing cables and hoses to reduce clutter.
Angle Grinder and Saw
These tools are indispensable for material preparation and post-weld cleanup.
- Angle Grinder: Used for grinding down welds, removing rust or paint, and preparing metal surfaces for welding. Choose a grinder with multiple disc attachments for versatility.
- Chop Saw: Ideal for cutting metal pieces to size before welding. Look for models with adjustable angles for precision cuts.
Additional Accessories for Optimal Welding Performance
Clamps and Vises
- Welding clamps and vises are essential for securing materials in place during welding. They prevent movement and ensure accuracy in your work.
- Magnetic clamps are particularly useful for holding materials at specific angles.
Wire Brush and Chipping Hammer
- A wire brush removes slag, rust, or other debris from the weld surface to ensure better weld quality.
- A chipping hammer helps clean up slag from stick welding and other processes.
Fire Extinguisher
- Keep a fire extinguisher rated for electrical or chemical fires nearby to address any accidents immediately.
- Regularly check that your extinguisher is functional and within its expiration date.
Ventilation System
- Welding produces fumes and gases that can be hazardous if inhaled.
- Install fans, fume extractors, or exhaust systems to ensure proper ventilation in your workspace.
Extension Cords
- Use heavy-duty extension cords rated for the welder’s amperage if your power source is not directly accessible. Ensure the cords are designed for industrial use to prevent overheating or voltage drops.
Flame-Resistant Blankets
- Place flame-resistant blankets over nearby surfaces to protect them from sparks and heat. These are especially useful in confined spaces or when welding near flammable materials.
Key Considerations When Choosing Accessories
- Quality: Always choose high-quality, durable accessories designed for welding applications. Inferior equipment can compromise safety and performance.
- Compatibility: Ensure all tools and accessories are compatible with your specific welder and project requirements.
- Storage: Organize your workspace with proper storage solutions, like welding carts or toolboxes, to keep everything within reach and avoid clutter.
By equipping yourself with the right tools and safety gear, you can run a welder safely and efficiently at home, achieving professional-grade results while minimizing risks. Investing in these accessories not only protects you but also extends the lifespan of your welding equipment.
Safety Considerations When Using a Welder at Home
Welding is a powerful and versatile process, but it carries inherent risks, especially in a home environment where spaces and setups may not be optimized for industrial-grade equipment. Proper safety measures are essential to prevent accidents, injuries, and damage to your property. Below are detailed guidelines to ensure a safe and efficient welding experience at home.
Proper Ventilation
- Welding produces harmful fumes and gases, including metal oxide particles, carbon dioxide, and ozone, which can be hazardous to your health if inhaled.
- Ventilation Options: Open windows, doors, or garage bays to increase airflow. Use fans to direct fumes away from your workspace.
- Fume Extractors: Install a fume extraction system for confined areas to remove harmful gases directly from the source. Portable fume extractors are ideal for home setups.
- Respiratory Protection: In poorly ventilated areas, wear a respirator designed for welding fumes to protect your lungs from prolonged exposure.
Remove Flammable Materials
- Sparks and heat from welding can easily ignite flammable materials like sawdust, wood scraps, paper, or chemicals.
- Clear the Workspace: Inspect your welding area and remove any flammable items within a 10-15 foot radius.
- Storage: Keep flammable materials in fireproof containers or cabinets far from your workspace.
Fire Extinguishers and Emergency Preparedness
- Fire Extinguisher Types: Have a fire extinguisher rated for Class C (electrical) and Class D (metal) fires readily accessible.
- Emergency Plan: Ensure you know how to use the extinguisher and have an evacuation plan in case of fire.
Inspect and Secure Electrical Connections
- Loose or damaged connections can cause short circuits, leading to sparks, overheating, or equipment failure.
- Inspection Checklist: Regularly check outlets, extension cords, and cables for wear or damage. Replace any frayed or cracked components immediately.
- Secure Connections: Ensure all plugs are fully inserted into outlets, and avoid overloading circuits by using a dedicated breaker for your welder.
Use Flame-Resistant Blankets and Shields
- Welding produces intense sparks, which can damage nearby surfaces or cause fires.
- Flame-Resistant Blankets: Cover work surfaces, walls, or floors with flame-resistant blankets to shield them from sparks and heat splashes.
- Welding Curtains: Use welding curtains or screens to protect other people and objects in the vicinity from stray sparks and UV radiation.
Personal Protective Equipment (PPE)
- Welding Helmet: Always wear an auto-darkening helmet to protect your eyes and face from UV rays, sparks, and debris.
- Gloves and Clothing: Use flame-resistant gloves, jackets, and pants made of leather or other non-synthetic materials. Avoid loose-fitting clothing that could catch fire.
- Footwear: Wear leather boots with steel toes for maximum protection from sparks and heavy objects.
Organized Workspace
- Tidy Environment: Keep your workspace clear of unnecessary tools, hoses, and wires to avoid tripping hazards and maintain an efficient workflow.
- Tool Storage: Use welding carts or toolboxes to organize and store equipment safely.
Troubleshooting Common Issues
Despite precautions, issues may arise during home welding. Here are some quick solutions to common problems:
Breaker Tripping
- Cause: Breaker trips when your welder draws more amperage than the circuit can handle.
- Solution:
- Check the amperage rating of the circuit and compare it with the welder’s requirements.
- Upgrade the circuit to a higher amperage or switch to a smaller welder compatible with your existing setup.
- Reduce the load on the circuit by unplugging other devices.
Low Weld Quality
- Cause: Poor welds can result from insufficient amperage, improper grounding, or contaminated materials.
- Solution:
- Adjust the welder’s amperage settings to match the material thickness and type.
- Ensure a solid ground connection by attaching the ground clamp to clean, bare metal.
- Clean the workpieces with an angle grinder or wire brush to remove rust, paint, or dirt.
Overheating
- Cause: Overheating occurs when the welder exceeds its duty cycle (the percentage of time it can operate continuously within a 10-minute period).
- Solution:
- Monitor the duty cycle specified in the welder’s manual and allow the machine to cool as required.
- Use a fan or place the welder in a well-ventilated area to dissipate heat more effectively.
- Consider upgrading to a higher-duty-cycle machine for prolonged welding tasks.
Arc Instability
- Cause: The arc flickers or breaks due to incorrect electrode size, poor gas flow, or inconsistent wire feed.
- Solution:
- Match the electrode size and type to the material being welded.
- Check the gas cylinder for leaks or low pressure and adjust the flow rate.
- Inspect and clean the wire feed mechanism to ensure smooth operation.
Sparks or Smoke from Outlets
- Cause: Overloaded or faulty outlets can emit sparks or smoke, posing serious fire risks.
- Solution:
- Immediately stop using the outlet and unplug all devices.
- Inspect the outlet for visible damage and consult an electrician for repairs or upgrades.
By taking these safety precautions and addressing common issues proactively, you can create a safer, more efficient welding environment at home while achieving high-quality results. Always prioritize safety and adhere to the manufacturer’s guidelines for your equipment.
Final Thoughts
Plugging a welder into a regular outlet is entirely possible for light-duty welding tasks if you choose the right welder and ensure your electrical setup is adequate. For more demanding projects, upgrading to a 220V outlet or using a generator may be necessary. Always prioritize safety, use the proper equipment, and follow manufacturer guidelines to ensure a smooth and successful welding experience. Whether you’re tackling home repairs or exploring a new hobby, welding at home can be a rewarding and practical endeavor.
Additional Resources
Get your welding gear here.
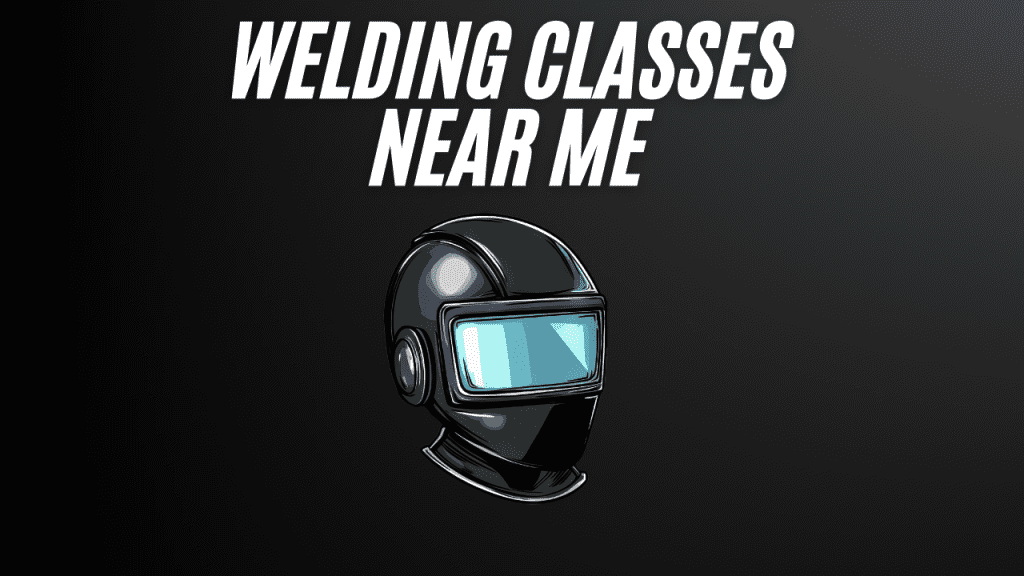